Состав портландцемента, его взаимодействие с водой, производство
Портландцемент часто называется просто цементом – это важнейшее минеральное вяжущее вещество. Порошкообразный материал, содержащий искусственные минералы, большинство которых в природе не встречаются или встречаются крайне редко. Эти минералы обладают высокой химической активностью и способны взаимодействовать с водой. Портландцементом называется гидравлическое вяжущее вещество, получаемое тонким измельчением портландцементного клинкера с гипсом и другими специальными добавками. Клинкер получают обжигом до спекания тонкодисперсной однородной сырьевой смеси, состоящей из известняка, глины, кремнезёма. Гипс вводится с целью регулирования, скорости схватывания и некоторых других свойств. Клинкерный порошок без гипса при смешивании с водой быстро схватывается и затвердевает в цементный камень с пониженными прочностными свойствами. Согласно ГОСТ 1581-96 в портландцемент разрешается вводить при помоле до 15 % активных минеральных добавок. При этом, название, цемента не меняется. Свойства портландцемента определяются, прежде всего, качеством клинкера.
Считается, что портландцемент был изобретен в Англии каменщиком Джозефом Аспдином, который получил патент в 1824 году на изготовление вяжущего вещества из смеси извести с глиной обжигом её до полного удаления углекислоты. Это вяжущее он назвал портландцементом. Однако в России, портландцемент был получен несколько ранее, в 1817 году начальником военно-рабочей команды Е. Г. Челиевым. В 1825 году им была: издана книга о получении вяжущего вещества, аналогичного по составу применяемому ныне портландцементу.
Историческая справка
Портландцементный клинкер и его химический состав
Портландцементный клинкер обычно получают в виде спёкшихся мелких и более крупных гранул и кусков размером до 10-20 или до 50-60 мм в зависимости: от типа печи. По микроструктуре клинкер, получаемый спеканием, представляет собой сложную тонкозернистую смесь кристаллических фаз и небольшого количества стекловидной фазы. Химический состав клинкера колеблется в широких пределах. Главными окислами цементного клинкера является окись кальция CaO, двуокись кремния SiО2, окись алюминия Аl2O3 и окись железа Fe2O3, суммарное содержание которых достигает обычно 95-97%. Кроме них имеются примеси окиси магния MgО, серный ангидрит SO3, двуокись титана ТiО2, окись хрома Cr2O3, окись марганца Мn2O3, щёлочи Na2O и K2O, фосфорный ангидрит P2O5 и др. Ориентировочно химический состав портландцемента выглядит следующим образом: CaO 63-66%; SiО2 21-24%; Аl2O3 4-8%; Fe2O3 2-4%; MgО 0,5-5%; SO3 0,3-1%; Na2O и K2O 0,4-1%; ТiО2 и Сг2O 0,2-0,5%; P2O5 0,1-0,3%.
Минералогический состав портландцементного клинкера
Образующийся в результате обжига сырьевой смеси клинкер, имеет достаточно сложный минералогический состав. Основную роль в нем играют четыре минерала.
Трёхкальциевый силикат Ca3SiO5 или 3CaO•SiO2 (C3S). Образующийся в портландцементном клинкере трёхкальциевый силикат содержит некоторое количество примесей MgO, Al2O3, Fe2O3, Cr2O3, которые влияют на его структуру и свойства. Эта разновидность называется алитом и обозначается С3S. Содержание алита в клинкере наибольшее и составляет 40-55%. При рассмотрении процессов гидратации цементов примесями, входящими в трёхкальциевый силикат, как правило, пренебрегают, и все расчёты ведутся на чистую систему 3CaO•SiO2. В портландцементе алит обеспечивает набор точности камня в ранние сроки твердения (от нескольких дней до 3-х месяцев). Трёхкальциевый силикат получают в лабораторных условиях из химически чистых компонентов. Кристаллы алита имеют обычно шестигранную или прямоугольную форму, которая хорошо просматривается в шлифах клинкера в отраженном свете.
Двухкальциевый силикат Ca2SiO4 или 2CaO•SiO2 (C2S). В портландцементном клинкере присутствует в бета — модификации, называемой белитом. Количество его в клинкере составляет 20 — 30%. Белит имеет меньшую гидравлическую активность, по сравнению с алитом и обеспечивает рост прочности цементного камня на поздних стадиях твердения. Белит, как и алит представляет собой твёрдый раствор бета — двухкальциевого силиката (бета — 2СаO•SiO2) и небольшого количества (1-3) таких примесей как Аl2O3, Fе2O3, Сr2О3 и др. Гидравлическая активность белита также зависит от строения кристаллов. Цементы, в которых белит представлен округлыми плотными кристаллами с зазубренными краями со средним размером 20-50 мкм характеризуются повышенной прочностью. Расщепление кристаллов способствует повышению её гидравлической активности. Промежуточное вещество, расположенное между кристаллами алита белита включает алюмоферритную и алюминатную фазу.
Алюминаты кальция обычно встречаются в клинкере в виде трёхкальциевого алюмината С3Аl2O6 или 3CaO•Al2O3 (С3А). С3А кристаллизуется в кубической системе в виде очень мелких шестиугольников и прямоугольников. Содержится в цементном клинкере в количестве до 15%. Это наиболее химически активный минерал клинкера и именно его гидратация определяет сроки схватывания цементных растворов. Его присутствие в больших количествах ускоряет схватывание и твердение портландцементного раствора при низких температурах. При повышенном содержании трехкальциевого алюмината ослабляется устойчивость цементного камня в средах, содержащих сульфаты и сероводород. Алюмоферритная фаза представляет собой твердый раствор алюмоферритов кальция разного состава, который в свою очередь зависит от состава сырьевых смесей, условий обжига и т.п. При этом возможно образование серии твердых растворов между С6А2F, С4АF, C6AF2 и С2F. В клинкере алюмоферритная фаза по своему составу близка к четырёхкальциевому алюмоферриту.
Четырёхкальциевый алюмоферрит Ca4•Al2O5•Fe2O5 или 4CaO•AI2O3•Fe2O3 (C4AF) (браунмиллерит) — железосодержащий минерал обладающий достаточно высокой скоростью гидратации и обеспечивающий рост прочности системы в первые часы твердения. В портландцементах его количество находится в пределах 10-20%. Скорости процессов гидратации — примерно равны.
Кроме указанных минералов в состав клинкера входит стекловидная фаза, содержащая в своем составе незакристаллизованные ферриты, алюминаты, оксид магния, щелочные соединения и др. При резком охлаждении цементного клинкера стеклофаза, покрывая поверхность минералов, предотвращает фазовые переход. Окись магния находится в клинкере в виде: а) минерала периклаза; б) твердого раствора в алюмоферитной фазе или в трехкальциевом силикате; в) в клинкерном стекле. Вредное влияние MgO при содержании более 5% на равномерность изменения объема цемента проявляется в том случае, когда она присутствует в виде кристаллов периклаза, медленно реагирующих с водой в уже затвердевшем цементе и дающих Mg(ОН)2 характеризующийся увеличенным, удельным объемом. Щелочи: натрий и калий присутствуют в клинкере в виде сульфатов, а также входят в алюминатную и алюмоферритную фазу.
Для регулирования сроков схватывания цемента при помоле клинкера вводится 3-5% двуводного гипса. Кроме этого портландцемент может содержать до 15% кремнезёмосодержаших компонентов, в качестве которых могут использоваться молотый песок, шлаки, золы от сжигания твёрдых топлив. Введением добавок достигается два преимущества: во-первых, цемент стоит дешевле т.к. портландцементный клинкер дороже любой добавки; во-вторых, добавками можно регулировать свойства раствора и камня. Для придания специальных качеств цементу при его помоле вводятся гидрофобизаторы, пластификаторы и другие вещества.
Твердение портландцемента
При смешении цемента с водой на начальных стадиях твердения в реакцию гидратации интенсивно вступают алюминаты и алюмоферриты кальция, благодаря более высокой константе скорости растворения по сравнению с алитом и белитом. Раствор становится пересыщенным по отношению к конечному продукту и из него на поверхности зёрен клинкера и в объёме раствора образуются иглообразные кристаллы гидроалюминатов и гидроферритов кальция различного состава. В общем, виде их состав можно обозначить xCaO•yAI2O3•mН2О и xСаО•yFe2O3•mН2O. Значения коэффициентов x, y, m изменяются в различных соотношениях и зависят, главным образом, от термодинамических условий процессов гидратации. Через некоторое время (3-6 часов) в системе накапливается достаточно много кристаллогидратов и образуются «стеснённые» условия, приводящие к образованию коагуляционной структуры, которая по мере накопления гидроалюминатов переходит в кристаллизационную. Через 6 — 10 часов весь объём между постепенно уменьшающимися зёрнами цемента заполняется скелетом иглообразных кристаллов — продуктов гидратации алюминатных составляющих клинкера. Эта структура иногда называется алюминатной. Цементный раствор, бывший до этого пластичным, начинает терять подвижность и набирать прочность.
В оставшемся объёме одновременно с алюминатной, но со значительно меньшей скоростью, возникают продукты гидратации силикатных клинкерных минералов алита и белита. Последние образуют чрезвычайно тонко пористый ворс из очень малых кристаллов, так называемую силикатную структуру. Влияние этой структуры на прочность твердеющего цементного камня со временем всё более увеличивается. Она уже является собственно носителем прочности цементного камня и приблизительно через 1 сутки начинает преобладать над алюминатной. К месячному сроку в цементном камне обнаруживается практически только силикатная структура. К этому времени процесс гидратации не заканчивается и в ряде случаев может продолжаться годами за счёт неиспользованного клинкерного фонда цемента.
Структура цементного камня
Для полной гидратации цементного зерна необходимо наличие 0,4 кратного количества воды от его массы. При этом только 60% её (т.е. 0,25 от массы цемента) связывается химически, остальные (40 % исходной воды) остаются в порах цементного геля в слабосвязанном состоянии. Размер, гелевых пор около 3•10-8 см. Они неизбежны и служат причиной тонкопористого строения гелевой массы. При химическом связывании вода претерпевает объёмную контракцию, которая составляет около 1/4 её первоначального объёма. Поэтому плотный объём геля (без пор) на такую же величину меньше суммы объёмов исходных компонентов цемента и воды. Этот процесс называют усадкой, а освобождавшийся в цементном камне объём — объёмом усадки. При твердении цементного камня в водной среде или при высокой влажности рассмотренный объём пор заполняется водой. Таким образом, при полной гидратации цемента получается гель, объём которого примерно на 30% состоит из пор.
Рассмотренный случай является идеальным и на практике практически никогда не встречается. Если количество воды будет меньше 0,4 от массы цемента, то её будет недостаточно для полной гидратации цементных зёрен, и в цементном камне останутся непрореагировавшие зёрна цемента. При избыточном количестве воды часть её не участвует в процессе гидратации и образует в камне капиллярные поры диаметром около 10-4 см, которые на несколько порядков больше гелевых пор. Примерно таких же размеров достигают и пустоты, возникающие в результате уже упомянутой усадки. Таким образом, водоцементное отношение (В/Ц) в значительной мере определяет структуру цементного камня и его физико-механические свойства. Суммарная пористость камня возрастает с увеличением В/Ц.
Производство портландцемента
Производство портландцемента может быть разделено на два комплекса операций. Первый из них включает изготовление клинкера, второй — получение портландцемента измельчением клинкера совместно с гипсом, активными минеральными и другими добавками. Получение клинкера — наиболее сложный и энергоёмкий процесс, заключающийся в добыче сырья, его смешении и обжиге. В настоящее время применяют два основных способа подготовки сырьевой смеси из исходных компонентов: «мокрый», при котором помол и смешение сырья осуществляется в водной среде, и «сухой», когда материалы измельчаются и смешивается в сухом виде. Каждый из этих способов имеет свои положительные и отрицательные стороны. В водной среде облегчается измельчение материалов, при их совместном помоле быстро достигается высокая однородность смеси, но расход топлива на обжиг в 1,5-2 раза больше чем при сухом. Сухой способ, несмотря на его технико-экономические преимущества по сравнению с мокрым, длительное время находил ограниченное применение из-за пониженного качества получаемого клинкера, однако, успехи в технике тонкого измельчения и гомогенизации сухих смесей обеспечили возможность получения высококачественных, портландцементов и по сухому способу. Применение находит и третий, так называемый, комбинированный способ. Сущность его заключается в том, что подготовка сырьевой смеси осуществляется по мокрому способу, затем шлам обезвоживается на специальных установках и направляется в печь.
Комбинированный способ по ряду данных почти на 20-30% снижает расход топлива по сравнению с мокрым, но при этом возрастает трудоёмкость производства и расход электроэнергии.
Обжиг сырьевой смеси осуществляется во вращающихся печах. Длина современных, вращающихся печей достигает 150-185 м и более, а диаметр 4-7 м. Скорость вращения печи составляет 0,5-1,2 об/мин. Шлам, проходя через печь и подвергаясь воздействию газов всё более высокой температуры, претерпевает ряд физических и физико-химических превращений. При температурах же 1300-1500 °С материал спекается, причём образуются клинкерные зерна размером до 15-20 мм и больше. Пройдя зону высоких температур, клинкер начинает охлаждаться потоками более холодного воздуха. Из печи он выходит с температурой 1000-1100 °С и направляется в колосниковый холодильник, где охлаждается до 30-50 °С. Охлаждённый клинкер поступает на склад. В процессе движения шлама по печи протекают следующие физико-химические процессы. В той части печи, где температура составляет 300-600 °С начинается энергичное испарение воды, которое сопровождается постепенным загустеванием шлама. Образуются крупные комья. Затем, три температуре 400-500 °С из материала выгорают органические пpимеси; начинается дегидратация каолинита, и других глинистых минералов с образованием, в частности; каолинитового ангидрида. Удаление из глины гидратной воды сопровождается потерей пластичности и связующих свойств, что приводит к распаду образовавшихся ранее комьев материала в подвижный порошок. Участок печи, где вода испаряется, и материал высыхает, называется зоной сушки. Следующая зона, где происходит дегидратация глины и идет дальнейшее нагревание до 700-800 °С, называется зоной подогрева. Эти две зоны занимают до 50 — 55% длины печи. При температурах 750-800 °С и выше в материале начинаются реакции в твердом состояний между его составляющими. Вначале они едва заметны, однако с повышением температуры материала до 1000 °С и более интенсивность их резко возрастает. Сначала в реакции вступают оксиды алюминия и железа. Они присоединяют к себе оксид кальция и образуются однокальциевый алюминат и однокальциевый феррит.
В чистом виде эти соединения не существуют, а образуют твёрдый раствор, растворяются друг в друге. Количество присоединённого оксида кальция увеличивается с ростом температуры. При 900-1000 °С резко усиливается разложение карбоната кальция с образованием окиси кальция в свободном виде и углекислого газа СО2. Этот участок печи называют зоной кальцинирования. В этой зоне вследствие того, что разложение СаСО3 идёт с поглощением тепла потребление последнего наибольшее. На участке печи, где температура материала достигает 1000-1100 °С и где основная масса СaСO3 уже превратилась в свободную окись кальция здесь резко возрастает интенсивность реакций в твёрдом состоянии. Раствор алюмината и феррита кальция связывает всё большее количество оксида кальция и уже образуются двухкальциевый алюминат и феррит кальция. Этот твёрдый раствор содержит равное количество оксида алюминия и оксида кальция. Этот раствор имеет состав 4CaO•AI2O3•Fe2O3.
В сырьевой смеси оксида алюминия содержится больше чем оксида железа, поэтому оставшийся алюминат кальция продолжает связывать оксид кальция с образованием трехкальциевого алюмината. Его образование заканчивается при температуре 1200 °С. Присоединение оксида кальция к оксиду кремния начинается при 600 °С, но достаточно быстро происходит при температуре 900-1100 °С. Реакции образования силикатов, алюминатов и ферритов кальция являются экзотермическими, что приводит к интенсивному повышению температуры материала на 150-200 °С на коротком участке печи в несколько метров. Этот участок печи получил название экзотермической зоны. К концу экзотермической зоны температура материала достигает, примерно, 1300 °С. При температуре 1250 °С заканчивается образование двухкальциевого силиката. Поскольку сырьевая смесь содержит больше оксида кальция чем это нужно для образования С2S, С4АF, С3А, то остальное количество СаО идёт на образование трехкальциевого силиката. При температуре 1300 °С начинается спекание материала вследствие образования в нём расплава в количестве 20-30% объёма начавшей спекаться массы.
В начальный момент спекания в расплав переходят С3А, С4АF, и СаО, в дальнейшем в нём начинает растворяться и двухкальциевый силикат C2S. При этом в жидкой фазе создаются благоприятные условия для образования основного минерала портландцемента — трехкальциевого силиката C3S из C2S и СаО. Это соединение плохо растворимо в расплаве, вследствие чего оно выделяется из него в виде мелких кристаллов, которые в последующем могут значительно увеличиваться в размерах. Выделение из расплава C3S сопровождается понижением в нём концентрации: C2S и окиси кальция, что приводит к переходу в расплав новых порций этих веществ, оставшихся в твёрдом состоянии в общей массе материала. Это в свою очередь обуславливает дальнейший ход процесса образования в расплаве и выделения из него С3S до почти полного связывания свободной окиси кальция с С2S. Трехкальциевый силикат выделяется из расплава вместе с небольшими количествами Al2O3 и MgO, образуя с ними твёрдый раствор, который называют алитом.
Участок печи, где проходит спекание материала, и образование алита называется зоной спекания. Здесь материалы нагревается примерно от 1300 до 1450 °С, что способствует более быстрому усвоению окиси кальция двухкальциевым силикатом и образованию алита. После зоны спекания обжигаемый материал переходит в зону охлаждения. До температуры примерно 1300 °С в нём ещё присутствует жидкая фаза и продолжается реакция усвоения окиси кальция и образования C3S. Затем жидкая фаза застывает и спекание заканчивается. Последний участок печи, где полученный клинкер охлаждается воздухом от 1300 °С до температуры при которой выходит из печи (1000-1100 °С) называется зоной охлаждения. Обычно при охлаждении клинкера с 1450 до 1300 °С и ниже жидкая фаза в нём застывает частично в виде стекла, частично при этом происходит кристаллизация из расплава С3A, C4AF, а также MgO. Степень закристаллизованности расплава зависит от скорости охлаждения материала после его выхода из зоны спекания.
Охлажденный клинкер в основном состоит из кристаллов минералов — силикатов (алита и белита) и промежуточного вещества, в которое входит стекло, минералы плавки (С4АF, C3A, С3А3), а также окись кальция и магния (в виде кристаллов).
55) Химико-минералогический состав портландцементного клинкера
Портландцемент – гидравлическое вяжущее, получаемое тонким измельчением портландцементного клинкера и небольшого количества гипса (1,5…3 %). Клинкер получают обжигом до спекания сырьевой смеси, обеспечивающей в портландцементе преобладание силикатов кальция. К клинкеру для замедления схватывания цемента добавляют гипс. Для улучшения некоторых свойств и снижения стоимости портландцемента допускается введение минеральных добавок.
Производство.
Основные операции при получении
портландцемента: приготовление сырьевой
смеси, обжиг ее до получения цементного
клинкера и помол его совместно с
добавками. Клинкер имеет следующий
химический состав(%): СаО – 62. ..68, SiO2 –
18…26, А12О3 – 4…9, Fе2О3 – 2…6. Чаще используют
известняк и глину в соотношении 3:1. В
сырьевую смесь вводят корректирующие
добавки и промышленные отходы,
обеспечивающие требуемый состав
клинкера.
Тщательно
подготовленную сырьевую смесь (рис.8.1.)
подают на обжиг во вращающуюся печь,
диаметром до 7 м и длиной до 185 м. Изнутри
печь выложена огнеупорным кирпичом.
Печь установлена под небольшим (3…4˚)
углом к горизонту и вращается (0,8…1,3
мин-1), благодаря этому сырьевая смесь
перемещается в ней от верхнего конца к
нижнему, куда подается топливо.
Максимальная температура обжига 1450°
С. При таких высоких температурах оксид
кальция СаО, образовавшийся в результате
разложения известняка, взаимодействует
с оксидами SiO2, А12О3 и Fе2О3, образующимися
при разложении глины. Продукты
взаимодействия, частично плавясь и
спекаясь друг с другом, образуют
портландцементный клинкер – плотные
твердые гранулы серого цвета. В состав
портландцементного клинкера входят
четыре основных минерала (табл.
Таблица 8.1. Минеральный состав портландцементного клинкера
Минерал | Формула | Количество, % |
Трехкальциевый силикат (алит), C3S Двухкальциевый силикат (белит), C2S Трехкальциевый алюминат, C3A Четырехкальциевый алюмоферрит, C4AF | 3CaO · SiO2 3CaO · SiO2 3CaO · AL2O3 4CaO · Al2O3 · Fe2O3 | 42…65 12…35 4…14 10…18 |
Примечание:
В скобках сокращенное обозначение
клинкерных минералов.
Портландцементный клинкер (на 60…80%) состоит из силикатов кальция, из-за чего портландцемент называют силикатным цементом.
Для получения портландцемента клинкер размалывают в трубных или шаровых мельницах с гипсом и другими добавками. Свойства портландцемента зависят от его минерального состава и тонкости помола клинкера. При взаимодействии с влагой воздуха активность портландцемента падает, поэтому его предохраняют от действия влаги. Портландцемент хранят в силосах, а транспортируют в специальных вагонах, автомобилях-цементовозах.
Клинкер.
Качество клинкера зависит от его
химического и минералогических составов.
Для производства портландцементного
клинкера применяют известняк и глину.
Известняк в основном состоит из двух
оксидов: СаО и СO2, а глина — из различных
минералов, содержащих в основном три
оксида: SiO2, Аl2О3 и Fe2O3. В процессе обжига
сырьевой смеси удаляется СO2, а оставшиеся
четыре оксида: СаО, SiO2, Аl2О3 и Fe2O3 —
образуют клинкерные минералы. Содержание
оксидов в цементе примерно следующее:
64.
Кроме указанных основных оксидов в портландцементном клинкере могут присутствовать MgO и щелочные оксиды К2О и Na2O, снижающие качество цемента. Оксид магния, обожженный при температуре около 1500°С, при взаимодействии с водой очень медленно гасится и вызывает появление трещин в уже затвердевшем растворе или бетоне, поэтому содержание оксида магния в портландцементе не должно быть более 5%. Наличие в цементе щелочных оксидов выше 1 % может вызвать разрушение отвердевшего бетона на таком цементе.
Указанные
выше основные оксиды находятся в клинкере
не в свободном виде, а образуют при
обжиге четыре основных минерала,
относительное содержание которых в
портландцементе следующее (%): трехкальциевый
силикат 3CaO•SiO2 (алит) — 45…60; двухкальциевый
силикат 2CaO•SiO2 (белит)— 20…35; трехкальциевый
алюминат 3СaO•Аl2O3 — 4…12; четырехкальциевый
алюмоферрит 4CaO•Al2O3•Fe2O3—10…18. Сокращенное
обозначение этих минералов следующее:
C3S, C2S, С3А и C4AF.
• Алит (C3S) — основной минерал клинкера, быстро твердеет и практически определяет скорость твердения и нарастания прочности портландцемента. Он представляет собой твердый раствор трехкальциевого силиката и небольшого количества (2…4%) MgO, Аl2O3, Р2О5, Cr2О3 и других примесей, которые могут существенно влиять на структуру и свойства портландцемента.
• Белит (β-C2S) — второй по важности и содержанию силикатный минерал клинкера, медленно твердеет и достигает высокой прочности при длительном твердении. Белит в клинкере представляет собой твердый раствор двухкальциевого силиката (β-C2S) и небольшого количества (1…3%) Аl2O3, Fe2O3, MgO, Сr2O3 и др. В связи с тем что белит при медленном охлаждении клинкера теряет вяжущие свойства, переходя из β-C2S в γ-C2S, это явление предотвращается быстрым охлаждением клинкера.
Содержание
минералов-силикатов в клинкере в сумме
составляет около 75%, поэтому гидратация
алита и белита в основном определяет
свойства портландцемента. Оставшиеся
25% объема клинкера между кристаллами
алита и белита заполнены кристаллами
С3А, C4AF, стекла и второстепенными
минералами.
• Трехкальциевый алюминат (С3А) при благоприятных условиях обжига образуется в виде кубических кристаллов. Он очень быстро гидратирует и твердеет. Продукты гидратации имеют пористую структуру и низкую прочность. Кроме того, С3А является причиной сульфатной коррозии цемента, поэтому его содержание в сульфатостойком цементе ограничено 5%.
• Четырехкальциевый алюмоферрит (C4AF) — алюмоферритная фаза промежуточного вещества клинкера, представляет собой твердый раствор алюмоферритов кальция разного состава, обычно ее состав близок к 4СаО•Аl2О3•Fe2О3. По скорости гидратации этот минерал занимает как бы промежуточное положение между алитом и белитом и не оказывает определяющего значения на скорость твердения и тепловыделение портландцемента.
Клинкерное стекло присутствует в промежуточном веществе в количестве 5… 15%, которое в основном состоит из СаО, Аl2О3, MgO, К2О и Na2O.
При
правильно рассчитанной и тщательно
подготовленной и обожженной сырьевой
смеси клинкер не должен содержать
свободного оксида кальция СаО, так как
пережженная при температуре около
1500°С известь, так же как и магнезия MgO,
очень медленно гасится, увеличиваясь
в объеме, что может привести к растрескиванию
уже затвердевшего бетона.
Portland Cement – Pavement Interactive
Цемент является основным ингредиентом цементной пасты – вяжущего вещества в портландцементном бетоне (PCC). Это гидравлический цемент, который при соединении с водой затвердевает в твердую массу. Вкрапленный в агрегатную матрицу, он образует ПКК. В качестве материала портландцемент используется уже более 175 лет, и с эмпирической точки зрения его поведение хорошо изучено. Однако с химической точки зрения портландцемент представляет собой сложное вещество, механизмы и взаимодействия которого еще предстоит полностью определить. ASTM C 125 и Ассоциация портландцемента (PCA) дают следующие точные определения:
- Гидравлический цемент: неорганический материал или смесь неорганических материалов, которые затвердевают и набирают прочность в результате химической реакции с водой путем образования гидратов и способны делать это под водой.
- Портландцемент: гидравлический цемент, состоящий в основном из гидравлических силикатов кальция.
Фон
Рисунок 1. Остров Портленд, Англия | Рисунок 2. Известняк в Портленд-Билль возле Уэймута |
Хотя использование цемента (как гидравлического, так и негидравлического) насчитывает много тысячелетий (по крайней мере, со времен Древнего Египта), первое появление «портландцемента» произошло в 19 веке. В 1824 году Джозеф Аспдин, каменщик из Лидса, получил патент на гидравлический цемент, который он назвал «портландским» цементом (Mindess and Young, 1981 [1] ). Он назвал цемент, потому что он производил бетон, напоминающий по цвету природный известняк, добываемый на острове Портленд, полуострове в Ла-Манше (см. рис. 1 и 2). С тех пор название «портландцемент» прижилось и пишется строчными буквами, потому что теперь оно признано торговым названием типа материала, а не конкретной ссылкой на Портленд, Англия.
Сегодня портландцемент является наиболее широко используемым строительным материалом в мире: ежегодно производится около 1,56 миллиарда тонн (1,72 миллиарда тонн). Ежегодное мировое производство бетона на портландцементе колеблется в пределах 3,8 миллиона кубических метров (5 миллиардов кубических ярдов) в год (Cement Association of Canada, 2002 [2] ). В США жесткие дорожные покрытия являются самым частым применением портландцемента и портландцементного бетона (ACPA, 2002 [3] ).
Производство
Несмотря на то, что существует несколько разновидностей портландцемента, производимого в промышленных масштабах, в каждом из них используются одни и те же основные сырьевые материалы и химические компоненты. Основными химическими компонентами портландцемента являются кальций, кремнезем, глинозем и железо. Кальций получают из известняка, мергеля или мела, а кремнезем, глинозем и железо — из песка, глины и источников железной руды. Другое сырье может включать сланцы, ракушки и побочные продукты производства, такие как прокатная окалина (Ash Grove Cement Company, 2000 9).0027 [4] ).
В основном производственном процессе эти материалы нагреваются в печи примерно до 1400–1600°C (2600–3000°F) — температурный диапазон, в котором два материала химически взаимодействуют с образованием силикатов кальция (Mindess and Young, 1981 [1 ] ). Это нагретое вещество, называемое «клинкером», обычно имеет форму небольших серо-черных гранул диаметром около 12,5 мм (0,5 дюйма). Затем клинкер охлаждают и измельчают в мелкий порошок, который почти полностью проходит через сито 0,075 мм (№ 200) и обогащается небольшим количеством гипса. В результате получается портландцемент. Ассоциация портландцементов (PCA) имеет прекрасную интерактивную иллюстрацию этого процесса на своем веб-сайте.
Химические свойства
Портландцементы можно охарактеризовать по их химическому составу, хотя они редко используются для дорожного покрытия. Однако именно химические свойства портландцемента определяют его физические свойства и то, как он затвердевает. Таким образом, базовое понимание химии портландцемента может помочь понять, как и почему он ведет себя так, как ведет себя. В этом разделе кратко описывается основной химический состав типичного портландцемента и то, как он гидратируется.
Базовый состав
В таблице 1 и на рисунке 3 показаны основные химические соединения портландцемента.
Таблица 1. Основные компоненты типичного портландцемента (Mindess and Young, 1981 [1] )
Химическое название | Химическая формула | Стенографическая запись | Массовые проценты |
---|---|---|---|
Трехкальциевый силикат | 3CaO×SiO 2 | С 3 С | 50 |
Двухкальциевый силикат | 2CaO×SiO 2 | С 2 С | 25 |
Трехкальциевый алюминат | 3CaO×Al2O 3 | С 3 А | 12 |
Тетракальциевый алюмоферрит | 4CaO×Al 2 O 3 ×Fe 2 O 3 | С 4 АФ | 8 |
Гипс | CaSO 4 ×H 2 O | ЧСХ 2 | 3,5 |
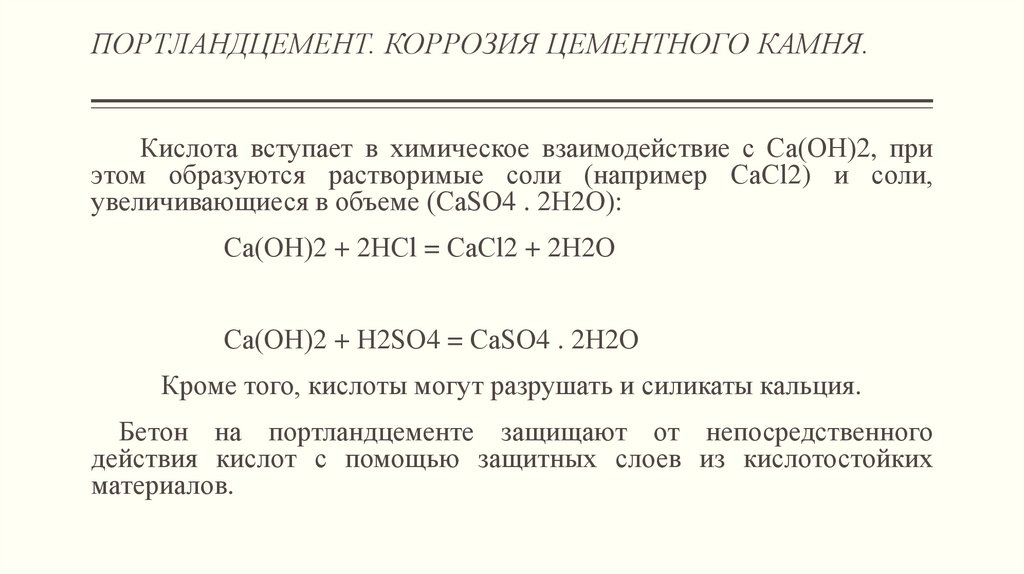
Гидратация
Когда портландцемент смешивается с водой, его химические соединения претерпевают ряд химических реакций, в результате которых он затвердевает (или схватывается). Все эти химические реакции включают добавление воды к основным химическим соединениям, перечисленным в таблице 1. Эта химическая реакция с водой называется «гидратацией». Каждая из этих реакций происходит в разное время и с разной скоростью. Вместе результаты этих реакций определяют, как портландцемент затвердевает и набирает прочность.
- Трехкальциевый силикат (C 3 S) . Быстро увлажняется и затвердевает и в значительной степени отвечает за начальное схватывание и раннюю прочность. Портландцементы с более высоким процентным содержанием C 3 S будут демонстрировать более высокую начальную прочность.
- Двухкальциевый силикат (C 2 S) .
Увлажняет и затвердевает медленно и в значительной степени отвечает за увеличение прочности в течение одной недели.
- Трехкальциевый алюминат (C 3 A) . Увлажняет и затвердевает быстрее всего. Выделяет большое количество тепла почти сразу и в некоторой степени способствует ранней прочности. Гипс добавляют в портландцемент для замедления С9.0079 3 А гидратация. Без гипса C 3 Гидратация привела бы к схватыванию портландцемента почти сразу после добавления воды.
- Алюмоферрит тетракальция (C 4 AF) . Быстро увлажняет, но очень мало способствует укреплению. Его использование позволяет снизить температуру печи при производстве портландцемента. Большинство цветовых эффектов портландцемента связано с C 4 AF.
На рис. 4 показаны скорости тепловыделения, которые дают приблизительное представление о времени гидратации и времени первоначального схватывания типичного портландцемента.
Типы портландцемента
Знание основных характеристик химических соединений, входящих в состав портландцемента, можно изменить его свойства, регулируя количество каждого соединения. В США AASHTO M 85 и ASTM C 150, Стандартные технические условия на портландцемент , различают восемь основных типов бетона на портландцементе (таблица 2). Есть также много других типов смешанных и патентованных цементов, которые здесь не упоминаются.
Таблица 2. Типы портландцемента ASTM
Тип | Имя | Назначение |
---|---|---|
я | Обычный | Цемент общего назначения, подходящий для большинства целей.![]() |
ИА | Нормальный воздухововлекающий | Воздухововлекающая модификация типа I. |
II | Средняя стойкость к сульфатам | Используется в качестве меры предосторожности против умеренного воздействия сульфатов. Обычно он выделяет меньше тепла и медленнее, чем цемент типа I. |
ИИС | Средняя стойкость к сульфатам — воздухововлекающие | Воздухововлекающая модификация Type II. |
III | Высокая ранняя прочность | Используется, когда требуется высокая начальная прочность. В нем больше C3S, чем в цементе типа I, и он имеет более тонкий помол, чтобы обеспечить более высокое отношение поверхности к объему, что ускоряет гидратацию. Прирост прочности в два раза выше, чем у цемента типа I за первые 24 часа. |
IIIА | Высокая ранняя прочность с воздухововлечением | Воздухововлекающая модификация Type III. |
IV | Низкая теплота гидратации | Используется, когда тепло гидратации необходимо свести к минимуму в приложениях большого объема, таких как гравитационные плотины.![]() |
В | Высокая стойкость к сульфатам | Используется в качестве меры предосторожности против сильного воздействия сульфатов – в основном там, где почва или грунтовые воды имеют высокое содержание сульфатов. Он набирает прочность медленнее, чем цемент типа I. Высокая устойчивость к сульфатам объясняется низким содержанием C3A. |
Физические свойства
Портландцементы обычно характеризуют по их физическим свойствам в целях контроля качества. Их физические свойства можно использовать для классификации и сравнения портландцемента. Задача при характеристике физических свойств состоит в том, чтобы разработать физические тесты, которые могут удовлетворительно охарактеризовать ключевые параметры. В этом разделе, в основном взятом из PCA (1988 [5] ), перечислены наиболее распространенные тестируемые физические свойства портландцемента в США. Значения спецификаций, если они указаны, взяты из ASTM C 150 9.0201, Стандартные технические условия на портландцемент .
Имейте в виду, что эти свойства, как правило, относятся к «чистым» цементным тестам, то есть они включают только портландцемент и воду. Чистые цементные пасты, как правило, трудно обрабатывать и тестировать, и поэтому они вносят большую изменчивость в результаты. Цементы также могут работать по-разному при использовании в «строительном растворе» (цемент + вода + песок). Со временем было обнаружено, что испытания строительных растворов обеспечивают более точное определение качества цемента, поэтому испытания неразбавленных цементных паст обычно используются только в исследовательских целях (Mindess and Young, 19).81 [1] ). Однако, если песок не будет тщательно указан в тесте раствора, результаты могут быть непереносимы.
- Тонкость
- Прочность
- Время установки
- Прочность
- Удельный вес
- Теплота гидратации
- Потери при зажигании
Сноски (↵ возвращается к тексту)
- Миндесс, С.
и Янг, Дж. Ф. (1981). Бетон . Prentice-Hall, Inc. Энглвуд Клиффс, Нью-Джерси. ↵
- Цементная ассоциация Канады. (2002). Веб-сайт. Доступ по адресу http://www.cement.ca/. Цементная ассоциация Канады. Оттава, Онтарио. По состоянию на 15 января 2002 г. ↵
- Американская ассоциация бетонных покрытий (ACPA). (2002). Веб-сайт. Доступ на http://www.pavement.com. По состоянию на 15 января 2002 г. ↵
- Ash Grove Cement Company. (2000). Веб-сайт. Доступ по адресу http://www.ashgrove.com/index.html. Цементная компания Эш Гроув. Оверленд-Гроув, Канзас. По состоянию на 15 января 2002 г. ↵
- Ассоциация портландцемента (PCA). (1988). Проектирование и контроль бетонных смесей . Ассоциация портландцемента. Skokie, IL.↵
Что такое портландцемент: виды, состав, применение
Качество используемого цемента определяет долговечность и прочность конструкции в долгосрочной перспективе. Таким образом, этот тип цемента широко считается выдающимся материалом для архитектурных сооружений. Основной причиной этого является его уникальный состав с высоким содержанием оксидов марганца и железа. Кроме того, известь является основным компонентом этого цемента, на долю которого приходится от 60 до 67 процентов состава. Кроме того, этот цемент обогащен кремнеземом, серой, железом и магнезией. Узнайте больше о его составе и различных типах:
Для чего используется портландцемент?
Портландцемент является одним из наиболее часто используемых цементов, применяемых в строительстве. Основной причиной его популярности является его способность мгновенно приобретать твердость. Он обычно используется при строительстве сооружений, где гидратация почвы является нормальной. Общая конструкция, построенная из портландцемента, — это тротуары, мосты, дамбы и здания. Кроме того, этот цемент также используется для заполнения трещин в стенах. Еще одной важной причиной использования этого цемента является его низкая стоимость и низкий уровень загрязнения воздуха.
В чем разница между портландцементом и обычным цементом?
Цемент является важной частью конструкции, поскольку он является связующей силой, скрепляющей конструкцию. Существует два типа цемента: портландцемент и обычный, но между ними есть существенные различия. Вот таблица, которая отличает его:
Портландцемент | Белый цемент |
---|---|
Состав портландцемента имеет высокий процент оксидов марганца и железа. | Состав белого цемента содержит меньше оксидов по сравнению с портландцементом. |
Портландцемент крупнозернистый. | Этот тип цемента имеет более мелкий состав. |
Энергопотребление этого цемента низкое. | Энергоемкость этого цемента сравнительно высока. |
Он используется, среди прочего, для изготовления штукатурных швов, сборных труб, водонепроницаемых полов и резервуаров для воды. | Белый цемент используется для эстетических целей (декорация, благоустройство дома, напольные покрытия) |
Состав/формула портландцемента
В состав портландцемента обычно входят четыре элемента: трехкальциевый алюминат (3CaO · Al2O3), трехкальциевый силикат (3CaO · SiO2), четырехкальциевый алюмоферрит (4CaO · Al2O3Fe2O3) и двухкальциевый силикат (2CaO · SiO2). Эта таблица состоит из процентного содержания химических соединений в портландцементе:
Химическое соединение | Процент |
---|---|
Известь (CaO) | от 60 до 67 процентов |
Триоксид серы (SO3) | 1–3% |
Силикагель (SiO2) | от 17 до 25 процентов |
Сода и/или калий (Na2O+K2O) | 0,5–1,3% |
Глинозем (Al2O3) | от 3 до 8 процентов |
Оксид железа (Fe2O3) | от 0,5 до 6 процентов |
Магнезия (MgO) | от 0,1 до 4 процентов |
Типы портландцемента
В настоящее время в строительной отрасли используется пять типов портландцемента. Каждый из них имеет свои свойства и области применения:
- Тип 1: Этот цемент обычно используется для общих целей. Портландцемент типа 1 широко используется при строительстве мостов, резервуаров, водопропускных труб, коллекторов, железнодорожных сооружений и резервуаров.Химический состав портландцемента: Состав портландцемента, его взаимодействие с водой, производство