Что такое древесный композит на полимерной основе?
Дерево и различные виды древесных композитов широко применяются в строительстве и отделке. Что касается древесно-композитных материалов, то наиболее известны такие их виды, как ДВП, МДФ, фанера, клееный брус, ОСБ и ДВП. Древесно-полимерные композиты (общепринятое сокращение – ДПК) появились в массовой продаже сравнительно недавно. Данные материалы иногда называют «жидкое дерево». ДПК стоит дороже других древесных композитов, зато превосходит их по многим характеристикам.
Жидкое дерево является полусинтетическим материалом. Его производят из отходов древесины, которая перемалывается до фракции мелкой пыли, и искусственных/натуральных мономеров. ДПК изготавливается путем экструзии, при которой образуется древесно-полимерная масса. Роль связующих веществ в данном случае выполняют полимеры. Кроме этого, в состав вводятся соответствующие химические присадки, улучшающие определенные свойства материала. ДПК может содержать 70-80% дерева, которое и придает основной объем готовым изделиям.
При производстве ДПК используются разные виды полимеров – обычный полиэтилен, поливинилхлорид или полипропилен. В качестве добавок-аддитивов чаще всего применяются следующие компоненты: биоциды (повышают стойкость в действию разных биофакторов), лубриканты (ускоряют экструзию и увеличивают влагостойкость), реагенты вспенивания (снижают вес изделий и обеспечивают получение более гладкой поверхности), присадки для улучшения механических показателей твердости, жесткости и общей прочности, красящие пигменты (позволяют придавать изделиям требуемый цвет/оттенок).
Область применения ДПКЖидкое дерево применяется для тех же целей, что и натуральное дерево, и другие древесные композиты. Прежде всего, ДПК широко используется для монтажа полов и стеновой отделки. Из него также делают различные конструкции, предназначенные для эксплуатации в условиях улицы – террасы, заборы, веранды, стойки уличных баров, внешние витрины, танцплощадки, дачные беседки, двери/калитки, садовые дорожки и многое другое.
В частности, полимерные древесные композиты применяется в автостроении, а также «идут» на отделку конструкций, которые эксплуатируются в условиях высокой влажности – причалов, бортов бассейнов и т.д. Из материалов с повышенной влагостойкостью делают даже мосты небольших размеров и различные детали лодок, яхт и кораблей.
Сайдинг ДПК является отличной альтернативой виниловому сайдингу и вагонке. Из него изготавливают предметы мебели, столешницы, межкомнатные двери, откосы и подоконники. Наиболее распространен так называемый декинг (или террасная доска), выполненный из полимерно-древесных композитов. Данный материал применяется для устройства уличных полов и создания напольных покрытий в помещениях разного назначения (от гостиных зал до саун).
Хорошим спросом пользуется и древесно-полимерный садовый паркет. Он производится в виде плиток (стандартный размер – 300х300 мм). Паркетные планки закреплены на легких пластиковых основаниях. Такой паркет быстро и просто монтируется и демонтируется, что дает возможность использовать его при возведении временных и сезонных строений.
Помимо готовых изделий различных видов в продаже есть специальная краска – ДПК в жидком виде. С ее помощью можно надежно защитить поверхность из дерева, ДСП и т.п. от действия факторов внешней среды и придать ей вид натуральной древесины (краска отлично имитирует структуру древесных волокон).
Преимущества ДПК- Повышенная влагостойкость. По данной характеристике древесные композиты на полимерной основе примерно в пять раз превосходят дерево.
- Высокий запас механической прочности и устойчивость к износу.
- Материал практически не «скользит», в отличие от большинства лакированных напольных покрытий.
- Универсальность в плане обработки. Как и дерево, ДПК отлично поддается распилу, строганию, шлифованию, просверливанию и т.д. По сути, с ним можно проделывать все операции, что и с натуральной древесиной. В этом отношении полимерный материал выгодно отличается от ряда других древесных композитов. Например, от ДСП, в которые не рекомендуется забивать гвозди, или от тонких ДВП, кромки которых разлохмачиваются при распиле.
- ДПК полностью сохраняет свои свойства при высокой (до +180 градусов) и низкой (до -50 градусов) температуре, а также при ее значительных перепадах в указанном диапазоне.
- Устойчивость к микроорганизмам, вызывающим плесень и грибок. Материал также является «несъедобным» для насекомых-древоточцев.
- Простой монтаж. Никаких специальных навыков и инструментов для него не требуется.
- Длительный срок службы. Самые качественные материалы из высокой ценовой категории могут сохранять не только свои эксплуатационные характеристики, но и эстетичный внешний вид до пятидесяти лет.
- Практичность. В отличие от дерева, полимерно-древесный композит не нуждается в периодической шлифовке/циклевке и лакировании/окрашивании.
Минусов у данного композита практически нет. Можно выделить только два недостатка. Во-первых, это быстрый износ материала при постоянном/регулярном воздействии сразу двух факторов – высокой температуры и значительной влажности (более 65%). Во-вторых, появление плесени при эксплуатации на плохо вентилируемых/проветриваемых объектах. Имеется в виду плесень, которая появляется только на поверхности ДПК и не проникает внутрь композита.
Древесно-полимерный композит (ДПК) – состав, содержащий полимер (химического или натурального происхождения) и древесный наполнитель, модифицированный, как правило, химическими добавками. Другие используемые названия древесно-полимерных композитов: «жидкое дерево», дерево-пластиковый композит, древесно-пластиковый композит, древопласт, поливуд, древотермопласт, wpс, wood polymer composite, wood plastic composite, ЭДНП (экологически чистые древеснонаполненные пластмассы), ДНПП (древеснонаполненный полипропилен). Особенность древесно-полимерных композитов заключается в том, что готовые изделия получаются, по сути, из отходов производства и потребления: опилок, стружек, древесной муки, сельскохозяйственных отходов и различных видов отходов потребления.![]() По внешнему виду древесно-полимерный композитный профиль с высоким содержанием древесины более всего напоминает МДФ или твердую ДВП, а с малым ее количеством — пластмассу. Его можно пилить, строгать рубанком, вбивать гвозди. Он может окрашиваться в массе или подвергаться лакокрасочной отделке обычными красками и эмалями, или облицовываться синтетическими пленками или натуральным шпоном. Рынок жидкого дерева в России находится пока в зачаточном состоянии. Однако с усилением государственного регулирования в области деревообработки и переработки отходов, материал получает дополнительный стимул для развития в России: появляется спрос на изделия, открываются первые производства. Древесно-полимерные композиционные (ДПК) материалы, в последнее время пользуются особым вниманием у инвесторов и производителей. Древесно-Полимерный Композит — суперсовременный материал. В состав ДПК входят древесная мука (или мелкая щепа) с фракцией 0,5-2мм, полимер и аддитивы. В качестве полимера может быть ПВХ (50/50), полиэтилен (70/30)или полипропилен (60/40). Производство экструзионных древесно-полимерных композитов является одним из наиболее перспективных в области рационального использования отходов лесопиления, мебельного и деревообрабатывающего производств, использования низкосортной древесины, растительных целлюлозосодержащих отходов и вторичных пластмасс для переработки в высококачественные профильные детали для широкого спектра применений, включая строительство и мебель. В настоящее время корпорация Интервесп готова предложить комплектные высокотехнологические экструзионные линии для производства древесно-полимерных композиционных материалов различной производительности, надежным и стабильным производственным процессом. |
|
Что такое ДПК? Это удачный союз дерева и пластика. В состав входят древесная мука, полимер и аддитивы.
Древесно — полимерный композит (ДПК) — это удачный союз дерева и пластика. В состав входят древесная мука, полимер и аддитивы. В качестве полимера может быть ПВХ (50/50), полиэтилен (70/30) или полипропилен(60/40).
Этот материал обладает всеми эстетическими и тактильными свойствами дерева, экологически безопасен, и при этом абсолютно не подвержен каким-либо воздействиям внешней среды (атмосферные условия, насекомые, микроорганизмы), не ломается, не образует сколов и трещин, обладает свойствами самозатухания и устойчивостью к грибкам и плесени.
Из Древесно-Полимерных Композитов изготавливаются: различные панели и профили для обшивки стен и потолков, паркетные доски, сложные конструкционные элементы.
Этот материал с успехом заменяет кафель при отделке бассейнов и бань.Идеальный материал везде, где необходим прочный, влагостойкий, безопасный и экологичный материал.
В последнее время, появились новые интересные идеи использования композитной террасной доски: площадки для патио, эксплуатируемые крыши, обводные дорожки искусственных водоёмов и бассейнов.
Террасная доска обладает положительными свойствами, выгодно отличающими ее от других монопокрытий:
- минимальная теплопроводность
- натуральный запах и внешний вид, то есть то, что роднит древесно-полимерный композит с деревянным покрытием
- изделия из древесно-полимерных композитов можно очистить при помощи обыкновенной щетки
- они не требуют окрашивания или какой либо другой дополнительной обработки
- не образуют сколов и трещин
- не впитывают влагу
- устойчивы к атмосферным воздействиям
- полностью пригодны к вторичной переработке
- не электростатичны
- экологичны – не содержат вредных веществ, не выделяют формальдегидов
-
Изделия из ДПК обрабатываются такими же инструментами, что и обыкновенная древесина: легко строгаются, распиливаются, шлифуются, сверлятся, достаточно хорошо удерживают скобы, гвозди, шурупы и т.
д.
- изделияиз ДПК имеют ровный цвет и окрашены по всей массе независимо от геометрических параметров, что позволят создавать единый стиль конструкции любого размера
В последние годы спрос на натуральные строительные и отделочные материалы увеличивается с геометрической прогрессией. Люди все чаще задумываются о своем здоровье и здоровье своих детей.
Период эксплуатации этого материала без каких-либо изменений его характеристик будет составлять 30 и более лет (зависит от возможных нагрузок в повседневном применении).
Древесно полимерные материалы -качество дпк | ПластЭксперт
Древесно-полимерные композиционные материалы (ДПК), которые удачно сочетают в себе достоинства как полимера так и древесины, испытывают бурный рост производства во всем мире. Российское производство ДПК также продолжает расти и в 2012 году составило порядка 9,4 тыс. тонн, однако этот объем в сотни раз меньше объема рынка США или Китая.1. Замедленный темп роста отечественной продукции из ДПК по оценкам экспертов портала Drevoplastic. ru и других специалистов, объясняется тем, что потребителем материала являются частные негосударственные организации. Большие строительные компании не рассматривают этот материал в своих проектах в связи с тем, что на него в данный момент отсутствует отраслевой стандарт. Создание нормативной базы качества готовой продукции и системы контроля производства будет значительно стимулировать рост рынка ДПК.
ООО «НИЦ «ДПК», единственная в России аккредитованная организация, которая проводит системные исследования по вопросам оценки качества товаров из ДПК. Одним из результатов этой работы было создание, поддержание и совершенствование классификатора по одному из видов продукции – террасной доске.
2. Следующим этапом в направлении развития нормативной базы для последующей стандартизации нового материала является разработка «Руководства по качеству продукции из ДПК», которое может лечь в основу единого нормативного документа (стандарта или ТУ) для всех отечественных производителей данного вида продукции. «Руководство…» как основополагающий документ для дальнейшей стандартизации продукции принято и одобрено в рамках объединения производителей ДПК – официально зарегистрированной организации НП «Объединение производителей древесно-полимерного композита» в марте 2012 года. Деятельность Некоммерческого партнерства «Объединение производителей древесно-полимерного композита» направлена на:
-цивилизованное развитие рынка ДПК;
-вытеснение с рынка низкосортной продукции;
-создание нормативной базы для продукции из ДПК;
-представление и отстаивание интересов ведущих предприятий отрасли
В настоящее время в НП входят 5 компаний, в том числе 3 иностранных. «Руководство по качеству…» не только определяет обязательные к использованию методы оценки качества изделий из ДПК, но указывает предельно допустимые значения, устанавливает четкие критерии для отсечения некачественной продукции. Продукция участников некоммерческого партнерства проверяется в строго регламентированном порядке в соответствии с требованиями, прописанными в «Руководстве по качеству…» ежегодно. Производителям, прошедшим эту проверку, присваивается отечественный «Знак качества», форма которого зарегистрирована в установленном порядке (Рис. 1).
Рис.1 Знак качества продукции из ДПК
Прописана также процедура присвоения и регистрации «Знака качества» Таким образом гарантируется, что продукция, произведенная членами этого объединения, отвечает всем требованиям, предъявляемой к данному виду продукции: долговечность, геометрическую и биологическую стабильность и безопасность для окружающей среды и здоровья человека.
Первая редакция этого «Руководства» была разработана для наиболее широко распространенного вида продукции — террасной доски и представлена в соответствующем докладе на 2-й Международной конференции «Древесно-полимерные композиты — 2012», прошедшей 21.09.2012 г. в Москве в отеле «Балчуг-Кемпински» и организованной Inventra-Creon.
3. В идеальном случае «Руководство…» должно охватывать все этапы жизненного цикла продукции. В первую редакцию были включены требования к компонентному составу и сырью для производства ДПК, а также требования к готовой продукции (декингу), выполнение которых необходимо для присвоения Знака качества НП.
Выдержки из «Руководства по качеству продукции из ДПК»
Древесно-полимерные композиционные материалы должны представлять собой однородную смесь измельченного целлюлозосодержащего биологического сырья и полимера (полиэтилен, полипропилен, ПВХ) с необходимыми технологическими и эксплуатационными добавками. Изделия получаются методом экструзии на специализированном оборудовании в виде профиля различного сечения.
Продукты, аттестованные на Знак качества кроме древесины не должны содержать никакие другие естественные волокна, например, от однолетних растений. Не разрешено использовать в качестве сырья переработанную древесину, а исключительно массивную древесину или отходы механической обработки древесины. Полимер или смесь полимеров, используемые в производстве ДПК, должны состоять из 100% первичных синтетических полимеров. Прямая рециркуляция остатков от производства древесно-полимерных композитов разрешена
4. Требования к готовой продукции, аттестованной на Знак качества приведены в табл.1. Периодичность подтверждения результатов испытаний: №1-4 — 1 раз в год, остальные — 1 раз в 2 года.
Таблица 1
Требования к готовой продукции
№ | Наименование показателя | Ед. изм. | Предельное значение | ||||||
1 | Плотность | г/см | - | ||||||
2 | Предел прочности при изгибе | МПа | 25 | ||||||
3 | Выдержка 2 часа в кипящей воде | Водопоглощение | % | 5,0 | |||||
Разбухание | по длине | % | 1,5 | ||||||
по ширине | 0,7 | ||||||||
по толщине | 0,3 | ||||||||
4 | Твердость при вдавливании шарика | Н/мм2 | 90 | ||||||
5 | Стойкость к удару падающим шаром | трещины не более | мм | 10 | |||||
углубления не более | 1 | ||||||||
6 |
Несущая способность профильной доски при расстоянии между опорами 400 мм.![]() |
Н | 2000 | ||||||
7 | Сопротивление скольжению | Коэффициент трения, не менее | 0,43 | ||||||
8 | Сопротивление изгибу под температурной нагрузкой (величина прогиба под воздействием груза 85 кг) | мм | 10 | ||||||
9 | Коэффициент линейного теплового расширения (в диапазоне температур +30…+80 °С) | по длине | °С-1 | 5×10-5 | |||||
по ширине | 7×10-5 | ||||||||
по толщине | 9×10-5 | ||||||||
10 | Стойкость к циклическим климатическим воздействиям (потеря прочности при статическом изгибе после 20 циклов вымачивание/замораживание/нагрев, не более) | % | 20 | ||||||
11 | Условная светостойкость -24 часа уф-облучения (визуально — по серой шкале) | балл | 2 | ||||||
12 |
Оценка воздействия микроорганизмов |
Метод A: тест на грибостойкость | балл | 0 | |||||
Метод B: определения фунгистатического действия | 0 |
Показатель №1 «Плотность» (метод испытаний по EN ISO 1183-1).

Показатель №2 «Предел прочности при изгибе» (метод испытаний по EN 310) основной показатель физико-механических свойств материала. Характеризует правильность выбранной композиции и технологических режимов производства. Эффективность работы совместителя в композиции. Величина этого показателя характеризует сбалансированность формулы и правильность ведения технологического процесса. Среднее значение предела прочности при изгибе не должно быть ниже 25 МПа.
Показатели №3: «Водопоглощение и разбухание» при выдержке в кипящей воде в течение 2-х часов (метод испытаний по EN 1087-1) характеризуют геометрическую стабильность и гигроскопичность ДПК профиля. Вода является основным агрессивным фактором атмосферных воздействий, поскольку вызывает разбухание материала и накопление дефектов, особенно при перепадах температур от (-) до (+).

Величина показателей водопоглощения и разбухания зависит от рецептуры и гомогенизации композиции, показывает на сколько компоненты распределились и совместились во всем объеме древесного наполнителя. Пороговые значения:
— Среднее значение водопоглощения при погружении в воду на 24 часа не должно превышать 5 %.
— Средние значения разбухания не должны превышать 1,5 % по толщине, 0,7 % по ширине и 0,3 % в длине.
Показатель №4 «Твердость при вдавливании шарика»
(метод испытаний
по
EN 1534
)
характеризует контактную прочность изделия, позволяет косвенно оценить сопротивление вдавливанию и стойкость к царапинам.

Показатель №5 «Стойкость к удару при положительной и отрицательной температуре» (метод испытаний по EN 477) Показатель позволяет оценить хрупкость доски как готового изделия при положительной (+6 °С) и отрицательной (-10 °С) температуре. На величину показателя влияет вид полимерной матрицы а также содержание наполнителя. Пороговые значения:
— полые профили: 9 из 10 образцов не должны показать поверхностные трещины с длиной более 10 мм.
— полые профили: максимальная остаточная глубина воздействия не должна превышать 1 мм
Показатель №6 «Несущая способность профильной доски» при расстоянии между опорами 400 мм (метод испытаний по EN 310). Показатель характеризует, насколько удачно спроектирован профиль балки (половой доски), что может быть существенно при монтаже напольных покрытий и выборе расстояния между лагами.
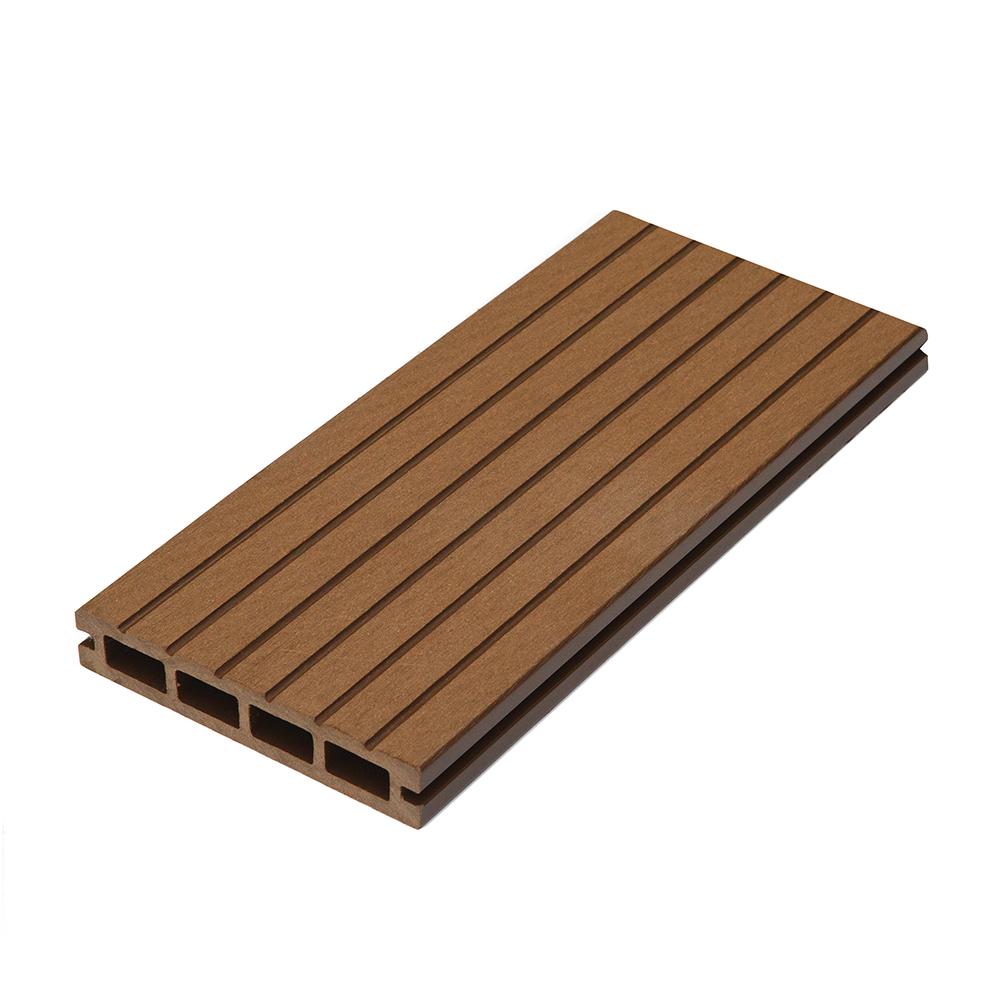
Показатель №7 «Сопротивление скольжению» — коэффициент трения покоя (метод испытаний по EN 425). Важный показатель травмобезопасности напольных покрытий. Величина показателя в основном зависит от вида обработки поверхности профиля (гладкий, рифление, тиснение, шлифовка, брашинг) Минимальное значения коэффициента трения не должно быть ниже μ = 0,43, что соответствует «безопасному» классу скольжения.
Показатель №8 «Сопротивление изгибу под температурной нагрузкой» под воздействием груза 85 кг (метод испытаний по EN 899-2). Характеризует ползучесть профиля и геометрическую стабильность конструкции при повышенных температурах, возникающих при нагреве конструкции солнечными лучами. На величину показателя влияет вид полимера, а также содержание наполнителя в изделии.

Показатель №9 «Коэффициент линейного теплового расширения (КЛТР)» (метод испытаний по ISO 11359-2) Характеризует поведение профиля при повышенных температурах (+30…+80 °С), возникающих при нагреве конструкции солнечными лучами. Показатель важен для расчета величины деформации напольных покрытий при монтаже и для определения необходимых зазоров между досками и ограждающих стен во избежание коробления.
Пороговые значения:
— по длине: 5×10-5
— по ширине: 7×10-5
— по толщине: 9×10-5
Значения установлены по статистическим данным в результате испытания более 50 видов террасной доски различных производителей.
Показатель №10 «Стойкость к циклическим климатическим воздействиям» (собственная методика ООО «НИЦ ДПК» основанная на методе испытаний 6 по ГОСТ 9.

Испытание характеризует стойкость материала к погодным условиям, правильность выбора термостабилизаторов, антиоксидантов и УФ-адсорберов в композиции и. в конечном счете, долговечность материала.
Не правильно стабилизированные композиции не выдерживают воздествия жесткого УФ-облучения. Полимерная матрица разрушается и выкрашивается. Значение величины потери прочности при статическом изгибе после 20 циклов климатических воздействий не должно превышать 20 % по отношению к первоначальной прочности образца, также фиксируются изменения декоративных характеристик изделия
Показатель №11 «Условная светостойкость — 24 часов уф-облучения» (испытание по ГОСТ 21903, метод оценки ISO 105-А2-99).

Показатель №12 «Оценка воздействия микроорганизмов» (метод испытаний по ISO 846) Данный показатель характеризует биостойкость ДПК. На величину показателя влияет наличие биоциодов, вид целлюлозного наполнителя (порода древесины), содержание и размер древесных частиц, вид механической обработки поверхности профиля (гладкий, шлифовка, брашинг). Испытание проводится по двум тестам:
Метод A: тест на грибостойкость. Образцы помещаются на несовершенный агар (без источника углерода) и инокулируются суспензией спор различных грибов. Грибы могут развиваться только за счет материала пробы в отсутствии иных органических источников питания. Пороговое значение: На образцах должны отсутствовать следы роста грибов при всех вариантах тестирования: без обводнения, с обводнением, с обводнением и воздействием УФ, в т.
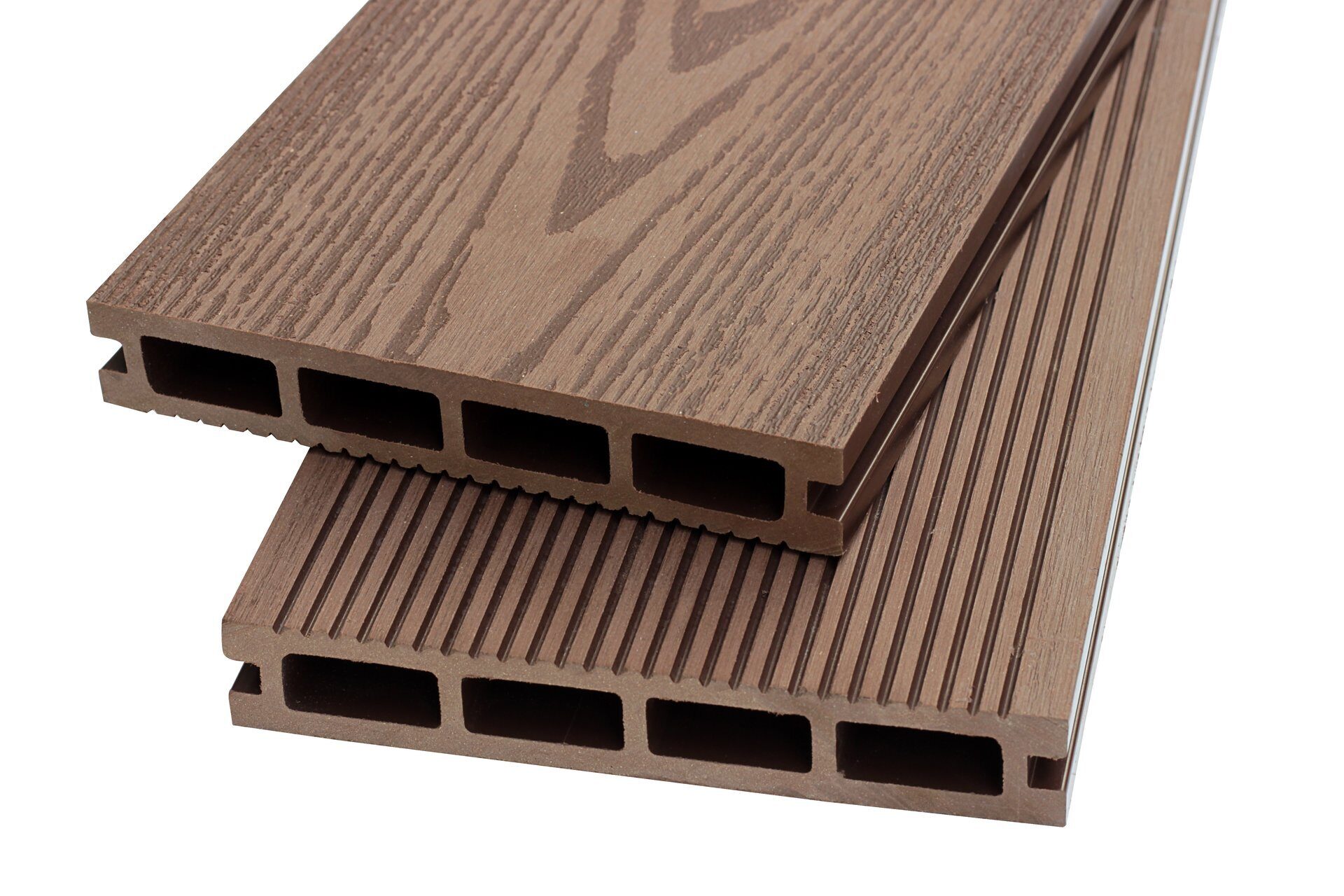
Метод B: определения фунгистатического действия.Образцы помещаются на совершенный агар (с источником углерода) и инокулируются суспензией спор различных грибов. Даже если в образцах нет питательных веществ, которые могут усваиваться микроорганизмами, грибы могут развиваться на их поверхности, а продукты их обмена могут разрушать материал. Методика отражает ситуацию загрязнения поверхности на практике (органическими отложениями, другими загрязнениями и пр.).
Пороговое значение: На образцах должны отсутствовать следы роста грибов при всех вариантах тестирования: без обводнения, с обводнением, с обводнением и воздействием УФ, в т.ч. под микроскопом.
Опыт натурных испытаний ДПК в условиях атмосферных воздействий показал, что три последних показателя №10, №11 и №12 в наибольшей степени подвержены негативным воздействиям и соответственно характеризуют долговечность ДПК.
Значения показателей установлены на основе 2-х летнего опыта испытаний образцов террасной доски, в том числе ведущих европейских производителей, а также наблюдений за изменением свойств образцов под воздействием атмосферных факторов в условиях климатической зоны Подмосковья.

Библиографический список:
Журнал Пластинфо №9-02/16(58) стр.1,стр10,2012г;
Журнал Пластикс №1-2(107-108)2012г;
Пост-релиз «Древесно-полимерные композиты 2012: Цена доверия», creonenergy.ru
„Quality and Testing Specifications for Production Control for Terrace Decking made from Wood-Polymer Composites“, version 01.03.2012. The „Qualitätsgemeinschaft Holzwerkstoffe e.V.“ (Quality Association for WoodbasedPanels, registered association), Giessen, Germany.
Галина Пресман
Доска из древесно-полимерного композита — применение и назначение
Древесно-полимерный композит (ДПК) является смесью, в составе которой имеется полимер (химический или натуральный), а также древесный наполнитель, модифицированный, чаще всего, химическими агентами. Этот материал называют и «жидкое дерево», и дерево-пластиковый композит, и древопласт, и поливуд. Главная особенность такого материала состоит в том, что конечный продукт получается, фактически из отходов производства и потребления, таких как опилки, стружка, древесная мука, сельскохозяйственные отходы и разные виды отходов потребления. Сегодня создаются методы, которые дают возможность применять в процессе производства не первичные, а вторичные полимеры.
Что это такое?
Внешне древесно-полимерный композит с большим содержанием древесины очень похож на МДФ или твердую ДВП, а с малым ее количеством – на пластмассу. Такой материал отлично поддается пилению, строганию рубанком. В него легко вбиваются гвозди. Также его можно красить обычными красками и эмалями, или отделывать синтетическими пленками, натуральным шпоном.
Древесно-полимерный композит является суперсовременным материалом. ДПК обладает всеми лучшими природными свойствами древесины, но при этом лишен таких его недостатков, как склонность к гниению и плесени, горючесть, изъяны поверхности, восприимчивость к влаге.
В составе ДПК присутствует:
- древесная мука (или измельченные щепки), размером от 0,5 до 2 мм
- полимер, в качестве которого может выступать ПВХ, полиэтилен или полипропилен
- аддитивы.
Изготовление экструзионных древесно-полимерных композитов можно назвать одним из самых перспективных направлений в сфере рационального использования остатков лесопильного, мебельного и деревообрабатывающего производств, применения лесоматериалов низкого сорта, растительных отходов, в которых много целлюлозы, вторичных пластмасс для создания высококачественных профильных деталей.
Преимущества древесно-полимерного композита
К основным плюсам такого материала можно отнести:
- доску из ДПК не нужно красить каждый год
- террасная доска во время дождя не скользит, потому что имеет рифленую поверхность
- материал выдерживает колоссальные перепады температурного режима (от -50°С до +50°С)
- высокая прочность. Изделия из этого материала выдерживают большие нагрузки, что дает возможность применять их в качестве настилов даже на автомобильных парковках.
Наиболее популярен ДПК в таких сферах деятельности:
- строительство. В этой отрасли он использует для наружной обшивки домов, создания дверных и оконных профилей, панелей, а также для отделки проемов, фронтонных досок
- ландшафтный дизайн. Из полимерно-древесного композита изготавливают настилы (декинги), тротуары, изгороди, заборы, садовую архитектуру (скамейки, беседки), надворные сооружения, детские площадки. Также им отделывают бассейны и используют как напольное покрытие
- внутренняя отделка. В этой отрасли из ДПК создаются перила, лестницы, ставни, декоративные профиля, отделочные панели, кухонные встроенные шкафы, паркет, офисная мебель, полки, плинтуса, звукоизоляционные панели
- промышленность. Из «жидкого дерева» создают мосты, транспортные поддоны, тару, пирсы, морские сваи и переборки, железнодорожные детали (шпалы), контейнеры для мусора, таблички, вывески.
Доска из древесно-полимерного композита
Декинг, или другими словами террасная доска из древесно-полимерного композита является наиболее современным материалом среди уличных напольных покрытий. Древесная мука и полимер наделяют уникальными свойствами данный материал. Период эксплуатации такой доски достигает 40 лет. Такому материалу необходима ежегодная антисептическая обработка и покраска.
Основные свойства:
- нет скольжения даже в мокром виде
- высокие показатели прочности и износостойкости
- температурный режим от -50 до +80 0С
- не восприимчив к влажности, может использоваться под открытым небом
- не боится ультрафиолетовых лучей, не выцветает, не гниет, не плесневеет.
Сегодня производят такие типы террасной доски:
- шовные, имеют шов от 2 до 6 мм. Они используются на больших площадях, свыше 300 м2, где нужно гарантировать большой отток воды
- бесшовные. Такие доски идеально подходят для летних кафе, в которых нужно сделать монолитное покрытие
- полнотелые используются на пирсах и палубах кораблей
- пустотелые. Эта доска имеет меньший вес, и следовательно, меньшую цену
- с полимером ПВХ. Обладают лучшей износостойкостью, большой устойчивостью к ультрафиолету, прочностью
- с полиэтиленом. Отличается невысокой стоимостью
- шлифованные доски
- брашированные, обработанные щетками, то есть состаренные
- тисненные, имеющие текстурный узор
- эмбоссинг, с фактурой натурального дерева.
Устанавливать доски из ДПК легче, чем деревянные доски.
Производство древесно-полимерного композита
ДПК – является инновационным материалом, технология изготовления которого базируется на смешивании муки, PE, PP, ПВХ и прочих составляющих с помощью особого оборудования, согласно установленным стандартам.
Для того, чтобы создать древесно-полимерный композит необходимо, прежде всего, измельчить древесное сырье. После измельчения древесину нужно тщательно высушить. Далее следует этап четкого взвешивания и отмеривания компонентов. После смешивания всех ингредиентов происходит экструдирование материала. Заключительным этапом производства является обрезка по длине, а также разрезание по ширине.
Схема производства ДПК очень похожа на создание плит ДСП. Однако реализация процесса происходит на оборудовании химического типа, т.е. пластмассовой промышленности. Такие установки довольно компактны, то есть для них не нужно большое помещение. Предприятия, выпускающие ДПК, эффективны даже при малых объемах производства, следовательно, несравнимы с масштабами заводов ДСП или МДФ.
Рынок древесно-полимерного композита
Сегодня мировой рынок ДПКТ пребывает в стадии роста, и каждый год растет примерно на 18-20%. По последним данным даже на американском рынке не наблюдается точка насыщения. В ближайшие годы ожидается бум потребления и производства древесно-полимерных композитов.
Принимая во внимание периоды жизненного цикла рынка, динамику роста потребления и производства в России и других государствах, потенциал российского рынка древесно-наполненных композитов колоссален.
Сфера использования этого материала очень широка. В России главной областью использования является строительство. Также, согласно данным аналитиков, в ближайшие годы древесные композиты будут активно применяться в автомобильной отрасли и в производстве мебели.
Этот материал отличается высокой стойкостью к влиянию внешней среды, перепадам температур, он более долговечен в сравнении с древесиной и древесными плитами. Такие свойства крайне важны в условиях сурового климата большей части нашего государства. Изготовление предметов уличной мебели из ДПКТ (лавок, перил, настилов) отличается более высоким качеством. Вследствие способности древесных полимеров принимать любую форму в ходе производства, мебельщики имеют возможность более широкого применения элементов дизайна и креативных идей во время проектирования мебели.
ЭЗКМ / Древесно-полимерный композит, ДПК, террасная доска, декинг, изделия из композитов
и изделия из них. Террасная доска и декинг.
Древесно-полимерный композит (ДПК) – материал, в составе которого содержится полимер (химический или натуральный) и древесный наполнитель, наполненный химическими добавками. Вот несколько названий древесно-полимерного композита: «жидкое дерево», древопласт, дерево-пластиковый композит, поливуд, вуд полимер композит, древотермопласт, wpс, вуд пластик композит, ЭДНП (экологически чистые древеснонаполненные пластмассы), ДНПП (древеснонаполненный полипропилен).
Готовый древесно-полимерный композит получается благодаря отходам производства и потребления. Для его изготовления используются опилки, стружки, мука древесная, отходы сельского хозяйства и другие виды отходов потребления. В процессе разработки технологии, которые позволят использовать не первичные, а вторичные полимеры в процессе производства композитов.
Своим внешним видом профиль древесно-полимерного композита, в котором содержится много древесины очень походит на МДФ или твердую ДВП. А при малом содержании древесины профиль композита имеет вид пластмассы. Этот материал легко подвергается распилу, строганию рубанком, вбиванию гвоздей. Древесно-полимерный композит отлично окрашивается красками и эмалями, подвергается облицовке синтетическими пленками или натуральным шпоном.
Рынок жидкого дерева на российских просторах развивается ещё на начальном этапе. Однако при скором усилении государственного регулирования в сфере таких производств как деревообработка и переработка отходов, древесно-полимерный композит получит ещё один стимул для успешного применения в России. Ожидается хороший спрос на изделия, основываются все новые и новые производства. Такой материал начал пользоваться конкретным вниманием у инвесторов и производителей.
Древесно-полимерный композит – один из самых современных и востребованных материалов. ДПК обладает лучшими природными свойствами дерева, однако у него отсутствуют такие недостатки, как гниение и образование плесени, быстрая сгораемость, поверхностные дефекты и впитывание влаги.
Материал ДПК состоит из древесной муки с фракцией 0,5-2мм, а также из полимера и аддитивы. За полимер может быть взят ПВХ (50/50), полиэтилен (70/30) или полипропилен (60/40).
Производство древесно-полимерных композитов и изделий из них является очень перспективным. Это происходит благодаря рациональному применению отходов с лесопилок, мебельных и деревообрабатывающих отходов. Приветствуется применение древесины низкого сорта, растительных отходов содержащих целлюлозу и вторичных пластмасс. Благодаря чему происходит переработка в профильные детали высокого качества для широкой области применения, включая строительство и мебельное производство.
Примеры изделий из древесно-полимерных композитов:
НА ГЛАВНУЮ СТРАНИЦУ
Фасад из древесно-полимерного композита (ДПК)
Фасад из древесно-полимерного композита (ДПК) будет служить гораздо дольше по сравнению с обычным деревом, устойчив к перепадам температуры и погодных условия, имитирует внешней вид натурального дерева, не прихотлив в эксплуатации, не требует специальной обработки и покраски. Фассадные панели из ДПК на 30% больше удерживают тепло и на 50% больше увеличивают шумоизоляцию, по сравнению с обычным деревом. Таким образом, приобретая более долговечные материалы, вы экономите на отопление, при этом получая более высокую шумоизоляцию и комфорт. Фасады из древесно-полимерного композита очень долговечны, и имеют срок службы более 35 лет!
Облицовка дома сайдингом из ДПК – это самый простой и надежный способ придать Вашему дому эстетичный вид, защитив его фасад от капризов погоды. Сайдинг из ДПК выгодно отличается от обычного дерева, за счет своего качества и долговечности. Выбирая облицовку фасада из древесно-полимерного композита (ДПК) вы приобретаете красоту и долговечность вашего дома!
Сайдинг, фасадная панель или планкен из древесно-полимерного композита позволяет выполнить такую обшивку, которая будет сочетать в себе как современный дизайн, так и все необходимые свойства для обеспечения комфорта:
- свойства теплопроводности и звукоизоляции – поскольку в состав ДПК входит древесина, то этот материал обладает ее лучшими свойствами, которые идеально подходят для наружной отделки жилых помещений;
- высокая устойчивость к воздействию влажности – входящие в состав ДПК пластмассовые компоненты не позволяют материалу как накапливать, так и выделять влагу, что исключает вероятность усушки и появления трещин в покрытии;
- повышенная огнестойкость – ДПК-сайдинг не подвержен возгоранию и хорошо выдерживает воздействие высоких температур;
- устойчивость к агрессивным агентам окружающей среды – ДПК не подвержен воздействию коррозии, гниению, влиянию химических веществ;
- податливость в обработке – древесные компоненты ДПК позволяют легко шлифовать материал, придавая ему необходимую фактуру;
- долговечность – гарантийный срок эксплуатации фасада из древесно-полимерного композита составляет не менее четверти века. Даже по истечении этого времени обшивка будет радовать глаз своим видом и свойствами;
- простота в уходе – мытье с использованием воды и чистящих средств идеально подходит для этого материала.
Достижения и проблемы древесно-полимерных композитов
Лесная служба США
Забота о земле и служение людям
Министерство сельского хозяйства США
Достижения и проблемы древесных полимерных композитов
Автор (ы): Роджер М. Роуэлл
Дата: 2006
Источник: Труды 8-го симпозиума по биокомпозитам Тихоокеанского региона, Достижения и проблемы биокомпозитов : 20–23 ноября 2006 г., Куала-Лампер, Малайзия.Кепонг, Малайзия: Институт лесных исследований Малайзии, c2006: ISBN: 9832181879: 9789832181873: страницы 2-11.
Серия публикаций: Прочие публикации
PDF: Скачать публикацию (235 КБ)
Описание Древесная мука и волокно были смешаны с термопластами, такими как полиэтилен, полипропилен, полимолочная кислота и поливинилхлорид, для образования древесно-пластиковых композитов (ДПК). В последние годы в Соединенных Штатах наблюдается значительный рост WPC, в основном на рынке настилов для жилых домов, когда настилы из обработанной древесины CCA были удалены с рынков жилых домов.Несмотря на то, что есть много успехов, о которых следует сообщить в WPC, все еще есть некоторые проблемы, которые необходимо решить, прежде чем эта технология достигнет своего полного потенциала. это вопросы разделения фаз и совместимости. Эта технология также включает две очень разные отрасли; деревообрабатывающая и / или сельскохозяйственная промышленность и пластмассовая промышленность. Обработка двух фаз представляет проблемы, связанные с максимальным смешиванием при минимальном повреждении композиции биомассы.Индекс текучести расплава, температуры обработки, статическое электричество и плотность также являются проблемами для пластмассовой промышленности, которая привыкла к условиям обработки с высокой текучестью и высокой температурой, необходимым при экструзии пластмасс в чистом виде или при использовании неорганических наполнителей, таких как стекло, карбонат кальция или тальк. В то время как биомасса в композите набухает и сжимается из-за влаги, пластическая фаза набухает и сжимается из-за температуры. Циклы замораживания и оттаивания также вызывают проблемы, а также последствия атаки микроорганизмов и ультрафиолетового излучения.Крашение, повторная окраска, стабильность цвета и застежки также вызывают беспокойство. Экструзия твердых материалов, экструзия профилей, коэкструзия, литье под давлением и термическое формование используются для производства различных изделий из ДПК в разных частях мира. Примечания к публикации- Мы рекомендуем вам также распечатать эту страницу и прикрепить ее к распечатке статьи, чтобы сохранить полную информацию о цитировании.
- Эта статья была написана и подготовлена государственными служащими США в официальное время и поэтому находится в открытом доступе.
XML: Просмотр XML
Показать больше
Показать меньше
https: // www.fs.usda.gov/treesearch/pubs/25693
Использование и преимущества древесно-пластикового композитного материала
Если вы планируете начать строительный проект в ближайшем будущем, то вы знаете, насколько сложно найти строительный материал, отвечающий вашим требованиям. В связи с последними нововведениями на сцене появился новый материал, заставляющий кружиться головы.
Этот материал — ДПК, и он может навсегда изменить будущее строительства. (Если вы не знакомы с WPC, читайте дальше и узнайте, как этот новичок может изменить ваш проект.)
Что такое древесно-пластиковый композит?
Как следует из названия, древесно-пластиковый композит (ДПК) представляет собой материал, созданный из уникальной смеси натурального дерева и пластиковых волокон. Опилки, целлюлоза, бамбук, скорлупа арахиса и неиспользованные деревообрабатывающие материалы, такие как кора, из различных проектов, объединяются с пластиковым порошком для образования WPC.
Что самое примечательное в древесно-пластиковом композитном материале, так это то, что его можно полностью создать из переработанных материалов, собранных на предприятиях C&D, на предприятиях по производству изделий из дерева и т. Д.В довершение всего, использованный WPC можно даже переработать для создания совершенно нового WPC, что делает его идеальным вторичным товаром.
Почему WPC такой захватывающий?
Поскольку древесно-пластиковый композит создается из вещества, которое начинается в виде пасты, ему можно придать практически любую форму и размер, включая дугообразные или изогнутые формы. Эта врожденная гибкость распространяется и на цвет — WPC можно красить или раскрашивать в соответствии практически с любой схемой дизайна.
С функциональной точки зрения древесно-пластиковый композит является влагостойким и устойчивым к гниению, а это означает, что он эстетически и цельно прослужит дольше, чем обычная древесина.Кроме того, WPC более термостойкий, чем обычные пиломатериалы, поэтому продукт можно использовать в местах, где обычные пиломатериалы могут гнуться или деформироваться.
Настоящая альтернатива пиломатериалам
В зависимости от того, с каким материалом смешиваются опилки — полиэтиленом или полипропиленом — ДПК можно использовать в различных строительных проектах так же, как натуральные пиломатериалы. Сверление, строгание, шлифование; С ДПК все это делается так же легко, как и с деревом.
Специалисты в области строительства могут даже обнаружить, что деревянные крепежи, такие как гвозди и шурупы, на самом деле обеспечивают лучшую фиксацию в ДПК по сравнению с обычным деревом.Кроме того, WPC с меньшей вероятностью расколется или сломается, когда шурупы используются рядом с концом досок, что может быть обычной проблемой при использовании натурального дерева.
WPC может бросить вызов стихиям
Благодаря специализированному и настраиваемому составу WPC, этот материал уникально приспособлен к изменениям погоды с меньшими повреждениями, чем средний материал. Если вы ищете материал, который выдержит испытание временем для вашего следующего проекта, возможно, WPC вам подойдет.
General Kinematics знает, насколько важны новые экологичные строительные материалы, такие как WPC.Вот почему мы гордимся тем, что производим и поставляем продукты, которые помогают в переработке и сортировке товаров C&D, древесины, лесного хозяйства и пластмассы для создания таких материалов, как WPC.
Посетите наш стенд на выставке WasteExpo 2017 с 8 по 11 мая, чтобы узнать больше об оборудовании GK для вторичной переработки. Мы хотели бы показать вам и вашей команде все преимущества, которые может предложить General Kinematics!
(PDF) Древесно-полимерные композиты
Древесно-полимерные композиты
283
Тимара, М.; Питманб А. и Михай М. (1999). Биологическая устойчивость химически модифицированных композитов из осины
, International Biodeterioration & Biodegradation Vol. 43: 181-187
Tshabalala, M .; Kingshott, P .; Ван Ландингем М. и Плакетт Д. (2003). Химия поверхности
и влагосорбционные свойства древесины, покрытой многофункциональными алкоксисиланами
с помощью золь-гель процесса, Journal of Applied Polymer Science Vol. 88: 2828-2841
Винсент, Дж.(2002). Выживание самых дешевых, Материалы сегодня, Том 5 (№ 12): 24–41.
Валлстрём, Л. и Линдберг, К. (1999). Измерение проникновения в клеточную стенку древесины
химикатов на водной основе с использованием методов SEM / EDS и STEM / EDS, Wood Science
и Technology Vol. 33: 111-122
Wang, Y .; Минато Л. и Иида И. (2007). Механические свойства древесины в нестабильном состоянии
из-за изменений температуры и анализ соответствующего механизма III: влияние закалки
на релаксацию напряжений в химически модифицированной древесине, Journal of Wood
Science Vol.53 (№ 2): 94-99.
Westin, M .; Рапп А. и Нильссон Т. (2006). Полевые испытания устойчивости модифицированной древесины к воздействию
морских бурильных машин, Wood Material Science and Engineering Vol.1: 34-38
Witt, A. (1977). Применения в древесных пластиках. Радиационная физика и химия Том 9 (№ 1-3):
271-288
Witt ,. A.E .; Henise, P.D. И Griest, L.W. (1981). Акриловая древесина в США, Радиационная
Physics and Chemistry Vol.18 (No. 1-2): 67-80
Yalinkilic, M.; Gezer, E .; Takahashi, M .; Demirci, Z .; Иихан, Р., Имамура, Ю. (1999). Бор
Добавление к сшивающим реагентам без формальдегида или с низким содержанием формальдегида для повышения
биологической устойчивости и размерной стабильности древесины. Европейский журнал древесины
и изделий из дерева, том 57 (№ 5): 351-357.
Yamamoto, Y .; Nakao, W .; Atago, Y .; Ито К. и Ягчи Ю. (2003). Новый макроинимер полиэтиленоксида
: синтез гиперразветвленных сетей с помощью фотоиндуцированного процесса абстракции H-
.European Polymer Journal Vol.39 (№ 3): 545–550
Yap, M .; Чиа, Л. и Теох, С. (1990). Древесно-полимерные композиты из тропической древесины твердых пород I:
Свойства WPC, Journal of Wood Chemistry and Technology 10 (1): 1–19.
Яп, М .; Que, Y. & Chia, L. (1991a). Динамический механический анализ композитов из полимеров древесины тропических пород
, Журнал прикладной науки о полимерах, том 43 (№ 11): 1999-2004 гг.
Яп, М .; Que, Y .; Чиа, Л. и Чан, Х. (1991b). Термические свойства композитов из полимеров тропической древесины
, Journal of Applied Polymer Science Vol.43 (№11): 2057-2065
Яп, М .; Que, Y. & Chia, L. (1991c). FTIR характеристика композитов тропическая древесина-полимер
, Journal of Applied Polymer Science Vol.43: 2083-2090
Yildiz, Ü; Йылдыз, С и Гезер, Э. (2005). Механические свойства и сопротивление гниению древесины —
Полимерные композиты, полученные из быстрорастущих видов в Турции, Bioresouce
Technology Vol.96 (No. 9): 1003-1011.
Янг Р., Роуэлл Р. (1986). Целлюлоза: структура, модификация и гидролиз, В: Янг,
R.; Роуэлл, Р. (ред.), В: Wiley Interscience, 3-50, ISBN 0471827614, Нью-Йорк
Янгквист, Дж. (1995). Брак древесины и недревесных материалов. Лесной журнал
Том 45 (№ 10): 25-30.
Zhang, Y .; Чжан С. и Чуй Ю. (2006). Адсорбция водяного пара и объемное набухание
древесно-полимерных композитов, пропитанных расплавом, Journal of Applied Polymer Science
Vol. 102: 2668-2676
Древесно-полимерные композиты — последние достижения и области применения | Санджай Мавинкере Рангаппа
Доктор.Санджай Мавинкере Рангаппа в настоящее время работает научным сотрудником, а также советником в офисе президента по продвижению и развитию университетов для достижения международных целей в Технологическом университете короля Монгкута в Северном Бангкоке, Бангкок, Таиланд. Он получил степень бакалавра E (машиностроение) в 2010 году, степень магистра технических наук (вычислительный анализ в механических науках) в 2013 году, докторскую степень (факультет машиностроения) Технологического университета Висвесварая, Белагави, Индия, в г. 2017 год и докторская степень Технологического университета короля Монгкута в Северном Бангкоке, Таиланд, в 2019 году.Он является пожизненным членом Индийского общества технического образования (ISTE) и ассоциированным членом Института инженеров (Индия). Он является членом совета директоров различных международных журналов в области материаловедения и композитов. Он является рецензентом более чем 85 международных журналов (для Nature, Elsevier, Springer, Sage, Taylor & Francis, Wiley, Американского общества испытаний и материалов, Американского общества сельскохозяйственных и биологических инженеров, IOP, Hindawi, NC State University USA, ASM International, Emerald Group, Bentham Science Publishers, Universiti Putra, Малайзия), также рецензент предложений книг и международных конференций.Он опубликовал более 130 статей в высококачественных международных рецензируемых журналах, 5 редакционных уголках, 35 глав книг, одну книгу, 15 книг в качестве редактора, а также представил исследовательские работы на национальных и международных конференциях. Кроме того, он зарегистрировал 1 патент Таиланда и 5 патентов Индии. Его текущие области исследований включают композиты из натурального волокна, полимерные композиты и передовые технологии материалов. Он является получателем программы DAAD Academic exchange — PPP (Project-related Personnel Exchange) между Таиландом и Германией в Институте композитных материалов Университета Кайзерслаутерна, Германия.Он получил награду Top Peer Reviewer 2019, Global Peer Review Awards, Powered by Publons, Web of Science Group. KMUTNB выбрал его для вручения премии «Выдающийся молодой исследователь 2020». Он включен в список 2% самых цитируемых ученых в мире по результатам одного года цитирования в 2019 году в списке Стэнфордского университета.
Д-р Джиотишкумар Парамесваранпиллай, в настоящее время работает профессором-исследователем в Центре инноваций в дизайне и проектировании для производства Технологического университета короля Монгкута в Северном Бангкоке.Он получил докторскую степень. Кандидат технических наук и технологий полимеров (химия) Университета Махатмы Ганди. Он имеет опыт исследований в различных международных лабораториях, таких как Институт исследования полимеров им. Лейбница в Дрездене (IPF), Германия, Католический университет Левена, Бельгия и Потсдамский университет, Германия. Он опубликовал более 100 статей в высококачественных международных рецензируемых журналах по полимерным нанокомпозитам, полимерным смесям и сплавам и биополимерам, а также отредактировал пять книг. Он получил множество наград и признаний, в том числе престижную премию штата Керала лучшему молодому ученому 2016 года, премию факультета INSPIRE 2011 года, премию лучшего исследователя 2019 года Технологического университета короля Монгкута в Северном Бангкоке.
Доктор Мохит Хемат Кумар, получил степень бакалавра искусств. (Машиностроение) из Университета Анна, Ченнаи, Тамилнад, Индия, в 2012 году, и ME (Тепловая инженерия со специализацией в области холодоснабжения и кондиционирования воздуха) из инженерного колледжа Гуинди Кампус, Университет Анна, Ченнаи в 2014 году. его докторская степень. окончил факультет машиностроения Национального технологического института Тиручираппалли в 2019 году и защитил докторскую диссертацию в Технологическом университете короля Монгкута в Северном Бангкоке, Таиланд.Он является пожизненным членом Института инженеров (Индия), Ассоциации порошковой металлургии Индии (Индия), Общества анализа отказов (Индия) и Ассоциации научно-технических исследований (Сингапур). Кроме того, он опубликовал более 10 статей в высококачественных международных рецензируемых журналах, более 5 глав книг, а также представил исследовательские работы на национальных и международных конференциях. К настоящему времени он зарегистрировал более 20 патентов и 15 промышленных образцов, а также выдал два патента и семь промышленных образцов в рамках прав интеллектуальной собственности Индии.В настоящее время он занимается исследованиями в области полимерных нанокомпозитов на основе натуральных волокон и неорганических наполнителей, композитов с металлической матрицей и разработки инновационных промышленных продуктов.
Проф. Д-р техн. habil. Сухарт Сиенгчин — президент Технологического университета короля Монгкута в Северном Бангкоке. Он получил степень дипл. Инж. Кандидат технических наук в Университете прикладных наук Гиссена / Фридберга, Гессен, Германия, 1999 г., степень магистра наук. получил степень магистра в области полимерных технологий Университета прикладных наук Аалена, Баден-Вюртемберг, Германия, 2002 г., M.Sc. Имеет степень доктора наук в области материаловедения в Университете Эрлангена-Нюрнберга, Бавария, Германия, в 2004 году, доктор философии в области инженерии (Dr.-Ing.) из Института композитных материалов, Университет Кайзерслаутерна, Рейнланд-Пфальц, Германия, в 2008 году и постдокторские исследования из Кайзерслаутерна. Университет и школа материаловедения, Университет Пердью, США. В 2016 году получил абилитацию в университете Хемница в Сахене, Германия. Он работал преподавателем кафедры производства и материаловедения в Международной тайско-немецкой высшей школе инженерии Сириндхорн (TGGS), KMUTNB.Он был профессором в KMUTNB и стал президентом KMUTNB. Он выигрывал премию «Выдающийся исследователь» в KMUTNB в 2010, 2012 и 2013 годах. Его исследовательские интересы в области обработки полимеров и композитных материалов. Он является главным редактором Международного журнала прикладной науки и технологий KMUTNB и автором более 250 рецензируемых журнальных статей, 8 редакционных углов, 50 глав книг, одной книги и 20 книг в качестве редактора. Он участвовал с презентациями на более чем 39 международных и национальных конференциях по темам материаловедения и инженерии.Он признан и входит в число 2% лучших ученых мира, перечисленных престижным Стэнфордским университетом.
Сравнение древесно-полимерных композитов с массивной древесиной: пример устойчивости террасных полов
Bergman R, Han H, Oneil E, Eastin I (2013) Оценка жизненного цикла настилов из красного дерева в США по сравнению с тремя другие отделочные материалы. Заключительный отчет CORRIM. Вашингтонский университет, Сиэтл
Google Scholar
Болин С.А., Смит С.Т. (2011) Оценка жизненного цикла пиломатериалов, обработанных ACQ, по сравнению с древесно-пластиковым композитным настилом.J Clea Prod 19: 620–629
CAS Статья Google Scholar
Brueck C (2009) WPC — Produkte für einen wachsenden Markt (WPC — продукты для растущего рынка) (на немецком языке). http://www.nova-institut.de/ppnf/data/File/Dokumente/Kosche_Praesentation-Koeln-13022008-1-2.pdf. По состоянию на 24 февраля 2009 г.
Dupui F (2011), личное сообщение. Holzwelt Baier GmbH & Co, Вюрцбург
Google Scholar
Frischknecht R, Jungbluth N, Althaus HJ, Doka G, Hellweg S, Hischier R, Nemecek T., Rebitzer G, Spielmann M (2007a) Обзор и методология.Отчет Ecoinvent No. 1
Frischknecht R, Jungbluth N, Althaus HJ, Doka G, Dones R, Hellweg S, Hischier R, Nemecek T., Rebitzer G, Spielmann M (2007b) Свод правил. Отчет Ecoinvent No. 2
Frischknecht R, Jungbluth N, Althaus HJ, Doka G, Dones R, Hirschier R, Hellweg S, Humbert S, Margni M, Nemecek T., Spielmann M (2007c) Внедрение методов оценки воздействия жизненного цикла. Отчет Ecoinvent No. 3
Ibach RE (2010) Прочность древесно-пластиковых композитных пиломатериалов.В: McGraw-Hill (ed) Yearbook of Science & Technology 2010. McGraw-Hill Companies, стр. 113–116
ISO 14040 (2006a) Экологический менеджмент — оценка жизненного цикла — принципы и рамки
ISO 14044 (2006b) Экологический менеджмент — оценка жизненного цикла — требования и руководящие принципы
Jungbluth N, Busser S, Frischknecht R, Flury K, Stucki M (2012) Возможность получения экологической информации о продукте на основе анализа жизненного цикла и рекомендаций для Швейцарии.J Clea Prod 28: 187–197
Статья Google Scholar
Kurt Obermeier GmbH & Co. KG (2010) Technisches Merkblatt Koralan Holzöl (Технический бюллетень Koralan Wood Oil) (на немецком языке). Статус 07/2010
Müller M (2011) Личное сообщение. Universität Göttingen, Abteilung Holzbiologie und Holzprodukte
Nova (2012) Nova-Institut Pressemitteilung WPC-Kongress mit neuen Marktdaten WPC (Пресс-релиз Конгресса WPC с новыми рыночными данными WPC) (на немецком языке).http://www.wpc-kongress.de/wpc2011/data/uploads/File/12-01-10PMWPC.pdf. По состоянию на 21 февраля 2012 г.
Osmo (2011) Volldeklaration Holz-Spezial-Öle (полная декларация специальных масел для древесины) (на немецком языке). Osmo Holz und Color GmbH & Co, Варендорф
Google Scholar
RÜTGERS Organics GmbH (2010) impralit ® -KDS 4 — Technisches Merkblatt (impralit ® -KDS 4 — Technical Bulletin) (на немецком языке) Mannheim
Schneckener H (2011) Личное сообщение.Fa Jenz GmbH Maschinen und Fahrzeugbau, Petershagen
Google Scholar
Сегерхольм Б.К., Ибах Р.Э., Велиндер Е.П. (2012) Сорбция влаги в искусственно состаренных древесно-пластиковых композитах. Биоресурсы 7 (1): 1283–1293
Google Scholar
Soiné H (1995) Holzwerkstoffe — Herstellung und Verarbeitung (древесные плиты — производство и обработка) (на немецком языке). DRW-Verlag, Лайнфельден
Google Scholar
Старк Н. М., Гарднер Д. Д. (2008) Долговечность древесно-полимерных композитов на открытом воздухе.В: Саин М., Оксман Ниска К. (ред.) Древесно-полимерные композиты. Woodhead Publishing / CRC Press, Кембридж / Бока-Ратон, стр. 142–165
Google Scholar
Vogt C, Karus M, Ortmann S, Schmidt C, Gahle C (2006) Древесно-пластиковый композит — Märkte в Нордамерике, Япония и Европа мит Schwerpunkt auf Deutschland (Древесно-пластиковый композит — рынки Северной Америки. Япония и Европа с особым вниманием к Германии) (на немецком языке), Hürth
Google Scholar
Wagenführ R (2000) HOLZatlas-5, ergänzte und erweiterte Auflage (WOODatlas-5, исправленное и дополненное издание) (на немецком языке).Carl Hanser Verlag, München, Wien
Google Scholar
Wegener G, Zimmer B, Nebel B (2004) Analyze der Transportketten von Holz, Holzwerkstoffen und Restholzsortimenten als Grundlage für Produktbezogen Ökobilanzen (Анализ транспортных цепей для древесины, древесных плит и остаточной древесины как основы жизненного цикла продукции). оценки цикла), München / Kuchl (на немецком языке)
Древесно-полимерная композитная мебель подлежит вторичной переработке, имеет низкую воспламеняемость
Дерево — популярный материал в дизайне интерьеров, но его водопоглощение ограничивает его использование в ванных комнатах, где натуральное дерево легко обесцвечивается или покрывается плесенью.Ученые и партнеры Fraunhofer разработали древесно-полимерный композитный материал для мебели, устойчивый к влажности и обладающий низкой горючестью.
Ресурсосберегающие древесно-полимерные композиты (ДПК) — это последняя тенденция в материалах для садовой мебели и других наружных применений, особенно для настилов террас, а также для обшивки и ограждений. В рамках спонсируемого ЕС проекта LIMOWOOD исследователи из Института исследования древесины им. Фраунгофера, Wilhelm-Klauditz-Institut WKI в Брауншвейге теперь сотрудничают с промышленными партнерами в Бельгии, Испании, Франции и Германии в разработке материалов, подходящих для прессования в влагостойкие плиты WPC для изготовления внутренней мебели.
Эти плиты состоят примерно на 60 процентов из древесных частиц и на 40 процентов из термопластического материала, обычно полипропилена или полиэтилена. Как деревянные, так и пластмассовые компоненты могут быть получены из потоков вторичной переработки. Древесный компонент в плитах WPC может быть заменен другими продуктами из лигноцеллюлозы, полученными из волокнистой части растений, таких как конопля или хлопок, или шелухой рисовых зерен и семян подсолнечника. Все эти материалы подлежат 100% вторичной переработке. Кроме того, прессованные плиты WPC, произведенные исследователями WKI, не содержат формальдегид.«Спорный вопрос о выбросах формальдегида из-за связующего, используемого в традиционных прессованных деревянных изделиях, в данном случае не является проблемой», — говорит исследователь WKI д-р Арне Ширп.
Выбрав соответствующие добавки, исследователи смогли улучшить огнезащитные свойства своих плит из ДПК. Первоначально они разработали свою формулу в лабораторных масштабах, используя коммерчески доступные антипирены, не содержащие галогенов, которые добавляли в древесно-полимерную смесь во время фазы плавления.Первым шагом было определение предельного кислородного индекса испытуемого объекта: этот параметр определяет поведение пластмасс или древесно-наполненных пластиковых компаундов при воздействии огня. Он представляет собой минимальную концентрацию кислорода, при которой материал будет продолжать гореть после возгорания. Чем выше это значение, тем ниже воспламеняемость материала. Ширп и его коллеги получили наилучшие результаты с комбинацией антипиренов, таких как красный фосфор и расширенный графит.Предельный кислородный индекс плит WPC, обработанных таким образом, увеличивается до 38 процентов при условии, что содержащиеся в них древесные частицы также являются огнестойкими. Для сравнения: предельный кислородный индекс стандартной древесностружечной плиты составляет 27 процентов, а необработанной плиты ДПК — 19 процентов. Даже в испытании с одним источником пламени, в котором горелка Бунзена прижимается к испытуемому образцу, обработанные плиты из ДПК продемонстрировали высокую огнестойкость. Даже после воздействия 300 секунд доски не загорелись.Напротив, контрольные образцы — стандартной древесно-стружечной плиты и необработанной плиты ДПК — загорелись и продолжали гореть.
Подробнее на: http://phys.org/news/2015-05-wood-polymer-composite-furniture-flammability.html
Древесно-пластмассовые композиты сделано правильно | Технология пластмасс
Изделия из древесно-пластикового композита (ДПК) впервые стали широко продаваться в начале 1990-х годов как устойчивые к атмосферным воздействиям террасные доски. Концепция продукта быстро превратилась в перила, ограждение, отделку, автомобильные детали и другие области применения.Добавление дерева к пластику для изготовления WPC снижает стоимость формулы, повышает модуль упругости и снижает коэффициент теплового расширения. Однако эти преимущества имеют свою цену: экструзия древесного волокна в пластиковую матрицу технически сложна.
Древесина — не единственное натуральное волокно, используемое в пластмассовых композитах, но и самое распространенное. Древесина, используемая для изготовления WPC, перед экструзией измельчается, просеивается и сушится. Для профилей настилов и ограждений, где шероховатая текстура поверхности приемлема или даже желательна, просеивание древесного волокна размером от 40 до 60 меш дает хорошие характеристики текучести и легкость смешивания с пластиковой матрицей.
Для перил и других профилей, требующих гладкой отделки, древесина просеивается до 80–100 меш. Мелкие частицы, которые проходят через сито с размером ячеек 120 меш, нежелательны: они плохо растекаются и их трудно равномерно распределить в пластиковой матрице. Плохо распределенные древесные волокна, называемые «древесными пятнами», являются распространенной проблемой качества, когда древесина содержит слишком много мелких частиц или когда экструдер слишком изношен для достижения хорошего перемешивания.
Молотое древесное волокно уравновешивается при влажности от 8% до 12% по весу, в зависимости от влажности.Остаточная вода в экструдате, покидающем экструзионную головку, вызывает набухание профиля WPC, поэтому необходимо удалить практически всю воду из экструдата, прежде чем она покинет головку и подвергнется воздействию атмосферного давления.
Экструдерыимеют возможность удаления летучих веществ с использованием атмосферной и вакуумной вентиляции, но количество воды, которое может быть удалено из экструдата WPC, ограничено диффузией. Для экструдеров с противовращением самые высокие производственные показатели достигаются, когда древесное волокно сушат до содержания влаги 1% или ниже перед подачей в экструдер.Экструдеры с одновременным вращением обеспечивают лучшее обновление поверхности экструдата, чем экструдеры с противовращением, и могут выдерживать более высокую влажность древесины в сырье. Идеальное содержание влаги в древесине находится в диапазоне от 2% до 4% по весу. Снижение влажности древесины ниже 2% в сырье для экструдера, вращающегося в одном направлении, может фактически снизить максимальную производительность, поскольку выделение пара из экструдата оказывает благоприятный охлаждающий эффект.
Экструдеры с противовращением и совместным вращением могут обрабатывать древесное волокно при влажности выше 1% и 4% соответственно, но за счет производительности.Снижение производительности увеличивает максимальное время пребывания в экструдере, что увеличивает процент воды, которая может быть удалена из экструдата. Если количество воды в древесине, подаваемой в экструдер, вдвое превышает рекомендуемый уровень, например. 2% в экструдерах с противовращением и 8% в экструдерах с одновременным вращением — максимальная производительность экструдера будет примерно вдвое меньше.
ПрофилиWPC с избыточной влажностью на штампе образуют локальные пузырьки или «корь» под «кожей» профиля.Если уровень влажности достаточно высок, «кожа» почти полностью отделится от нижележащего профиля, поскольку вода испаряется и расширяется.
Древесина представляет собой сложную смесь, состоящую в основном из целлюлозы и лигнина. Это важно при производстве WPC, поскольку целлюлоза и лигнин термически разлагаются при температурах выше 190 C (374 F). На рисунке 1 показан термогравиметрический анализ (ТГА) древесного волокна, который представляет собой график зависимости процента оставшейся массы образца древесного волокна от температуры.
В анализе ТГА наблюдаются два значительных события потери массы: потеря воды при температуре от 25 ° C до 125 ° C, составляющая 6,02% от первоначального веса образца; и разложение целлюлозы и лигнина при температуре от 190 ° C до 400 ° C, что составляет 73,86% от веса образца.
На рис. 2 показаны диапазоны температур для сушки древесины, медленного разложения целлюлозы и лигнина и быстрого разложения целлюлозы и лигнина.
Сложность, которую это создает для производителя WPC, становится очевидной при рассмотрении стандартных температур экструзии для пластиков, обычно используемых в WPC, показанных в таблице на стр.34. Это диапазон типичных температур расплава на входе в экструзионную головку.
Значения в таблице почти полностью совпадают с температурным диапазоном, обозначенным «Медленное разложение» на рис. 2. Это означает, что производитель WPC создает профиль, в котором компонент с наибольшим массовым процентным содержанием в составе, вероятно, будет подвергается термическому разложению при входе в экструзионную головку. Предотвращение этого разложения — или, в лучшем случае, его адекватный контроль — представляет собой самую большую проблему при экструзии WPC.Распространенными проблемами качества ДПК, возникающими в результате термического разложения древесины, являются деформации экструдированного профиля, известные в промышленности как «скалывание», «набухание» и «гребни».
На рис. 3 показан термогравиметрический анализ образца древесноволокнистой плиты средней плотности (МДФ). Этот источник волокна был дешевым, многочисленным и непригодным для экструзии. Обратите внимание, что значительная потеря массы начинается при 150 ° C, вероятно, из-за разложения смолы или клея, используемых в процессе производства МДФ.
РОЛЬ СМОЛ
Новички в WPC, имеющие опыт работы с пластмассами, склонны думать, что «дерево есть дерево.«Новички в деревообрабатывающей промышленности склонны думать, что« пластик есть пластик ». На самом деле, свойства как волокна, так и пластика имеют решающее значение для успеха экструзии.
ПВХ, полиэтилен и полипропилен являются наиболее часто используемыми пластиками при экструзии WPC. ПВХ подходит для экструдеров с противовращением и низкой (<50 об / мин) скоростью вращения шнека, поскольку он разлагается под действием высокого сдвига или температур выше стандартной температуры обработки. Полиэтилен и полипропилен лучше подходят для экструдеров, вращающихся в одном направлении, поскольку эти полимеры могут выдерживать более высокие сдвиговые нагрузки и температуры, чем ПВХ.Это позволяет экструдерам, вращающимся в одном направлении, достигать производительности, превышающей 3000 фунтов / час (1365 кг / час) в машине диаметром 103 мм.
Поскольку WPC — это процесс экструзии с ограничением температуры, приблизительное практическое правило масштабирования — это квадрат диаметра экструдера. Например, учитывая известную производительность в 1600 фунтов / час на 73-мм экструдере, ожидаемая производительность 103-мм экструдера будет (103/73) 2 x 1600, или 3185 фунтов / час.
PE — это наиболее часто используемый пластик для WPC в США.S. HDPE используется в приложениях WPC, потому что он предлагает лучшие физические свойства, чем LD или LLDPE. HDPE с индексом текучести от 0,3 до 1 г / 10 мин, известный как марки с фракционной текучестью расплава, обычно используется для настила из ДПК. HDPE с фракционной текучестью расплава предлагает лучшие физические свойства, чем HDPE с более высокой текучестью, но существует предел того, насколько низкая текучесть расплава является практичной.
HDPE с очень низкими потоками расплава, скажем, менее 0,2 г / 10 мин, требуют более высокой удельной энергии для обработки в экструдере.Это приводит к более высоким температурам плавления. Поскольку древесина в WPC разлагается при температурах выше 190 C, для максимального увеличения производительности производитель WPC должен выбирать пластик с наивысшим индексом текучести расплава, который неизменно обеспечивает требуемые физические свойства в конечном продукте.
ИЗМЕНЕНИЯ В ПЛАСТИКОВЫХ СЫРЬЯХ
Пластмассы химически просты, но сложны в отношении длины цепи, конфигурации цепи, молекулярно-массового распределения, кристалличности и т. Д.Эти свойства редко измеряются на экструзионных заводах WPC, но они могут иметь огромное влияние на производство WPC.
Большая часть пластика, используемого в WPC, перерабатывается, а другая значительная часть — это первичный материал широкого или некондиционного качества. Поскольку свойства этих потоков жестко не контролируются, в процессе экструзии со временем могут быть значительные изменения. Это изменение может повлиять на максимальную производительность, выход и процент брака. Изменения в производительности процесса на ± 15% в течение нескольких дней не редкость.Эти изменения могут происходить с той же периодичностью, что и доставка пластика на завод по производству ДПК. Измерение показателя текучести расплава поступающего пластика дает неполное, но все же полезное указание на технологические характеристики пластмасс. Но даже это относительно простое измерение часто отсутствует на предприятиях WPC.
При производствеWPC смазочные материалы широко используются в качестве вспомогательного средства. Смазочные материалы в WPC выполняют две основные функции. Во-первых, это минимизация нагрева экструдата при сдвиге для ограничения температуры плавления, известная как «внутренняя смазка».Вторая функция состоит в том, чтобы преодолеть граничное условие отсутствия проскальзывания на поверхностях профильного штампа, чтобы профиль имел гладкую «кожу», известную как «внешняя» смазка. Уровни смазки в формулах WPC на основе полиэтилена обычно составляют от 3% до 5% по весу. Составы на основе полипропилена обычно содержат от 1% до 3% мас. Смазки.
На крупнейшем рынке WPC — наружных настилов — механические свойства WPC важны как для установщика, так и для конечного пользователя продукта. Сопротивление продукта изгибу под нагрузкой или модуль упругости определяет, сколько конструкции необходимо для поддержки поверхности настила и «ощущения» деки под ногами конечного пользователя.Устойчивость продукта к разрушению под нагрузкой или модуль разрыва — это вопрос безопасности конечного пользователя и долгосрочной удовлетворенности установкой палубы.
По сравнению с 100% древесиной, ДПК имеют более низкие модули упругости и прочности. Связующие агенты были разработаны для улучшения механических свойств WPC. Наиболее распространенными связующими агентами являются малеиновые ангидриды, привитые к основной цепи полиолефина. Они работают за счет улучшения адгезии пластиковой матрицы к поверхности древесного волокна.Преимущества связующих агентов должны быть сопоставлены с увеличением стоимости рецептуры, более высокой удельной энергией в экструдере и сниженной эффективностью внешней смазки в профильной головке.
Использование верхнего слоя на WPC повышает производительность продукта несколькими способами. ДПК на основе полиэтилена и полипропилена относительно мягкие и обладают плохой устойчивостью к царапинам. Древесное волокно в WPC подвержено воздействию плесени. Красители, антиоксиданты и средства защиты от УФ-излучения дороги, особенно когда они равномерно распределены по профилю WPC, когда нужно окрашивать и защищать только поверхность продукта.Верхний слой из более твердого пластика с концентрированным пакетом присадок смягчает все эти проблемы и значительно улучшает характеристики продукта из ДПК. Однако преимущества Capstocking компенсируются дополнительной сложностью и стоимостью процесса.
.