Клинкер и его химический и минералогический состав
Портландцементный клинкер обычно получают в виде спекшихся мелких и более крупных гранул и кусков размером до 10—20 или до 50—60 мм в зависимости от типа печи.
По микроструктуре клинкер, получаемый спеканием, представляет собой сложную тонкозернистую смесь многих кристаллических фаз и небольшого количества стекловидной фазы.
Химический состав клинкера колеблется в сравнительно широких пределах. Главными окислами цементного клинкера являются окись кальция СаО, двуокись кремния Si02, окись алюминия А1203 и окись железа Fe203, суммарное содержание которых достигает обычно 95— 97%. Кроме них в состав клинкера в виде различных соединений в небольших количествах могут входить окись магния MgO, серный ангидрид S03, двуокись титана ТЮ2, окись хрома Сг203, окись марганца Мп203, щелочи Na20 и К20, фосфорный ангидрид P2Os и др.
Обычно содержание этих окислов в клинкере колеблется в следующих пределах (в %):
СаО 63—66 MgO 0,5—5
Si02 21—24 S03 0,3—1
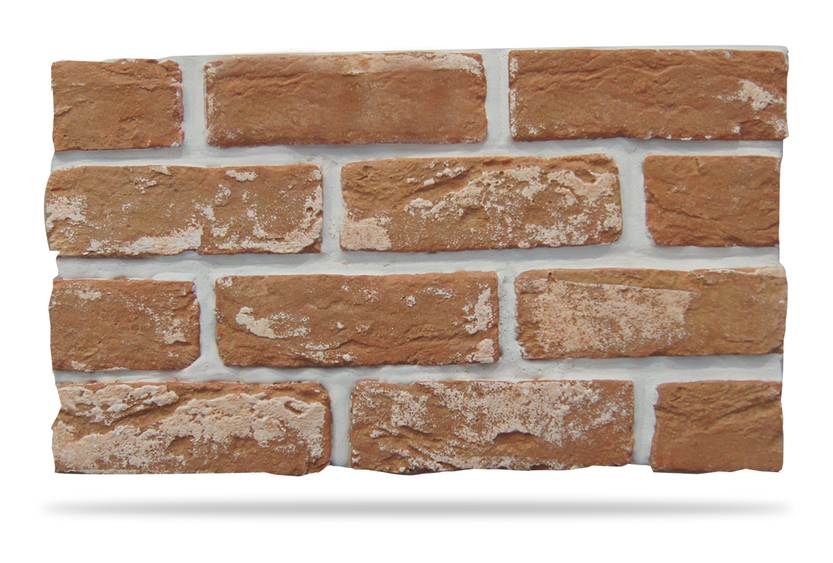
Fe203 2-4 Ti02+Cr203 . 0,2—0,5
P205 0,1—0,3
Химический анализ клинкера проводят по методике, регламентированной ГОСТ 5382—65. При этом определяют обычно общее процентное содержание окиси кальция, как связанной, так и находящейся в свободном состоянии; двуокиси кремния Si02; полуторных окислов Fe203 и А1203; окиси магния MgO; серного ангидрида S03; окислов щелочных металлов Na20 и K20; P2Os; Mn203; Ti02; Cr203, а также нерастворимого остатка и потерь при прокаливании.
Повышенное содержание окиси кальция (при условии обязательного связывания в химические соединения с кислотными окислами) обусловливает обычно повышенную скорость твердения портландцемента, его высокую конечную прочность, но несколько пониженную водостойкость.
Цементы с повышенным содержанием кремнезема в составе клинкерной части характеризуются пониженной скоростью твердения в начальные сроки при достаточно интенсивном нарастании прочности в длительные сроки; они отличаются повышенными водо- и сульфатостой-костью.

При повышенном количестве А1203, а следовательно, и алюминатов в составе цементов последние приобретают способность к ускоренному твердению в начальные сроки. Цемент при повышенном содержании глинозема характеризуется меньшими водостойкостью, сульфато-стойкостью и морозостойкостью.
Страниц: 1 2 3 4 5 6 7
Самое читаемое
Цементный клинкер
Цементный клинкер представляет собой продукт, который производят в процессе обжига до состояния плавления или спекания сырьевой смеси определенного состава. Клинкер является промежуточным продуктом в процессе производства цемента.
В специальных печах, при очень высокой температуре (выше 1000 градусов) нагревают смесь известняков и разных глин, в итоге получая спекшийся гранулированный материал. Химически это смесь алюмината и алюмоферрита кальция с силикатами. Для приготовления цемента клинкер измельчают, добавляют в него гипс и другие вещества.
Стоимость клинкера находится в достаточно широких пределах и напрямую зависит от сорта. Применяется в самых разных ремонтно-строительных работах.
Производство цемента
В процессе нагревания смеси, которую получают из известняка (до 75%), глины (до 25%) либо других похожих по составу и активности материалов, до температуры +1450С достигается состояние частичного плавления – таким образом образуются гранулы клинкера.
Чтобы в итоге получить цемент, клинкер смешивается с 2-5% гипса (точный объем зависит от содержания SO3 в самом клинкере и марки гипса), затем перемалывается в тончайшую пыль. Благодаря гипсу удается обеспечить быстрое схватывание материала. Хотя, в некоторых случаях его частично заменяют иными формами сульфата кальция. При помоле также допускается вводить другие добавки.
Виды цемента, который производят из клинкера:
- Портландцемент – после обжига известняков, глинистых примесей, мергелей получают раствор цемента.
Клинкер обычно смешивают с доменным шлаком, ракушечником и другими добавками. Портландцемент производят двумя способами: мокрым (когда компоненты смалывают и смешивают с водой, потом обжигают) и сухим (аналогичные действия, но без воды). Из портландцемента делают высокопрочные бетоны, облицовочные плитки, монолитные конструкции, даже искусственный мрамор и т.д.
- Романцемент – создается посредством обжига известняков (содержание глинистых минимум 25%) при температуре свыше +1000С. Применяют для производства блоков, стеновых панелей, бетонных смесей низких марок.
Стандартный клинкер предполагает такой состав:
- Трехкальциевый силикат (алит) – активный минерал, достаточно интенсивно набирает прочность и твердость с выделением тепла.
- Двухкальциевый силикат (белит) – медленно твердеет в первоначальной стадии.
- Трехкальциевый алюминат – обладает низким уровнем стойкости под воздействием серно-кислых соединений.
- Четырехкальциевый алюмоферрит – намного медленнее твердеет в сравнении с алитом, но все равно быстрее белита.
Прочность демонстрирует более низкую, чем у алита.
Четыре главные фазы клинкера
Цементный клинкер – это основной материал, который используется для производства цемента разных марок. То есть, проводится два действия: сначала производится клинкер в виде гранул, который получают путем нагревания глины и извести (с добавками) методом плавления, потом клинкер смалывается, в него добавляется гипс и получается цемент.
Разные способы обработки обуславливают то, что клинкер может быть с элементарным химическим или минералогическим составом. От того, какие объемы клинкерных материалов использовались при обжиге, зависят свойства цемента: он может быть быстросохнущим, созданным специально для использования при минусе, обладать другими свойствами.
Состав представляет собой систему нескольких клинкерных минералов, которые появляются в процессе плавки и обжига. Но заметить части отдельных составляющих клинкера невозможно, так как речь идет об аморфных и тонкозернистых кристаллических фазах.
Прежде, чем производить цемент, клинкер подбирают по составу. Обычно речь идет о четырех основных фазах, указанных ниже. Кроме них, в небольших объемах в веществе могут присутствовать другие фазы (оксид кальция, щелочные сульфаты).
Алит
Самая важная составляющая любого клинкера для цемента. В составе должно быть минимум 50-70% трехкальциевого силиката (обозначается 3СаO*SiО2 или сокращенно C3S). Структура и состав данной фазы модифицируются благодаря размещению в решетке инородных ионов (в особенности Аl3+, Mg2+, Fе3+). Алит стремительно реагирует с водой, в нормальных цементах имеет самое большое значение для обеспечения прочности. Особенно важен алит для обеспечения набора прочности цемента в течение 28 суток.
Белит
Когда производится клинкер цементный, содержание белита должно быть равно 15-30%. Двухкальциевый силикат обозначается как 2СаO*SiО2 (либо сокращенно C2S), модификация происходит за счет добавления в структуру инородных ионов, чаще всего большей частью либо полностью присутствует в формате β-модификации.
Белит с водой реагирует достаточно медленно, не оказывает воздействия на уровень прочности цемента на протяжении 28 суток. Но он влияет на прочность в значительно поздние сроки, что также немаловажно. Так, через год в идентичных условиях показатель прочности чистого белита и чистого алита примерно одинаков.
Алюминатная фаза
Алюминатная фаза в клинкере цементном составляет 5-10%. Трехкальциевый алюминат обозначается как 3СаO*Al2O3, меняется по составу и структуре в некоторых случаях благодаря инородным ионам (в особенности Nа+, Si4+, К+, Fe3+). Фаза мгновенно реагирует с водой, из-за чего становится причиной быстрого высыхания, если в состав не был введен контролирующий скорость схватывания реагент, в качестве которого выступает обычно гипс.
Алюмоферритная фаза
Ферритная фаза составляет около 5-15% цементного клинкера, обозначается как 4CaO*Al2O3*Fe2O3 (сокращенно CaAlFe). Четырехкальциевый алюмоферрит существенно меняет состав при изменениях пропорции Al/Fe и нахождении в структуре инородных ионов.
Скорость реакции базы с водой может быть разной из-за отличий в составе. Как правило, показатель достаточно высокий на первых этапах, в более поздние сроки средний между показателями алита и белита.
Состав портландцемента, его взаимодействие с водой, производство
Портландцемент часто называется просто цементом – это важнейшее минеральное вяжущее вещество. Порошкообразный материал, содержащий искусственные минералы, большинство которых в природе не встречаются или встречаются крайне редко. Эти минералы обладают высокой химической активностью и способны взаимодействовать с водой. Портландцементом называется гидравлическое вяжущее вещество, получаемое тонким измельчением портландцементного клинкера с гипсом и другими специальными добавками. Клинкер получают обжигом до спекания тонкодисперсной однородной сырьевой смеси, состоящей из известняка, глины, кремнезёма. Гипс вводится с целью регулирования, скорости схватывания и некоторых других свойств. Клинкерный порошок без гипса при смешивании с водой быстро схватывается и затвердевает в цементный камень с пониженными прочностными свойствами.
Считается, что портландцемент был изобретен в Англии каменщиком Джозефом Аспдином, который получил патент в 1824 году на изготовление вяжущего вещества из смеси извести с глиной обжигом её до полного удаления углекислоты. Это вяжущее он назвал портландцементом. Однако в России, портландцемент был получен несколько ранее, в 1817 году начальником военно-рабочей команды Е. Г. Челиевым. В 1825 году им была: издана книга о получении вяжущего вещества, аналогичного по составу применяемому ныне портландцементу.
Историческая справка
Портландцементный клинкер и его химический состав
Портландцементный клинкер обычно получают в виде спёкшихся мелких и более крупных гранул и кусков размером до 10-20 или до 50-60 мм в зависимости: от типа печи. По микроструктуре клинкер, получаемый спеканием, представляет собой сложную тонкозернистую смесь кристаллических фаз и небольшого количества стекловидной фазы. Химический состав клинкера колеблется в широких пределах. Главными окислами цементного клинкера является окись кальция CaO, двуокись кремния SiО
Минералогический состав портландцементного клинкера
Образующийся в результате обжига сырьевой смеси клинкер, имеет достаточно сложный минералогический состав. Основную роль в нем играют четыре минерала.
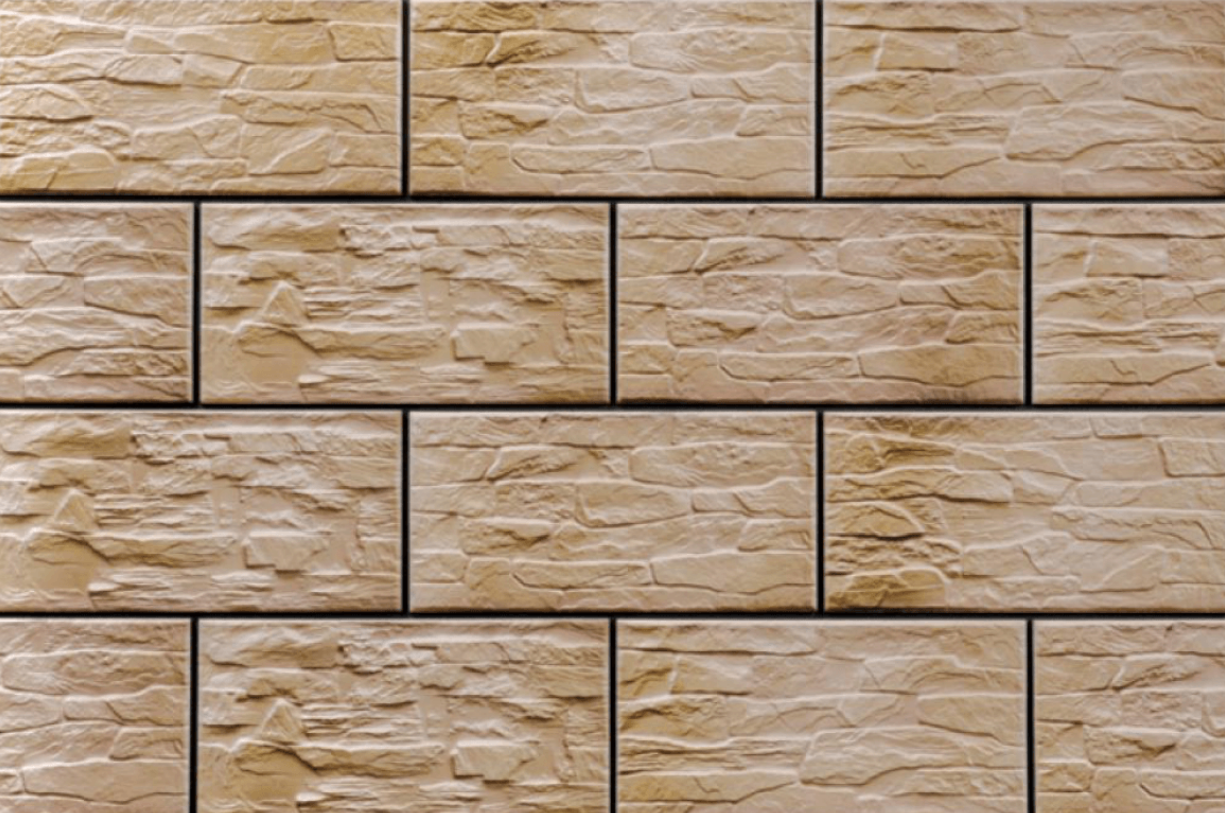
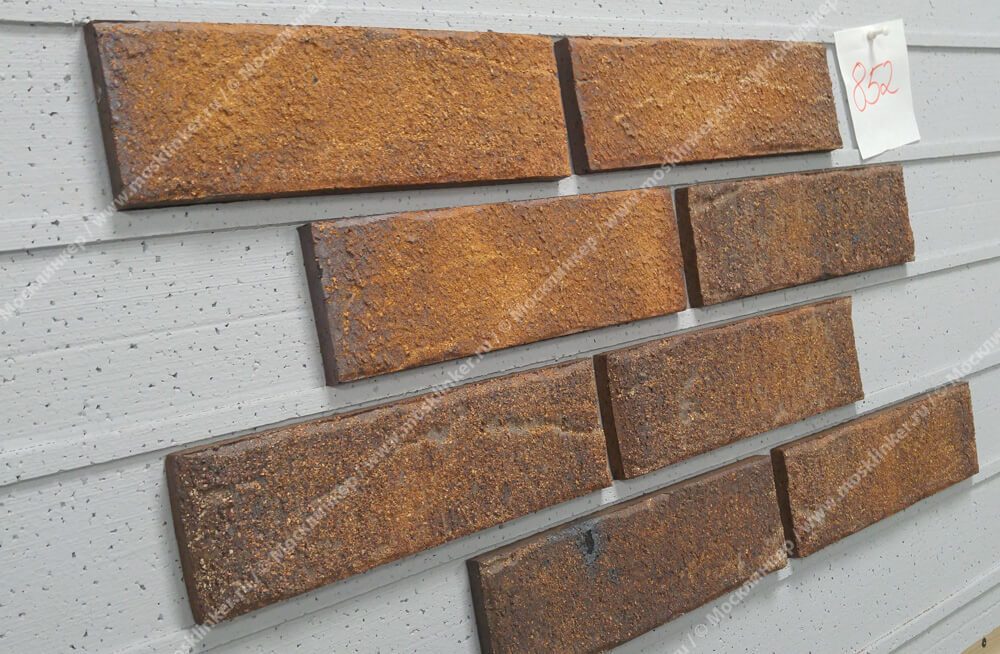
Алюминаты кальция обычно встречаются в клинкере в виде трёхкальциевого алюмината С3Аl2O6 или 3CaO•Al2O3 (С3А). С3А кристаллизуется в кубической системе в виде очень мелких шестиугольников и прямоугольников. Содержится в цементном клинкере в количестве до 15%. Это наиболее химически активный минерал клинкера и именно его гидратация определяет сроки схватывания цементных растворов. Его присутствие в больших количествах ускоряет схватывание и твердение портландцементного раствора при низких температурах. При повышенном содержании трехкальциевого алюмината ослабляется устойчивость цементного камня в средах, содержащих сульфаты и сероводород. Алюмоферритная фаза представляет собой твердый раствор алюмоферритов кальция разного состава, который в свою очередь зависит от состава сырьевых смесей, условий обжига и т.
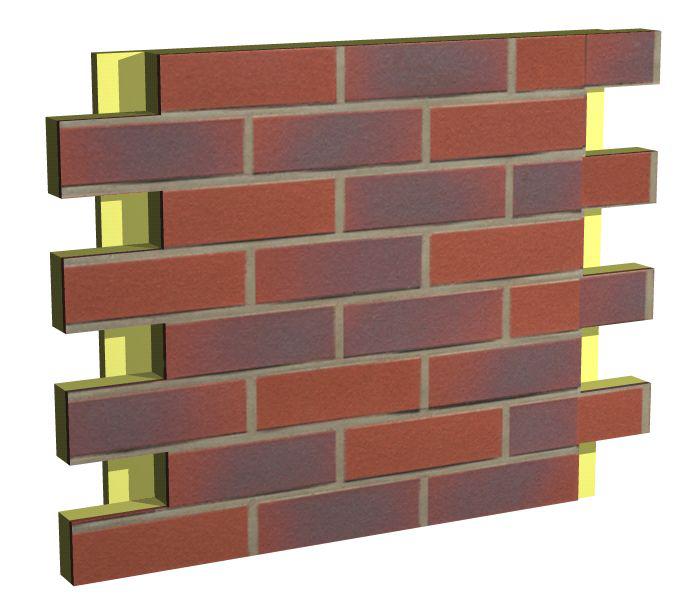
Четырёхкальциевый алюмоферрит Ca4•Al2O5•Fe2O5 или 4CaO•AI2O3•Fe2O3 (C4AF) (браунмиллерит) — железосодержащий минерал обладающий достаточно высокой скоростью гидратации и обеспечивающий рост прочности системы в первые часы твердения. В портландцементах его количество находится в пределах 10-20%. Скорости процессов гидратации — примерно равны.
Кроме указанных минералов в состав клинкера входит стекловидная фаза, содержащая в своем составе незакристаллизованные ферриты, алюминаты, оксид магния, щелочные соединения и др. При резком охлаждении цементного клинкера стеклофаза, покрывая поверхность минералов, предотвращает фазовые переход. Окись магния находится в клинкере в виде: а) минерала периклаза; б) твердого раствора в алюмоферитной фазе или в трехкальциевом силикате; в) в клинкерном стекле. Вредное влияние MgO при содержании более 5% на равномерность изменения объема цемента проявляется в том случае, когда она присутствует в виде кристаллов периклаза, медленно реагирующих с водой в уже затвердевшем цементе и дающих Mg(ОН)2 характеризующийся увеличенным, удельным объемом. Щелочи: натрий и калий присутствуют в клинкере в виде сульфатов, а также входят в алюминатную и алюмоферритную фазу.
Для регулирования сроков схватывания цемента при помоле клинкера вводится 3-5% двуводного гипса. Кроме этого портландцемент может содержать до 15% кремнезёмосодержаших компонентов, в качестве которых могут использоваться молотый песок, шлаки, золы от сжигания твёрдых топлив. Введением добавок достигается два преимущества: во-первых, цемент стоит дешевле т.к. портландцементный клинкер дороже любой добавки; во-вторых, добавками можно регулировать свойства раствора и камня. Для придания специальных качеств цементу при его помоле вводятся гидрофобизаторы, пластификаторы и другие вещества.
Твердение портландцемента
При смешении цемента с водой на начальных стадиях твердения в реакцию гидратации интенсивно вступают алюминаты и алюмоферриты кальция, благодаря более высокой константе скорости растворения по сравнению с алитом и белитом. Раствор становится пересыщенным по отношению к конечному продукту и из него на поверхности зёрен клинкера и в объёме раствора образуются иглообразные кристаллы гидроалюминатов и гидроферритов кальция различного состава. В общем, виде их состав можно обозначить xCaO•yAI2O3•mН2О и xСаО•yFe2O3•mН2O. Значения коэффициентов x, y, m изменяются в различных соотношениях и зависят, главным образом, от термодинамических условий процессов гидратации. Через некоторое время (3-6 часов) в системе накапливается достаточно много кристаллогидратов и образуются «стеснённые» условия, приводящие к образованию коагуляционной структуры, которая по мере накопления гидроалюминатов переходит в кристаллизационную. Через 6 — 10 часов весь объём между постепенно уменьшающимися зёрнами цемента заполняется скелетом иглообразных кристаллов — продуктов гидратации алюминатных составляющих клинкера. Эта структура иногда называется алюминатной. Цементный раствор, бывший до этого пластичным, начинает терять подвижность и набирать прочность.
В оставшемся объёме одновременно с алюминатной, но со значительно меньшей скоростью, возникают продукты гидратации силикатных клинкерных минералов алита и белита. Последние образуют чрезвычайно тонко пористый ворс из очень малых кристаллов, так называемую силикатную структуру. Влияние этой структуры на прочность твердеющего цементного камня со временем всё более увеличивается. Она уже является собственно носителем прочности цементного камня и приблизительно через 1 сутки начинает преобладать над алюминатной. К месячному сроку в цементном камне обнаруживается практически только силикатная структура. К этому времени процесс гидратации не заканчивается и в ряде случаев может продолжаться годами за счёт неиспользованного клинкерного фонда цемента.
Структура цементного камня
Для полной гидратации цементного зерна необходимо наличие 0,4 кратного количества воды от его массы. При этом только 60% её (т.е. 0,25 от массы цемента) связывается химически, остальные (40 % исходной воды) остаются в порах цементного геля в слабосвязанном состоянии. Размер, гелевых пор около 3•10-8 см. Они неизбежны и служат причиной тонкопористого строения гелевой массы. При химическом связывании вода претерпевает объёмную контракцию, которая составляет около 1/4 её первоначального объёма. Поэтому плотный объём геля (без пор) на такую же величину меньше суммы объёмов исходных компонентов цемента и воды. Этот процесс называют усадкой, а освобождавшийся в цементном камне объём — объёмом усадки. При твердении цементного камня в водной среде или при высокой влажности рассмотренный объём пор заполняется водой. Таким образом, при полной гидратации цемента получается гель, объём которого примерно на 30% состоит из пор.
Рассмотренный случай является идеальным и на практике практически никогда не встречается. Если количество воды будет меньше 0,4 от массы цемента, то её будет недостаточно для полной гидратации цементных зёрен, и в цементном камне останутся непрореагировавшие зёрна цемента. При избыточном количестве воды часть её не участвует в процессе гидратации и образует в камне капиллярные поры диаметром около 10-4 см, которые на несколько порядков больше гелевых пор. Примерно таких же размеров достигают и пустоты, возникающие в результате уже упомянутой усадки. Таким образом, водоцементное отношение (В/Ц) в значительной мере определяет структуру цементного камня и его физико-механические свойства. Суммарная пористость камня возрастает с увеличением В/Ц.
Производство портландцемента
Производство портландцемента может быть разделено на два комплекса операций. Первый из них включает изготовление клинкера, второй — получение портландцемента измельчением клинкера совместно с гипсом, активными минеральными и другими добавками. Получение клинкера — наиболее сложный и энергоёмкий процесс, заключающийся в добыче сырья, его смешении и обжиге. В настоящее время применяют два основных способа подготовки сырьевой смеси из исходных компонентов: «мокрый», при котором помол и смешение сырья осуществляется в водной среде, и «сухой», когда материалы измельчаются и смешивается в сухом виде. Каждый из этих способов имеет свои положительные и отрицательные стороны. В водной среде облегчается измельчение материалов, при их совместном помоле быстро достигается высокая однородность смеси, но расход топлива на обжиг в 1,5-2 раза больше чем при сухом. Сухой способ, несмотря на его технико-экономические преимущества по сравнению с мокрым, длительное время находил ограниченное применение из-за пониженного качества получаемого клинкера, однако, успехи в технике тонкого измельчения и гомогенизации сухих смесей обеспечили возможность получения высококачественных, портландцементов и по сухому способу. Применение находит и третий, так называемый, комбинированный способ. Сущность его заключается в том, что подготовка сырьевой смеси осуществляется по мокрому способу, затем шлам обезвоживается на специальных установках и направляется в печь.
Комбинированный способ по ряду данных почти на 20-30% снижает расход топлива по сравнению с мокрым, но при этом возрастает трудоёмкость производства и расход электроэнергии.
Обжиг сырьевой смеси осуществляется во вращающихся печах. Длина современных, вращающихся печей достигает 150-185 м и более, а диаметр 4-7 м. Скорость вращения печи составляет 0,5-1,2 об/мин. Шлам, проходя через печь и подвергаясь воздействию газов всё более высокой температуры, претерпевает ряд физических и физико-химических превращений. При температурах же 1300-1500 °С материал спекается, причём образуются клинкерные зерна размером до 15-20 мм и больше. Пройдя зону высоких температур, клинкер начинает охлаждаться потоками более холодного воздуха. Из печи он выходит с температурой 1000-1100 °С и направляется в колосниковый холодильник, где охлаждается до 30-50 °С. Охлаждённый клинкер поступает на склад. В процессе движения шлама по печи протекают следующие физико-химические процессы. В той части печи, где температура составляет 300-600 °С начинается энергичное испарение воды, которое сопровождается постепенным загустеванием шлама. Образуются крупные комья. Затем, три температуре 400-500 °С из материала выгорают органические пpимеси; начинается дегидратация каолинита, и других глинистых минералов с образованием, в частности; каолинитового ангидрида. Удаление из глины гидратной воды сопровождается потерей пластичности и связующих свойств, что приводит к распаду образовавшихся ранее комьев материала в подвижный порошок. Участок печи, где вода испаряется, и материал высыхает, называется зоной сушки. Следующая зона, где происходит дегидратация глины и идет дальнейшее нагревание до 700-800 °С, называется зоной подогрева. Эти две зоны занимают до 50 — 55% длины печи. При температурах 750-800 °С и выше в материале начинаются реакции в твердом состояний между его составляющими. Вначале они едва заметны, однако с повышением температуры материала до 1000 °С и более интенсивность их резко возрастает. Сначала в реакции вступают оксиды алюминия и железа. Они присоединяют к себе оксид кальция и образуются однокальциевый алюминат и однокальциевый феррит.
В чистом виде эти соединения не существуют, а образуют твёрдый раствор, растворяются друг в друге. Количество присоединённого оксида кальция увеличивается с ростом температуры. При 900-1000 °С резко усиливается разложение карбоната кальция с образованием окиси кальция в свободном виде и углекислого газа СО2. Этот участок печи называют зоной кальцинирования. В этой зоне вследствие того, что разложение СаСО3 идёт с поглощением тепла потребление последнего наибольшее. На участке печи, где температура материала достигает 1000-1100 °С и где основная масса СaСO3 уже превратилась в свободную окись кальция здесь резко возрастает интенсивность реакций в твёрдом состоянии. Раствор алюмината и феррита кальция связывает всё большее количество оксида кальция и уже образуются двухкальциевый алюминат и феррит кальция. Этот твёрдый раствор содержит равное количество оксида алюминия и оксида кальция. Этот раствор имеет состав 4CaO•AI2O3•Fe2O3.
В сырьевой смеси оксида алюминия содержится больше чем оксида железа, поэтому оставшийся алюминат кальция продолжает связывать оксид кальция с образованием трехкальциевого алюмината. Его образование заканчивается при температуре 1200 °С. Присоединение оксида кальция к оксиду кремния начинается при 600 °С, но достаточно быстро происходит при температуре 900-1100 °С. Реакции образования силикатов, алюминатов и ферритов кальция являются экзотермическими, что приводит к интенсивному повышению температуры материала на 150-200 °С на коротком участке печи в несколько метров. Этот участок печи получил название экзотермической зоны. К концу экзотермической зоны температура материала достигает, примерно, 1300 °С. При температуре 1250 °С заканчивается образование двухкальциевого силиката. Поскольку сырьевая смесь содержит больше оксида кальция чем это нужно для образования С2S, С4АF, С3А, то остальное количество СаО идёт на образование трехкальциевого силиката. При температуре 1300 °С начинается спекание материала вследствие образования в нём расплава в количестве 20-30% объёма начавшей спекаться массы.
В начальный момент спекания в расплав переходят С3А, С4АF, и СаО, в дальнейшем в нём начинает растворяться и двухкальциевый силикат C2S. При этом в жидкой фазе создаются благоприятные условия для образования основного минерала портландцемента — трехкальциевого силиката C3S из C2S и СаО. Это соединение плохо растворимо в расплаве, вследствие чего оно выделяется из него в виде мелких кристаллов, которые в последующем могут значительно увеличиваться в размерах. Выделение из расплава C3S сопровождается понижением в нём концентрации: C2S и окиси кальция, что приводит к переходу в расплав новых порций этих веществ, оставшихся в твёрдом состоянии в общей массе материала. Это в свою очередь обуславливает дальнейший ход процесса образования в расплаве и выделения из него С3S до почти полного связывания свободной окиси кальция с С2S. Трехкальциевый силикат выделяется из расплава вместе с небольшими количествами Al2O3 и MgO, образуя с ними твёрдый раствор, который называют алитом.
Участок печи, где проходит спекание материала, и образование алита называется зоной спекания. Здесь материалы нагревается примерно от 1300 до 1450 °С, что способствует более быстрому усвоению окиси кальция двухкальциевым силикатом и образованию алита. После зоны спекания обжигаемый материал переходит в зону охлаждения. До температуры примерно 1300 °С в нём ещё присутствует жидкая фаза и продолжается реакция усвоения окиси кальция и образования C3S. Затем жидкая фаза застывает и спекание заканчивается. Последний участок печи, где полученный клинкер охлаждается воздухом от 1300 °С до температуры при которой выходит из печи (1000-1100 °С) называется зоной охлаждения. Обычно при охлаждении клинкера с 1450 до 1300 °С и ниже жидкая фаза в нём застывает частично в виде стекла, частично при этом происходит кристаллизация из расплава С3A, C4AF, а также MgO. Степень закристаллизованности расплава зависит от скорости охлаждения материала после его выхода из зоны спекания.
Охлажденный клинкер в основном состоит из кристаллов минералов — силикатов (алита и белита) и промежуточного вещества, в которое входит стекло, минералы плавки (С4АF, C3A, С3А3), а также окись кальция и магния (в виде кристаллов).
Производство цемента и состав цементного клинкера
Состав цементного клинкера который получается от производства цементного камня по новой технологии. Способы схем процесса производства цемента из клинкера.
Производство цемента из клинкера
Романцемент — получают путем обжига известняков, содержащих глинистых не менее 25% при температуре 1000-1200 градусов по Цельсию. Применение: производство бетонов низких марок, стеновые панели, блоки.
Портландцемент — после обжига известняков, мергелей и глинистых примесей получают цементный клинкер. Клинкер смешивают с добавками (ракушечник, доменный шлак).
Способы производства портландцемента
1. Мокрый — компоненты измельчают и смешивают в присутствии воды, полученную суспензию (шлам) обжигают.
2. Сухой — все тоже самое, только в сухом состоянии.
Минералогический состав цементного клинкера
Трехкальциевый силикат (алит) является активным минералом. Быстро твердеет и набирает прочность, сопровождается значительным тепловыделением.
Двухкальциевый силикат (белит) в начальный период твердеет медленно.
Трехкальциевый алюминат — низкая стойкость против серно-кислых соединений.
Четырехкальциевый алюмоферрит твердеет медленнее алита, но быстрее белита. Прочность ниже алита.
Применение портландцемента
Приготовление растворов невысоких марок для кладочных и штукатурных работ, бетонные изделия.
Виды портландцемента
Глиноземистый — быстро твердеет. Получают путем обжига известняков и бокситов (богаты глиноземом). Процесс твердения сопровождается большим тепловыделением.
Свойства: сульфатостойкий, водонепроницаемый, жаростойкий, в 3-4 раза дороже портландцемента.
Применение: срочные ремонтные работы, аварийные работы, бетонные работы в зимних условиях, производство жаростойких бетонов.
Водонепроницаемый расширяющийся портландцемент получают путем тщательного измельчения глиноземистого цемента, гипса и гидроалюминатов кальция. При взаимодействии двух последних происходит образование гидросульфатоалюминатов кальция. Твердение сопровождается увеличением объема.
Применение: создание гидроизоляционных покрытий, заделка стыков и трещин железобетонных конструкций.
Быстротвердеющий портландцемент характеризуется быстрым нарастанием прочности.
Конечно, скорость твердения не сравнить с гипсом. Но самая быстрая из всех видов цемента.
Применение: возведение монолитных сооружений, приготовление высокопрочных бетонов.
Шлакопортландцемент жаро-, водо- и сульфатостойкий. Процесс твердения медленный.
Применение: изготовление железобетонных конструкций для работы в горячих цехах, гидротехнические сооружения.
Пуццолановый портландцемент твердеет медленно, требует систематического увлажнения.
Свойства: водостойкий, сульфатостойкий, не морозостойкий.
Применение: бетонные и ж/б конструкции.
Пластифицированный позволяет снизить водопотребление бетонных смесей и расход цемента на 5-8%.
Применение: дорожные бетоны, аэродромное и гидротехническое строительство.
Гидрофобный по своим свойствам похож на пластифицированный. Применение тоже.
Белый и цветной портландцемент
Белый изготавливают из сырья в котором мало окрашивающих оксидов (чистый известняк). Цветной — в которых много (охра, железный сурик).
Применение: облицовочные плитки, фактурный слой стеновых панелей, искусственный мрамор.
Сульфатостойкий портландцемент изготавливают из клинкера с другими примесями не более 7%.
Производство цемента
Цемент — это один из самых востребованных строительных материалов на рынке. Однако, производство готового цемента является затратным как по капитальным вложениям, так и по использованию энергии. Заводы по его производству обычно расположены вблизи мест добычи основного сырьевого компонента, каковым является известняк. Сам цемент используется в строительстве, как в чистом виде, так и в качестве основы для изготовления незаменимых материалов (бетона и железобетона).
Производство цемента начинается с добычи клинкера. Затем клинкер измельчают и получают вещество в виде порошка, в которое добавляют гипсовый компонент и другое. Расходы на добычу клинкера — большая доля затрат в себестоимости цемента. В итоге такая статья затрат, как добыча сырья, составляет долю в себестоимости готового продукта равную 70%.
Метод, с помощью которого осуществляют добычу и разработку залежей известняка называется «сносом». Используя этот метод, часть горной породы «сносят», освобождая путь к известняку желто-зеленого цвета. Глубина залегания известняка обычно составляет 10 м, толщина пласта равна 70 см. До принятой глубины породу желто-зеленого цвета можно встретить еще примерно четыре раза. На следующем этапе добытый известняк с помощью ленты для транспортировки отправляется на измельчение. Здесь известняковая порода должна приобрести размер кусков не более 10 см в диаметре. Измельченный до таких размеров известняковый компонент транспортируется на сушку и повторное перемалывание, где к нему добавляются другие составляющие. Затем известняковая смесь обжигается. Так происходит процесс получения клинкера.
Следующая стадия заключается в обработке клинкера. В первую очередь, клинкер дробят. Одновременно проходит процесс подсушки минеральных компонентов и дробление гипсового камня. Затем все компоненты смешивают и еще раз подвергают перемалыванию.
Поскольку сырье имеет порой разные технические и физические характеристики, то в промышленности существует три метода производства готового продукта. Так, при производстве цемента применяется три способа изготовления готовой смеси: мокрый, сухой и комбинированный.
Цементная смесь, произведенная мокрым способом, сделана на основе карбоната (мела), силикатов (глины) и добавок, содержащих железо. К последним относятся конвертерный шлам, огарки пирита и железистый продукт. При этом глина должна содержать влагу не более 20%, а мел не более 29%. Все компоненты смеси проходят измельчение в воде, в итоге получается суспензия, влажность которой составляет 30-50%. Суспензия, а вернее шлам, поступает в специальные печи, где проходит обжиг. Печь для обжига имеет весьма внушительные размеры: ее высота составляет 7 м, а длина — 200 м. В процессе обжига из шлама происходит выделение углекислот. На выходе из печи после обжига получается клинкер, который имеет вид шариков. Эти шарики измельчают и получают готовую цементную смесь.
При сухом способе производства происходит сушка всех сырьевых составляющих цемента, и только затем перемалывание. Таким образом, смесь имеет вид порошка.
При комбинированном способе осуществляется частичное использование двух предыдущих. Таким образом, комбинированный способ производства подразделяется на два вида. При первом из них смесь сырьевых компонентов готовят по мокрому способу, и только затем влажность смеси снижают с помощью специальных фильтров, она не должна превышать 16-18%. Потом эту массу отправляют на обжиг. При втором виде для получения смеси используется способ сухого получения первоначальной смеси, а затем в нее добавляют воду. Так получают гранулы, размер которых составляет не более 10-15 мм. Затем эти гранулы отправляют в печь для обжига.
Последнее обновление: 19 января 2021 в 15:50
Портландцементный клинкер
Библиотека строителя
Минералогический состав портландцементного клинкера.
- Химический состав портландцементного клинкера дан в таблице 1.5.1.
- Основные минералы, которые может содержать портландцементный клинкер, даны в табл. 1.5.2.
Портландцементный клинкер. Клинкерные минералы не являются чистыми соединениями, а представляют собой смеси, содержащие в незначительном количестве компоненты других минералов в виде смешанных кристаллических соединений; это относится и к остальным химическим примесям клинкера, которые не могут образовать самостоятельных фаз. Поэтому, чтобы четко отличать чистые соединения от клинкерных минералов, Териебом в 1897 г. дал основным минералам клинкера C3S и C2S названия «алит» и «белит» и, еще не зная их состава, исследовал под микроскопом отличия между ними.
Алит. Белит.
Алит.
- Алит.
- C3S является основным клинкерным минералом, определяющим прочность цемента. Из шести известных модификаций C3S в клинкере возникают только две высокотемпературные модификации, которые стабилизируются путем включения атомов примесей. Третья модификация — триклиниая — также изредка встречается.
Белит.
- Белит.
- Белит главным образом представляет собой β-форму C2S. При температуре спекания клинкера, превышающей 1420 С, образуется α-C2S, а при температуре до 1420 С — α’-C2S. Последняя форма во время охлаждения клинкера при температуре 670 С превращается в метастабилынй β-C2S.
Потери при прокаливании 0,5 — 3 | |||
SiO2 | 16-26 | CaO | 58-67 |
Al2O3 | 4-8 | MgO | 1-5 |
Fe2o3 | 2-5 | K2O+Na2O | 0-1 |
Mn2O3 | 0-3 | SO3 | 0,1-2,5 |
TiO2 | 0-0,5 | P2O5 | 0-1,5 |
При дальнейшем медленном охлаждении из β-C2S может образоваться стабильная ɣ-форма. Этот процесс протекает с увеличением объема на 10% и при определенных условиях может привести к рассыпанию клинкера. Быстрое охлаждение клинкера и наличие примесей препятствует переходу белита в гидравлически инертную ɣ-фазу, снижающую его качество.
Белит твердеет значительно медленнее алита, но в конце кондов достигает такой же прочности, как алит.
Если в клинкере глинозема содержится меньше, чем оксида железа (в молях), то оба компонента, вступая в соединение с известью, образуют алюмоферрит кальция (см, табл. 1.5.2.) —смешанно-кристаллическую фазу с конечным членом 2CaO•Fe2O3, где Fe может непрерывно замещаться Al. Этот смешанно-кристаллический ряд сохраняет стабильность до молярного отношения Al2O3:Fe2O3=2:1; однако в портланд-цементном клинкере, содержащем только соединения, богатые известью, ряд завершается уже при отношении 1:1. Если в клинкере преобладает глинозем, то его избыток сверх указанного отношения (как это имеет место в формуле 4CaO•Al2O3•Fe2O3) образует трехкальцисвый алюминат, богатый известью.
Трехкальциевый алюминат очень легко вступает в реакцию с водой, однако не имеет ясно выраженных гидравлических свойств и совместно с силикатами повышает начальную прочность цемента. Алюмоферрит кальция мало способствует гидравлическому твердению цемента.
Как уже указывалось щелочи только тогда попадают в клинкерные фазы, когда количество SO3, содержащееся в клинкере, недостаточно для полного образования щелочных сульфатов. Щелочи входят в состав всех клинкерных фаз, однако преимущественно содержатся в алюмииатной фазе в виде смешанных кристаллов, причем состав, указанный в формуле табл. 1.5.2, может быть получен только в присутствии SiO2.
Книга Вальтера Дуды «Цемент».
Цементный клинкер
В данной статье речь пойдет о таком материале как цементный клинкер. Данное вяжущее вещество получают методом обжига до спекания или плавления сырьевой смеси надлежащего состава и содержащий, в основном, высокоосновные силикаты и высоко — либо низкоосновные алюминаты кальция.
Характеристика клинкера
Цементный клинкер — это система из нескольких искусственных минералов, получаемых при обжиге сырьевой смеси.
Ниже приведена таблица примерного минералогического состава портландцементного клинкера:
1 | Трехкальциевого силиката (алита) | 3СаО х SiO2 | 40-65% |
2 | Двухкальциевого силиката (белита) | 2СаО х SiO2 | 15-45% |
3 | Трехкальциевого алюмината | 3СаО х Al2O3 | 4-12% |
4 | Четырехкальциевого алюмоферрита | 4СаО х Al2O3 х Fe2O3 | 12-25% |
Свойства клинкера
Свойства цементного клинкера зависят от химического состава исходного сырья и корректирующих технологических присадок и добавок, от способа обжига, охлаждения и помола. В роли разжижителей (при мокром способе) выступают многие вещества, а именно: жидкое стекло, сода, содовая вытяжка из торфа, сульфидно-спиртовая барда, торфощелочные вещества, триполифосфат и пр.
Для получения быстротвердеющего цемента, из которого преимущественно производят сборные железобетонные изделия и конструкции для того чтобы можно было сократить сроки их изготовления, используют цементный клинкер с высоким содержанием трехкальциевого силиката и трехкальциевого алюмината и в этом случае данные минералы составляют окло 65-70% от общего веса клинкера. Данный вид портландцемента с высоким содержанием трехкальциевого силиката и трехкальциевого алюмината, обладающий высокой экзотермией, с успехом твердеет при отрицательной температуре воздуха.
Ознакомьтесь также с гидравлической известью.
Клинкер и его свойства
Клинкер и его свойства
Клинкерная плитка считается одной из самых прочных, морозоустойчивых, износоустойчивых и экологичных материалов. Клинкер является проверенным продуктом не одним веком.
Характеристики и свойства клинкерной плитки
При изготовлении плитки не используют искусственные красители и пластификаторы. В основу берут высокопластичную сланцевую глину. После того как все материалы минералов будут очищены, их помещают в шнековое устройство для тщательного перемешивания. Затем полученную массу пропускают через экструдер, режут на формы и обжигают при температуре от 1200 °С.
Клинкер имеет приблизительный минеральный состав:
- Четырехкальциевый алюмоферрит составляет примерно 12-25%;
- Трехкальциевый силикат занимает около 40-65%;
- Трехкальциевого алюмината содержание составляет 4-12%;
- Двухкальциевый силикат содержится в пределах 15-45%.
У клинкера развита цветовая гамма, насчитывающая более 100 расцветок, которая достигается за счет натуральных компонентов. Клинкерная плитка имеет разнообразную поверхность: она бывает необработанной, шероховатой или глазурованной.
Водопоглощение. После изготовления плитка имеет минимальное водопоглощение за счет мелкопористой структуры.
Долговечность. Это свойство определяется показателем морозостойкости. Мелкопористая структура делает плитку устойчивой к морозам и она способна выдержать до 300 циклов замораживания и размораживания.
Плотность. Качество хорошего дорожного клинкера составит 2,10-2.32 кг/дм3, а стенового клинкера не меньше 1,9 кг/дм3.
Сопротивление испарению. Это является важным показателем для дорожного клинкера и оно составит 0,2-0,4 г/см2.
Сопротивление на удар. Оценка сопротивления учитывается по числу выдержанных ударов. Этот показатель важен для клинкера, который используется для дорожных покрытий.
Стойкость к химическому воздействию. Это свойство определяется кислотостойкостью более 97,5% и щелочестойкостью 75-80%.
Антипроскальзывющая стойкость. Это свойство важное для покрытий, которые используются для полов, ступеней, участков на которые попадает влага и масляные вещества.
Теплопроводность составит 0.9-1,2 Вт.
Плотная структура позволит выдержать даже механические повреждения. Клинкерная плитка не выгорает на солнце, так как устойчива к ультрафиолетовым лучам. На поверхности не выступают высолы, не образуются грибки и плесень.
Применение клинкерной плитки
В первую очередь клинкерная плитка используется при отделке фасадов. С ее помощью можно создать вид древнего дворца, старинный русский особняк либо готический замок. Фасад, сделанный из плитки, устойчив к выветриванию, испарению, воздействию кислотных дождей. Плитка не требует больших затрат для содержания. С ее поверхности легко смывается грязь и пыль во время дождя.
Продукт часто применяется в ландшафтном дизайне. С его помощью выкладывают внутренние дворики, дорожки, подъезды к гаражу, помещения садовых террас.
Особенности
Очень экономичен, ведь рассчитан на неоднократное использование. По желанию можно изменять узор на площадках. Для этого нужно вынуть плитку, очистить от раствора и уложить заново, создавая новый узор.
Клинкерная плитка является хорошим материалом для укладки площадки перед камином. Поверхность плитки не потрескается от жара и не испортится от неаккуратно разложенных дров.
Она используется для облицовки бассейнов, саун, ведь обладает практически нулевым свойством водопоглощения. Для безопасности всей семьи плитку используют для отделки лестниц. Только стоит выбирать изделия с рельефными полосами для сведения к нулю получение травм.
Что такое цементный клинкер? Состав, типы и применение
Клинкер представляет собой материал с шаровидным графитом, получаемый на стадии обжига во время производства цемента и используется в качестве связующего во многих цементных изделиях. Комки или узелки клинкера обычно имеют диаметр 3-25 мм и темно-серого цвета. Его получают путем нагревания известняка и глины до точки разжижения при температуре около 1400-1500 ° C во вращающейся печи. При добавлении клинкера к гипсу (для контроля схватывания цемента и обеспечения прочности на сжатие) и мелкого измельчения образуется цемент.Клинкер можно хранить в течение длительных периодов времени в сухом состоянии без ухудшения качества, поэтому он продается на международном уровне и используется производителями цемента, когда сырье оказывается дефицитным или недоступным.
Состав клинкера
Состав клинкера исследуется двумя отдельными подходами:
- минералогический анализ с использованием петрографической микроскопии и / или рентгеноструктурного анализа
- химический анализ, наиболее точно с помощью рентгенофлуоресцентной спектрометрии
Четыре основных компонента клинкера:
- Алит : приблизительно трехкальциевый силикат (обычно около 65% от общего количества)
- Белит : приблизительно двухкальциевый силикат (обычно около 15% от общего количества)
- Алюминат : приблизительно трикальцийалюминат (обычно около 7% от общего количества)
- Феррит : очень приблизительно тетракальциевый алюмоферрит (обычно около 8% от общего количества)
Другие вещества могут присутствовать в небольших количествах:
- Соль фазы — различные комбинации катионов натрия, калия и кальция с сульфатом и с хлорид-анионы, такие как:
- Арканит — K 2 SO 4
- Кальций Лангбейнит — K 2 Ca 2 (SO 4 ) 3
- Афтиталит — K 3 Na ( SO 4 ) 2
- Сильвит — KCl
- Низкотемпературные фазы — различные промежуточные химические соединения, не подвергшиеся дальнейшей термической обработке, такие как:
- Спуррит — Ca 5 (SiO 4 ) 2 (CO 3 )
- Тернезит — Ca5 (SiO 4 ) 2 (SO 4 )
- Эллестадит — Ca 10 (SiO 4 ) 3 (SO 4 ) 3 (OH) 2
- Йеэлимит — Ca 4 (AlO 2 ) 6 (SO 4 )
Химический анализ клинкера обычно приводится в следующая форма оксида (в мас. % оксида):
SiO2 | Al 2 O 3 | Fe 2 O 3 | CaO | MgO | K 2 O | Na 243 O 9012 | LOI | IR | Всего | |
21.5 | 5,2 | 2,8 | 66,6 | 1,0 | 0,6 | 0,2 | 1,0 | 1,5 | 0,5 | 98,9 |
Добавка свободной извести = 1,0% Ca2O 9 сульфатов щелочных металлов и незначительных примесей, таких как небольшие количества оксидов титана, марганца, фосфора и хрома.
Количество различных компонентов варьируется в зависимости от желаемых свойств производимого клинкера.
Термохимия клинкера
Сырье, вводимое в печь, отбирается при комнатной температуре. Внутри печи температура продолжает расти, и когда она достигает своего пика, клинкер производится путем быстрого охлаждения. Хотя стадии реакции часто перекрываются, их можно выразить в четко определенной последовательности следующим образом:
- 65-125 ° C : Свободная вода испаряется: необходимо подводить скрытое тепло. Чистая тепловая нагрузка: 2145 кДж / кг клинкера.
- 400-650 ° C : Глины разлагаются эндотермически, а щелочи реагируют с атмосферой печи с образованием жидких сульфатов.Чистая тепловая нагрузка: 42,2 кДж / кг клинкера.
- 500-650 ° C : Доломит разлагается эндотермически. Потребляемая полезная энергия: 19,7 кДж.
- 650-900 ° C : Карбонат кальция эндотермически реагирует с кремнеземом с образованием «зарождающегося белита». Полезное тепловложение: 722,5 кДж
- 700-900 ° C : Карбонат кальция эндотермически реагирует с оксидом алюминия и оксидом железа с образованием зарождающихся алюмината и феррита. Полезная тепловая нагрузка: 207,2 кДж.
- 900-1050 ° C : Когда все доступные диоксид кремния, оксид алюминия и оксид железа прореагируют, оставшийся карбонат кальция эндотермически разлагается до оксида кальция.
Требуемая теплопроводность: 601,9 кДж / кг клинкера.
- 1300-1425 ° C : Алюминат, феррит и часть белита плавятся эндотермически, а белит реагирует с оксидом кальция с образованием алита.
- 1425-1300 ° C : Пройдя пик температуры, расплав повторно экзотермически замораживается до алюмината, феррита и белита.
Типы клинкера
Самый распространенный вид клинкера производится для портландцемента и его смесей. Типы клинкера различаются в зависимости от типа цемента, для которого клинкер производится.Помимо портландцементных смесей, ниже перечислены некоторые специальные типы цементного клинкера:
- Сульфатостойкий клинкер
- Низкотемпературный клинкер
- Белый клинкер
- Низкощелочной клинкер
- Белит Кальцийсульфоалюминат Тернезит (BCT)
Стойкий клинкер
Он содержит 76% алита, 5% белита, 2% алюмината трикальция, 16% алюмоферрита тетракальция и 1% свободного оксида кальция. Его производство снизилось в последние годы, поскольку сульфатостойкость можно легко получить, используя гранулированный доменный шлак в производстве цемента.
Низкотемпературный клинкер
Он содержит 29% алита, 54% белита, 2% алюмината трикальция и 15% алюмоферрита тетракальция с очень небольшим количеством свободной извести. Его больше не производят, потому что цемент, произведенный из обычного клинкера и измельченного гранулированного доменного шлака, имеет отличные низкотемпературные свойства.
Белый клинкер
Он содержит 76% алита, 15% белита, 7% трикальцийалюмината, отсутствие тетракальциевого алюмоферрита и 2% свободной извести, но состав может широко варьироваться.Из белого клинкера получается белый цемент, который используется в строительстве в эстетических целях. Большая часть белого цемента идет на заводской сборный бетон.
Клинкер с низким содержанием щелочи
Уменьшение содержания щелочи в клинкере осуществляется либо заменой исходного сырья глинозема другим компонентом (таким образом, получая более дорогой материал из более удаленного источника), либо установкой «щелочного отвода», который включает удаление некоторых высокотемпературных газов из системы печи (которые содержат щелочи в виде дыма), что приводит к некоторым потерям тепла.
Белит Тернезит сульфоалюмината кальция (BCT)
Эта концепция используется для производства клинкера с сокращением выбросов углекислого газа до 30%. Повышается энергоэффективность, а затраты на электроэнергию для производственного процесса также снижаются примерно на 15%.
Использование клинкера: преобразование в цемент
Клинкер, смешанный с добавками и измельченный в мелкий порошок, используется в качестве связующего в цементных изделиях. Для достижения определенных свойств производимого цемента добавляются различные вещества.Гипс, добавленный и измельченный с клинкером, регулирует время схватывания и придает самое важное свойство цемента — прочность на сжатие. Это также предотвращает агломерацию и покрытие порошка на поверхности шаров и стенок мельницы. Некоторые органические вещества, такие как триэтаноламин (используется в количестве 0,1 мас.%), Добавляются в качестве вспомогательных средств измельчения, чтобы избежать агломерации порошка. Иногда используются и другие добавки: этиленгликоль, олеиновая кислота и додецилбензолсульфонат. Наиболее известным типом производимого цемента является портландцемент, но некоторые активные ингредиенты и химические добавки могут быть добавлены в клинкер для производства других типов цемента, таких как:
- измельченный гранулированный доменный шлак цемент
- пуццолановый цемент
- микрокремнезем цемент
Клинкер в основном используется для производства цемента.Поскольку он может храниться в сухом состоянии в течение нескольких месяцев без заметного ухудшения, он продается на международном уровне в больших количествах. Производители цемента покупают клинкер для своих цементных заводов в регионах, где сырье для цемента ограничено или недоступно.
Качество клинкера зависит от состава сырья.
* Выберите страну / regionUnited StatesCanadaAfghanistanAlbaniaAlgeriaAmerican SamoaAndorraAngolaAnguillaAntarcticaAntigua и BarbudaArgentinaArmeniaArubaAustraliaAustriaAzerbaijanBahamasBahrainBangladeshBarbadosBelarusBelgiumBelizeBeninBermudaBhutanBoliviaBosnia и HerzegovinaBotswanaBouvet IslandBrazilBritish Индийский океан TerritoryBrunei DarussalamBulgariaBurkina FasoBurundiCambodiaCameroonCape VerdeCayman IslandsCentral африканских RepublicChadChileChinaChristmas IslandCocos (Килинг) IslandsColombiaComorosCongoCongo, Демократическая Республика ofCook IslandsCosta RicaCote D’IvoireCroatiaCubaCyprusCzech RepublicDenmarkDjiboutiDominicaDominican RepublicEast TimorEcuadorEgyptEl SalvadorEquatorial GuineaEritreaEstoniaEthiopiaFalkland (Мальвинские) острова Фарерские IslandsFijiFinlandFmr Югославская Республика МакедонияФранцияФранцузская ГвианаФранцузская ПолинезияФранцузские Южные ТерриторииГабонГамбияГрузияГерманияГанаГибралтарГрецияГренландияГренадаГваделупаГуамГватемалаГвинеяГвинея-БисауГайанаГаити Херд и Макдональд IslandsHoly Престол (Ватикан) HondurasHong KongHungaryIcelandIndiaIndonesiaIran (Исламская Республика) IraqIrelandIsraelItalyJamaicaJapanJordanKazakstanKenyaKiribatiKorea, Корейские Народно-Демократической RepKorea, Республика ofKuwaitKyrgyzstanLao Народный Демократической RepLatviaLebanonLesothoLiberiaLibyan Arab JamahiriyaLiechtensteinLithuaniaLuxembourgMacauMadagascarMalawiMalaysiaMaldivesMaliMaltaMarshall IslandsMartiniqueMauritaniaMauritiusMayotteMexicoMicronesia, Федеративные StatesMoldova, Республика ofMonacoMongoliaMontserratMoroccoMozambiqueMyanmarNamibiaNauruNepalNetherlandsNetherlands AntillesNew CaledoniaNew ZealandNicaraguaNigerNigeriaNiueNorfolk IslandNorthern Mariana IslandsNorwayOmanPakistanPalauPanamaPapua Нового GuineaParaguayPeruPhilippinesPitcairnPolandPortugalPuerto RicoQatarReunionRomaniaRussian FederationRwandaSaint HelenaSaint Киттс и НевисСент-ЛюсияСент-Пьер и МикелонСамоаСан-МариноСао-Томе и ПринсипиСаудовская АравияСенегалСейшельские островаСьерра-ЛеонеСингапурСловацкий iaSloveniaSolomon IslandsSomaliaSouth AfricaSpainSri LankaSth Georgia & Sth Sandwich Институт социальных Винсент и GrenadinesSudanSurinameSvalbard и Ян MayenSwazilandSwedenSwitzerlandSyrian Arab RepublicTaiwan, провинция ChinaTajikistanTanzania, Объединенная Республика ofThailandTogoTokelauTongaTrinidad и TobagoTunisiaTurkeyTurkmenistanTurks и Кайкос IslandsTuvaluUgandaUkraineUnited арабских EmiratesUnited KingdomUruguayUS Minor Отдаленные IslandsUzbekistanVanuatuVenezuelaVietnamVirgin острова (Британские) Виргинские острова (U. S.) Острова Уоллис и Футуна Западная Сахара Йемен Югославия Замбия Зимбабве
Влияние и контроль химического состава клинкера для производства цемента
Сануси Нуху 1, 2 , Самила Ладан 3 , Абубакар Умар Мухаммад 4
1 Департамент химического машиностроения, Политехнический институт Умару Али Шинкафи Сокото, Нигерия
2 Студент, факультет химической инженерии, Университет Ахмаду Белло Зария, Нигерия
3 Департамент мониторинга и оценки, Целевой фонд высшего образования, Нигерия
4 Факультет чистых и прикладных наук, Университет Усмана Данфодийо Сокото, Нигерия
Для корреспонденции: Сануси Нуху, Департамент химического машиностроения, Политехнический институт Умару Али Шинкафи, Сокото, Нигерия.
Эл. Почта: |
© 2020 Автор (ы). Опубликовано Scientific & Academic Publishing.
Эта работа находится под лицензией Creative Commons Attribution International License (CC BY).
http://creativecommons.org/licenses/by/4.0/
Аннотация
В этом исследовании основное внимание уделялось изучению эффектов и способов контроля химического состава клинкера для лучшего производства цемента.Цемент — это вещество, получаемое путем измельчения смеси глины и известняка и нагревания до температуры 1450 ° C, при которой химическое превращение происходит внутри печи с образованием нового соединения, называемого клинкером. Методология данной исследовательской работы: 10 образцов клинкера собирали на пластинчатом конвейере, 10 г каждого образца взвешивали, измельчали и гранулировали с помощью пиридина и связующего агента. Затем образец был подвергнут рентгеновскому анализатору для определения минералогического состава клинкера, обнаруженных минералов и оксидов; C 3 S, C 2 S, C 3 A и C 4 AF и CaO, SiO 2 , Al 2 O 3 и Fe 2 O 3 .Другие модули упругости цемента, такие как LSF, AM и SM, были рассчитаны с использованием уравнения Bogues. Из результатов на рис.8 показано увеличение начальной прочности цемента в результате увеличения AM, на рис.10 показано снижение начальной прочности цемента в результате увеличения SM, на рис.9 также представлена диаграмма LSF и свободной известь (FCaO), и результат показывает, как количество свободной извести увеличивается по мере увеличения LSF, что приводит к увеличению потребления энергии для образования клинкера, клинкера низкого качества, объемного расширения и низкой прочности цемента.Поэтому химический состав цементного сырья и клинкера имеет решающее значение для эффективности цементного завода и энергопотребления. Чтобы обеспечить постоянный и стабильный химический состав и качество цементного клинкера с минимально возможным потреблением энергии, необходимо уделять внимание питанию для печи и химическому составу клинкера.
Ключевые слова: Химический, Цемент, Клинкер, Состав, Печь, Потребление
Процитируйте этот документ: Сануси Нуху, Самила Ладан, Абубакар Умар Мухаммад, Влияние и контроль химического состава клинкера для производства цемента, Международный журнал науки и техники управления , Vol.10 No. 1, 2020, pp. 16-21. DOI: 10.5923 / j.control.20201001.03.
1. Введение
- Влияние и контроль химического состава клинкера является важным элементом процесса производства цемента. При производстве цемента необходимо анализировать, контролировать и эффективно контролировать влияние химического состава клинкера на технологические материалы и готовую продукцию, чтобы оптимизировать процесс и обеспечить постоянное желаемое качество цемента. Цементное вещество получают путем измельчения смеси глины и известняка и нагревания до температуры 1450 ° C. Химическое превращение происходит внутри печи с образованием нового соединения, называемого клинкером. Клинкер образуется в результате обжига на ступени печи, его можно описать как комки или конкреции, обычно диаметром от 3 до 25 мм. CaO, SiO 2 , Al 2 O 3 и Fe 2 O 3 являются основным компонентом цементного клинкера, на их долю приходится более 95% и MgO, TiO 2 , P 2 O 5 и щелочи являются второстепенными компонентами в исходном количестве менее 3%, они не присутствуют в отдельном оксиде, но существуют в виде соединения, образованного двумя или более оксидами (Mohammd A.Aldies, et al 2010). C 3 S, C 2 S, C 3 A и C 4 AF являются минералами состава клинкера, и эти минералы являются результатом пирообработки или реакции оксидов в печи, которая приводит к к образованию коэффициента насыщения известью (LSF). LSF — это отношение CaO к SiO 2 , Al 2 O 3 и Fe 2 O 3 . Клинкер с LSF, близким к 1,0 или выше, указывает на вероятность присутствия свободной извести, это приводит к сильному горению клинкера и, следовательно, затрудняет измельчение (Nuhu.S и др., 2019). Однако LSF также контролирует долю C 3 S в C 2 S в клинкере, высокое значение LSF приводит к тому, что свободная известь (CaO) не соединяется с этими оксидами, остается в виде свободной извести, а избыток свободной извести приводит к нежелательным эффектам, таким как поскольку увеличивает время схватывания, затрудняет измельчение клинкера, объемное расширение и снижает прочность цемента (CCNN-Sokoto, 2013). Таким образом, рисунок 9 ниже подтверждает, что химический состав цементного клинкера имеет решающее значение для энергопотребления, поскольку измельчение цементного клинкера зависит от LSF и композиций свободной извести, любое отклонение скольжения от этого состава может значительно повлиять на производительность установки, т. Е. включая потребление энергии и качество цемента.Эта исследовательская работа была сосредоточена на изучении роли эффектов и способов контроля химического состава клинкера для лучшего производства качественного цемента с минимально возможным потреблением энергии. Исследование проводилось на основе анализа химического состава клинкера, полученного на Сокотском цементном заводе.
1.1. Химический состав сырого корма
- Для достижения необходимого химического состава клинкера во время спекания должен быть установлен химический состав сырого корма. Различные химические параметры могут использоваться для контроля в зависимости от количества сырья, используемого для приготовления корма.Обычно количество целевых параметров, которые можно контролировать, на единицу меньше количества сырья. Однако также для контроля сырьевой смеси с использованием карбоната кальция требуются два вида сырья — камень высокого и низкого качества, если необходимо также контролировать содержание железа, то необходимо добавить третье сырье, содержащее оксид железа, для надлежащей регулировки (CCNN — Sokoto, 2009). . Обычно в качестве исходного сырья на заводе используется доступное сырье и важные параметры клинкера. Обычные комбинации целевых параметров исходного сырья могут быть основаны на: § Химический состав — CaCO 3 , SiO 2 и Fe 2 O 3 § Расчетная минералогия C 3 S, C 3 A и C 4 AF § Расчетные отношения, такие как LSF, SM и AM § Или комбинация параметров из всех трех групп.
1.2. Процесс обжига
- Современная технологическая система производства цемента, время удерживания материала внутри печи составляет от 30 до 40 минут, большая часть из которых находится в зоне обжига. Температура материала быстро увеличивается с 850 ° C до 1250 ° C до 1300 ° C, при которой формируется расплав клинкера (Mohamed A. Aldieb, 2010). Химические и физические изменения материала происходят в зоне горения одновременно; это важно с точки зрения кинетики реакций клинкеризации и процесса агломерации.Фактическая температура образования расплава зависит от химического состава сырья. Однако оператору печи необходимо поддерживать стабильную температуру в каждой части системы печи, чтобы преобразовать сырье (сырье для печи) в минералы клинкера, поскольку из-за отклонения температуры работа печи становится нестабильной. а минералы клинкера не сформированы должным образом, что приводит к изменению характеристик цемента (CCNN — Sokoto, 2009). Более того, слишком долгое нагревание сырья в печи приведет к увеличению размера минералов в клинкере, и, следовательно, клинкер станет менее реактивным и приведет к плохому качеству цемента. Рис.1 Ниже описан процесс образования клинкера. Первичные фазы клинкера завершают преобразование и свойства (Mohamed A. Aldieb, 2010): § Наиболее важным компонентом является алит (C 3 S), 50-70% в нормальных клинкерах портландцемента. Это силикат трикальция (Ca 3 SiO 5 ), модифицированный по составу и кристаллической структуре ионными замещениями. Он обеспечивает максимальную прочность до 28 дней включительно. Каждое увеличение содержания C 3 S на 10% увеличивает прочность строительного раствора EN 196 на 28 дней примерно на 5 МПа (Mohamed A.Алдиеб, 2010). § Белит (C 2 S) составляет 15-30% обычного портландцементного клинкера. Это силикат дикальция (Ca 2 SiO 4 ), он медленно вступает в реакцию и улучшает прочность на более поздних этапах (≥28 дней). § Алюминат (C 3 A) составляет 5-10% обычного портландцементного клинкера; это трикальцийалюминат (Ca 2 Al 2 O 6 ). Он выделяет много тепла, сокращает время схватывания и улучшает очень раннюю прочность, но делает цемент склонным к сульфатной атаке. § Феррит (C 4 AF) составляет до 5-15% обычного портландцементного клинкера. Это алюмоферрит тетракальция (Ca 4 AlFeO 5 ). Это мало влияет на прочность, но придает цементу темную окраску.
Рис ure 1. Схематическое изображение реакций образования клинкера (markus, 2003) |
2. Материалы и методы
- Материалы и методы, используемые при проведении химического анализа с использованием рентгеновского дифракционного аппарата в цементной промышленности для определения присутствия и количества минералов. в образцах, а также идентифицируют фазы.И метод испытания прочности на сжатие.
2.1. Материалы
- § Дистиллированная вода § 10 Утяжеленные образцы клинкера § Машина для испытания на сжатие § Тряска § Призматическая форма § Смеситель
2.2. Методика эксперимента
- § 10 г каждого образца клинкера взвешивали, измельчали и гранулировали с помощью пиридина и связующего агента. § Гранулированные образцы были подвергнуты анализу XRD / XRF, это было сделано для определения минералогического химического состава образцов клинкера и их соответствующих элементарных оксидов.Минералы клинкера, состав которых был определен с помощью XRDF / XRD: C 3 S, C 2 S и C 4 AF, а также определены составы элементарных оксидов: CaO, SiO 2 , Al 2 , O 3 и MgO. Модуль диоксида кремния, модуль оксида алюминия, коэффициент насыщения известью были найдены из составов элементарных оксидов с использованием уравнения Богога, сохраненного в виде программы в анализаторе XRD / XRF. § Для прочности на сжатие. Взвешивали 1350 г, 450 г и 225 г стандартного песка, образца цемента и дистиллированной воды соответственно и затем смешивали в автоматической смесительной машине.Затем смеси переносились в призменную форму, установленную на встряхивающей машине, и встряхивались в течение 2 минут. Затем призменную форму удаляют для отверждения в камере отверждения в течение 24 часов, а затем извлекают ее для удаления куба в разные периоды: 2 дня, 7 дней и 28 дней. Затем куб был извлечен из камеры отверждения в машину для испытания прочности на сжатие, затем куб был помещен в точку покоя машины и работал на низкой скорости, и были сняты показания. § Свободная известь определялась методом влажной химии. § Коэффициент насыщения извести (LSF) Коэффициент насыщения известью — это мера степени превращения кремнезема, глинозема и оксида железа в соответствующую известь, и его можно рассчитать по формуле: LSF обычно составляет от 93 до 97% для портландцементного клинкера, чтобы получить хороший баланс цементных свойств и приемлемую горючесть. § Модуль упругости кремнезема Модуль кремнезема по существу определяет долю кремнеземных фаз в клинкере или является показателем горючести сырья или клинкера, и его можно рассчитать по формуле: Модуль упругости кремнезема равен единице. основных компонентов C 2 S & C 3 S, которые составляют жидкую фазу и помогают в образовании алита (Taylor and Francis Group, 2018). § Модуль глинозема Модуль глинозема также используется как индикатор температуры горения и характеристики флюса в печи. Это мера соотношения оксида алюминия и оксида железа в смеси, и ее можно рассчитать по формуле: Модуль упругости оксида алюминия около 1,4 приведет к образованию жидкой фазы или флюса при самой низкой температуре в печи. . Более раннее образование жидкой фазы или флюса в печи позволяет формированию алита начинаться раньше и продолжаться в течение более длительного времени, что улучшает преобразование белита в алит.Однако AM с выше или ниже этих целевых значений 1,4, количество жидкой фазы уменьшится при более низкой температуре, длина покрытия зоны горения уменьшится, флюс станет менее жидким, что замедлит образование алита, и, следовательно, потребуется больше топлива для того, чтобы получить заданный уровень свободного известкового клинкера (Taylor and Francis Group, 2018).
Рис ure 2 . Машина для прессования бетона |
Фиг. ure 3. Тряска |
Рис ure 4 . Весы |
Рис ure 5. Химический анализатор |
Рис ure 6 . Форма призмы |
Рис. ure 7. Камера отверждения |
3. Результаты и обсуждение
3.1. Таблица 1: XRD-анализ образцов клинкера
- Гибридный цементный клинкер и цемент из этого клинкера Князь 9.0, версия 5 (www.princexml.com) AppendPDF Pro 5.5 Ядро Linux 2.6 64-битная 2 октября 2014 Библиотека 10.1.0 конечный поток эндобдж 5 0 obj > эндобдж 3 0 obj > эндобдж 8 0 объект > эндобдж 9 0 объект > эндобдж 16 0 объект > / ProcSet [/ PDF / Text / ImageB] / XObject >>> / Type / Page >> эндобдж 17 0 объект > / ProcSet [/ PDF / Text / ImageB] / XObject >>> / Type / Page >> эндобдж 18 0 объект > / ProcSet [/ PDF / Text / ImageB] / XObject >>> / Type / Page >> эндобдж 19 0 объект > / ProcSet [/ PDF / Text / ImageB] / XObject >>> / Type / Page >> эндобдж 20 0 объект > / ProcSet [/ PDF / Text / ImageB] / XObject >>> / Type / Page >> эндобдж 40 0 объект > поток HWn} W1}.
|