доски, плиты, аналоги фанеры и их производство из отходов древесины
Древесные опилки используют для изготовления транспортных материалов, таких как:
- плиты;
- поддоны;
- доски.
В этой статье расскажем об особенностях и различиях данных материалов, а также о том, как их изготавливают и где применяют.
Поддонами называют транспортную тару, которую используют для перевозки или иной транспортировки различных грузов. Такая тара защищает товары от контакта с погрузчиком и полом, поэтому многократно снижается вероятность испачкать транспортируемую продукцию.
Кроме того, поддон позволяет перегружать довольно большое количество грузов, упакованных в коробки или мешки, а также имеющих прямоугольную форму, с помощью вилочных погрузчиков.
Отличия поддонов и паллетов
Поддоны и паллеты состоят из досок и бобышек, причем доски образуют решетку.
Разница между поддонами и паллетами в том, что последние подходят для транспортировки не только с помощью вилочного погрузчика
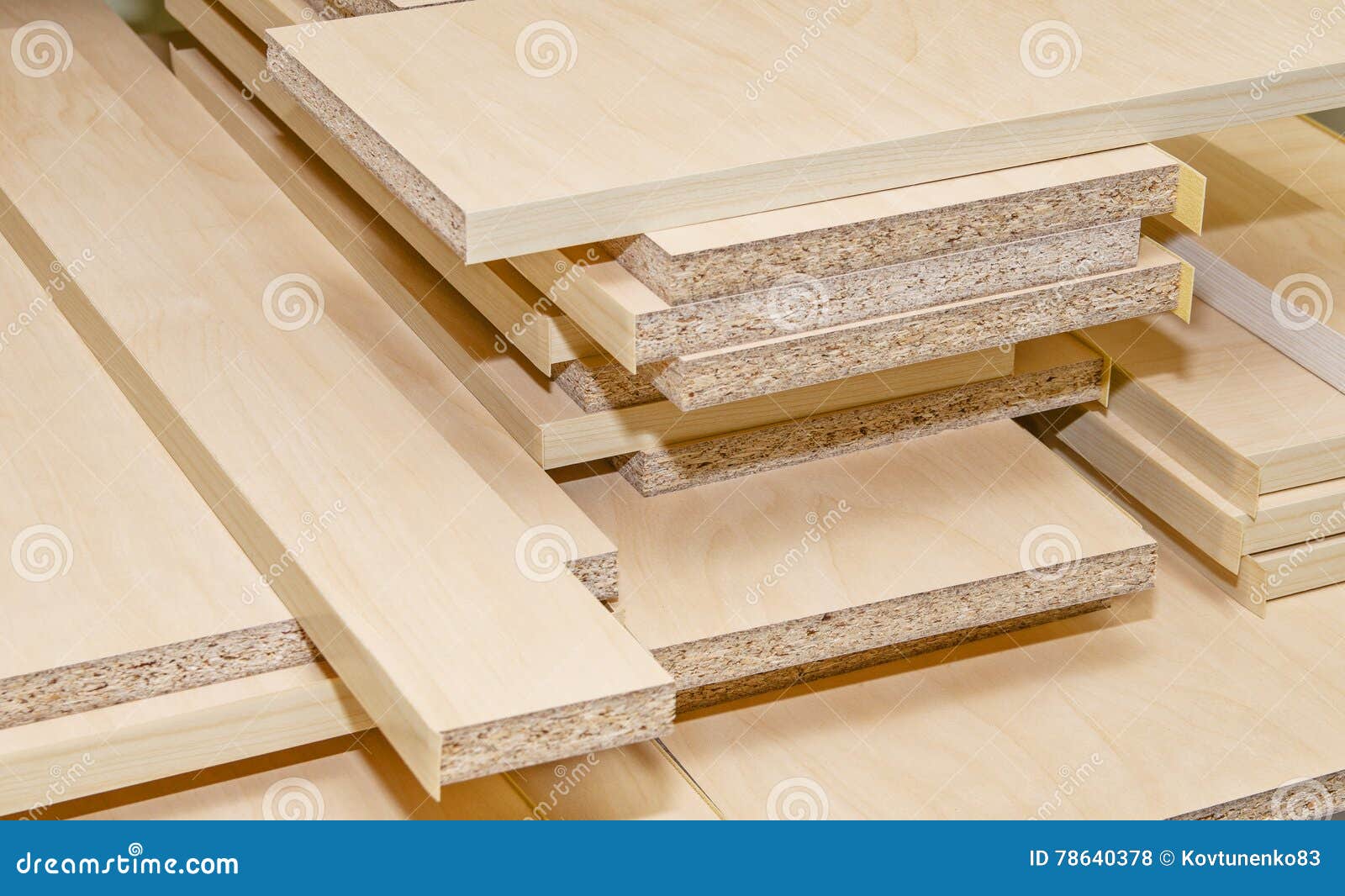
Это расширяет область их применения.
Конструктивно они устроены одинаково, а разница получается за счет более удачного подбора формы и размеров.
Нередко те, кому нужна тара для транспортировки различных грузов, покупают не готовые изделия, а только основной элемент, то есть бобышки, которые являются перемычкой между верхней и нижней решетками из досок.
Именно от бобышек зависит возвышение верхней площадки паллеты над землей. Кроме того, от бобышки зависит надежность удержания гвоздей, которыми соединяют между собой все части поддона.
Чем мягче древесина этой детали, тем менее прочными получаются поддоны и тем выше вероятность повреждения упаковки груза вылезшей из доски шляпкой гвоздя.
Технология изготовления
Все виды поддонов и паллет из опилок изготавливают по одной технологии:
- опилки просушивают, доводя влажность до 8–10 %;
- высушенные опилки смешивают с клеем;
- заполняют этим составом формы;
- прессуют и нагревают;
- окрашивают в нужный цвет.
Просушивание необходимо для того, чтобы опилки сжались до минимального размера и приобрели максимальную прочность.
Ведь чем больше влаги в древесине, тем больше ее размер.
Кроме того, наполненные водой опилки размягчаются, что негативно влияет на жесткость и прочность готового изделия.
Оптимальная влажность составляет 8%.
Чтобы довести отходы распиливания древесины до этого состояния, их
Просушенный материал смешивают с различными клеями до образования однородной массы. В качестве клея используют множество различных натуральных и синтетических веществ.
Если производитель нацелен на максимальную прибыль, пусть даже в ущерб безопасности его продукции, то будет применять дешевые смолы, которые выделяют формальдегид.
Этот газ является не только высокотоксичным отравляющим веществом, но и канцерогеном, то есть может вызвать появление раковых опухолей.
Несмотря на то, что даже качественный клей содержит это вещество, разница в количестве и возможности свободного испарения формальдегида.
Допуски по содержанию ядовитых веществ для транспортных материалов гораздо выше, чем для продукции, которая идет на изготовление мебели, поэтому в качестве вяжущего вещества используют тот же клей, что применяют при производстве ДСП (древесностружечных плит).
После смешивания клея и опилок готовую массу загружают в матрицы или специальные агрегаты, которые придают материалу необходимую форму. Плиты делают с помощью прессов, которые вдавливают пуансон в матрицу, благодаря чему плита обретает нужную форму.
Ребра жесткости на ней позволяют экономить материал без потери прочности, благодаря чему снижается стоимость изделия.
Одновременно с прессованием массу в матрице подвергают нагреву, ускоряющему полимеризацию клея.
Таким же образом изготавливают и доски, поэтому единственное отличие в форме матрицы и пуансона.
Бобышки поддонов, они же шайбы или шашки, делают из бруса, нарезая его на куски необходимой длины.
Это позволяет снизить затраты на оборудование, ведь не придется покупать еще один пресс с комплектом матриц и пуансонов.
Нарезанные из бруса бобышки обладают теми же характеристиками, что и изготовленные прессованием в матрицах, и заметно превосходят детали, изготовленные из цельной древесины или полноразмерных отходов.
Для изготовления бруса используют другой тип пресса, в нем шнек подает готовую массу к калиброванному отверстию.
Благодаря избыточной производительности шнека, поступление готовой массы гораздо больше пропускной способности калиброванного отверстия, что и приводит к увеличению давления.
После этого брус проходит по каналу такой же формы и размера, что и калиброванное отверстие, стенки которого нагреты до температуры 140–160 градусов. Это ускоряет полимеризацию клея
и делает брус более прочным.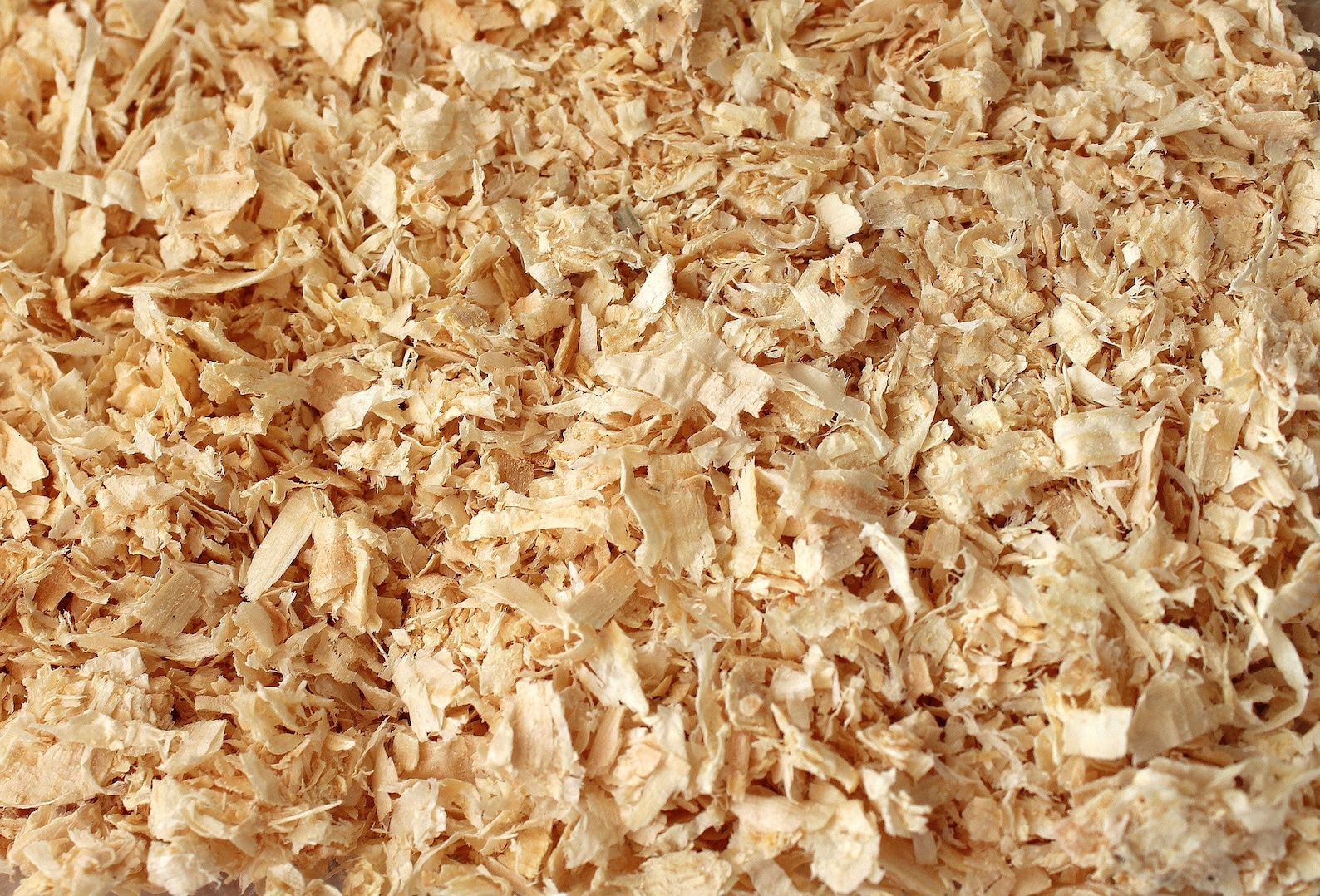
Технология производства одинакова для любого типа изделий.
Разница лишь в способе подачи смеси и форме матрицы/пуансона, которые используют на последнем этапе (для придания продукции необходимой формы).
Мы подготовили несколько ссылок на сайты, где производители предлагают полный комплект оборудования, необходимого для производства этих изделий из опилок, а также краткое описание данного технологического цикла:
- Пресс для производства шашек.
- Линия для производства бобышек.
- Линия для производства поддонов.
Применение тары из древесных отходов
Чаще всего такие изделия применяют в качестве транспортной тары, ведь поддон или паллет из опилок обходятся как минимум на 20 % дешевле, чем сделанные из цельной древесины или полноразмерных отходов.
При этом технические характеристики ничем не уступают транспортной таре, изготовленной из дерева.
Поддоны и паллеты применяют для хранения и транспортировки любых сухих не сыпучих грузов, таких как:
- мешки с любым содержимым;
- бочки с любым содержимым;
- прямоугольные или квадратные предметы.
Преимущество паллет и поддонов по сравнению с мешками и коробками в том, что их можно перемещать с помощью различных погрузчиков, это многократно ускоряет процесс погрузки и выгрузки любого транспортного средства.
Кроме того, различные товары невозможно экспортировать в многие страны, если они не установлены на поддоны или паллеты.
Большой популярностью пользуются бобышки из опилок, которые можно использовать для изготовления поддонов нестандартной формы или размера.
Нередко одно предприятие производит бобышки нужных размеров, другое выпускает доски из опилок, а третье собирает из них готовые паллеты необходимой формы.
Фанера
Многие считают, что из опилок также делают фанеру, которую используют для упаковки и транспортировки различных товаров.
На самом деле фанеру делают только из цельной древесины, луща ее на специальных станках, чтобы получить шпон. Затем этот шпон склеивают послойно, чтобы получить фанеру.
Готовый материал отличается очень высокой гибкостью и прочностью на скручивание, ведь в его основе лежат тонкие слои древесины, поэтому и стоимость готовой продукции гораздо выше, чем у любых материалов из опилок той же толщины и размера.
Вместо фанеры из опилок делают плиты сложной формы, которые эффективно заменяют большинство видов паллет и поддонов,
Благодаря сложному профилю и большому количеству ребер жесткости, прессованные плиты из опилок обладают хорошей грузоподъемностью и не уступают по этому параметру деревянной таре, а весят в несколько раз меньше.
Еще одно преимущество плит в том, что при складывании они входят одна в другую благодаря соответствию профилей верхней и нижней сторон друг другу. Такое же соответствие есть у картонных клеток для яиц, поэтому при укладывании их одна на другую они входят друг в друга.
Нередко под термином «фанера из опилок» подразумевают листы низкосортной ДСП, которую изготавливают их мелких древесных отходов.
Стоимость таких листов гораздо ниже, чем у фанеры аналогичных размеров и толщины.
Кроме того ДСП не выносят даже незначительных крутильных нагрузок, поэтому сравнивать их с фанерой некорректно.
Существует также ОСП (ориентированно-стружечная плита), которую тоже иногда называют фанерой из опилок, но и этот материал не имеет с фанерой ничего общего. Ведь по сути оба вида материала являются плитами (листами) из прессованных опилок и стружки, а также других древесных отходов.
Листы из прессованных опилок также используют для создания транспортной тары небольшой грузоподъемности и стоимости.
Для этого к листу ДСП или ОСП выбранного размера снизу прикручивают с помощью саморезов/шурупов или прибивают гвоздями необходимое количество бобышек.
Стоимость таких поддонов заметно выше, чем у штампованных плит, но они все равно обходятся дешевле полностью деревянной транспортной тары. Кроме того, подобная тара идеально подходит
Сравнение поддонов из различных материалов
Основное преимущество поддонов и паллет из опилок в их невысокой цене при аналогичных технических характеристиках, таких как срок службы и грузоподъемность.
По сравнению с деревянной тарой изделия из опилок обладают большей огнеустойчивостью и тяжелей разгораются, а также быстро тухнут без воздействия высокой температуры и открытого огня.
Составные поддоны, благодаря большей прочности материала, из которого сделаны бобышки, гораздо реже выпускают наружу шляпки гвоздей, поэтому перевозка любых товаров на них более безопасна.
Поддоны в форме штампованных плит полностью лишены этого недостатка, ведь они состоят из одной детали сложной формы и в них нет никаких гвоздей.
Цена на поддоны из опилок
Единой стоимости тары из опилок не существует, ведь цену определяет множество факторов, основные из которых:
- стоимость и качество опилок;
- тип клея;
- тип тары;
- форма и размеры;
- соответствие ГОСТ и другим нормативным документам, в том числе международным;
- наличие документов, подтверждающих возможность использовать паллет или других элементов внутри России, на территории СНГ или в других странах.
Поэтому стоимость продукции необходимо уточнять у производителей или продавцов.
Мы подготовили несколько ссылок на сайты, где предлагают такую продукцию. Пройдя по ним, вы сможете связаться с производителями или продавцами и обсудить стоимость различных вариантов поддонов и паллет.
Кроме того, мы подготовили ссылку на сайт, где предлагают не поддоны целиком, а только бобышки:
- Зеленый транспорт Presswood поддон.
- Прессованные поддоны.
- Демонстрационный поддон из прессованной древесины.
- Бобышки шашки для поддонов.
Видео по теме
Смотрите видео о производстве шашек для поддонов из опилок с помощью специального пресса:
Вывод
Изготовленные из опилок паллеты и поддоны, а также их комплектующие, то есть доски и бобышки, обходятся заметно дешевле деревянных или металлических аналогов. При этом продукция из прессованных отходов распиливания древесины по своим эксплуатационным свойствам ничуть не уступает изделиям из других материалов.
Прочитав статью, вы узнали:
- как создают эти изделия;
- чем отличаются различные технологии;
- где можно купить паллеты и поддоны из опилок.
ОСП панели — основной стройматериал в каркасной технологии
Каркасные дома, все больше набирающие популярность не вызывают сомнений в своей практичности и эффективности эксплуатации. А что же можно сказать о самом процессе постройки и тех материалах, которые используются для возведения таких строений?
Основными типами стройматериалов для таких сооружений являются деревянные брусья, балки и панели ОСП. Именно применение панелей обеспечивает каркасный дом теми характеристиками, которые так привлекают застройщиков.
Что такое ОСП
Для тех, кто задумал строительство дома из этих материалов, следует знать не только значение аббревиатуры, но и те качества, которыми они обладают, а также функциональные отличия от других аналогичных материалов.
Панели из ОСП представляют собой плиты, изготовленные из древесных щепок.
Значение аббревиатуры в переводе с английского языка означает «ориентированная стружечная плита» — Oriented Strand Board.
Отличие этих панелей от привычных отечественным застройщикам плит ДСП состоит в методе укладки и типе стружек. Если в ДСП основной компонент прессуется в хаотичном порядке, то панели ОСП в своей структуре содержат стружку, уложенную в одном направлении, то есть, — ориентированную.
Характерно то, что укладка стружки производится в каждом слое в другом направлении. Количество слоев в каждой плите — три или четыре. Обычно направление укладки стружки принято в следующем порядке:
- Первый слой — волокна размещаются в параллельно конструкции панели
- Второй слой всегда содержит направление стружки перпендикулярно направлению первого слоя
- Третий слой — снова укладка производится аналогично первому слою
- Четвертый слой — перпендикулярно размещенные волокна
В некоторых вариантах панелей принят другой метод прессования стружки, который включает параллельное расположение волокон стружки в наружных слоях и поперечное их размещение в двух внутренний пластах.
Для создания сэндвич панели из ОСП используется стружка длиной до 15 см, прессование которой проходит под высоким давлением. Их объем в структуре плиты достигает 90 процентов. Скрепление волокон стружки производится водостойкими смолами синтетического происхождения.
Как свидетельствуют многочисленные отзывы застройщиков, использовавших этот материал в строительстве своих домов, именно такая структура обеспечивает массу преимуществ эксплуатации дома. Одно из них, позволяющее экономить расход энергетических ресурсов в период отопления — высокая теплоемкость плит ОСП.
Сэндвич панели из ОСП в основном применяются в строительстве домов по канадской технологии. Теплые дома по канадской технологии за счет того, что панели, из которых они строятся, представляют собой трехслойную конструкцию — два листа OSB, между которыми расположен утеплитель.
SIP-панели — удобный материал с отличными эксплуатационными качествами и высокой долговечностью, позволяющий строить действительно быстро. Тем не менее, канадская технология строительства домов имеет минусы, которые описаны здесь.
Классификация панелей ОСП
В строительных целях рекомендуется применять отдельные виды панелей, так как структура и свойства разных типов отличаются и не всегда подходят для одних и тех же целей.
Отзывы о качествах ОСП панелей склоняются в сторону осознанного выбора только отдельных категорий таких панелей.
Чтобы не ошибиться при заказе материала, нужно изучить характерные параметры и классификацию ОСП плит. Тем более что сделать это несложно — их всего четыре, а различия в основном касаются количества пластов, степени прочности и показателей влагостойкости:
- Панели OSB-1 — плиты с очень невысокой степенью прочности и низким уровнем влагостойкости. В строительстве такие панели могут применяться только в интерьерных работах. Но чаще их использование распространено в сфере изготовления мебельных конструкций, а также для упаковочных изделий
- Плиты OSB-2 — обладают невысокой прочностью, хотя немного выше, чем панели первой категории.
Также могут применяться в отделочных интерьерных работах, иногда — при сооружении легких конструктивных элементов, перекрытий и перегородок. Но ввиду низкой влагостойкости не рекомендуется использовать в подвальных помещениях, при отделке цокольных этажей и во внутренних работах в санузлах и кухне
- OSB 3 — самая распространенная модель панелей ОСП. Она отлично зарекомендовала себя в наружных и внутренних работах. Может использоваться в разных частях здания. Обладает устойчивостью во влажной среде
- Панель категории OSB-4 — самая прочная марка плит ОСП, используемая во всех видах строительных работ. Благодаря высокой прочности может успешно монтироваться на наружных частях строительной конструкции, при устройстве крыш и чердаков. Отлично выдерживает действие влаги, благодаря чему применяется в нижних частях здания и помещениях с повышенной влажностью
Все эти свойства, присущие каждой категории панелей в разной степени, достигаются применением клеевой основы различного состава.
Влагостойкостью такие плиты обязаны смолистым соединениям клея, а прочностью — расположению волокон древесных стружек и количеству пластов в плите.
Различия в плитах ОСП имеются по типу покрытия
Промышленностью выпускаются панели с ламинированной поверхностью, которые можно использовать в качестве опалубки, причем неоднократно. В декоративных целях также выпускаются плиты лакированные с обеих или с одной стороны.
Для устройства горизонтальных поверхностей производятся панели с соединительными элементами по принципу ламинатной доски. С двух или четырех сторон таких панелей имеются торцевые гребни и пазы для соединения рядом лежащих плит.
Отзывы об ОСП панелях от покупателей склоняются к тому, что они имеют перспективу в производстве отделочных работ, могут выступать отличной альтернативой в устройстве полов.
Свойства ОСП панелей
Отзывы покупателей панелей и застройщиков отмечают несколько существенных преимуществ этого материала:
- Технология укладки древесной щепы и длина стружки делают панели ОСП более жесткими, что позволяет им обрести устойчивость к механическим воздействиям
- Благодаря методу конвейерного производства в плитах соблюдаются заданные технологическими требованиями габариты.
По этой же причине достигается и равномерность толщины во всех частях плиты. Это качество способствует удобству монтажа плит ОСП
- Снижение трудоемкости процесса монтажа, повышение оперативности постройки. Панели имеют малый вес, могут легко транспортироваться и не создают дополнительных сложностей при погрузочно-разгрузочных работах
- Высокие показатели теплоизоляции — еще одно весомое преимущество этого материала. Это свойство достигается благодаря высокой концентрации древесных компонентов, известных теплоизоляционными свойствами
- Доступность в процессе обработки — ОСП могут беспрепятственно подвергаться шлифовке, сверлению, резке. А при забивании гвоздей края плиты не крошатся
Свойства OSB | толщина плиты 12мм |
Отклонение по длине, мм | +/-3 |
Отклонение по ширине, мм | +/-0,3 |
Отклонение по толщине, мм | +/-0,8 |
Отклонение от прямого угла, максимум, мм/м | 2 |
Сопротивление при изгибе, главная ось, МПа | 20 |
Сопротивление при изгибе, латеральная ось, МПа | 10 |
Модуль упругости на изгибе, главная ось, минимум, МПа | 3500 |
Модуль упругости на изгибе, латеральная ось, минимум, МПа | 1400 |
Разбухание по толщине за 24ч, максимум, % | 15 |
Плотность, кг/м3 | 630(+/-10%) |
Влажность, % | 5-12 |
Теплопроводность, Вт/(мК) | 0,10 |
Содержание формальдегида, мг/100г | <8мг/100г |
Что касается конкретного использования плит в строительстве домов по каркасной технологии, то в своих отзывах многие строители и владельцы уже готовых жилых домов отмечают быстроту сооружения и простоту монтажных работ.
В отношении эксплуатации тоже заметны неоспоримые преимущества:
- Дома из ОСП панелей не дают осадки по причине легкости материала
- В зимнее время отмечается заметная экономия энергоресурсов, что облегчает бюджетную нагрузку
- Возможность проводить дополнительную планировку помещения без капитального вмешательства в целостность конструкции
Одновременно с этим в отзывах можно заметить и отсутствие негативных качеств, свойственным другим материалам, а именно — подверженность процессу гниения, наличие образований в виде сучков и пустот внутри панели, опасность возникновения возгорания снижена.
На фоне такого объема достоинств отдельные недостатки плит ОСП кажутся незначительными, но их нельзя игнорировать.
В числе основных минусов этого материала — наличие фенола в клеевых смолах, что может негативно сказываться на здоровье. Однако в каждой категории плит, перечисленных выше, содержание этого элемента регламентировано.
Так что при выборе плит для конкретного применения надо ориентироваться на их основное назначение. Например, OSB-3 лучше применять в наружных работах, а для интерьерной отделки рекомендована плита марки OSB-2.
Покраска ОСП панелей
Нанесение красочных материалов на панели ОСП не требует особых условий. Для этой цели могут применяться любые краски по дереву.
Для лучшей сцепки с поверхностью плиты и более длительного периода сохранности можно поверхность панели прогрунтовать.
Для интерьерных работ по панелям можно использовать акриловый лак. С этой же целью используется морилка или водоэмульсионная краска. В отношении всех вариантов отмечаются только положительные отзывы.
В строительстве каркасных домов предлагается несколько различных технологий, получивших название географических регионов, где они разработаны и пользуются спросом. Можно встретить такие наименования, как канадская, скандинавская, финская технология каркасных домов и прочие.
В зависимости от их особенностей имеются определенные различия в проектных решениях и, соответственно, в выборе материалов для строительства. Об основных материалах для строительства каркасного дома вы можете прочитать тут.
Далее вы можете перейти непосредственно к строительству дома по каркасной технологии. Данная статья поможет вам в его возведении.
Видео о производстве ОСП панелей
Фанера из опилок как называется
ОСБ-плита: характеристики, применение, размеры и отзывы :
Ориентировано-стружечная плита по уровню спроса сегодня занимает одно из первых мест на рынке отделочных стройматериалов. У такого элемента, как ОСБ плита, характеристики соединяют в себе основные преимущества натуральной древесины с технологичностью и ценовой доступностью плиточных материалов.
Вафельные плиты – прообраз ОСБ
До середины прошлого века были известны ДС- и ДВ-плиты. Первые из них производятся из древесной стружки (щепы) разной формы и крупности, получаемой на обычных щепо-рубочных машинах, вторые – из древесных волокон, образовавшихся после размола древесины.
Стружка (или щепа) для ДСП всегда получается путем разрезания древесины поперек ее волокон. Рассказывают, что изобретателю новой технологии пришла в голову мысль делать древесную стружку путем срезания её по длине ствола, чтобы она получалась тонкой и широкой, когда он затачивал точилкой карандаш. Для этого были модернизированы традиционные щепо-рубочные машины, применяемые для производства щепы для ДСП.
В результате возник прообраз ОСБ плит – так называемые вафельные, которые появились на рынке стройматериалов в середине 60-х годов прошлого века. Они обладали большей прочностью, чем ДСП, за счет применения однородной тонкой стружки с типовыми размерами 50 х 70 х 0,8 мм. Производилась она из древесины тех пород, которые ранее просто шли в отходы при массовой рубке леса (например, осины).
Как родилась ОСБ-технология
Несколько позже, в 70-х годах прошлого века, стало ясно, что стружку вафельных плит нужно разделять на слои, в каждом из которых ориентировать ее перпендикулярно стружке в прилегающих слоях. Простейшим вариантом такой конструкции стала трехслойная система. А для облегчения технологии ориентирования стружки в определенном направлении ее стали делать длиннее и уже, с типовыми размерами 25х150 мм. Так постепенно к началу 80-х годов прошлого века была разработана новая технология производства древесно-стружечных плит. Сама аббревиатура ОСБ (OSB) возникла от сокращения английского названия «ориентированно-стружечные плиты».
Производство ОСБ плиты
90 % ее объема составляет натуральная, в основном сосновая, древесина, хотя используются и клен, тополь, осина, различные виды березы. После ошкуривания бревен их измельчают до получения плоской стружки прямоугольной формы с типовыми размерами 150х40х0,6 мм, которую укладывают в форму в несколько слоев. В типовой трехслойной плите стружка в наружных слоях ориентируется вдоль длины плиты, а во внутреннем слое – перпендикулярно к ее длине. Высокие для такого материала, как ОСБ плита, характеристики достигаются благодаря тому, что волокна древесины в выровненных в одном направлении и сцепленных между собой плоских стружках придают конструкции прочность натурального дерева.
После укладки слоев их пропитывают синтетическими смолами с добавкой парафиновой эмульсии, придающими плите водостойкость, и прессуют при высокой температуре.
ОСБ-плита: характеристики и основные типы
Сегодня деревообрабатывающей промышленностью производятся четыре основных их вида, различающихся по ряду основных параметров и, как следствие, применяющихся для определенных целей:
1 – характеризуется низкой плотностью и влагостойкостью и предназначена для использования при внутренних отделочных работах, а также в мебельном производстве.
2 – характеризуется повышенной, по сравнению с видом 1, плотностью и прочностью, но такой же низкой влагостойкостью. Предназначена для обшивки несущих конструкций внутри помещений при нормальном уровне влажности.
3 – обладает достаточно высокой прочностью и влагостойкостью. Предназначена для наружной обшивки строительных конструкций при умеренной влажности и дополнительной защите в виде водоотталкивающей пропитки или покраски, а также для любых внутренних ремонтно-отделочных работ.
4 – это ОСБ плита влагостойкая, она имеет высокую прочность и применяется для наружной обшивки строительных конструкций без какой-либо дополнительной защиты. По сравнению с видом 3 стоит вдвое дороже.
На рынке предлагаются также плиты лакированные или ламинированные с одной стороны, предназначенные для многократного использования при изготовлении опалубки. Плита ОСБ на пол имеет соединения типа «паз-гребень» на торцах с двух или четырех сторон.
Какие ОСБ плиты предлагает российский рынок
Известны американский и европейский стандарты таких плит. Первый отличается строгостью экологических требований, показателей прочности, минимальными допусками на габариты. Однако продукция по второму стандарту более влагостойка, и функциональность ее заметно выше. Отличается и сырье: «американские» плиты делаются из древесины лиственных деревьев, а «европейские» — из хвойных пород.
Наибольший сегмент российского рынка занял бренд Kronospan, поставки идут с заводов в Польше и Латвии. Толщина ОСБ-плиты, которую можно найти на нашем рынке, находится в диапазоне от 6 до 30 мм. Так что есть возможность применить ее для любого вида строительных работ. Типовой (ОСБ-плита) размер равен 2500 x 1250 мм.
Преимущества стройматериала
Перпендикулярность направления волокон стружки в разных слоях при однородной ориентации в каждом из них обеспечивают ОСБ-плитам прочность, в два с половиной раза большую, чем у ДСП. Наглядным подтверждением этого является сейсмостойкость домов, построенных по американской технологии с обшивкой их несущих конструкций такими плитами. Во время землетрясений в Калифорнии и Японии они выстояли, тогда как кирпичные постройки частично разрушились.
Не являясь натуральной древесиной, этот стройматериал сохраняет ее цвет и красивую структуру. При этом он избавлен от ее типовых недостатков – влагопоглощения, расслоения и коробления, растрескивания, выпавших сучков и др.
Ниже приведены (по сравнению с традиционными пиломатериалами и фанерой) основные для такого материала, как ОСБ-плита, характеристики и преимущества:
• одинаковость их физико-механические свойств по всему объему при слабой зависимости от влажности;
• влагостойкость: после суточного намокания в воде набухание материала не превышает 10-12% при сохранении плитой целостности и прочности;
• ОСБ-плиты легко режутся и сверлятся, их можно клеить и окрашивать любыми предназначенными для дерева красками;
• способность к удержанию крепежных изделий на 25 % выше, чем у фанеры и ДСП;
• небольшой вес постройки из ОСБ-плит, делающий ненужным подведение массивного фундамента, применение грузоподъемных машин и механизмов, что весьма ощутимо уменьшает себестоимость постройки;
• экологическая и гигиеническая безопасность материала;
• устойчивость к порче насекомыми;
• меньшая стоимость по сравнению с натуральной древесиной и фанерой.
Сферы применения
1. Обшивка ОСБ-плитами несущих конструкций. Строительство частных и малоэтажных домов с обшивкой стен данным стройматериалом ускоряется и удешевляется. При этом плиты могут покрываться любыми облицовочными материалами.
2. Съемная опалубка. Прочность и влагоустойчивость позволяет использовать материал в качестве мелкощитовой опалубки для нескольких десятков циклов.
3. Основа для кровли. ИЗ ОСБ-плит выполняют обрешетку кровельных «пирогов» под шифер, профнастил, натуральную или металлочерепицу. Высокое звукопоглощение этого материала сочетается с высокой стойкостью к ветровым и снеговым нагрузкам.
4. Черновой пол. Плиты могут сплошным настилом укладываться на слой гидроизоляции поверх стяжки или на деревянные лаги. Поверх них укладывается напольная доска, линолеум, ковролин.
5. Напольное покрытие. Уложенные на лаги плиты окрашивают в несколько слоев и лакируют.
6. Изготовление прочной упаковки: ящиков, коробов, контейнеров и т.д.
Плюсы ОСБ-плит
На сленге производителей их иногда называют «улучшенной» древесиной. При сохранении такой же прочности, легкости и простоты в обработке, как у древесины, ОСБ-плиты не подвержены гниению и плесени, не имеют пустот и сучков. Их технические характеристики лучше, чем у любых конструкционных древесных плит и даже фанеры. Поточное конвейерное производство обеспечивает стабильный (что очень важно для такого строительного материала, как ОСБ-плита) размер и равномерность толщины вдоль всей поверхности. Плиты являются отличной звуко- и теплоизоляцией, лучшие их марки не деформируются в воде. Обрабатываются они теми же инструментами, что и древесина. Размеры их позволяют иметь в обшивке стен домов минимальное число стыков, а срок службы стеновых конструкций, обшитых такими плитами, практически не ограничен.
Минусы ОСБ-плит
Однако ничто на свете не совершенно. Не избежала общей участи и ОСБ-плита: отзывы, имеющиеся в Сети, выделяют хрупкость всех типов плит (может быть, кроме ОСБ4), проявляющуюся при транспортировке, когда значительный объём товара портится, еще не дойдя до своего потребителя. Этот материал, хотя и умеренно, но все же поддерживает горение. Отмечается также крайне низкая влагостойкость ОСБ1 и ОСБ2, что, впрочем, отвечает заявляемым производителями характеристикам, а также трудность их мехобработки, особенно при сверлении отверстий. Многие мастера сетуют на то, что крепежные изделия в них не держатся. Впрочем, многие из этих претензий можно отнести на тот счет, что использовались низкокачественные дешевые плиты, изготовленные с нарушением классической технологии.
Безопасны ли ОСБ плиты для здоровья?
Сегодня в Интернете можно нередко встретить негативные о таком распространенном материале, как ОСБ-плита, отзывы, в которых подчеркивается ее негативное влияние на здоровье. Дело в том, что при производстве используются синтетические смолы. Действительно, наружные поверхности и внутренние слои ОСБ плит для скрепления стружек между собой пропитываются веществами, содержащими формальдегид. Их массовая доля в готовом стройматериале может превышать 10%, что делает возможным выделение в окружающую среду токсичных веществ. Это обстоятельство, несомненно, показывает вредность ОСБ-плиты, чем и вызваны существующие ограничения сферы их использования для внутренних работ. Для обшивки внутренних перегородок и стен домов изнутри необходимо использовать специальные экологически чистые марки данного материала, хотя цены у них существенно выше.
Большинство производителей из стран ЕС на сегодняшний день отказались от применения в составе своей продукции формальдегидсодержащих смол. Они перешли на выпуск полностью безопасных плит, маркируемых обычно пометками «ЭКО» или «Green». В любом случае, приобретая ОСБ-плиты для строительства дома, нужно изучить сертификат соответствия и убедиться, что они соответствует классу эмиссии соединений формальдегида не выше Е1 (лучше – Е0).
ОСБ-плиты: уже вчерашний день?
Как известно, научно-технический прогресс неостановим. Вот и вместо привычных нам ОСБ-плит несколько лет назад на рынке появились новые древесно-стружечные QSB плиты.
Они состоят из одного слоя более мелких, специально отсортированных стружек, чем ОСБ. Такие плиты не прессуются, а динамически накатываются, подобно листовой стали. При этом достигается небывалая плотность (порядка 800-900 кг/м3 ), тогда как плотность ОСБ2 и ОСБ3 находится в диапазоне 550- 650 кг/м3. Кроме того, QSB плиты имеют двустороннее покрытие гидрофобизатором.
По прочностным и влагозащитным характеристикам, а также ценовым показателям новый материал оказался примерно эквивалентным плитам ОСБ4. Поэтому сколько-нибудь заметного вытеснения с рынка всем привычных ОСБ3 с его появлением не произошло.
Последним словом в технологиях конструкционных древесных плит стали так называемые древесно-цементные плиты (например, марки Green Board). Основой их (до 60 % массы) являются узкие и длинные древесные ленты («древесная шерсть») и связующее вещество в виде высококачественного цемента. Такие плиты абсолютно негорючи и влагостойки.
Разновидности плит и листов для обшивки стен, пола и потолка
Разновидности плит и листов для обшивки стен, пола и потолка
Какие разновидности плит для строительства, ремонта и обшивки стен, пола и потолка существуют? Их особенности, достоинства и недостатки. Если взять для примера, каркасные дома, то долговечность и внешний вид таких домов напрямую зависят от используемых панелей для внутренней и наружной обшивки. Более того, применение панелей с готовой отделкой или слоем теплоизоляции (панель «сендвич») заметно сокращает и так непродолжительные сроки возведения сборно-каркасного дома.
ДСП
Древесно-стружечная плита изготавливается путем горячего прессования древесных стружек со связующими термоактивными смолами, которые составляют 6-18 % от массы стружки. Смолы экологически небезопасны, так как содержат вредный для человека формальдегид. По содержанию этого вещества ДСП разделяют на классы E1 и Е2. Более экологически безопасен класс E1, он разрешен к использованию в производстве даже детской мебели. Целиком облицованные ДСП-плиты не несут никакого вреда здоровью, вредное воздействие оказывают только открытые кромки. Новые технологии позволяют производить плиты класса Super Е, которые по всем санитарным нормам считаются безопасными. В целом материал отличается достаточно высокой плотностью, низкой стоимостью и простотой в обработке. ДСП обшивают стены, крыши, изготавливают перегородки, полы, используют в качестве основания под линолеум и ковровые покрытия.
ДСП Древесно-стружечная плита
Достоинства ДСП:
- широкая номенклатура цветов, рисунков, толщины;
- легко обрабатывается;
- однородность структуры.
Недостатки ДСП:
- плохо удерживает шурупы и гвозди, особенно при повторной сборке;
- уязвим для влаги;
- содержит канцерогены (например, меламин).
МДФ
Древесная плита средней плотности или древесноволокнистая плита сухого прессования. МДФ от английского (Medium Density Fiberboard). Изготавливается из древесной стружки, перемолотой в муку методом сухого прессования, при высоких температуре и давлении с добавлением вещества лигнин, который содержится в натуральной древесине. Лигнин делает этот материал экологически чистым и устойчивым к грибкам и микроорганизмам. Плиты МДФ бывают толщиной от 3 до 30 мм и ламинируются пластиками, лакируются или облицовываются шпоном. По влагостойкости и механическим характеристикам МДФ превосходят натуральное дерево и ДСП. Также МДФ в 2 раза прочнее и лучше держит шурупы. МДФ используется для отделки помещений, например, в виде стеновых панелей или ламинированного напольного покрытия — ламината, при производстве мебели, корпусов акустических систем. МДФ имеет однородную структуру, легко обрабатывается, очень прочная.
МДФ Древесная плита средней плотности или древесноволокнистая плита сухого прессования
Достоинства МДФ:
- огнестойкость;
- биостойкость;
- высокая прочность;
- лучше, чем ДСП держит шурупы;
- влагостойкость выше, чем у ДСП;
- широкий выбор цветов и рисунков благодаря покрытию пленками и шпоном.
Недостатки МДФ:
- горит с выделением ядовитого дыма;
- пылевидные опилки, образующиеся при обработке и распилке плит, вредны для здоровья.
Гипсокартон (ГКЛ)
По праву считается одним из самых популярных материалов для выравнивания стен, потолков и полов, устройства межкомнатных перегородок и даже элементов декора, таких как арки, колонны, сфероиды, многоуровневые потолочные покрытия и т.д. Основным компонентом гипсокартонных листов служит гипсовый наполнитель и это определяет многие положительные качества стройматериала. Так, гипсокартон химически инертен, его кислотность примерно равна кислотности человеческой кожи, он не содержит и не выделяет во внешнюю среду вредных для человека химических соединений. Стандартная плита на 93% состоит из двуводного гипса, 6% из картона и еще 1% приходится на поверхностно — активные вещества, крахмал и влагу.
Так, хрупкость панелей затрудняет их транспортировку, погрузочно-разгрузочные работы. По этой же причине ГКЛ не может выдерживать значительных физических нагрузок и не рекомендуется для выравнивания полов. Подвесные потолки из гипсокартона могут выдерживать вес не более чем 4 кг на метр квадратный, в то время как натяжные потолки способны нести нагрузку больше 100 кг на эту же единицу площади.
Гипсокартон
Разновидностью или более современной модификацией простого листа гипсокартона служит окрашенный или ламинированный гипсокартон, гипсовинил или гипсолам — гипсокартон цветной, с виниловым покрытием. Принципиально новый материал, имеющий изначально эксклюзивный внешний вид с широким выбором декора. Применяется для внутренней облицовки стен, для зашивки оконных откосов, создания перегородок, витрин и выставочных стеллажей, без дополнительной отделки.
Ламинированный гипсокартон, гипсовинил или гипсолам — гипсокартон цветной, оклеенный виниловым покрытием
Эти экологически чистые негорючие панели представляют собой гипсовую плиту, оклеенную с двух сторон специальным картоном. Имеют идеальную геометрию и используются для устройства внутренних перегородок и подшивки потолков. Поставляются в листах 2700 (3000) х 1200 х 12 мм. Выпускаются специальные марки гипсокартона для влажных (ванная комната) и пожароопасных (стена у камина) помещений. Они окрашены в «сигнальные» цвета — красный и зеленый. Есть гипсокартон и повышенной пластичности (толщина 6 мм, ширина 900 мм) для обшивки закругленных стен. На основе гипсокартона изготавливают панели «сэндвич» с теплоизолирующим слоем пенополиуретана (до 50 мм). Их используют уже для внутренней обшивки наружных стен без последующего утепления и пароизоляции. Это значительно сокращает сроки строительства.
Достоинства гипсокартона:
- экологическая и санитарная безопасность;
- легко обрабатывается: режется, сверлится;
- не горит, но при значительном нагреве разрушается;
Недостатки гипсокартона:
- низкая прочность, хрупкость;
- большая уязвимость для влаги даже влагостойкой разновидности;
- плохо переносит низкую температуру и значительные перепады температур;
- пригоден только для внутренней отделки.
Гипсоплита
Гипсоплиты практичный, современный и экологически безопасный материал, так как изготавливается без использования токсичных веществ из природного гипса, который не проводит электричества и не имеет запаха. Гипсоплита отвечает всем требованиям противопожарной безопасности. Гипсоплита, гипсовая пазогребневая плита (ПГП) является основным материалом при конструировании перегородок, подвесных потолков, различных декоративных выступов. Используется для выравнивания потолков, стен, «зашивки» систем коммуникаций. Гипсоплита бывает влагостойкой и стандартной. Стандартная используется в зданиях с нормальной влажностью. Для сырых помещений предназначены плиты с гидрофобными добавками. Такие плиты легко отличить по характерной зеленой окраске.
Гипсоплита, гипсовая пазогребневая плита (ПГП)
Достоинства гипсоплит:
- экологическая и санитарная безопасность;
- легко обрабатывается: режется, сверлится;
- мало горючий материал, класс горючести Г1
- относительно дешевая.
Недостатки гипсоплит:
- низкая прочность, хрупкость;
- большая уязвимость для влаги даже влагостойкой разновидности.
Гипсоволокнистый лист
Гипсоволокнистый лист (ГВЛ) – это современный экологически чистый гомогенный материал, обладающий отличными техническими характеристиками. Он производится методом полусухого прессования смеси гипса и целлюлозной макулатуры. По своим физическим свойствам гипсоволоконный лист представляет собой достаточно прочный, твердый материал, славящийся также своими огнеупорными качествами.
Гипсоволокнистый лист, благодаря своей универсальности, получил очень широкое распространение в строительной сфере. Применяется для устройства межкомнатных перегородок, стяжек полов, подвесных потолков, облицовки стен и огнезащиты конструкций. Популярностью пользуется ГВЛ для пола, который служит для сборки основания напольного покрытия, а также облицовочный вариант, при помощи которого обшиваются, к примеру, деревянные поверхности, за счет чего повышается их огнестойкость. В зависимости от области применения гипсоволокнистые листы подразделяют на два типа: ГВЛВ (влагостойкие) и ГВЛ (обычные).
Гипсоволокнистый лист. Укладка пола
Достоинства гипсоволокнистых листов:
- ГВЛ по сравнению с ГКЛ легче переносит распиловку в любом направлении, так как однороден по составу;
- Более высокая прочность за счет армирования целлюлозным волокном;
- Повышенная шумоизоляция.
Недостатки гипсоволокнистых листов:
- Менее прочен на изгиб, чем ГКЛ;
- Менее приспособлен для внутренней отделки, чем ГКЛ;
- Необходимость предварительной обработки перед покраской.
Цементно-стружечные плиты
Цементно-стружечные плиты (ЦСП) — идеальный материал для наружной обшивки каркаса и перегородок во влажных и огнеопасных помещениях, служит хорошим выравнивающим основанием для любых напольных покрытий. Имеет твердую и гладкую поверхность, штукатурится и облицовывается плиткой, пилится ножовкой, негорюч, устойчив к влаге и колебаниям температуры. Поставляется в листах 3600 х 1200 х 10 (12, 16, 20 и 26) мм.
Цементно-стружечные плиты
Фанера
Фанера является одним из наиболее распространенных материалов, широко применяемых в строительстве. Производство фанеры происходит путем склеивания нескольких слоев лущеного шпона фенолформальдегидными смолами. Для этой цели, как правило, используют березовый или хвойный шпон небольшой толщины. Выбор данных пород обусловлен их широким распространением в наших лесах: в Европе, Новой Зеландии и некоторых других странах для производства фанеры разных сортов широко используют дуб, клен, граб и даже грушу. Склеивание шпона осуществляется под давлением при повышенной температуре. Образовавшиеся в результате листы охлаждаются, и после непродолжительной вылежки собираются в упаковки по 10 или 20 штук.
В зависимости от древесины и клея, которые используются при производстве фанеры, она классифицируется на:
- фанера повышенной влагостойкости (ФСФ)
- фанера средней влагостойкости (ФК)
- фанера бакелизированная (БФ)
Фанера
Фанера ламинированная — представляет собой облицованную с одной или двух сторон бумагосмоляным покрытием фанеру. Данное покрытие весьма эффективно препятствует проникновению влаги, обладает высокой устойчивостью к стиранию и образованию плесени и грибков, устойчива к коррозии и разрушению. Данный тип фанеры благодаря ламинированию пользуется достаточной популярностью. При помощи ламинирования можно нанести практически любой рисунок или имитацию под: дуб, тополь, клён, березу, орех, сосну и лиственницу.
Фанера ламинированная
Достоинства фанеры:
- высокая прочность на разрыв и изгиб;
- отлично пилится, сверлится и скрепляется как гвоздями, так и шурупами;
- сравнительно недорогой материал.
Недостатки фанеры:
- смолы, используемые при склейке шпона, содержат довольно большую концентрацию фенольных соединений;
- горючесть;
Ориентированно-стружечная плита
Ориентированно-стружечная плита (ОСП — OSB), производимая методом прессования стружки толщиной до 0,7 мм и длиной до 140 мм под высоким давлением и температурой с применением небольшого количества склеивающей смолы. ОСП-плиты в 3 раза прочнее ДСП и МДФ-плит за счет расположения стружки продольно во внешних слоях и поперечно во внутренних. При такой прочности ОСП — материал очень гибкий и отлично используется при строительных и отделочных работах. ОСП-плитами различной толщины (от 6 до 30 мм) обшивают мансарды, потолки, стены, из них изготавливают черновые полы, опалубки, стеновые панели, ограждения и разборные конструкции. На пол под ламинат обычно используют самые тонкие плиты — 6 и 8 мм толщиной, для конструкций и опалубок более толстые — от 10 мм. ОСП-3 — это более прочная разновидность данного материала, используемая при малоэтажном строительстве в условиях повышенной влажности. Также из-за оригинальной текстуры ОСП является излюбленным материалом у декораторов и дизайнеров для отделки интерьеров. Из ОСП получается достаточно эффектное оформление потолка или элементов во встроенной мебели или в стенах.
ОСП Ориентированно-стружечная плита
На ряду с обычными плитами ОСП, есть и ОСП шпунтованная — плита с обработанными торцами паз — гребень, с 2-х или 4-х сторон.
ОСП шпунтованная — плита с обработанными торцами паз — гребень
Достоинства ОСП:
- прочность относительно других применяемых плит;
- влагостойкость выше, чем у ДСП и гипсоплиты;
- широкий размерный ряд;
- дешевле ДСП;
- хорошо держит шурупы, даже при повторном вкручивании.
Недостатки ОСП:
- обрабатывается хуже ДСП из-за неоднородности структуры;
- пыль, выделяющаяся при резке ОСП, раздражает слизистые оболочки носа, глаз.
- содержит формальдегид, особенно его много во влагостойких плитах.
Стекломагниевый лист
Стекломагниевый лист или стекломагнезитовый лист (СМЛ) белый, армированный стеклотканью, на 40 процентов легче ГВЛ, гибкий, прочный, огнеупорный, влагостойкий. Благодаря армирующей стеклотканной сетке СМЛ может гнуться с радиусом кривизны до трех метров. Это качество позволяет применять его на неровных поверхностях. Высокие влагостойкие качества позволяют использовать его в помещениях с повышенной влажностью. На лицевую сторону плиты допускается наклеивание любых отделочных материалов. При толщине листа 6мм он способен удерживать огонь в течение 2-х часов, выдерживает нагрев до 1500 градусов. Толщина листа: 3-20 мм.
Стекломагниевый лист (СМЛ) — универсальный листовой отделочный материал на основе магнезита и стекловолокна. Технология изготовления и состав материала придают ему такие качества, как гибкость, прочность, огнеупорность и влагостойкость. Его качества, позволяют применять его на неровных поверхностях и понижает возможность перелома листа при монтаже и переносе. Кроме того, этот материал экологически чистый, не содержит вредных веществ и асбеста, не выделяет токсических веществ даже при нагревании. В отличие от гипсокартона СМЛ-Премиум класса отностится к трудногорючим материалам (НГ).
Область применения стекломагниевого листа чрезвычайно высока. Как и из гипсокартона, из него можно делать потолки, стены и межкомнатные перегородки. Более того, с помощью стекломагнезитовых листов можно отделывать наружные фасады коттеджей и домов. СМЛ — надежная основа для любого вида отделки. Новый материал идеально подходит для душевых, саун, бассейнов — ведь стекломагниевый лист способен выдерживать высокую влажность, перепады температуры и открытый огонь. На поверхность СМЛ можно наносить самые разные виды шпатлевок, красок, клеев. Можно наклеить обои, алюминиево-композитные панели, шпон, пластик, керамическую, стеклянную или зеркальную плитку.
Лицевая (гладкая) поверхность листов предназначена для окрашивания, наклеивания обоев, ламинирования и нанесения различных видов декоративных текстур без предварительного, окончательного шпатлевания и грунтования всей поверхности материала. Тыльная (шероховатая) поверхность листов предназначена для прочной сцепки при приклеивании штучных облицовочных и декоративных материалов (керамической или кафельной плитки, шпона и т.п.), либо самого материала на стены и пол, склейке листов между собой. СМЛ может крепиться на крепежную систему, как из металла, так и из дерева. А также непосредственно на ограждающую конструкцию при помощи клея.
На ряду с обычными стекломагниевыми листами, в последнее время все чаще стали появляться ламинированные стекломагниевые листы с разнообразным рисунком и толщиной внешего покрытия.
СМЛ Стекломагниевый лист, стекломагнезитовый лист или стекломагнезит
Достоинства стекломагнезита:
- Влагостойкость — не подвергается деформации, не разбухает и не теряет своих свойств;
- Огнестойкость — магнезитные панели негорючий материал;
- Хорошая звукоизоляция — 12мм панель по звукопроницаемости соответствует четырем слоями двенадцати миллиметрового гипсокартонового листа, или кирпичной стены толщиной 150мм;
- Высокая прочность и гибкость — может гнуться с радиусом кривизны от 25 см до 3 метров;
- Легче аналогичных плит из дерева или гипса;
- Низкая теплопроводность, может использоваться как дополнительный утеплитель;
- Может применяться для отделки, как снаружи, так и изнутри.
Недостатки стекломагнезита:
- Более хрупкий, чем гипсоволокнистый лист;
- При шпатлевке стыков необходимо использовать шпатлевки на химических клеях;
- Свойства значительно разнятся в зависимости от производителя и класса СМЛ.
Фибролитовые плиты
Фибролит — это плитный материал, изготавливаемый прессованием специального древесного волокна (древесной шерсти) и неорганического вяжущего вещества (магнезиальное вяжущее). Волокно получают из отходов деревообрабатывающей промышленности, в результате обработки на деревострогательных станках. Один из плюсов фибролитовых плит – небольшой объемный вес. Фибролит отличается огнестойкостью: стружки пропитаны цементом, и при воздействии огня на них образуется лишь копоть. Материал допускает различные варианты отделки, легко крепится к любым конструкциям с помощью гвоздей, саморезов, дюбелей, легко поддается распилке.
Фибролитовые плиты — трудносгораемый, биостойкий материал, который применяют в качестве теплоизоляционного, конструкционно-теплоизоляционного и акустического материалов в строительных конструкциях зданий и сооружений с относительной влажностью воздуха не выше 75%.
Обычные фибролитовые плиты производятся толщиной 3-5 мм с использованием в качестве вяжущего серого цемента. Эти плиты применяются для различного рода термоизоляции, при устройстве кровельного покрытия и оштукатуренных перегородок. Акустические плиты обычно производятся из мелкой древесной шерсти (0,75-2 мм), что улучшает их внешний вид, ничем не закрываются, а также колеруются в цвета, гармонирующие с интерьером или производятся с использованием магнезита или белого цемента вместо серого. Композитная фибролитовая панель — это двух- или трехслойная панель со средним слоем из термоизоляционного материала, например, жесткой пены или минерального волокна (минеральная силикатная шерсть). Толщина среднего слоя обычно колеблется от 15 до 140 мм, хотя внешние слои фибролита имеют толщину от 5 до 20 мм. В этом случае уровень термоизоляции значительно увеличивается.
Фибролитовые плиты
Достоинства фибролитовых плит:
- Легкость монтажа;
- Хороший утеплитель;
- Механически прочный;
- Обширные декоративные возможности;
- Хорошая влагостойкость и огнестойкость;
- Звукоизоляция;
- Гигиеничность, безвредность здоровью человека и окружающей среды;
- Не портят грызуны и насекомые, не гниет.
Недостатки фибролитовых плит:
- Малая прочность на изгиб;
- Значительный вес.
Не стесняйтесь комментировать статью, если у Вас есть чем дополнить этот материал. Если Вы нашли ошибки или несоответствия. Возможно Вы знаете еще какой то аналогичный материал не представленный в этой статье?
Полезное применение прессованных опилок: листы, поддоны и доски
Древесные опилки используют для изготовления транспортных материалов, таких как:
В этой статье расскажем об особенностях и различиях данных материалов, а также о том, как их изготавливают и где применяют.
Поддонами называют транспортную тару, которую используют для перевозки или иной транспортировки различных грузов. Такая тара защищает товары от контакта с погрузчиком и полом, поэтому многократно снижается вероятность испачкать транспортируемую продукцию.
Кроме того, поддон позволяет перегружать довольно большое количество грузов, упакованных в коробки или мешки, а также имеющих прямоугольную форму, с помощью вилочных погрузчиков.
Отличия поддонов и паллетов
Поддоны и паллеты состоят из досок и бобышек, причем доски образуют решетку.
Разница между поддонами и паллетами в том, что последние подходят для транспортировки не только с помощью вилочного погрузчика, но и подъемным краном.
Это расширяет область их применения.
Конструктивно они устроены одинаково, а разница получается за счет более удачного подбора формы и размеров.
Нередко те, кому нужна тара для транспортировки различных грузов, покупают не готовые изделия, а только основной элемент, то есть бобышки, которые являются перемычкой между верхней и нижней решетками из досок.
Именно от бобышек зависит возвышение верхней площадки паллеты над землей. Кроме того, от бобышки зависит надежность удержания гвоздей, которыми соединяют между собой все части поддона.
Чем мягче древесина этой детали, тем менее прочными получаются поддоны и тем выше вероятность повреждения упаковки груза вылезшей из доски шляпкой гвоздя.
Технология изготовления
Все виды поддонов и паллет из опилок изготавливают по одной технологии:
- опилки просушивают, доводя влажность до 8–10 %;
- высушенные опилки смешивают с клеем;
- заполняют этим составом формы;
- прессуют и нагревают;
- окрашивают в нужный цвет.
Просушивание необходимо для того, чтобы опилки сжались до минимального размера и приобрели максимальную прочность.
Ведь чем больше влаги в древесине, тем больше ее размер.
Кроме того, наполненные водой опилки размягчаются, что негативно влияет на жесткость и прочность готового изделия.
Оптимальная влажность составляет 8%.
Чтобы довести отходы распиливания древесины до этого состояния, их помещают в различные сушильные агрегаты, о которых мы рассказывали в этой статье.
Просушенный материал смешивают с различными клеями до образования однородной массы. В качестве клея используют множество различных натуральных и синтетических веществ.
Если производитель нацелен на максимальную прибыль, пусть даже в ущерб безопасности его продукции, то будет применять дешевые смолы, которые выделяют формальдегид.
Этот газ является не только высокотоксичным отравляющим веществом, но и канцерогеном, то есть может вызвать появление раковых опухолей.
Несмотря на то, что даже качественный клей содержит это вещество, разница в количестве и возможности свободного испарения формальдегида.
Допуски по содержанию ядовитых веществ для транспортных материалов гораздо выше, чем для продукции, которая идет на изготовление мебели, поэтому в качестве вяжущего вещества используют тот же клей, что применяют при производстве ДСП (древесностружечных плит).
После смешивания клея и опилок готовую массу загружают в матрицы или специальные агрегаты, которые придают материалу необходимую форму. Плиты делают с помощью прессов, которые вдавливают пуансон в матрицу, благодаря чему плита обретает нужную форму.
Ребра жесткости на ней позволяют экономить материал без потери прочности, благодаря чему снижается стоимость изделия.
Одновременно с прессованием массу в матрице подвергают нагреву, ускоряющему полимеризацию клея.
Таким же образом изготавливают и доски, поэтому единственное отличие в форме матрицы и пуансона.
Бобышки поддонов, они же шайбы или шашки, делают из бруса, нарезая его на куски необходимой длины.
Это позволяет снизить затраты на оборудование, ведь не придется покупать еще один пресс с комплектом матриц и пуансонов.
Нарезанные из бруса бобышки обладают теми же характеристиками, что и изготовленные прессованием в матрицах, и заметно превосходят детали, изготовленные из цельной древесины или полноразмерных отходов.
Для изготовления бруса используют другой тип пресса, в нем шнек подает готовую массу к калиброванному отверстию.
Благодаря избыточной производительности шнека, поступление готовой массы гораздо больше пропускной способности калиброванного отверстия, что и приводит к увеличению давления.
После этого брус проходит по каналу такой же формы и размера, что и калиброванное отверстие, стенки которого нагреты до температуры 140–160 градусов. Это ускоряет полимеризацию клея и делает брус более прочным.
Технология производства одинакова для любого типа изделий.
Разница лишь в способе подачи смеси и форме матрицы/пуансона, которые используют на последнем этапе (для придания продукции необходимой формы).
Мы подготовили несколько ссылок на сайты, где производители предлагают полный комплект оборудования, необходимого для производства этих изделий из опилок, а также краткое описание данного технологического цикла:
Чаще всего такие изделия применяют в качестве транспортной тары, ведь поддон или паллет из опилок обходятся как минимум на 20 % дешевле, чем сделанные из цельной древесины или полноразмерных отходов.
При этом технические характеристики ничем не уступают транспортной таре, изготовленной из дерева.
Поддоны и паллеты применяют для хранения и транспортировки любых сухих не сыпучих грузов, таких как:
- мешки с любым содержимым;
- бочки с любым содержимым;
- прямоугольные или квадратные предметы.
Преимущество паллет и поддонов по сравнению с мешками и коробками в том, что их можно перемещать с помощью различных погрузчиков, это многократно ускоряет процесс погрузки и выгрузки любого транспортного средства.
Кроме того, различные товары невозможно экспортировать в многие страны, если они не установлены на поддоны или паллеты.
Большой популярностью пользуются бобышки из опилок, которые можно использовать для изготовления поддонов нестандартной формы или размера.
Нередко одно предприятие производит бобышки нужных размеров, другое выпускает доски из опилок, а третье собирает из них готовые паллеты необходимой формы.
Фанера
Многие считают, что из опилок также делают фанеру, которую используют для упаковки и транспортировки различных товаров.
На самом деле фанеру делают только из цельной древесины, луща ее на специальных станках, чтобы получить шпон. Затем этот шпон склеивают послойно, чтобы получить фанеру.
Готовый материал отличается очень высокой гибкостью и прочностью на скручивание, ведь в его основе лежат тонкие слои древесины, поэтому и стоимость готовой продукции гораздо выше, чем у любых материалов из опилок той же толщины и размера.
Вместо фанеры из опилок делают плиты сложной формы, которые эффективно заменяют большинство видов паллет и поддонов, но обходятся в 5–8 раз дешевле.
Благодаря сложному профилю и большому количеству ребер жесткости, прессованные плиты из опилок обладают хорошей грузоподъемностью и не уступают по этому параметру деревянной таре, а весят в несколько раз меньше.
Еще одно преимущество плит в том, что при складывании они входят одна в другую благодаря соответствию профилей верхней и нижней сторон друг другу. Такое же соответствие есть у картонных клеток для яиц, поэтому при укладывании их одна на другую они входят друг в друга.
Нередко под термином «фанера из опилок» подразумевают листы низкосортной ДСП, которую изготавливают их мелких древесных отходов.
Стоимость таких листов гораздо ниже, чем у фанеры аналогичных размеров и толщины.
Кроме того ДСП не выносят даже незначительных крутильных нагрузок, поэтому сравнивать их с фанерой некорректно.
Существует также ОСП (ориентированно-стружечная плита), которую тоже иногда называют фанерой из опилок, но и этот материал не имеет с фанерой ничего общего. Ведь по сути оба вида материала являются плитами (листами) из прессованных опилок и стружки, а также других древесных отходов.
Листы из прессованных опилок также используют для создания транспортной тары небольшой грузоподъемности и стоимости.
Для этого к листу ДСП или ОСП выбранного размера снизу прикручивают с помощью саморезов/шурупов или прибивают гвоздями необходимое количество бобышек.
Стоимость таких поддонов заметно выше, чем у штампованных плит, но они все равно обходятся дешевле полностью деревянной транспортной тары. Кроме того, подобная тара идеально подходит для перевозки большого количества грузов мелкого размера, которые просыпаются сквозь обычные поддоны и паллеты.
Основное преимущество поддонов и паллет из опилок в их невысокой цене при аналогичных технических характеристиках, таких как срок службы и грузоподъемность.
По сравнению с деревянной тарой изделия из опилок обладают большей огнеустойчивостью и тяжелей разгораются, а также быстро тухнут без воздействия высокой температуры и открытого огня.
Составные поддоны, благодаря большей прочности материала, из которого сделаны бобышки, гораздо реже выпускают наружу шляпки гвоздей, поэтому перевозка любых товаров на них более безопасна.
Поддоны в форме штампованных плит полностью лишены этого недостатка, ведь они состоят из одной детали сложной формы и в них нет никаких гвоздей.
Цена на поддоны из опилок
Единой стоимости тары из опилок не существует, ведь цену определяет множество факторов, основные из которых:
- стоимость и качество опилок;
- тип клея;
- тип тары;
- форма и размеры;
- соответствие ГОСТ и другим нормативным документам, в том числе международным;
- наличие документов, подтверждающих возможность использовать паллет или других элементов внутри России, на территории СНГ или в других странах.
Поэтому стоимость продукции необходимо уточнять у производителей или продавцов.
Мы подготовили несколько ссылок на сайты, где предлагают такую продукцию. Пройдя по ним, вы сможете связаться с производителями или продавцами и обсудить стоимость различных вариантов поддонов и паллет.
Кроме того, мы подготовили ссылку на сайт, где предлагают не поддоны целиком, а только бобышки:
Видео по теме
Смотрите видео о производстве шашек для поддонов из опилок с помощью специального пресса:
Вывод
Изготовленные из опилок паллеты и поддоны, а также их комплектующие, то есть доски и бобышки, обходятся заметно дешевле деревянных или металлических аналогов. При этом продукция из прессованных отходов распиливания древесины по своим эксплуатационным свойствам ничуть не уступает изделиям из других материалов.
Прочитав статью, вы узнали:
- как создают эти изделия;
- чем отличаются различные технологии;
- где можно купить паллеты и поддоны из опилок.
Вконтакте
Google+
Одноклассники
Плиты для пола: свойства, характеристики, монтаж — Школа пола
Для выравнивания деревянных и бетонных полов используют современные деревянные, а точнее древесноволокнистые плиты OSB. Этот способ позволяет легко и быстро выровнять поверхность пола без трудоемких и дорогих мокрых процессов, ведь плита для пола ГСП монтируется обычными гвоздями или саморезами.
Мы расскажем, что собой представляют полы из OSB плиты и как их следует монтировать.
Для выравнивания поверхности кладется плита на пол osb.
Древесные плиты
Состав и особенности
Плита для пола УСБ состоит из прессованных опилок.
Существует множество различных древесных плит: фанера, МДФ, ДСтП, ЦСП, ЛДСП и ОСП (OSB). Однако в последнее время для строительства черновых полов и выравнивания стяжек и плит чаще всего используют именно OSB, так как плита для пола ОСВ обладает лучшими характеристиками при той же, а часто и меньшей стоимости.
Существуют различные виды плит из древесины.
Аббревиатура OSB расшифровывается как «Oriented Strand Board», что в переводе на русский язык звучит как «ориентированно-стружечная плита». Это название отражает структуру материала и способ его производства: древесину строгают на крупные щепки, длиной до 150 мм и толщиной около 0.7 мм.
Щепки затем прессуют слоями, ориентированными в перпендикулярных направлениях, и в результате получается плита с высокими прочностными характеристиками, причем эти характеристики одинаковы во всех направлениях и по всей площади изделия.
На фото видна многослойная структура стружечной плиты.
Для склеивания щепок и слоев используют различные разновидности смол: карбамидно-формальдегидные, меламиноформальдегидные, мочевиноформальдегидные и фенолформальдегидные. Все эти смолы являются токсичными для человека и способны выделять в атмосферу такие вещества, как метанол, фенол и формальдегид.
Однако современные технологии производства этого материала позволяют создавать изделия с показателем эмиссии формальдегида Е1 и ниже, что вполне приемлемо для жилых помещений.
Также существует технология, где вместо формальдегидной смолы используется метилендифенилдиизоцианат (MDI), который не выделяет вредных веществ. Такие изделия обычно маркируют с приставкой «eco» или «green».
Для жилых помещений лучше использовать экологически безопасные материалы.
Древесностружечная плита для пола имеет такие характеристики:
- Достаточно высокая прочность материала. Физико-механические свойства ОСП-плиты примерно в 2 – 2.5 раза превышают аналогичные показатели ДСтП и сравнимы с характеристиками хвойной фанеры;
- Отличная влагостойкость (OSB-3 и выше). Материал после суточного пребывания в воде набухает не более чем на 15% (чаще ближе к 10), а после высыхания восстанавливает свою геометрию и свойства. Рекомендован для использования во влажных помещениях и на улице;
- Материал не боится биологической коррозии, что для древесины особенно важно, ведь она является традиционным питательным субстратом для насекомых, грибов и бактерий;
- Ориентированно-стружечные плиты очень просты в обработке и монтаже: они легко нарезаются, пилятся, сверлятся, пробиваются гвоздями, шурупами, клеятся, прибиваются скобами. Также следует отметить относительно небольшой удельный вес материала, которые позволяет поднимать плиты на высоту без использования специальной техники;
- OSB-плита для пола из ориентированных щепок лучше удерживает крепежные изделия, по сравнению с ДСтП и фанерой прочность крепежа увеличена на 25%;
- Высокое качество и низкий уровень дефектов. Структура материала однородна по своим физико-механическим показателям, в ней отсутствуют пустоты, сучки, расслоения и прочие дефекты, характерные для других видов древесных плит;
- Плиты OSB можно покрывать лаком, красками, воском, практически всеми видами внутренней и наружной отделки. Это делает их применение в гражданском строительстве особенно привлекательным.
ОСП используют для обшивки различных конструкций и поверхностей.
Важно! Как видим, ОСП имеют множество преимуществ и может применяться в гражданском и жилищном строительстве, что делает этот материал особенно популярным.
К его преимуществам также относится невысокая цена, что часто является основным аргументом в пользу выбора данного материала.
Использование для обшивки полов
Пол из плиты OSB подходит для жилых и даже детских помещений.
Все вышеперечисленные свойства и характеристики позволяют широко использовать стружечные плиты для выравнивания и обшивки полов, причем, с их помощью можно создавать как черновые полы, так и финишные покрытия. Также данный материал удобно использовать для так называемой «сухой» стяжки, когда неровности пола устраняют путем настила на него слоя древесных плит.
Стружечные материалы применяют даже в качестве финишного покрытия пола.
Далеко не всегда имеется возможность выполнить стяжку пола по стандартной технологии с использованием цементно-песчаного раствора и маяков. Материалы для наливных полов порой слишком дороги, а их монтаж своими руками вызывает ряд затруднений у неподготовленных строителей. Другое дело ОСП: дешево, просто и быстро, при этом результат вполне приемлемый и нареканий почти никогда не вызывает.
Для настилки на пол удобно использовать шпунтованные изделия.
Настилка на пол выполняется двумя способами:
- По лагам. При этом на пол сначала крепят обрешетку из деревянного бруса, которую выставляют по уровню, а затем обшивают двойным слоем древесных плит. Способ позволяет наиболее успешно выравнивать поверхность, при этом есть возможность уложить в подпольное пространство утеплитель или звукоизоляцию;
- По «плавающей» технологии. Плиты укладывают прямо на бетонную или деревянную основу, оставляя технологические зазоры между полом и стенами. Для этого способа требуется, чтобы основание было достаточно ровным, и ОСП выполняет функцию звукоизоляции и дополнительного утепления.
Плавающая технология укладки.
Важно! При обшивке пола следует помнить, что материал имеет заметный коэффициент температурного расширения, поэтому между отдельными листами оставляют деформационный зазор не менее 3 мм с каждой стороны.
Чаще всего применяют первый метод, так как он позволяет быстро и легко выровнять пол и сделать хорошую основу для таких напольных покрытий, как линолеум, ламинат или паркет. Поэтому далее мы будем рассматривать именно эту технологию укладки материла.
Лаги позволяют максимально выровнять любой пол.
Важно! Иногда для таких же целей используют плиты на пол МДФ, которые также отличаются неплохими показателями, однако их стоимость намного выше, и они боятся влаги.
ОСП может быть использована как плита для теплого пола. Формат плиты для теплого пола предполагает низкую теплопроводность и достаточную жесткость, и всеми этим требованиям стружечные плиты вполне соответствуют, однако есть одно существенное «но»: при нагревании адгезионная смола будет выделять повышенное количество вредных соединений, что может привести к нежелательным последствиям, поэтому мы рекомендуем применять материал только по прямому назначению.
Монтаж
Работа выполняется простыми инструментами.
Если вас заинтересовала технология выравнивания сухой стяжкой из ОСП, то вам пригодится наша инструкция:
- Вдоль короткой стенки комнаты на пол монтируем брус сечением 50х50 мм с шагом 50 см. Выставляем все бруски по уровню строго горизонтально, для этого используем подкладки из тонкой фанеры, обработанной антисептиком. Далее выкладываем листы для пола и определяем места их стыков с учетом зазоров по 12 мм от стен и по 3 мм с каждой стороны, и монтируем в этих местах ригеля (перемычки, перпендикулярные лагам) из того же бруса;
Укладываем лаги, которые фиксируем к полу дюбелями;
- Начинаем укладку плит толщиной 20 мм на пол. Расстояние до стен – 12 мм, расстояние между листами – 3 мм, все стыки должны лежать на лагах и ригелях, швы смещаем наподобие кирпичной кладки;
Правила укладки листов просты и понятны из схемы.
- Покрываем весь пол, затем укладываем второй слой, но при этом кладем плиты так, чтобы стыки предыдущего слоя перекрывались;
Накрываем пол еще одним слоем, гвозди (саморезы) забиваем через каждые 15 см.
- Зазоры заполняем эластичным герметиком.
Зазоры и щели заполняем герметиком.
Важно! Если используется шпунтованный материал, тогда места стыков проклеиваем монтажным клеем для дерева, а стыки после укладки не герметизируем.
Вывод
С помощью ориентированно-стужечных листов можно быстро и без особых затрат выровнять пол перед финишной отделкой ламинатом, линолеумом или паркетом. Данный материал неплохо себя показал и полностью соответствует заявленным характеристикам, поэтому полы из OSB плиты отлично подходят для укладки финишных покрытий.
стружки и опилки для доброго дела
Производство пиломатериалов – это всегда горы отходов. В зависимости от размеров одни идут на поделки, вторые – на дрова, третьи – на подстилки. Эта статья как раз о третьей категории, самой полезной, утилитарной и практичной. Например, мы бесплатно отвозим опилки и стружку в Реабилитационный центр для животных «ЗОО Дом» города Королев, чем облегчаем жизнь четвероногих питомцев.
Так наше предприятие по изготовлению клееного бруса нашло возможность полезного применения производственных отходов. А их бывает очень много, потому что у нас свои цеха и перед склейкой мы до гладкости выравниваем каждую ламель. Что это значит? То, что после нас остаются ровненькие доски для будущего бруса и множество опилок.
Благодаря нашей инициативе хвостатые питомцы получают не только заботу волонтеров, но и отличные санитарные условия: хвойные остатки прекрасно дезинфицируют клетки животных и впитывают влагу. Лапы и шерсть собак остаются сухими, а сами они – здоровыми! Поэтому, мы надеемся, гораздо быстрее будут находить новых хозяев.
Кроме того, на влажном полу собаки хуже едят и быстро простуживаются. А так опилки прекрасно защищают их от холода, ведь добротный слой древесных отходов – это все равно, что толстенная плита ДСП. Но только в более удобном варианте – сменная и с проветриванием. В общем, такие подстилки отлично подходят для вольеров. Среди их преимуществ:
- мягкость – животным удобно лежать на пружинистом слое;
- безопасность – древесные остатки не выделяют токсичных веществ;
- приятный аромат – смолы и эфирные вещества, запах которых так нравится людям, отпугивают клещей и блох;
- простота утилизации – использованный наполнитель может пригодиться в агрохозяйстве как мульчирующий материал или удобрение.
Это же касается стружки. Она крупнее опилок, поэтому у нее нет пыли, которая может попасть собаке в глаза. Но ее водопоглощающие свойства немного хуже – подобная подстилка больше подходит для сохранения тепла, чем для защиты от влаги.
Мебель из опилок как называется
Автор На чтение 15 мин. Опубликовано
Из чего делают корпусную мебель? Какому варианту отдать предпочтение? Как выбрать качественную фурнитуру? Это основные вопросы, которыми задается потребитель перед покупкой мебели. Ответить на эти и другие вопросы мы постараемся в нашей статье.
МДФ, ДСП и ДВП – в чем отличия и что лучше
МДФ – это мелкодисперсная древесная фракция, из которой изготавливают мебельные плиты методом горячего прессования. Материал сравнительно новый и экологически безопасный. В нем, в отличие от ДСП, не используются формальдегиды и другие клеевые составляющие. Зачастую, это сырьё закупается за рубежом, где стандарты безопасности очень жёстки. Из положительных сторон можно назвать и относительную простоту обработки материала, что позволяет изделиям иметь более сложную форму. Из минусов – относительно высокая стоимость.
ДСП – древесностружечная плита, изготавливаемая, как и МДФ, из отходов деревообрабатывающих производств, а также из цельной древесины относительно дешевых пород. Этот материал известен достаточно давно, с советских времен, и остается любим потребителями за износостойкость и невысокую стоимость. При правильной обработке мебель из ДСП прослужит долгие годы, не выцветет и не деформируется.
ДВП – древесноволокнистая плита, изготавливается из мелкой древесной пыли так называемым «мокрым» способом. Сырьё размачивают и укатывают, а затем просушивают. Толщина ДВП небольшая, поэтому в мебели этот материал используется только для задних стенок шкафов и днищ выдвижных ящиков.
Материалы и способы облицовки мебели
Независимо от того, какую плиту вы выберете для своей будущей мебели, её конечная стоимость будет зависеть ещё и от того материала, которым облицуют МДФ или ДСП. На сегодняшний день самыми популярными можно назвать три варианта: шпонирование (фанерование), ламинирование и кэширование.
Фанерование, или в простонародье шпонирование – это облицовка плиты тонким срезом из натурального дерева. Такой способ позволяет сделать изделие максимально похожим на мебель из цельного массива древесины. Эта продукция будет, конечно же, стоить дороже, чем ламинированная, но выглядеть будет очень статусно и респектабельно. Кроме того, метод вакуумного прессования позволяет буквально обернуть шпон вокруг сложных резных деталей, а значит придать ещё больше натуральности. Однако шпон требует к себе бережного отношения и особого ухода, как и деревянные изделия.
Ламинирование – это нанесение на готовую плиту ДСП или МДФ состава из бумаги и полимеров, которые под воздействием высокой температуры буквально вплавляются в поверхность материала, одновременно приобретая нужную фактуру. Такой способ облицовки считается оптимальным по соотношению цена-качество, т.к. не боится влаги, солнца, перепадов температур и сохраняет первоначальный вид долгие годы.
Кэширование, в отличие от ламинирования, предполагает использование клея. То есть на массив МДФ или ДСП наклеивается готовая пленка с нужной фактурой. Такой способ самый недорогой из перечисленных, но и не самый надежный. Эта облицовка гораздо мягче ламината, а значит, не так устойчива к механическим повреждениям и влажности воздуха. Если для спальни этот вариант вполне приемлем, то для кухни лучше выбрать более надёжное покрытие.
Материалы для обработки кромки мебели
Внешний вид готовой мебели зависит не только от способа облицовки плиты, но и от качества кромочного покрытия. На сегодняшний день производители используют несколько материалов для обработки срезов:
Меламиновая кромка является пережитком прошлого, однако часто используется для мебели эконом-класса. Она представляет собой полоску декоративной бумаги, на одну сторону которой нанесен термоплавкий клей. Специальный агрегат нагревает её и плотно прижимает к срезу. Если бумага будет слишком тонкой, то все изъяны торца, бугорки и ямки, будут видны. Срок службы такого покрытия невелик, к тому же меламин неустойчив к механическим повреждениям. При неосторожном обращении он может крошится и трескаться, что испортит внешний вид изделия.
Кромки из ПВХ (на основе винила) и АБС (на основе акрила) превосходят меламиновые и по толщине, и по долговечности. Эти материалы более современные, а значит безопасные. К тому же, они имеют определенный запас гибкости, что позволяет им держаться на срезе долгий период времени. Такие кромки стоят чуть дороже, чем первый вариант, однако качество их на порядок выше.
ПВХ-профиль – это еще один метод закрыть торцы плит. Для этого в срезе может выпиливаться специальный паз (для Т-образного профиля) или он может просто надеваться на край (если профиль П-образный). Этот способ не обеспечивает герметичности, поэтому для кухонной или ванной мебели не подходит категорически. А вот рабочий или компьютерный стол вполне можно украсить, подобрав профиль контрастного со столешницей оттенка.
Как выбрать качественную фурнитуру
Сплавов, из которых делают мебельную фурнитуру, существует великое множество, поэтому для неспециалиста нет необходимости разбираться во всех этих тонкостях. К тому же, фирмы-производители постоянно улучшают качество своей продукции и патентуют новые составы. Главное, на что стоит обратить внимание при выборе фурнитуры:
- Логотип изготовителя должен стоять на самом видном месте и четко читаться.
- Цвет металла должен быть однородным, без пятен, заусениц, шершавостей, разводов.
- Открытая фурнитура – это прошлый век, лучше отдать предпочтение скрытым механизмам.
- Дверцы при открывании и закрывании не должны скрипеть, стукать, шататься и вообще вызывать какие-либо подозрения.
- Выдвижные ящики не должны греметь, заедать, съезжать в сторону.
- Механизм доводки, при его наличии, обязан срабатывать без нареканий.
Соблюдая эти рекомендации, вы сможете не только выбрать качественную мебель, подходящую по стоимости и функционалу, но и приобрести продукт, который прослужит долгие годы, сохранив товарный вид.
Немного рассуждений о мебельных материалах: ДСП, МДФ, фанера, мебельный щит, пиломатериал, шпон.
Выбор мебельных материалов может казаться сложным. И все же при понимании сути вопроса выбор всегда будет элементарным. Об этом видео. Смотри, задавай вопросы, комментируй …
Сегодня я хочу раскрыть такой вопрос: Чем отличаются материалы, используемые для производства мебели? На сегодняшний день существуют следующие материалы: ДСП, МДФ, фанера, мебельный щит, пиломатериал, шпон. Поговорим конкретно о каждом из них.
Отличие ДСПДСП – это сокращенная аббревиатура от полного названия: древесно-стружечная плита. Современный композиционный материал, полученный путем прессования древесных частиц (опилок и стружек), в качестве связующего вещества используются формальдегидные смолы. Интересный факт из Википедии: “Древесно-стружечные плиты появились в 1940-х годах в США (англ. Chipboard) для временной мебели американских беженцев.” Уместное пояснение, которое еще раз напоминает нам, для чего и для кого первоначально была придумана мебель из ДСП.
Эксплуатационные характеристики ДСП.
Одна (и наверное единственная его положительная характеристика) – это стабильность. Изделия из ДСП сохраняют свою форму, цвет и размеры в обычных комнатных условиях. Это мертвый материал и в сравнении с мебелью из дерева не требует соблюдения относительной влажности воздуха, если только совсем не залить его водой.
Продолжительность жизни мебели из ДСП.
У кого была мебель из ДСП (скорее всего у каждого из нас), тот знает насколько непрочен этот материал. Не смотря на внешнюю монолитность, которая создается тонким слоем пластика (ламинированное ДСП), внутри он состоит из опило и стружек. И по своей плотности ДСП могут отличаться, что сразу видно на спиле.
Рыхлое ДСП не прослужит вам и года: из него сразу повылетают петли, могут сломаться полки от тяжести книг, появляются сколы и т.д. Такая мебель не подлежит ремонту, даже не надейтесь! Если вам повезло и вы приобрели мебель из более качественного плотного ДСП, то она прослужит вам максимум 10 лет. Но только при условии правильной эксплуатации: не бить об углы, не царапать и не поливать водой. Если вы захотите разобрать и повторно собрать такую мебель, то имейте в виду, что на третий раз вы уже не сможете вкрутить саморезы.
Минусы мебели из ДСП.
Немаловажен экологический показатель, который скрыто, но направленно влияет на здоровье потребителей. Виноваты в этом связующие смолы, которые выделяют вредный для человека формальдегид. Предельно-допустимая эмиссия вредных веществ определяется санитарными нормами. Но все ли производители соблюдают данные требования? Низкосортные дешевые плиты иногда превышают ПДК до 40 раз.
За рубежом ( в Европе и США) плиты такого класса уже не выпускаются, а для производства мебели разрешено использовать только сверхбезопасные плиты класса «Super E». Особенно опасна для здоровья новая мебель, из которой еще не выветрились активные формальдегидные частицы. Поэтому при покупке стоит особенно обращать внимание на оклейку всех, даже невидимых снаружи, торцов мебели. Воспользуйтесь своим обонянием и принюхайтесь. Мебель из ДСП с высокой концентрацией формальдегида обладает едким неприятным запахом. Но зачастую, то что стоит в качестве образца – это не всегда, то что привезут к вам домой.
Отличие МДФЧем отличается МДФ (Medium Density Fibreboard – древесно-волокнистая плита) от ДСП?
Его относят к менее токсичным материалам, т.к плиты формуются методом сухого прессования мелкодисперсной древесной стружки при высоком давлении и температуре. В качестве связующего вещества используются карбамидные смолы, модифицированные меламином. Это обеспечивает очень низкую эмиссию формальдегида, сравнимую с эмиссией натуральной древесины. Поэтому его считают более экологичным материалом и широко используют в производстве мебели.
Прочность МДФ превышает ДСП примерно в 2 раза, незначительно увеличивая срок службы мебели. В отличие от древесно-стружечных плит МДФ является влагостойким материалом, особенно если он покрывается лаками и эмалью. Такую мебель практично использовать в ванной комнате, где постоянно высокая влажность.
Кроме этого МДФ может облицовываться пластиком, пленкой или шпоном. Разнообразие цветовых оттенков и эффектов (блеск, перламутр, металлик и т.д.) – впечатляет! Кроме того с помощью специального оборудования деталям из МДФ можно придать любые формы, сделать радиусные дверцы.
Любой из вариантов покрытия имеет свои плюсы и минусы. Поэтому первоначально стоит задуматься о предназначении мебели. В каком виде лучше использовать МДФ зависит от того, где и в каких условиях будет находиться будущая мебель и какие эстетические требования вы к ней предъявляете. МДФ в пленке, пластике или покрытый эмалью выглядит как пластик – холодно и безжизненно. А вот покрытый шпоном – невозможно с первого взгляда отличить от дерева. Поэтому очень часто коммерческие производители используют МДФ в мебели, где частично присутствует и дерево, и МДФ.
Отличие фанерыФанера – традиционный древесный материал, подобие которого находили даже в Древнем Египте. Позже в Греции и Риме мастера склеивали вручную грубый шпон дерева с помощью естественных смол. Промышленное производство фанеры началось лишь в 19 веке, что сделало мебель более доступной по цене и в то же время повысило ее качество.
Современная мебельная фанера получается путем склеивания 3 и более листов специального шпона с помощью карбамидной смолы. Эмиссии свободного формальдегида мебельной фанеры незначительна и сравнима по своим показателям с натуральной древесиной. В России для мебельного производства в основном используют фанеру из шпона березы.
А к примеру, в США можно встретить фанеру из вишни, которая в большом количестве произрастает северо-восточной части страны. Мебель из фанеры выпускается уже с конца 19 века и доказала свое право на существование. Прочность на выдергивание крепежа из фанеры примерно равна прочности дерева. Срок службы мебели из фанеры достигает от 50 до 100 лет. Недаром винтажные образцы 50-х годов становятся уже раритетом и предметом дизайнерских коллекций.
Первые стулья из гнутой фанеры американских дизайнеров и супругов Ray & Charles Eames стали выпускаться с 1941 года и пользовались большой популярностью в США и Европе.
Благодаря своей экологичности и невысокой стоимости мебель из фанеры излюбленным предметом современного интерьера. Из нее делают детскую мебель, кухонные гарнитуры, кресла и самую разнообразную дизайнерскую мебель. Фанера может использоваться в мебели, сохраняя свой естественный цвет березы, или окрашивается в любой цвет, а также шпонируется. Отделка торцов фанеры зависит от дизайна изделия. Их можно оставить открытыми или закрыть кромкой из дерева, зашпонировать, так что не отличишь от дерева.
Мебельный щитМебельный щит – это древесный материал, полученный из деревянных строганных брусков, склеенных между собой по ширине и длине. Изготавливается из массива березы, дуба, бука, хвойных пород разной толщины и размеров. Благодаря высокой прочности и экологичности, идентичной массиву дерева, широкое применение получил в строительстве, отделке и производстве мебели из дерева.
Мебельный щит имеет характерную внешнюю особенность, по которой его сразу можно отличить от массива дерева или фанеры. Своеобразный шахматный узор из срощенных брусков виден даже в готовом изделии, чем выдает свое происхождение. Работа с мебельным щитом требует определенного навыка, так как материал, склеенный из брусков, имеет внутреннее напряжение. Это может привести к деформации (короблению) уже в готовом изделии деталей из мебельного щита. Срок службы мебели из такого щита сравним с мебелью из массива дерева, а также подлежит восстановлению и полной реставрации.
Шпон – это тончайший лист древесины, толщина которого не превышает 3 мм. Натуральный шпон дерева получают путем тонкого среза части поверхности с массива дерева (фанерный кряж), который перед этим проходит специальную обработку. В настоящее время существует большой выбор шпона, полученного из различных пород древесины: дуб, береза, клен, вишня, бук, орех, венге, биболо, габон и т.д. с разных концов света.
В мебельном производстве применение шпона способствует удешевлению готовой мебели и одновременно увеличению дизайнерских возможностей. Теперь, используя фанеру или недорогую березу, можно получить эксклюзивные варианты мебели из экзотических пород древесины.
Наглядный пример искусной работы со шпоном из фото отчета изготовления буфета, дверцы которого декорированы шпоном дуба, наклеенного классическим ромбиком.
Экологичность мебели из шпона
Экологичность такой мебели зависит от применяемых клеев и лаков и полностью лежит на совести производителя. Следует также знать, что мебель с использованием шпона требует соблюдения определенных микроклиматических параметров помещения и не любит излишней влаги. Небольшие дефекты на поверхности шпона поддаются восстановлению. Прочность на выдергивание крепежа будет зависеть от того, что используется в качестве основного материала: дерево, фанера или МДФ. Последний вариант для меня совершенно неприемлем, т.к. имеет самый низкий (не более 10 лет) срок службы и несет лишь внешнюю видимость дерева, не неся в себе по сути ничего более.
Традиционным материалом для изготовления мебели испокон веков было дерево. В мебельное производство оно поступает уже в виде досок и брусков различных размеров, которые и называют пиломатериалом.
Качество мебели из дерева
Качество пиломатериала напрямую влияет на долговечность изготовленной из нее мебели. Наличие дефектов в пиломатериале, таких как сучки и трещины, значительно понижают его качество, нарушая целостность и прочность доски. А высококачественный пиломатериал стоит в несколько раз дороже низкосортного. На качество полученного пиломатериала влияют такие факторы, как сезон рубки, возраст дерева и даже экологичность, т.е. отсутствие токсических загрязнений окружающей среды.
Хороший пиломатериал действительно “на вес золота” и мебель из него будет настоящим эксклюзивным изделием по самой дорогой цене. Поэтому в изготовлении мебели из дерева ремесленники часто используют такие древесные материалы как фанера, шпон и мебельный щит. Это снижает стоимость изделий и ускоряет процесс изготовления, нисколько не ухудшая эксплуатационных характеристик мебели. Настоящего ценителя мебели из дерева не отпугивают страшилки о растрескивании и особых условиях влажности.
Не один из выше перечисленных древесных материалов не способен перенести то, что может перетерпеть дерево. Мой опыт показывает, что даже самые неблагоприятные условия хранения, не способны окончательно убить качественную мебель из дерева. Доказательством служит реальный процесс реставрации старинного письменного стола, восстановление которого стало удивление даже для самой хозяйки.
Иностранцы скупают наши леса за копейки, а россияне радуются новой мебели из опилок и стружек, пропитанных ядом
Диваны, столы, кухонные гарнитуры для отечественного рынка чаще всего делают из древесно-стружечных плит (ДСП). Но дешевая мебель – источник смертельной опасности. Эксперты утверждают: только 20 процентов мебели в стране можно использовать без страха за свое здоровье. 80 процентов древесно-стружечного хлама источают ядовитые испарения, вызывая рак, нервные расстройства, мутации и аллергию.
После 60-х годов практически вся недорогая мебель в России стала изготавливаться из прессованной стружки – в стране шло массовое строительство жилья, «обстановки» требовалось много. Технологию производства ДСП мы переняли у Запада. Тогда-то и появилась горькая шутка: только у нас заборы делают из дерева, а мебель из опилок.
Сегодня Россия – крупнейший экспортер круглого леса, более 40 млн. кубометров древесины ежегодно уходит за бугор. Китайский городок Маньчжурия на границе с нашим дальневосточным регионом превратился в склад: огромная территория завалена деревом – легальным и нелегальным.
– Весь мир скупает российские леса по дешевке. Доходов от экспорта не хватает, чтобы покрыть расходы на защиту зеленых массивов от пожара, вредителей, «черных» дровосеков, – сетует эксперт Россельхознадзора Владимир Попович . – В 2000 году я выступал за увеличение таможенных пошлин на вывоз круглого леса, но после вступления в ВТО Россию вынудили практически даром отдавать лесное добро. Сейчас идет преступное разбазаривание ресурсов страны, хищническим методом валят леса, лишь бы деньги «срубить». Только в Китай мы отправляем 12 млн. кубометров, он создает у себя запасы российского леса, чтобы не расходовать собственные ресурсы. Мы же стратегических запасов не делаем. Наша древесина возвращается на родину в виде евровагонки и товаров, изготовленных из отходов переработки нашей же продукции.
Деревянные опилки — использование и применение
Опилки – это наиболее доступное и бюджетное сырье с широким спектром использования. Это измельченная стружка бежевого цвета, частицы мелкой фракции, которые образуются в результате распила древесины. Отметим, что опилки не следует путать со щепой, ведь их получают специально.
Свойства опилок
Деревянные опилки обладают малым весом. Их насыпная плотность составляет примерно 220-580 кг на кубометр, все зависит от уровня влажности (стандартные показатели — от 8% до 15% и больше). Размеры не превышают 50 мм, а коэффициент парусности в сухом виде достигает 0,13-0,8 единиц.
В составе опилок содержится примерно 27% лигнина, который отвечает за одеревенение, а также 70% целлюлозы, гемицеллюлозы (фактически углеводов). Количество химических компонентов составляет:
- азот — 0,1%
- водород — 6%
- кислород — 44%
- углерод — 50%.
Основные показатели, различия и характеристики измельченной древесины обозначены в ГОСТе 23246-78, который регулирует этот тип сырья. В этом же документе прописаны главные термины и определения этого материала.
Это сырье можно назвать самым:
- экологичным. Опилки не вызывают аллергии, не дают вредных выбросов, являются абсолютно натуральными
- дешевым. Зачастую приходится платить только за доставку, потому что большая часть пилорам отдает опилки даром, считая их отходами
- теплосберегающим. Опилки прекрасно изолируют помещение от мостиков холода. По этому параметру он не хуже минераловаты.
Использование древесные опилок
Самым простым и незамысловатым способом можно назвать сжигание, иначе говоря, утилизацию. Однако в отличие от непосредственной утилизации, когда опилки сжигают без извлечения каких-либо полезных свойств, сегодня древесные опилки применяют как твердотельное топливо. Использование опилок, особенно прессованных, популярно вследствие их небольшого объема. Прессованные опилки очень удобны в транспортировке.
Востребованными опилки являются и в садоводческом хозяйстве. В сельском хозяйстве опилки применяются довольно часто. Они – ценное удобрение, которое улучшает качественные показатели почвы. Кроме этого, их используют для мульчирования. Ими посыпают почву в местах посадки рассады. Все это положительно отражается на росте растений. Опилки задерживают испарение жидкости, являются защитой от перепада температур, предотвращают размывание почвы, а также угнетают прорастание сорняков. На опилках довольно часто выращивают разные грибные культуры, такие как вешенки или шампиньоны.
Применение опилок в строительной отрасли также весьма востребовано. Их них создают древесно-стружечные плиты (ДСП) и древесно-волокнистые плиты (ДВП или МДФ). Из таких плит создают разнообразные предметы мебели. Также, после прессования с клеем, получаются детали наиболее причудливой формы. Стоимость таких изделий существенно ниже, чем изделий из цельного дерева.
В целлюлозно-бумажной промышленности также используются древесные опилки. Из опилок создают бумагу, картон и прочие лесобумажные материалы. Лиственные и хвойные опилки помогают сохранить гектары лесных массивов, предотвращая массовую вырубку деревьев.
Низкий уровень плотности и легкость, иначе говоря «воздушность», делает опилки востребованными в качестве упаковочного материала. Наполнитель из опилок дает возможность уберечь хрупкие предметы, к примеру, бутылки или вазы, от повреждения в процессе перевозки.
Строго определенные сорта опилок используются для копчения мяса или рыбы. Отличным вариантом для копчения являются сухие отходы ольхи, дуба, бука и любых фруктовых пород. Их используют отдельно друг от друга или смешивают несколько сортов, чтобы добиться более изысканного вкуса.
Отопление опилками
Рассказывая о применении древесных отходов в качестве горючего для отопительных систем, многим видится довольно легкий процесс: взять мешок, засыпать сырье в топку, поджечь и получить нужную температуру. Тем не менее, не стоит забывать, что не все опилки могут стать топливом. Основные параметры, которые нужно принять во внимание:
уровень влажности
плотность сырья.
От этих двух характеристик зависит эффективность работы котла. Исследования показали, что:
- мелкие невысушенные опилки из ленточной пилорамы имеют плотность примерно 250 кг/м3. Их расход на 1кВт мощности котла достигает примерно 0,5 кг в час, в процессе непрерывной работы
- пористая высушенная стружка от фрезерного станка отличается плотностью от 100 до 150 кг/м3. Расход такого материала составит 0,25 кг в час на 1кВт. Следовательно, для наиболее эффективной работы котла нужно приобретать наиболее сухое сырье, потому что его нужно намного меньше, чем влажного.
Однако, помните, что самым уязвимым местом всей системы отопления, построенной для применения сыпучих отходов деревообрабатывающего производства, является место для хранения топлива. Котел, имеющий мощность 25 кВт в не очень холодную зиму ежедневно нуждается примерно в половине кубометра опилок, поэтому понадобится регулярный подвоз топлива, либо довольно большой склад.
Вышеперечисленные советы касались только отопления с применением сыпучего сырья. Но ведь сегодня имеются технологии, позволяющие сделать топливо компактным, путем прессования стружки в небольшие брикеты.
Прессованные дрова из опилок в процессе горения выделяют такое же количество энергии, как и цельная древесина равного объема. В тоже время стоимость подобных прессованных брусков существенно ниже, чем дров. Учитывая еще и легкость перевозки, такое топливо получается предпочтительнее использовать. Брикетирование чаще всего осуществляется на тех же предприятиях, которые занимаются утилизацией отходов деревообработки.
Невзирая на тот факт, что деревообрабатывающая отрасль, а также бизнес по переработке древесных отходов в России развит давно, ниша все еще не заполнена. Разработано множество методов по переработке опилок, щепы, коры и прочих отходов. Переработка опилок использует лишь 50% имеющегося сырья, а на территории Сибири еще меньше – 35%. Вместе с тем остатки лесосечения и лесопиления вообще не перерабатываются и не используются. При изготовлении мебели используется примерно 45% древесных отходов. Следовательно, начинать бизнес в этой области сегодня является выгодным вложением.
Таблица плотности щепы и опилок в зависимости от породы дерева
Насыпная плотность свежеотгруженной технологической щепы | Насыпная плотность свежеотгруженных древесных опилок | |||
Порода дерева | Плотность (кг/м3) |
Предел плотности (кг/м3) |
Плотность (кг/м3) |
Предел плотности (кг/м3) |
Дуб | 292 | 248-371 | 227 | 193-288 |
Акация | 277 | 234-288 | 215 | 182-225 |
Граб | 273 | 266-286 | 213 | 207-223 |
Ясень | 270 | 187-342 | 210 | 146-266 |
Рябина (дерево) | 262 | 248-320 | 204 | 193-249 |
Яблоня | 259 | 237-302 | 202 | 185-235 |
Бук | 244 | 223-295 | 190 | 174-230 |
Вяз | 238 | 202-295 | 185 | 157-230 |
Лиственница | 239 | 194-239 | 186 | 151-186 |
Клён | 236 | 205-248 | 183 | 160-193 |
Берёза | 234 | 184-277 | 182 | 143-216 |
Груша | 241 | 211-256 | 188 | 164-199 |
Каштан | 234 | 216-259 | 182 | 168-202 |
Кедр | 205 | 202-209 | 160 | 157-162 |
Сосна | 187 | 112-274 | 146 | 87-213 |
Липа | 184 | 158-288 | 143 | 123-224 |
Ольха | 180 | 169-209 |
140 |
132-162 |
Ива | 176 | 167-212 | 137 | 129-165 |
Осина | 169 | 166-198 | 132 | 129-154 |
Ель | 162 | 133-270 | 126 | 104-210 |
Верба | 162 | 151-180 | 126 | 118-140 |
Орех лесной | 155 | 151-162 | 120 | 118-126 |
Орех грецкий | 202 | 176-212 | 157 | 137-165 |
Тополь | 153 | 140-212 | 119 | 109-165 |
Пихта | 148 | 126-216 | 115 | 98-168 |
типы и технология изготовления своими руками
Многие люди хотят узнать больше об изготовлении блоков из опилкобетона своими руками. Главная проблема в том, что информации по данному вопросу крайне мало, хотя многие энтузиасты уже довольно долгий срок возводят из подобных блоков здания и загородные дома, ведь компоненты, которые требуются для производства продукта, не являются дефицитом. В данной статье мы рассмотрим нюансы и тонкости изготовления опилкобетона собственноручно, а также виды, характеристики и пропорции опилкобетона.
Опилкобетоном называют изделие, которое изготавливают из смешанных в разных пропорциях песка, опилок, цемента и извести. Данный строительный продукт относят к типу легких материалов для строительства. Придуманы блоки во второй половине ХХ века, однако популярность обрели лишь в конце века.
Так как блоки из опилкобетона и извести отличаются большим числом санитарно-гигиенических достоинств, их позволяется применять для строительства совершенно разных типов сооружений, например для детей либо медицинских целей.
На блоках можно производить самую разную механическую отделку, ведь они практически не поддаются деформации. Не редко данный материал путают с блоками из арболита. Однако изготовление этих материалов происходит из разных компонентов.
Какими характеристиками обладают (плюсы и минусы)?
Главные свойства в опилкобетоне, которые важны потребителю:
- Опилкобетонные блоки имеют весьма низкую стоимость.
Экологичность. При производстве данного блока участвуют лишь экологически чистые и органические компоненты – цемент, опилки, песок. С помощью своих составляющих, данный продукт создает отличный микроклимат внутри помещения.
- Огнестойкость. Из-за особенной технологии производства, изделия получаются негорючими. Получается это потому, что опилки закрыты цементной оболочкой. К тому же несущие свойства не меняются при воздействии высоких температур.
- Паропроницаемость. Благодаря составу в блоке, готовый материал отличается повышенными показателями звукоизоляции и паропроницаемости.
- Морозостойкость.
- Теплотехнические показатели. По причине высоких параметров теплоизоляции, стена из опилкобетона получается более теплой, нежели кирпичная стена толщиной в 2 раза больше.
- Прочность. Так как блок имеет в своем составе фиброподобные компоненты, продукт отличается своей повышенной прочностью. Данный параметр выше, чем у аналогичных строительных материалов.
- Цена.
Главным минусом данного изделия можно назвать то, что он поглощает влагу. Однако этот нюанс поддается решению, ведь фасад можно покрыть водоотталкивающими растворами. А вот изнутри опилкобетон покрывается особыми гидроизоляционными смесями. Еще одним недостатком является то, что в качестве главного компонента не все опилки подходят.
Вернуться к оглавлениюТипы опилкобетона
Применительно к блокам существует различная классификация. Например:
- теплоизоляционный тип, обладающие плотностью 700 кг на 1м3;
- конструкционный тип, обладающий плотностью 1000 кг на 1м3.
Также существует классификация, согласно плотности блоков:
Самым высоким показателем плотности отличается тип М5. Их используют при монтаже цоколя и стен загородных домов. Материалы типа М10 используют для восстановления стен и подвалов. А вот для отелочных операций и установки перегородок отличным выбором будет тип М15 либо М20.
Вернуться к оглавлениюКак изготовить?
Производство опилкобетонных блоков абсолютно не тяжелое дело, по данной причине все чаще потребители выполняют данный процесс в домашних условиях. Важно лишь четко придерживаться технологий и рекомендаций.
Вернуться к оглавлениюПодготовка материалов и инструментов
Одним из основных достоинство материала является то, что опилкобетонные блоки своими руками сможет сделать любой человек, нужно лишь запастись самым необходимым. В перечне нужных материалов и инструментов, чтобы приготовить смесь в домашних условиях, значатся:
- древесные опилки;
- цемент;
- речной песок;
- глина;
- вода;
- деревянные доски;
- толь;
- стержни из стали с резьбой;
- специальные гайки;
- стальной лист;
- оборудование для трамбовки бетонного раствора;
- промышленный миксер либо бетономешалка;
- пленка из полиэтилена;
- строительное сито;
- лейка;
- известь;
- упаковка гвоздей;
- мастерок.
Создание формы для блока
Формы изготавливают из доски или приобретают готовые.Чтобы изготовить состав и сформировать блоки, необходимы специальные формы. Если необходимо изготовить продукт большого веса, то секцию рекомендуют выполнять разборной. А вот для изделия небольшого веса либо размера лучше использовать ячеистые секции.
Опалубка формируется из деревянных досок. Изнутри секции выстилаются стальными листами. По причине наличия стального покрытия, формы отличаются высокой гидроизоляцией. Ведь при заполнении форм составом, дерево не должно поглощать воду из бетонной смеси. Плюс ко всему, из созданных таким образом секций легче вытаскивать готовое изделие.
В случае же применения не стальных секций, перед заливкой замешенного состава и по ходу формирования изделий, форму следует постоянно поливать.
Опилкобетон ни в коем случае не должен высыхать раньше положенного срока. Во время конструирования секций стоит взять во внимание одну тонкость. Когда состав подсыхает, он подвергается усадке, соответственно, изделие в итоге получается меньшего объема. По данной причине, стоит при конструировании форм учитывать этот нюанс и выполнять работу с запасом около 10%.
Готовые формы закрепляют на специальных поддонах из металла, которые посыпают небольшим количеством деревянных опилок. В случае формирования отверстий в бетоне, в форму устанавливают специальные толи. Если необходимо приготовить большое количество материала, например, 1м3 лучше сформировать несколько секций.
Вернуться к оглавлениюСмешивание компонентов
Замешивание состава для формирования строительного изделия вручную весьма трудно, так как вес смеси немаленький. По этой причине рекомендуется применять промышленный миксер либо бетономешалку.
Сначала необходимо высушить древесные опилки и просеять их сквозь специальное строительное сито. Далее происходит смешивание песка, опилок и цемента. Следующим шагом будет добавление в рецепт особого состава извести. Такую известь еще называют строительным тестом.
Готовый состав необходимо хорошо размешать, а потом добавить воды. Ее вводят при помощи лейки, маленькими дозами. На всех этапах полученный рецепт хорошо размешивают.
Вернуться к оглавлениюУкладывание и трамбовка раствора
Изготовление стеновых блоков с помощью станка Блокмастер.Если при замешивании не было отступлений от рецепта и технологий, то при зажатии раствора в руке должен получаться сгусток. Это означает, что раствор был приготовлен без ошибок. Далее можно приступить к укладыванию раствора в формы. Не советуется медлить, так как через пару часов все начнет засыхать. При наполнении в секции, важно тщательно утрамбовать состав, дабы не возникли воздушные прослойки внутри.
Вернуться к оглавлениюСушка
Изделия находятся в форме примерно 3 дня. Готовность проверяют при помощи надавливания на поверхность гвоздем. При отсутствии повреждении продукт можно вытаскивать и оставлять на обсушку. Обсушка длится около недели. Готовый материал должен быть ровным и без дефектов.
Вернуться к оглавлениюПрименение блоков из опилкобетона
Данный материал отличается своей универсальностью. Его используют для возведения зданий разного назначения, фундаментов, стен, оград и много другого.
Вернуться к оглавлениюЗаключение
Для местности, где в избытке имеется такой основной компонент, как древесные опилки, идеальным выбором для возведения дома будет опилкобетон. Изделие славится своими характеристиками, стоимостью и легкостью самостоятельного производства.
Жилье, построенное из данного строительного материала, будет радовать своих хозяев не один десяток лет, и при этом не утратит ни одного из своих преимуществ.
ДСП — обзор
3.10.4.2 ДСП
Ежегодно в Европе производится около 28,4 млн. М 3 древесно-стружечных плит в основном для мебели и строительства (Klímek et al. , 2016). Дерево является основным сырьем, используемым с этой целью, хотя возможность использования недревесных альтернатив изучается в течение многих десятилетий. В последнее время многие факторы, в том числе нехватка древесины, экологическая осведомленность и низкая стоимость недревесных материалов, стимулировали не только интенсификацию этих исследований, но и серьезное влияние на промышленность.
В 2005 году по крайней мере 30 промышленных предприятий по всему миру интегрировали использование недревесных лигноцеллюлозных агрегатов в производство древесностружечных плит (Bektaş et al. , 2005). Сегодня, хотя техническая осуществимость недревесных древесностружечных плит является общепризнанной (Bajwa et al. , 2015), необходимы дальнейшие исследования, чтобы полностью понять, как внутренние свойства сырья могут способствовать повышению общих характеристик разработанных материалов. .Подавляющее большинство примеров разработок недревесных древесностружечных плит сосредоточено на использовании различных видов натуральных волокон. Это согласуется с тем фактом, что волокна вносят важный вклад в улучшение механических свойств плит. Волокнистые материалы сельскохозяйственных культур предпочтительны из-за их доступности и легкости доступа. Примерами являются солома (из пшеницы, ячменя, риса и т. Д.), Хлопковый джин или жмых, волокна кокосового волокна и кенафа или банана. Были проведены некоторые исследования, в которых оценивались растения, богатые растительной сердцевиной; тем не менее, редко можно найти примеры использования изолированной растительной сердцевины при производстве древесностружечных плит.
Хорошо известно, что размер и форма частиц влияют на свойства древесностружечных плит. Агрегаты сердцевины растений имеют тенденцию образовывать довольно сферические частицы (Magniont, 2010; Palumbo, 2015, 2015a, b). Как правило, более сферические частицы положительно влияют на внутреннее связывание ( IB ), но пагубно влияют на MOR и MOE, которым больше выгодны более длинные частицы или волокна (Bajwa et al. , 2015; (Klímek et al. al. , 2016) .Действительно, наличие растительной сердцевины, как сообщается, оказывает негативное влияние как на MOE, так и на MOR (Balducci et al., 2008 г .; Klímek et al. , 2016).
С другой стороны, когда растительная сердцевина измельчается вместе с волокнистыми тканями растений, получается смесь сферических и удлиненных частиц (Nozahic et al. , 2012). Такие смеси не могут компактно укладываться в плиты, что резко снижает плотность и IB (Bajwa et al. , 2015). Такой недостаток может быть компенсирован уменьшением размера частиц, увеличением целевой плотности древесностружечных плит, уменьшением толщины плиты (Klímek et al., 2016) или эффективное удаление растительной сердцевины перед формированием доски.
Salvado et al. Компания (2003) произвела экспериментальные древесноволокнистые плиты без связующего на основе мискантуса ( Miscanthus sinensis ). После уборки стебли мискантуса очищали и измельчали. Стружку взорвали паром с помощью процесса термомеханического водного пара в реакторе периодического действия для получения пульпы. Полученный материал сушили, слегка размалывали и использовали для производства древесноволокнистых плит. Были определены предварительная обработка и условия прессования, которые оптимизируют физико-механические характеристики.Полученные плиты показали довольно хорошие результаты: модуль упругости до 7630 МПа, MOR до 61 МПа, внутреннее сцепление до 4,1 МПа, набухание по толщине всего 2,5% и водопоглощение всего 8,9%. Средняя плотность досок составила 1240 кг / м 3 . Ниже 1100 кг / м 3 плиты не соответствовали требованиям MOR, установленным в EN 31094.
Bajwa et al. (2015) оценила возможность использования рогоздов для производства древесностружечных плит для коммерческого использования.ДСП на основе соломы и рогоза, скрепленные 3% полиметилендифенилдиизоцианата ( pMDI ), были изготовлены с использованием пресса с горячей плитой (190 ° C и 1,54 МПа в течение 420 с). Заданная плотность поддерживалась на уровне 480 кг / м 3 , а доля рогоза и пшеничной соломы варьировалась между 100%, 50% и 25% для получения четырех различных рецептур. Рогоз (как стебли, так и листья) и солома использовались в виде щепок размером от 2 до 6 см. Было обнаружено, что заделка рогоза привело к улучшению общих свойств по отношению к контролю 100% соломы.Однако не самые лучшие результаты дали и экземпляры 100% рогоза. Наилучшие результаты были получены для смесей, состоящих из 70% рогоза и 25% соломы, которые продемонстрировали превосходную среднюю жесткость на изгиб (MOE 446,3 Н / мм 2 ), прочность на изгиб (MOR 17,95 Н / мм 2 ) и внутреннее сцепление. , а также меньшее водопоглощение и набухание по толщине. Кроме того, разброс результатов измерений был ниже, чем для остальных составов. Слабое связывание между частицами соломы из-за наличия кутикулярного воскового слоя было предположено причиной плохих результатов, полученных для древесностружечных плит на основе соломы, в то время как плохие результаты, полученные для 100% образцов рогоза, были объяснены потерей плотности упаковки случайно организованные частицы.По мнению авторов, использование смесей заполнителей рогоза и соломы для производства древесностружечных плит возможно, и следует ожидать лучших результатов, если содержание влаги и размеры частиц двух заполнителей совпадают.
Binici et al. (2016) разработал композиты на основе кукурузы и проанализировал влияние размера частиц и соотношения матрица / заполнитель на термические, механические и звукоизоляционные свойства плит. Кукурузные початки измельчали с помощью молотка и просеивали до частиц размером от 1 до 1 мкм.6 и 6,3 мм и смешанный с эпоксидной смолой, добавленный в пропорции 50% и 75% и прессованный в течение 1 мин при комнатной температуре и переменном давлении (от 0,07 до 0,27 МПа). Полученные материалы имели плотность от 250 до 410 кг / м 3 и теплопроводность от 0,159 до 0,075 Вт / мК. Было обнаружено, что давление является основным движущим фактором, влияющим на анализируемые свойства: более высокое производственное давление привело не только к более высокой плотности и, следовательно, к лучшим механическим свойствам, но также к более высокой теплопроводности и звуковой проводимости.
Klímek et al. (2016) в качестве сырья для производства использовали два растения с высоким содержанием сердцевины, подсолнечник ( Helianthus annuus ) и топинамбур ( Helianthus tuberosus ), а также третье недревесное растение, чашечное растение ( Silphium perfoliatum ). ДСП. Смолы MDI и UF использовались в качестве связующих веществ. Растительный материал измельчали с помощью молотка и просеивали для получения агрегатов размером 5 и 1,24 мм. Было проанализировано соотношение сторон (отношение длины / ширины) агрегатов.В то время как топинамбур и чашечное растение образовывали довольно удлиненные частицы, частицы подсолнечника были «кубиками», вероятно, из-за меньшего количества волокнистых тканей и / или более низкого одревеснения пучков волокон. Разброс по размерам в заполнителях оказался выше, чем в древесной щепе. Агрегаты смешивали со смолами в барабанном смесителе с использованием распылительной насадки. MDI был добавлен в количестве 4% и 6%, а UF — в количестве 8% и 12%. Маты предварительно прессовали вручную перед горячим прессованием при 200 ° C и 3,2 МПа в течение 100 с до расчетной плотности 600 кг / м 3 , что является обычной плотностью в мебельном производстве.Между тремя используемыми видами сырья не было обнаружено небольших различий, хотя плиты на основе чашечных растений дают немного лучшие результаты. Напротив, тип и количество связующего играют более решающую роль. Наиболее благоприятные результаты были получены с MDI 6%. Хотя полученные плиты соответствовали механическим требованиям класса EN 312 P1 (использование в сухих условиях), их характеристики (измеренные с точки зрения MOR, MOE, IB, разбухания по толщине и водопоглощения) были хуже, чем у обычных древесно-стружечных плит.
Bektas et al. Компания (2004) разработала трехслойные ДСП из стеблей подсолнечника ( Helianthus annuus ) и древесины тополя ( Populus alba ). Соотношение частиц древесины или подсолнечника составляло 100%, 75%, 50% и 25%. Смеси заполнителей, просеянные на 1,5 мм для среднего слоя и 0,8 мм для поверхностного слоя, были связаны с UF (9% для среднего слоя и 11% для поверхностного слоя) и катализатора (1% хлорида аммония). горячего прессования (24–26 МПа и 150 ° C в течение 7 мин) для формования ДСП конечной плотностью 700 кг / м 3 .Были проанализированы свойства, связанные с влажностью (набухание по толщине и водопоглощение), механические свойства (внутренняя связь, модуль упругости и MOR) и способность удерживать винты панелей. Все полученные древесно-стружечные плиты соответствовали требованиям, установленным в стандарте EN 312 для общего использования. Однако производительность всех плит со стеблями подсолнечника была ниже, чем у 100% образцов древесины тополя. Композит из стеблей подсолнечника показал худшие характеристики.
Balducci et al. (2008) отобрал различные части сельскохозяйственных культур, богатые растительной сердцевиной, такие как подсолнечник, топинамбур, мискантус, стебли кукурузы и костры конопли, с целью производства легких древесностружечных плит. Однослойные и трехслойные древесно-стружечные плиты, связанные с 6% pMDI и UF смолами, характеризовались механическими и влагозависимыми свойствами. Ориентиром послужили древесно-стружечные плиты из дерева. Растительный материал был разрезан и обработан молотком для получения агрегатов.Сердцевина и коры использовались вместе. Типичный размер частиц не упоминается; однако авторы сообщают о важных различиях в форме и плотности полученных частиц. Агрегаты смешивали со смолой и прессовали до целевой плотности 400 или 600 кг / м 3 . Было обнаружено, что плотность является основным фактором вытяжки, влияющим на исследуемые свойства. Легкие плиты не соответствовали требованиям P2 (EN 312, плиты для внутреннего использования, включая мебель, в сухих условиях), в отличие от большинства плит плотностью 600 кг / м 3 , которые соответствовали таким требованиям.При одинаковых плотностях и составах плиты, склеенные pMDI, дают лучшие результаты. Существенных различий между однослойными и трехслойными ДСП по механическим свойствам не обнаружено. В тех же условиях доски топинамбура имели более высокий IB, чем остальные материалы, в то время как стебли кукурузы показали самый низкий IB.
Что такое ДСП? | Интернешнл Тимбер
Несмотря на то, что ДСП с годами приобрела популярность и их можно найти в большинстве престижных мебельных магазинов, многие люди до сих пор не знают, как они сделаны.
В этом руководстве мы углубимся в историю производства древесины и исследуем использование и преимущества ДСП в современном строительстве.
Немного истории
Первой альтернативой натуральному дереву была «современная фанера», изобретенная в 19 веке. Фанера изготавливается из тонкого шпона массивной древесины, скрепленного клеем. Однако к концу 1940-х годов для производства фанеры по доступной цене не хватало древесины — именно тогда ДСП стало популярной альтернативой.
ДСП, также известная как ДСП, была гораздо более доступной в то время, поскольку она изготавливалась из комбинации отходов, таких как строгальные стружки, обрезки или опилки, и древесной щепы, полученной механическим способом. Чипы склеиваются, а затем под действием тепла сжимаются до крупной формы. Затем его сушат и разрезают на кусочки разного размера для продажи.
Как это сделано
По сути, ДСП — это тип древесины, изготовленной из прессованных древесных частиц, но мы более подробно описали основные этапы производства ниже:
- Стружка: Перед рубкой бревна, возможно, придется окорить, если это еще не сделано в лесу, чтобы избежать затупления ножей рубильной машины.После удаления коры древесина разрезается на заданную длину и загружается в измельчитель.
Стружка строгального станка и аналогичные отходы измельчаются до необходимого размера частиц. Поверхностные и основные чипы часто подготавливаются по-разному и хранятся отдельно.
- Сушка: Древесная щепа пропускается через сушилку, чтобы снизить содержание влаги в ней примерно до 2,5% и облегчить склеивание и горячее прессование. Стружка сердцевины и поверхности может быть высушена до слегка различающейся влажности.
Альтернативой ротационным сушилкам является мгновенная сушка, которая требует несколько более низких температур сушки.
- Склеивание : Сухая стружка смешивается с синтетической смолой и любыми другими подходящими добавками, такими как отвердитель или восковая эмульсия. Дозирование клея и стружки должно быть очень точным и может варьироваться, так как поверхностные стружки часто имеют более высокое содержание клея.
На этом этапе могут быть добавлены любые особые требования, такие как обработка грибков или антипиренов.Тип используемого клея также может определять такие свойства, как влагостойкость.
- Формование мата : Матрац из древесной щепы, покрытой клеем, формируется путем ее падения на уплотнительные пластины или ленты. В зависимости от типа оборудования для формования матов это позволяет производить маты с постоянной градуированной плотностью или слоистые маты.
- Прессование : Обычно выполняется предварительное сжатие, а затем мат дополнительно сжимается до заданной толщины (обычно около 5 мм) в прессе с высоким давлением и температурой, который может быть многодневным, однократным или непрерывным.
- Обрезка и шлифование : После охлаждения каждая панель обрезается, а затем шлифуется до желаемой толщины для получения более гладкой поверхности.
Модификации
Как упоминалось выше, существует множество вариаций и модификаций, которые могут быть внесены в древесно-стружечную плиту для улучшения ее свойств, таких как влагостойкость, огнестойкость или звукоизоляция. Вот лишь некоторые из них:
Трехслойная ДСП: Более тонкие слои искусственных древесных стружек (обработанные из массива березы, бука, ольхи, сосны и т. Д.)) Размещаются на внешней стороне платы, а центральная часть состоит из более крупных и дешевых микросхем. Использование более однородной, изготовленной стружки придает плате большую прочность и внешний вид.
Влагостойкая (MR) древесно-стружечная плита : Меламино-мочевиноформальдегидная смола используется вместе с восковой эмульсией для обеспечения водоотталкивающих свойств.
Цементно-стружечная плита : Как следует из названия, в качестве связующего используется цемент, и поэтому она обладает высокой устойчивостью к влаге, ударам, звуку, огню и гниению.
Использует
ДСПчасто используется в мебели и интерьерах, поскольку стандартные ДСП не подходят для помещений, подверженных намоканию или высокой влажности, и более доступны по цене, чем массивная древесина.
Крупные компании, такие как IKEA, популяризировали использование ДСП в мебели благодаря своей репутации поставщиков ДСП, МДФ или аналогичных материалов высокого качества по низкой цене. В основном он встречается в мебели, для которой требуются большие предметы, такие как столешницы, столы, телевизоры и книжные полки.
ДСП можно купить голыми или покрытыми тонкими листами шпона или пластикового ламината. В то время как мебель из цельного дерева считается более привлекательной, эти материалы могут имитировать внешний вид настоящего дерева, хотя стоят немного дешевле, поэтому являются хорошей альтернативой при покупке мебели с ограниченным бюджетом.
Строительство
Что касается строительства, то ДСП хорошо подходит для внутренних проектов, например, для крепления петель дверных шкафов к бокам безрамных шкафов.В то время как другие материалы, такие как фанера, могут рассыпаться шкивами, когда на петли прикладывается чрезмерный вес, ДСП может удерживать винты на месте.
Однако, чтобы соединить два куска ДСП, обычный шуруп просто не прорежет их — вам понадобятся клеи, крепежные детали или специально разработанные шурупы для скрепления ДСП вместе.
По сравнению с фанерой или массивной древесиной, древесно-стружечная плита менее щадящая в процессе установки, так как части древесностружечной плиты могут деформироваться под действием растягивающего напряжения.Во многом это связано с недостаточной эластичностью смол для ДСП.
Он очень склонен к расширению и обесцвечиванию из-за влаги. Поэтому его редко используют на открытом воздухе или в местах с повышенным уровнем влажности. Чтобы бороться с этим, его можно покрыть краской или другим герметиком, чтобы помочь ему сохранить свою форму и внешний вид.
Если у вашего ДСП шпон или меламиновое покрытие, то при распиловке дисковой пилой он может сколоть. Чтобы с этим бороться, вы можете надрезать его универсальным ножом по линии разреза раньше.Вы также можете попробовать закрыть линию разреза липкой лентой перед тем, как сделать разрез.
Несмотря на то, что с меламином может быть трудно работать с точки зрения сколов, из-за его чистой и гладкой поверхности, он не требует покраски и при правильном нанесении будет стабильным и прочным в течение длительного времени.
Еще один совет при резке ДСП — работать в хорошо проветриваемом помещении (или, если это не удается — с чрезвычайно сильной системой пылеулавливания), так как при резке ДСП образуются очень мелкие опилки.Это может вызвать особую озабоченность, если ДСП содержит формальдегид.
Несмотря на то, что нельзя отрицать прочность массивной древесины в сравнении, ДСП может иметь преимущества перед массивной древесиной с точки зрения затрат, в зависимости от проекта. Например, толстый ДСП (обычно 3/4 дюйма) может выдерживать сжимающие нагрузки, такие как столешницы и бытовая техника. Достаточная прочность и низкая стоимость делают его популярным.
Таким образом, хотя древесно-стружечная плита может никогда не сравниться с превосходными свойствами натуральной древесины, она является недорогой и действительно универсальной, что делает ее отличным заменителем во многих отраслях промышленности.
Вопросы?
Надеюсь, что приведенное выше служит достойным обзором производства и наилучшего использования ДСП, но если у вас возникнут дополнительные вопросы, обязательно свяжитесь с нами через Twitter.
И если вы ищете идеальный материал для своего следующего проекта, обязательно ознакомьтесь с нашим ассортиментом продукции или закажите бесплатные образцы сегодня.
ДСПи Ориентированно-стружечная плита Учебный центр
ДСП
ДСП — это конструкционный материал, состоящий из фрагментов древесины, таких как древесная щепа, стружка лесопилок или опилки, и синтетической смолы или подходящего связующего, который механически прессуется в лист.Это разновидность древесноволокнистой плиты, но она состоит из более крупных кусков дерева, чем те, которые используются в древесноволокнистых плитах средней плотности (МДФ) и ДВП.
ДСП дешевле, плотнее и однороднее, чем обычная древесина и фанера. Его используют как замену им, когда стоимость предшествует внешнему виду и прочности. Хотя он более плотный, чем обычная древесина, это самый легкий и самый слабый тип древесноволокнистых плит, за исключением изоляционных.
Только в Европе ежегодно потребляется около 45 миллионов квадратных метров ДСП и МДФ.Его главные преимущества — цена и стабильность. Эта стабильность открывает новые возможности дизайна. Но при воздействии высокой влажности необработанная ДСП окажется совершенно непригодной для установки на открытом воздухе.
ДВП этого типа очень положительно влияет на лесные ресурсы и окружающую среду. Семьдесят пять процентов древесностружечных плит, производимых в Канаде и США, полностью изготавливаются из переработанных материалов.
Ориентированно-стружечная плита (OSB)
Ориентированно-стружечная плита (OSB) представляет собой конструктивное изделие из древесины, образованное прямоугольными деревянными прядями (хлопьями), уложенными в поперечно ориентированные слои с помощью водостойких клеев.В результате получается конструкционная деревянная панель, аналогичная фанере по прочности и характеристикам, но более однородная и менее дорогая.
Ориентированно-стружечная плита, широко используемая в жилищном и коммерческом строительстве, уже начала заменять натуральную фанеру во многих областях. Чаще всего используется в качестве обшивки стен, полов и крыш. OSB также называют стерлинговым картоном.
Ориентированно-стружечная плита имеет шероховатую поверхность различных цветов. Он производится в виде больших и сплошных матов и имеет неизменно высокое качество.OSB может иметь диапазон толщины, размера, прочности и жесткости за счет изменений в производственном процессе. Эти панели не имеют внутренних зазоров, перехлестов или пустот и водонепроницаемы.
Приходилось ли вам раньше использовать ДСП или OSB для ремонта?ДСП — хороший материал для мебели?
Древесно-стружечная плита также известна как древесно-стружечная плита или древесноволокнистая плита низкой плотности (ЛДФ). Обычно это наименее дорогой материал, который можно использовать для изготовления мебели.Он имеет более низкую стоимость, чем другие виды конструкционной древесины или фанеры.
Низкая стоимость ДСП достигается за счет использования всех отходов пиломатериалов. Сюда входят древесная щепа, стружка, опилки и другие отходы, оставшиеся от работы комбината. Их склеивают и плотно прижимают к доскам или листам.
Основным преимуществом древесностружечных плит является то, что они являются более экономичным вариантом по сравнению с фанерой или древесноволокнистыми плитами средней плотности. Благодаря легким свойствам ДСП легко транспортировать и обрабатывать.
ДСП дешевле, чем МДФ (древесноволокнистая плита средней плотности). ДСП лучше удерживает винты. Это делает его отличным вариантом для мебели, собираемой с помощью шурупов.
ДСП также обладают термоакустическими изоляционными свойствами. Это не особенно важно для мебели, но очень полезно для акустических систем и подвесных потолков зрительных залов, театров и т. Д.
Ламинированные древесно-стружечные плиты имеют декоративный пластиковый ламинат или деревянный шпон.Эти плиты прочнее, гладче и лучше выглядят, чем необработанные древесноволокнистые плиты. Они также требуют минимального ухода и легко чистятся.
В результате, ламинированные и шпонированные древесно-стружечные плиты часто являются предпочтительными при производстве недорогой мебели массового производства.
Древесно-стружечная плита также имеет ряд недостатков по сравнению с другими древесными материалами и фанерой.
Он имеет низкую прочность по сравнению с другими древесноволокнистыми плитами, а его низкая плотность позволяет легко повредить его при транспортировке.Низкая прочность древесностружечных плит означает, что они не выдерживают больших нагрузок.
В присутствии влаги ДСП может расширяться и коробиться. Также в экстремальных условиях может произойти обесцвечивание.
ДСП имеют низкую прочность и меньший срок службы, чем древесноволокнистые плиты и фанера средней плотности.
ДСП могут быть токсичными. В производственном процессе используется карбамидоформальдегидная смола, которая может выделять газообразный формальдегид.
Основным преимуществом ДСП перед массивом дерева или фанеры является очень низкая стоимость.
Мебель из ДСП стоит вдвое меньше, чем мебель из фанеры аналогичных размеров.
Эта низкая стоимость, конечно же, имеет свою цену, потому что ДСП не так долговечны, как фанера или массив дерева.
ДСП изготавливаются на станке с заданными размерами. Стандартные предметы мебели могут производиться серийно с использованием этих досок.
Это еще больше снижает затраты, так как не требуется столярных работ.
Тонкий слой пластикового или деревянного шпона обычно наклеивается на поверхность древесно-стружечных плит, используемых для изготовления мебели.Они известны как предварительно ламинированные плиты.
Ламинирование увеличивает красоту, а также немного увеличивает прочность доски.
В мебели с открытыми фанерными поверхностями также используются листы декоративного пластика или шпона. Процесс приклеивания этих ламинатов к фанерным листам требует времени и средств. Это значительно увеличивает стоимость изготавливаемой фанерной мебели.
ДСП очень легкие. Мебель из этих досок относительно легко транспортировать и перемещать.
Хотя это может быть преимуществом для некоторых людей, это также показатель того, что доска не такая прочная, как другие породы дерева.
Общее практическое правило, когда дело доходит до выбора древесины, заключается в том, что чем плотнее древесина, тем она прочнее. А чем плотнее, тем тяжелее. Вот почему мебель из массива дерева, которая прослужит несколько лет, такая тяжелая.
Мебель из ДСП не только является низкой прочностью, но и подвержена повреждениям из-за влаги и влажности.
Мебель из этих плит не такая прочная, как мебель из более плотной древесины или деревянных изделий.
Мебель из ДСП обычно прослужит 2–3 года, а возможно, и 5 лет, если она не будет интенсивно использоваться.
Пока нет комментариев. Будьте первым, кто оставит комментарий, заполнив форму ниже.
ДСП (ДСП, ДСП) — Foremost Trade
Материал: | Смешанная древесина |
Стандартные размеры (мм): | 1220 × 2440.Доступны индивидуальные размеры |
Стандартная толщина (мм): | 8-25 |
Для приклеивания: | E0, E1, E2 |
Содержание влаги (%): | 5-14 |
Плотность (кг / м3): | 650-700 |
Допуск по длине и ширине: | ± 1/16 ″ |
Допуск по толщине: | ± 0,004 ″ |
Отделки: | Ламинат, Шпон |
Приложение: | Может широко использоваться в помещении |
Упаковка: | Стандартная экспортная упаковка |
MOQ: | 1 * 20ГП.Меньше приемлемо |
Условия оплаты: | Т / Т, Л / К |
Срок поставки: | В течение 15 дней после подтверждения заказа |
ДСП используется для различных внутренних работ, в зависимости от сорта материала. Общие области применения включают мебель, фанеру и шкафы. ДСП конструкционного качества в основном используется для внутренних полов, но может использоваться и для других несущих конструкций в сухих условиях. ДСП идеально подходит для таких применений, как гардеробы, перегородки, тумбы под телевизор, стеллажи, игрушки, шкафы и облицовка стен, арматура.Для помещений с высоким уровнем влажности доступна влагостойкая версия (MR).
Если вы ищете плотную, однородную и экономичную неструктурную внутреннюю панель, ДСП — ваше решение. ДСП состоит из нескольких слоев древесных частиц, смешанных со смолами или связующими веществами, которые образуются под действием тепла и давления для создания панели. Изделия из ДСП доступны в различной толщине, ширине и длине и могут быть ламинированы ламинатом высокого давления, ламинатом холодного отжима или деревянным шпоном или окрашены.
ДСПобеспечивает однородную прочность и стабильность размеров. Обе поверхности отшлифованы для облегчения отделки. Также доступны древесно-стружечные плиты с кромкой из массивной древесины и покрытием из листов меламина (белая доска).
- Рентабельность
- Окрашиваемый и окрашиваемый
- Хорошо удерживает винты
- Постоянный градиент размера стружки от ядра до поверхности
- Высокопрочный для дома и офиса
- Постоянный внешний вид поверхности
- Высокая несущая способность
- Идеально для готовой мебели
- ДСП легко перепиливать и обрабатывать
- ДСП однородна и имеет одинаковую степень прочности в разных направлениях
- Можно нанести ламинат из шпона или меламина, чтобы он больше походил на массивную древесину
- Не имеет естественных дефектов и не набухает
В чем разница между ДСП, меламиновой фанерой и массивной древесиной? — Знание
В чем разница между ДСП и фанерой?
ДСП
ДСП (иногда также называемые ДСП).сделаны путем склеивания очень мелких древесных стружек (древесных частиц). и опилки с использованием фенольных смол. а затем прессование смеси при нагревании. для формирования плоских досок, из которых можно делать мебель.
ДСП Качество щепы зависит от размера частиц, из которых она состоит. клей, который скрепляет их. и плотность доски. Поскольку древесно-стружечная плита (ориентированная нить) может быть получена из большого количества древесных отходов, ее качество может сильно отличаться. Более мелкие частицы делают картон более качественным, плотным и тяжелым строительным материалом.Одним из лучших видов древесно-стружечных плит является древесноволокнистая плита средней плотности (МДФ). это высокое качество, но может быть очень тяжелым, что затрудняет развешивание больших шкафов. ДСП тоже выдолбливается или царапается. но это не такая большая проблема, если она защищена деревянным шпоном или ламинатом.
ДСП меламиновые Преимущества
— ДСП с меламиновым покрытием является самым дешевым из всех ДВП.
— Это дешевле, чем цельная древесина.
— ДСП придает гладкость на ощупь.
— ДСП имеет множество разновидностей.
— Не все древесно-стружечные плиты содержат формальдегид.
-ДСП легче по весу.
— Может удерживать шурупы больше, чем МДФ и ХДФ.
древесно-стружечная плита древесина Недостатки
— древесно-стружечная плита деформируется при насыщении водой.
— древесно-стружечная древесина самая слабая из всех древесноволокнистых плит.
— древесностружечная плита наименее прочный вид древесноволокнистой плиты.
-Влага оказывает на него большое влияние, как и на другие древесноволокнистые плиты.
— Не рассчитан на большие нагрузки из-за низкой прочности.
марки полов из ДСП
Пол из ДСП класса 1
Разработан для реализации концепции целостного покрытия полов. Полы из ДСП особенно подходят для строительства платформ. где укладывали пол до возведения стен. Изготовлен из древесных стружек прецизионного фрезерования. и скреплен влагостойкой синтетической смолой. Для большей защиты во время строительства и воздействия погодных условий.верхняя поверхность обогащена смолой, а все края запечатаны воском.
Красный, синий, желтый пол из ДСП
Также доступны полы из ДСП с обработкой против грибка и термитов. Листы, обработанные ФТ или фунгицидами, идеально подходят для участков. где может возникать кратковременная сырость и ТТ. или обработанные термитицидом листы добавили защиту от нападений термитов. произведено в Австралии в соответствии с требованиями. для пола из ДСП, класс 1, в соответствии с австралийским стандартом.AS / NZS 1860.1: 2002, ДСП плоская.
R-Flor
Включает металлизированную фольгу с высоким коэффициентом отражения (низким коэффициентом излучения). с полами из ДСП, чтобы уменьшить лучистую теплопередачу. через подвесной деревянный пол. и воздушное пространство на черновом полу для улучшения «общей R-ценности» напольной системы. все же позволяет укладывать пол обычным способом, обеспечивая скорость и легкость.
R-Flor позволяет использовать б / у. и давно установившаяся практика строительства с использованием платформенной конструкции.способ для подвесных черновых полов. более того. полы можно продолжать укладывать последовательно. с требованиями AS1860 Часть 2: Укладка ДСП.
R-Flor может похвастаться как теплицами, так и безопасностью для окружающей среды:
Произведено с использованием контролируемых и возобновляемых плантаций сосны с использованием рубок ухода за лесом. отходы лесопиления и лом. Это способствует снижению. в выбросах парниковых газов за счет более эффективного использования энергии.требуется для управления климатом в здании. в соответствии с обязательными мерами по энергоэффективности жилищного строительства. которые проистекают из озабоченности изменением климата; и
обеспечивает хранение углерода. Углерод, поглощенный в виде СО2 (парниковый газ), хранится в древесном волокне.
R-Flor — это новое поколение древесно-стружечных плит. разработан с учетом требований теплового комфорта. и энергоэффективность. R-Flor объединяет металлизированную фольгу с высоким коэффициентом отражения (низким коэффициентом излучения) с напольным покрытием из ДСП.для уменьшения теплопередачи через подвесной деревянный пол и воздушное пространство под полом.
Фанера
Фанера из тонких листов шпона, ламинированных в чередующемся направлении. Фанера — это изделие из дерева, состоящее из листов шпона. Панели из шпона спрессованы и склеены, образуя единое целое. Этот производственный процесс называется перекрестным зерном, и он снижает усадку. и расширение при улучшении материала отделки консистенции прочности панели.Различные сорта фанеры используются для разных целей.
Сорта фанеры, подверженные влиянию многих переменных. включая тип древесного слоя, толщину, клей. и процесс изготовления / уплотнения. Более низкие классы идеальны для чернового пола в зданиях и домах. Высокие сорта можно использовать для шкафов и стеллажей. На выбор существует множество видов фанеры. Убедитесь, что вы выбрали правильный тип фанеры для мебели или приспособлений, которые вы строите.
Фанера также является конструкционным деревянным продуктом, изготовленным прессованием.и скрепление листов шпона в одно целое.
Фанера бывает не только разной толщины. но также в разных классах, поэтому вы можете выбрать подходящий для своего проекта. Более низкие классы используются при строительстве домов для черновых полов и т. Д. эти типы фанеры не должны выглядеть красиво. так как они будут прикрыты. Фанера более высоких сортов (морилка, корпусная и т. Д.) Намного красивее. и плавнее. У них есть последовательная текстура древесины. и, как правило, не имеют отверстий для узлов или других серьезных дефектов.Фанера шкафного класса всегда шлифуется очень сильно.
Меламиновая фанера преимущества
-Она обладает большой однородной прочностью. Установив чередующийся узор для зерен. фанера способна набирать однородную прочность.
— Доступен в нескольких больших размерах, в отличие от массива дерева.
Слои фанеры могут быть изменены для придания красоты и прочности.
— В отличие от массивной или натуральной древесины, фанера максимально использует доступное сырье.Его изготовление способствует сохранению деревьев.
-В зависимости от вида фанера является универсальным материалом.
— Фанера из твердых пород древесины служит дольше из-за ее высокого качества и прочности. В целом фанера более долговечна, чем ДВП (МДФ, ХДФ и ДСП).
-Фанера стоит дешевле, чем цельная древесина.
меламиновые плиты Недостатки
-Покупателю необходимо покупать водостойкую фанеру, если ее последующее использование подвергнет ее воздействию влажных условий. Это потому, что слои могут отслоиться.
-При покупке материала необходимо найти надежный источник. Тип древесины, используемой для внешних слоев, легко определить, но не для внутренних.
-Работа по краям фанеры там, где наблюдаются слои. Это тот случай, когда фанера используется в качестве материала для изготовления мебели на заказ. В этом случае покрытие края деревянными полосками после нанесения клея может помочь.
-Фанера менее прочная, чем цельная древесина.
-Фанера дороже ДВП.
-Мебель из фанеры требует много времени.
-Не рекомендуется использовать гвозди для фанеры, так как они могут вызвать раскалывание материала. Винты — лучший способ закрепить материал с помощью правильной техники, например, сверления.
-Фанера может расслаиваться в регионах с жарким климатом.
фанера против ДСП
Стоимость | При всех преимуществах фанеры перед ДСП. тот факт, что ДСП дешевле, делает его по-прежнему довольно популярным.среди производителей мебели. и домовладельцы. ДСП стоит примерно вдвое или даже меньше, чем фанера или массив дерева. цена по-прежнему является одним из самых важных факторов. при участии в любом проекте, связанном с проектированием деревянных изделий. |
Экологичность | фанера экологически безопасна. Бывает, что ДСП тем более. Это потому, что древесностружечные плиты создаются из обрезков других пиломатериалов. Фанера, но требует шпона из свежей древесины.При производстве ДСП не требуется дополнительной обрезки деревьев. |
повреждение водой | Когда вы работаете над проектом, который подвергнется значительному воздействию влаги. лучше всего использовать фанеру вместо ДСП. учитывать повреждения водой В то время как обычная фанера не совсем водонепроницаема. хотя морская фанера очень близка. ДСП работают хуже, поскольку они набухают и расширяются под действием влаги. Когда это происходит, древесно-стружечные плиты также теряют большую часть своей прочности.Хуже того, набухшие от влаги ДСП становятся тяжелее. и это увеличивает риски безопасности. |
вес | Листы фанеры также намного легче, чем ДСП. Их легче переносить с места на место или с этажа на этаж. Вес также имеет значение, когда вы делаете навесной шкаф или мебель на колесиках. Будучи тяжелее, навесные шкафы. колесная мебель из ДСП могла разрушиться под собственным весом. |
ДСП и шкафы из фанеры
Обычно считается, что фанера является лучшим продуктом при строительстве шкафов.Фанера имеет большую долговечность конструкции, потому что в ней крепятся винты. и прочий механический крепеж подробнее. Обладает превосходными свойствами при растяжении и сдвиге. (это означает, что он сопротивляется тянущим силам и движению из стороны в сторону). и небольшое преимущество в прочности на сжатие (способность выдерживать вес). Фанера также весит меньше, чем ДСП. ., что может иметь значение при навешивании больших шкафов. Кроме того, фанера лучше скрепляет клеевые швы, чем ДСП. и более устойчив к вмятинам и царапинам.
ДСП имеет свои преимущества, в том числе большую стабильность размеров. он не коробится из-за перепадов температур. и другие изменения в окружающей среде. ДСП стоит дешевле фанеры. ДСП часто делают из обрезков древесины, которые считаются отходами. Многие производители фанеры также производят ДСП из остатков. Из-за этого ДСП дешевле. Используя ДСП, можно сэкономить от 8% до 12% на стоимости шкафов.
Основным недостатком ДСП является отсутствие влагостойкости.Если влага впитается через торцевые волокна, ДСП разбухнет. Например. если вода на полу попала на незавершенный нижний край ящика шкафа. Чтобы решить эту потенциальную проблему. Imperia заклеивает торцы всех частей ДСП кромочной кромкой. Установщик может также заклеить нижние края шкафных ящиков прозрачным слоем при их установке. Фанера, хотя и более водостойкая, к тому же не очень прочна во влажных условиях.
фанера. Основные отличия ДСП могут различаться по качеству, поэтому трудно сказать, что один всегда лучше другого.Качество фанеры зависит от количества слоев и толщины древесины. Меньшее количество слоев менее стабильно, поэтому у качественной фанеры будет больше слоев. Качество также зависит от того, насколько хорошо склеены слои. У некачественной фанеры будут зазоры, что сделает ее менее надежной. Фанера, используемая для бескаркасной мебели, обычно имеет от семи до девяти слоев. и толщиной 3/4 дюйма, сказала Линда. Для лицевых панелей используется фанера толщиной в полдюйма для боковин, верха. и снизу, потому что рама добавляет прочности коробчатой конструкции; полки из фанеры 3/4 дюйма.Итак, хотя фанера в целом лучше, есть много случаев. где ДСП будет работать достаточно хорошо, чтобы оправдать экономию средств, — говорит Линда.
За дверцами из вишни, березы или клена в конструкции кухонного шкафа прячется древесина, из которой изготовлен шкаф. спинка, бока, верх, полки и низ модульных кухонь. Обычно существует два варианта конструкции шкафной коробки: шкаф из фанеры и ДСП. Фанера состоит из слоев шпона, склеенных между собой.чередование волокон древесины для устойчивости. ДСП (также известная как мебельная плита) из клееных древесных волокон. и прижались друг к другу. иногда с помощью формы. У каждого материала есть свои преимущества.
Так как фанера из ценных пород древесины во многих отношениях превосходит ДСП, она обычно является лучшим выбором, если стоимость не является проблемой. Но, дело в том, что ДСП дешевле. делает его разумным выбором во многих ситуациях. Если шкаф большой и собирается навесить, лучшим вариантом может быть фанера, потому что она легче.В большинстве других ситуаций ДСП работает почти так же хорошо, как фанера. При ремонте. не забудьте принять решение о преимуществах фанеры в сравнении с ограничениями вашего бюджета. какой выбор лучше.
Что такое цельная древесина
Цельная древесина — это термин, который чаще всего используется для различения. между обычным пиломатериалом и конструкционной древесиной. но это также относится к конструкциям, в которых нет пустот. Инженерные изделия из дерева, изготовленные путем связывания древесных волокон.волокна или виниры с клеями для образования композитного материала. К конструкционной древесине относятся фанера, ориентированно-стружечная плита и древесноволокнистая плита. Дело в том, что изделие из массива дерева часто рекламируется в рекламе. Но использование массива дерева имеет свои преимущества и недостатки.
Твердая древесина — это пиломатериалы, вырезанные из деревьев. Другие породы дерева, такие как фанера, ДВП средней плотности или шпон. изготовлены из древесных композитов.
Твердая древесина — это древесина, вырезанная из дерева.В отличие от инженерной древесины. которые состоят из древесных волокон, скрепленных клеями. твердая древесина содержит древесные волокна по всей длине пиломатериала. Не используются ни наполнители, ни клеи. Массив дерева часто используется для изготовления мебели, строительства, столярных изделий и полов.
Она не коробится так же легко, как многие искусственные породы дерева, но более восприимчива к появлению пятен. Массивную древесину легче ремонтировать, чем шпон или другую конструкционную древесину, и это одна из причин. что он использовался для многих типов проектов.Доступны несколько видов массивной древесины — столяры, краснодеревщики. а плотники могут выбирать из большого выбора для своих проектов. У каждого вида массивной древесины есть свои особенности, в том числе рисунок текстуры. цвет и текстура.
фанера против цельной древесины
Фанера идеально подходит для применений, где требуется листовой материал. который не подвержен растрескиванию, усадке или деформации. Примеры включают шкафы, рабочие столы и контейнеры для хранения. Фанера также хорошо подходит для создания изогнутых поверхностей, таких как пандусы для скейтборда.
Твердая древесина использовалась в качестве строительного материала на протяжении тысячелетий, и она сияет в приложениях. где важны прочность и жесткость, в том числе книжные полки, настил. и структурные опоры, такие как балки перекрытий и стропила. Это также предпочтительный материал, когда важны эстетика и красота.
Массив дерева часто используется в сочетании с фанерой. Например, рабочий стол. или полка из фанеры часто будет иметь окантовку из цельного дерева, чтобы скрыть края фанеры.Другой пример — опорные планки из массива дерева, используемые для придания жесткости фанерной полке.
Массив дерева прочнее фанеры, особенно по жесткости. Полка из массива дерева будет меньше прогибаться, чем полка из фанеры того же размера.
Если мебель из массива не предназначена. со временем она ослабеет из-за движения древесины, связанного с изменениями влажности воздуха. В крайнем случае может произойти растрескивание и раскалывание древесины. Фанера этого не делает. Но слои фанеры могут расслаиваться во влажной среде.
Фанеру легко разорвать по ширине, но ее сложно разрезать из-за отрыва тонких внешних слоев шпона. При шлифовании фанеры следует соблюдать осторожность, чтобы не зашлифовать шпон. особенно при шлифовании краев.
Необходимо учитывать дополнительное время и усилия, связанные с нанесением кромочных полос. при строительстве мебели из фанеры.
Массив дерева легко раскалывается и раскалывается. хотя может произойти защемление пильного полотна. при распиловке заготовки с внутренними напряжениями.Массив дерева также можно строгать, чтобы сделать его тоньше, что не подойдет для работы с фанерой.
Дополнительная литература: Как выбрать фанеру из меламиновой плиты Wood Grave?
Теги:
фанера против ДСП. средняя плотность. МДФ против плотного ДВП. мдф частица. шкафные ящики. доска мдф. коробчатая конструкция. корпусное строительство. ДВП мдф. текстура древесины. ориентированная прядь. стружечная плита. фанера мдф. фанерный шкаф. доска против тяжелых грузов. поперечный узор.
Варианты чернового пола: OSB против ДСП
Варианты чернового пола: OSB против ДСП
Распространенный вопрос перед укладкой нового пола — какой тип основания использовать. Люди часто путают OSB с ДСП. Одним предложением — ДСП часто используют как черновой пол для ковров , OSB используют как основной черновой пол для любого напольного покрытия, включая паркет . Теперь давайте рассмотрим их обоих поближе.
OSB (Ориентированно-стружечная плита)
OSBили ориентированно-стружечная плита обычно используется в качестве основного чернового пола из-за ее устойчивости и доступной цены.Ориентированно-стружечная плита изготавливается из спрессованных и склеенных между собой кусков древесины, больших деревянных прядей и кусков. Большие куски придают каждой доске уникальный характер, поэтому каждая доска уникальна и полна цветов. Доски имеют размер 8 футов на 4 дюйма и бывают разной толщины, от 1/2 дюйма до 1-1 / 4 дюйма. Национальная ассоциация деревянных полов одобряет использование OSB в качестве основания для полов из твердых пород дерева с укладкой гвоздями с минимальной толщиной 23/32 ″ и рекомендуемой толщиной 7/8 ″ или 1-1 / 8 ″. Перед укладкой черного пола необходимо провести надлежащую акклиматизацию, чтобы добиться стабильных и продолжительных результатов.Кроме того, между древесиной твердых пород и OSB необходимо укладывать подкладочную бумагу. В настоящее время большинство производителей твердой древесины одобряют использование плит OSB в качестве надлежащего основания для деревянных полов.
С другой стороны, плиты OSB не подходят для укладки плитки . И керамическая, и керамогранитная плитка требуют установки твердого основания или цементной плиты поверх существующего черного пола перед укладкой плитки. (Примечание : New Floors Inc не продает и не устанавливает плитку )
ДСП
ДСП (или ДВП) имеет другую структуру — это мелкая щепа, частицы и древесная пыль.Этот переплетенный состав спрессован и склеен, но он хрупкий, плохо удерживает ногти и легко ломается голыми руками. Как правило, ДСП используются в качестве дополнения к обычному черновому полу при укладке ковровых покрытий от стены до стены. ДСП бывает разной плотности, но все же мягче по сравнению с плитами OSB. Самыми популярными типами являются HDF и MDF — древесноволокнистые плиты высокой / средней плотности, с меньшим количеством сколов и большим количеством пыли. ДСП и ДВП имеют более однородный внешний вид, а некоторые из них окрашиваются производителем для обеспечения влагостойкости.Однако они НЕ одобрены в качестве чернового пола для паркета из твердых пород древесины и должны быть удалены перед укладкой из твердой древесины.
Подводя итог, вот ссылка на материалы для пола и черновой пол, которые будут использоваться в вашем доме:
Твердая древесина -> OSB или обычная фанера , минимум 23/32 ″, рекомендуется 7/8 ″ или 1-1 / 8 ″
Плитка -> OSB или фанера со слоем цементной плиты или hardiback
Ковер -> OSB или фанера с ДСП (опция) для мягкости.
Верхний слой | Твердая древесина | Ковер | Винил | Керамика или фарфор |
Застежка | Гвоздь, поплавок или клей | Клей или растяжка | Клей или поплавок | Клей |
Влага Барьер | Подложка | – | Подложка | – |
Черный пол | OSB или фанера | ДСП, МДФ, ХДФ | любой | Hardyback или Цементная плита |