Расходные материалы для моделирования методом послойного наплавления (FDM/FFF)
Технология FFF имеет массу преимуществ, среди которых относительная простота конструкции принтеров и ценовая доступность как устройств, так и расходных материалов. Причем, ассортимент материалов является, пожалуй, самым широким среди всех доступных технологий. Как правило, для печати используются термопластики, но есть и исключения – композитные материалы, содержащие различные добавки, но основанные, опять-таки, на термопластиках. В этом разделе мы постараемся рассказать о наиболее широко применяемых материалах поподробнее, начиная с наиболее популярных видов.
- 1 Полилактид (PLA, ПЛА)
- 2 Акрилонитрилбутадиенстирол (ABS, АБС)
- 3 Поливиниловый спирт (PVA, ПВА)
- 4 Нейлон (Nylon)
- 5 Поликарбонат (PC, ПК)
- 6 Полиэтилен высокой плотности (HDPE, ПНД)
- 7 Полипропилен (PP, ПП)
- 8 Поликапролактон (PCL)
- 9 Полифенилсульфон (PPSU)
- 10 Полиметилметакрилат (Acrylic, оргстекло, акрил, ПММА)
- 11 Полиэтилентерефталат (PET, ПЭТ)
- 12 Ударопрочный полистирол (HIPS)
- 13 Древесные имитаторы (LAYWOO-D3, BambooFill)
- 14 Имитаторы песчаника (Laybrick)
- 15 Имитаторы металлов (BronzeFill)
Полилактид (PLA, ПЛА)
Полилактид – один из наиболее широко используемых термопластиков, что обуславливается сразу несколькими факторами. Начнем с того, что PLA известен своей экологичностью. Этот материал является полимером молочной кислоты, что делает PLA полностью биоразлагаемым материалом. Сырьем для производства полилактида служат кукуруза и сахарный тростник. В то же время, экологичность полилактида обуславливает его недолговечность. Пластик легко впитывает воду и относительно мягок. Как правило, модели из PLA не предназначаются для функционального использования, а служат в качестве дизайнерских моделей, сувениров и игрушек. Среди немногих практических промышленных применений можно отметить производство упаковки для пищевых продуктов, контейнеров для лекарственных препаратов и хирургических нитей, а также использование в подшипниках, не несущих высокой механической нагрузки (например, в моделировании), что возможно благодаря отличному коэффициенту скольжения материала.
Одним из наиболее важных факторов для применения в 3D-печати служит низкая температура плавления – всего 170-180°C, что способствует относительно низкому расходу электроэнергии и использованию недорогих сопел из латуни и алюминия. Как правило, экструзия производится при 160-170°C. В то же время, PLA достаточно медленно застывает (температура стеклования составляет порядка 50°C), что следует учитывать при выборе 3D-принтера. Оптимальным вариантом является устройство с корпусом открытого типа, подогреваемой рабочей платформой (во избежание деформаций моделей большого размера) и, желательно, дополнительными вентиляторами для охлаждения свежих слоев модели.
PLA обладает низкой усадкой, то есть потере объема при охлаждении, что способствует предотвращению деформаций. Тем не менее, усадка имеет кумулятивный эффект при увеличении габаритов печатаемых моделей. В последнем случае может потребоваться подогрев рабочей платформы для равномерного охлаждения печатаемых объектов.
Стоимость PLA относительно невелика, что добавляет популярности этому материалу.
Акрилонитрилбутадиенстирол (ABS, АБС)
ABS-пластик – пожалуй, самый популярный термопластик из используемых в 3D-печати, но не самый распространенный. Такое противоречие объясняется определенными трудностями технического характера, возникающими при печати ABS. Желание умельцев использовать ABS обуславливается отличными механическими свойствами, долговечностью и низкой стоимостью этого материала. В промышленности ABS-пластик уже получает широкое применение: производство деталей автомобилей, корпусов различных устройств, контейнеров, сувениров, различных бытовых аксессуаров и пр.
ABS-пластик устойчив к влаге, кислотам и маслу, имеет достаточно высокие показатели термоустойчивости – от 90°C до 110°C. К сожалению, некоторые виды материала разрушаются под воздействием прямого солнечного света, что несколько ограничивает применение. В то же время, ABS-пластик легко поддается окраске, что позволяет наносить защитные покрытия на немеханические элементы.
Несмотря на относительно высокую температуру стеклования порядка 100°C, ABS-пластик имеет относительно невысокую температуру плавления. Собственно, ввиду аморфности материала, ABS не имеет точки плавления, как таковой, но приемлемой температурой для экструзии считается 180°C, что на одном уровне с вышеописанным PLA.
Основным минусом ABS-пластика можно считать высокую степень усадки при охлаждении – материал может потерять до 0,8% объема. Этот эффект может привести к значительным деформациям модели, закручиванию первых слоев и растрескиванию. Для борьбы с этими неприятными явлениями используются два основных решения. Во-первых, применяются подогреваемые рабочие платформы, способствующие снижению градиента температур между нижними и верхними слоями модели. Во-вторых, 3D-принтеры для печати ABS-пластиком зачастую используют закрытые корпуса и регулировку фоновой температуры рабочей камеры. Это позволяет поддерживать температуру нанесенных слоев на отметке чуть ниже порога стеклования, снижая степень усадки. Полное охлаждение производится после получения готовой модели.
Относительно низкая «липучесть» ABS-пластика может потребовать дополнительных средств для схватывания с рабочей поверхностью, таких как клейкая лента, полиимидная пленка или нанесение раствора ABS-пластика в ацетоне на платформу непосредственно перед печатью. Подробнее о методах предотвращения деформаций читайте в разделе Как избежать деформации моделей при 3D-печати.
В то время как при комнатной температуре ABS не представляет угрозы здоровью, при нагревании пластика выделяются пары акрилонитрила – ядовитого соединения, способного вызвать раздражение слизистых оболочек и отравление. Хотя объемы производимого акрилонитрата при маломасштабной печати незначительны, рекомендуется печатать в хорошо проветриваемых помещениях или предусмотреть вытяжку. Не рекомендуется использовать ABS-пластик для производства пищевых контейнеров и посуды (особенно для хранения горячей пищи или алкогольных напитков) или игрушек для маленьких детей.
Хорошая растворимость ABS-пластика в ацетоне весьма полезна, так как позволяет производить большие модели по частям с последующим склеиванием, что значительно расширяет возможности недорогих настольных принтеров.
Поливиниловый спирт (PVA, ПВА)
Поливиниловый спирт – материал с уникальными свойствами и особым применением. Главной особенностью PVA является его водорастворимость. 3D-принтеры, оснащенные двойными экструдерами, имеют возможность печати моделей с опорными структурами из PVA. По завершении печати опоры могут быть растворены в воде, оставляя готовую модель, не требующую механической или химической обработки неровностей. Аналогично, PVA можно применять для создания водорастворимых мастер-моделей для литейных форм и самих литейных форм.
Механические свойства PVA достаточно интересны. При низкой влажности пластик обладает высокой прочностью на разрыв. При повышении влажности уменьшается прочность, но возрастает эластичность. Температура экструзии составляет 160-175°C, что позволяет использовать PVA в принтерах, предназначенных для печати ABS и PLA-пластиками.
Так как материал легко впитывает влагу, рекомендуется хранение PVA пластика в сухой упаковке и, при необходимости, просушка перед использованием. Сушку можно производить в гончарной печи или обыкновенной духовке. Как правило, просушка стандартных катушек занимает 6-8 часов при температуре 60-80°C. Превышение температуры в 220°C приведет к разложению пластика, что следует учитывать при печати.
Нейлон (Nylon)
Нейлон привлекателен своей высокой износоустойчивостью и низким коэффициентом трения. Так, нейлон зачастую используется для покрытия трущихся деталей, что повышает их эксплуатационные качества и зачастую позволяет функционировать без смазки. Вслед за широким применением нейлона в промышленности, материалом заинтересовались и в сфере аддитивного производства. Попытки печатать нейлоном предпринимались практически с первых дней технологии FDM/FFF.
В реальности существует несколько видов нейлона, производимых разными методами и имеющих несколько отличающиеся характеристики. Наиболее известным является нейлон-66, созданный американской компанией DuPont в 1935 году. Вторым наиболее популярным вариантом является нейлон-6, разработанный компанией BASF в обход патента DuPont. Эти два варианта очень схожи. С точки зрения 3D-печати основным различием является температура плавления: нейлон-6 плавится при температуре 220°C, а нейлон-66 при 265°C.
Многие любители предпочитают использовать нейлоновые нити, доступные в широкой продаже – такие, как проволока для садовых триммеров. Диаметр таких материалов зачастую соответствует диаметру стандартных FFF материалов, что делает их использование заманчивым. В то же время, подобные продукты, как правило, не являются чистым нейлоном. В случае с прутками для триммеров, материал состоит из нейлона и стеклопластика для оптимального сочетания гибкости и жесткости.
Стеклопластик обладает высокой температурой плавления, в связи с чем печать подобными материалами чревата высоким износом сопла и образованием пробок.
В последнее время предпринимаются попытки коммерческой разработки печатных материалов на основе нейлона специально для FDM/FFF устройств, в том числе Nylon-PA6 и Taulman 680. Указанные марки подлежат экструзии при температуре 230-260°C.
Так как нейлон легко впитывает влагу, расходный материал следует хранить в вакуумной упаковке или, как минимум, в контейнере с водоабсорбирующими материалами.
При печати нейлоном не рекомендуется использовать полиимидное покрытие рабочего стола, так как эти два материала сплавляются друг с другом. В качестве покрытия можно использовать липкую ленту с восковой пропиткой (masking tape). Использование подогреваемой платформы поможет снизить возможность деформации модели, аналогично печати ABS-пластиком. В связи с низким коэффициентом трения нейлона, следует использовать экструдеры с шипованными протягивающими механизмами.
Слои нейлона прекрасно схватываются, что минимизирует вероятность расслоения моделей.
Нейлон плохо поддается склеиванию, поэтому печать крупных моделей из составных частей затруднительна. Как вариант, возможна сплавка частей.
Так как при нагревании нейлона возможно выделение токсичных паров, рекомендуется производить печать в хорошо вентилируемых помещениях или с использованием вытяжки.
Поликарбонат (PC, ПК)
Поликарбонаты привлекательны за счет своей высокой прочности и ударной вязкости, а также устойчивости к высоким и низким температурам.
Стоит отметить потенциальный риск для здоровья при печати: в качестве сырья зачастую используется токсичное и потенциально карциногенное соединение бисфенол А. Остаточный бисфенол А может содержаться в готовых изделиях из поликарбоната и испаряться при нагревании, в связи с чем рекомендуется производить печать в хорошо вентилируемых помещениях.
Температура экструзии зависит от скорости печати во избежание растрескивания, но минимальной температурой на скорости 30мм/сек можно считать 265°С. При печати рекомендуется использование полиимидной пленки для лучшего схватывания с поверхностью рабочего стола. Высокая склонность поликарбоната к деформации требует использования подогреваемой платформы и, при возможности, закрытого корпуса с подогревом рабочей камеры.
Поликарбонат обладает высокой гигроскопичностью (легко поглощает влагу), что требует хранения материала в сухих условиях во избежание образования пузырьков в наносимых слоях. В случае длительной печати во влажном климате может потребоваться хранение даже рабочей катушки во влагозащитном контейнере.
Полиэтилен высокой плотности (HDPE, ПНД)
Пожалуй, наиболее распространенный пластик в мире, полиэтилен относительно редок среди 3D-печатных материалов. Причиной тому служат сложности при послойном изготовлении моделей.
Полиэтилен легко плавится (130-145°С) и быстро застывает (100-120°С), вследствие чего наносимые слои зачастую не успевают схватываться. Кроме того, полиэтилен отличается высокой усадкой, что провоцирует закрутку первых слоев и деформацию моделей в целом при неравномерном застывании. Печать полиэтиленом требует использования подогреваемой платформы и рабочей камеры с аккуратной регулировкой температурного режима для замедления остывания нанесенных слоев. Кроме того, потребуется производить печать на высокой скорости.
Трудности в использовании с лихвой компенсируются дешевизной и общедоступностью этого материала. В последнее время были разработаны несколько устройств для переработки пластиковых отходов из ПНД (бутылок, пищевой упаковки и пр.) в стандартные нити для печати на FDM/FFF принтерах. Примерами служат FilaBot и RecycleBot. За счет простоты конструкции, устройства RecycleBot зачастую собираются силами 3D-умельцев.
При плавлении полиэтилена происходит эмиссия паров вредных веществ, поэтому рекомендуется производить печать в хорошо вентилируемых помещениях.
Полипропилен (PP, ПП)
Полипропилен – широко распространенный пластик, применяемый в производстве упаковочных материалов, посуды, шприцов, труб и пр. Материал имеет низкую удельную массу, нетоксичен, обладает хорошей химической стойкостью, устойчив к влаге и износу и достаточно дешев. Среди недостатков полипропилена можно отметить уязвимость к температурам ниже -5°С и к воздействию прямого солнечного света.
Главной трудностью при печати полипропиленом является высокая усадка материала при охлаждении – до 2,4%. Для сравнения, усадка популярного, но уже достаточно проблематичного ABS-пластика достигает 0,8%. Несмотря на то, что полипропилен хорошо прилипает к холодным поверхностям, рекомендуется производить печать на подогреваемой платформе во избежание деформации моделей. Минимальная рекомендуемая температура экструзии составляет 220°С.
Полипропиленовые нити для печати предлагаются на продажу компаниями Orbi-Tech, German RepRap, Qingdao TSD Plastic. Компания Stratasys разработала имитатор полипропилена, оптимизированный для 3D-печати, под названием Endur.
Поликапролактон (PCL)
Поликапролактон (он же Hand Moldable Plastic, Mold-Your-Own Grips, InstaMorph, Shapelock, Friendly Plastic, Polymorph, Полиморфус, Экоформакс) – биоразлагаемый полиэстер, отличающийся чрезвычайно низкой температурой плавления порядка 60°С. На практике, это свойство создает определенные проблемы при 3D-печати, так как далеко не все 3D-принтеры можно настроить для работы при столь низких температурах. Нагревание поликапролактона до привычных экструзионных температур (около 200°С) вызывает потерю механических свойств и может привести к поломке экструдера.
Поликапролактон нетоксичен, что обуславливает его применение в медицинской отрасли, и биоразлагаем. При попадании в организм поликапролактон распадается, что делает печать этим материалом безопасной. Благодаря низкой температуре плавления отсутствует опасность ожогов при прикосновении к свежим моделям. Высокая пластичность материала делает возможным многократное использование.
Поликапролактон малопригоден для создания функциональных механических моделей ввиду вязкости (температура стеклования составляет -60°С) и низкой теплостойкости (температура плавления составляет 60°С). С другой стороны, этот материал прекрасно подходит для производства макетов и пищевых контейнеров.
Материал легко слипается с поверхностью даже холодного рабочего стола и легко поддается окраске.
Полифенилсульфон (PPSU)
Полифенилсульфон – высокопрочный термопластик, активно применяемый в авиационной промышленности. Материал имеет прекрасную химическую и тепловую устойчивость и практически не горит. Полифенилсульфон биологически инертен, что позволяет использовать этот материал для производства посуды и пищевых контейнеров. Диапазон эксплуатационных температур составляет -50°С — 180°С. Пластик устойчив к воздействию растворителей и горюче-смазочных материалов.
При всех своих достоинствах, полифенилсульфон редко используется в 3D-печати ввиду высокой температуры плавления, достигающей 370°С. Такие температуры экструзии не под силу большинству настольных принтеров, хотя теоретически печать возможна при использовании керамических сопел. В настоящее время единственным активным пользователем материала является компания Stratasys, предлагающая промышленные установки Fortus.
Полиметилметакрилат (Acrylic, оргстекло, акрил, ПММА)
Полиметилметакрилат – это всем известное органическое стекло. Материал прочен, влагоустойчив, экологичен, легко поддается склеиванию, достаточно пластичен и устойчив к воздействию прямого солнечного света.
К сожалению, акрил плохо подходит для FDM/FFF печати в силу ряда причин. Акрил плохо хранится в виде катушек с нитью, так как постоянное механическое напряжение приводит к постепенному разрушению материала. Во избежание образования пузырьков разрешение печати должно быть высоким – с точностью, практически недоступной для домашних принтеров. Быстрое застывание акрила же требует жесткого климатического контроля рабочей камеры и высокой скорости печати. Опять-таки, показатели скорости печати FDM/FFF принтеров обратно пропорциональны разрешению печати, что усугубляет проблему.
Тем не менее, попытки печати акрилом предпринимаются, а некоторые из них дают относительно положительные результаты. Однако при создании достаточно прочных моделей избежать образования пузырьков и достигнуть привычной прозрачности материала пока не удается. На данный момент наилучшие результаты с акрилом показывает другая технология печати – многоструйное моделирование (MJM) от компании 3D Systems. В данном случае используется фотополимерный вариант акрила. Значительных успехов достигла и компания Stratasys, использующая собственный фотополимерный имитатор акрила VeroClear на принтерах марки Objet Eden. Остается надеяться, что высокий спрос на акрил приведет к появлению композитных материалов на основе полиметилметакрилата, предназначенных специально для FDM/FFF печати.
Полиэтилентерефталат (PET, ПЭТ)
Полиэтилентерефталат – под этим сложным названием скрывается материал, используемый для производства пластиковых бутылок и другой пищевой и медицинской тары.
Материал имеет высокую химическую устойчивость к кислотам, щелочам и органическим растворителям. Физические свойства ПЭТ также впечатляют высокой износоустойчивостью и терпимостью к широкому диапазону температур – от -40°С до 75°С. Кроме всего прочего, материал легко поддается механической обработке.
Печать с использованием ПЭТ несколько проблематична, ввиду сравнительно высокой температуры плавления, достигающей 260°С и значительной усадки при остывании, составляющей до 2%. Использование ПЭТ в качестве расходного материала требует примерно тех же условий, что и печать ABS-пластиком.
Для достижения прозрачности моделей необходимо быстрое охлаждение при прохождении порога стеклования, составляющего 70°С – 80°С.
Материал стал предметом внимания 3D-умельцев, использующих использованную тару в качестве сырья для бытового производства расходных материалов для 3D-печати. Для изготовления нитей используются такие перерабатывающие устройства, как FilaBot или RecycleBot.
Ударопрочный полистирол (HIPS)
Ударопрочный полистирол широко используется в промышленности для производства различных бытовых изделий, строительных материалов, одноразовой посуды, игрушек, медицинских инструментов и пр.
При 3D-печати полистирол демонстрирует физические свойства, весьма схожие с популярным ABS-пластиком, что делает этот материал все более популярным среди 3D-умельцев. Наиболее же привлекательной особенностью полистирола является отличие от ABS в отношении химических свойств: полистирол достаточно легко поддается органическому растворителю Лимонену. Так как на ABS-пластик Лимонен эффекта не имеет, возможно использование полистирола в качестве материала для построения растворимых поддерживающих структур, что исключительно полезно при построении сложных, переплетенных моделей с внутренними опорами. В сравнении с удобным, водорастворимым поливиниловым спиртом (PVA-пластиком), полистирол выгодно отличается относительно низкой стоимостью и устойчивостью к влажному климату, затрудняющему работу с PVA.
Стоит иметь в виду, что некоторые производители ABS-пластика подмешивают в свои расходные материалы несколько более дешевый полистирол. Соответственно, модели из таких материалов могут раствориться в Лимонене вместе с опорными структурами.
При нагревании полистирола до температуры экструзии возможно выделение токсичных испарений, в связи с чем рекомендуется осуществлять печать в хорошо проветриваемых помещениях.
Древесные имитаторы (LAYWOO-D3, BambooFill)
LAYWOO-D3 – недавняя разработка, предназначенная для печати моделей, напоминающих деревянные изделия. Материал на 40% состоит из натуральных древесных опилок микроскопического размера и на 60% из связующего полимера. LAYWOO-D3 весьма прост в обращении, будучи практически неподверженным деформациям и не требуя использования подогреваемой платформы. Согласно производителям, полимер нетоксичен и полностью безопасен.
Уникальные свойства материала позволяют добиваться различных визуальных результатов при печати с разными температурами сопла. Диапазон рабочих температур составляет 180°С-250°С. По мере увеличения температуры экструзии, оттенок материала становится прогрессивно более темным, позволяя имитировать разные сорта древесины или годовые кольца.
Готовые модели прекрасно поддаются механической обработке – шлифовке, сверлению и пр. Кроме того, изделия легко окрашиваются, а неокрашенные модели даже имеют характерный древесный запах.
К сожалению, стоимость материала почти в четыре раза превышает цену на такие популярные материалы, как PLA и ABS-пластики. По мере прогнозируемого роста популярности, материал должен стать более доступным.
В настоящее время ведется разработка и тестирование альтернативных материалов, таких как BambooFill от голландской компании ColorFabb.
Имитаторы песчаника (Laybrick)
Композитный материал от изобретателя Кая Парти, ответственного за создание революционного древесного имитатора LAYWOO-D3. На этот раз Кай нацелился на имитацию песчаника, используя опробованный метод смешивания связующего материала с наполнителем – в данном случае минеральным.
Laybrick позволяет производить объекты с различной текстурой поверхности. При низких температурах экструзии порядка 165°С-190°С готовые изделия имеют гладкую поверхность. Повышение температуры печати делает материал более шершавым, вплоть до высокой степени сходства с натуральным песчаником при температуре экструзии свыше 210°С.
Материал легок в работе, не требуя подогрева рабочей платформы, не демонстрируя существенных деформаций при усадке и не производя токсичные испарения при нагревании. Единственным недостатком можно считать достаточно высокую стоимость материала, что в немалой степени обуславливается ограниченным производством.
Имитаторы металлов (BronzeFill)
Металлы привлекают сторонников аддитивного производства с ранних дней технологий 3D-печати. К сожалению, печать чистыми металлами и сплавами вызывает массу трудностей, непреодолимых для большинства методов 3D-печати. Полностью функциональные металлические изделия можно произвести только с помощью таких технологий, как SLS, DLMS или EBM, требующих использования промышленных установок, чья стоимость исчисляется сотнями тысяч долларов. В то же время, имитаторы металлов успешно используются в струйной 3D-печати (3DP), где формирование изделий происходит из металлических порошков, частицы которых скрепляются наносимым связующим материалом. В FDM/FFF печати металлические имитаторы лишь появляются на свет.
Интересным примером служит BronzeFill – фактически, прозрачный PLA-пластик с наполнителем из микрочастиц бронзы. Материал, в настоящее время проходящий бета-тестирование, должен доказать пригодность для использования в любых принтерах, предназначенных для работы с полилактидом.
Готовые изделия легко поддаются полировке, достигая высокого внешнего сходства с цельнометаллическими изделиями. В то же время стоит учитывать, что связующим элементом материала является термопластик, с соответствующими механическими и температурными ограничениями.
Перейти на главную страницу Энциклопедии 3D-печати
обзор материала, настройки 3D-печати и советы по устранению проблем
Полиэтилентерефталатгликоль (PETG, ПЭТГ) — износостойкий термопласт из класса полиэфиров, характеризуемый очень высокой прочностью и широким температурном диапазоном применения (от -40°С до +70°С). Буква G в названии означает, что материал был модифицирован гликолем для предотвращения кристаллизации и сохранения прозрачности при охлаждении.
Общие характеристики материала REC Relax на основе PETG
- Плотность: 1,30 г/см^3
- Температура эксплуатации: от -40°С до +70°С
- Температура размягчения: ~80°C
Механические характеристики
- Ударная вязкость по Шарпи: 4,17 кДж/м^2
- Прочность при растяжении вдоль слоев: 36,5 МПа
- Модуль упругости при растяжении вдоль слоев: 1,12 ГПа
- Прочность на изгиб: 76,1 МПа
- Модуль упругости на изгиб: 2,06 ГПа
- Максимальная нагрузка на изгиб: 120 Н
- Прочность при растяжении поперек слоев: 33,6 МПа
- Модуль упругости при растяжении поперек слоев: 1,73 ГПа
- Максимальная нагрузка на растяжение: 1485 Н
- Прочность на сжатие: 51,7 МПа
- Модуль упругости на сжатие: 1,81 ГПа
- Максимальная нагрузка на сжатие: 6386 Н
- Коэффициент удлинения: 2,41%
- Предел текучести при растяжении и при температуре 23°С: 53 МПа
- Прочность при изгибе 2,8 мм/мин.
23°C: 76,07 МПа
- Твердость по Шору (шкала D): 76
Основные преимущества PETG (REC Relax):
- Высокая жесткость и твердость;
- Стойкость к разбавленным кислотам и щелочам, растворам солей, мылу, маслам, спиртам, алифатическим углеводородам;
- Хорошо стерилизуется спиртами;
- Легко перерабатывается;
- Стойкость к внешним неблагоприятным климатическим факторам;
- Отсутствие запахов при 3D-печати;
- Высокая межслойная адгезия, низкая усадка, высокая адгезия к платформе, облегчающие 3D-печать
Проще говоря, преимуществ материала больше, чем недостатков, и изготовление изделий из PETG при правильно подобранных настройках 3D-печати не доставит трудностей. Поэтому наш материал получил название Relax.
Обладая лучшей ударной вязкостью, чем акрил, и более низкой стоимостью, чем поликарбонат, PETG пользуется популярностью в различных отраслях и зачастую служит выбором для производства сложных изделий.
Сферы применения включают производство как прототипов, так и конечных изделий: корпусов приборов, защитных кожухов, емкостей различного назначения, деталей механизмов, детских игрушек, функциональных изделий для размещения на улице и многого другого.
Температура размягчения PETG составляет 80°С градусов — ниже, чем у ABS-пластика (105°С), но выше, чем у PLA-пластика (55°С). В большинстве климатических зон это позволяет использовать изделия из PETG вне помещений без деформаций от солнечного нагрева.
Настройки 3D-печати PETG (REC Relax)
- Температура экструзии. Стандартная температура для 3D-печати PETG от разных производителей варьируется в диапазоне 215-245°C. Не превышайте температуру печати 250°C, так как это может привести к повреждению PTFE-трубки. Также стоит избегать превышения допустимой температуры по причине возможного подтекания пластика из сопла и образованию паутины или нитей (так называемых «соплей») на изделии.
- Температура стола. Стандартная температура стола составляет 60-80°C. Мнения как производителей, так и пользователей разнятся: некоторые рекомендуют ставить 20°C, другие — 90°C. Наша рекомендация: для хорошей адгезии достаточно стандартной температуры стола 60-80°C.
- Ретракт. PETG не любит высокие скорости по причине его мягкости, поэтому на большинстве 3D-принтеров с боуденовской системой подачи филамента (с отдельной установкой хотэнда и проталкивающего механизма, соединенных длинной трубкой) скорость ретракта желательно выставлять на уровне 25 мм/с, а длину ретракта — в диапазоне 6-7 мм. При использовании экструдеров с директ-подачей филамента (с хотэндом и проталкивающим механизмом в одной сборке) допускается ретракт в диапазоне 3-4 мм.
- Охлаждение. В большинстве случаев охлаждение печатаемых изделий не требуется, но если на вашей модели большое количество нависающих элементов, желательно включить обдув.
- Скорость. PETG достаточно чувствителен к настройкам скорости. При слишком быстрой укладке материал не будет успевать плавиться, что может привести к пропуску шагов экструдера и даже пропуску слоев. Повышение температуры экструзии в этом случае мало чем поможет. Слишком медленный режим наоборот может привести к возникновению «соплей» и деформации деталей. Для сопла 0,4 мм. мы рекомендуем выставлять скорость 3D-печати PETG на уровне 50-55 мм/с, а при построении первого слоя и внешних контуров не превышать 25 мм/с.
- Адгезия к столу. PETG очень прочно держится на стекле и иных материалах без дополнительных средств адгезии. Более того, ввиду избыточной адгезии при отделении напечатанных моделей возможен отрыв кусочков стекла.
Во избежание сколов рекомендуется наносить на стекло клей или скотч, а также выставлять правильный зазор между стеклом и соплом. Если для ABS и PLA зазор между стеклом и соплом требуется минимальный, то по многим рекомендациям для PETG необходимо немного увеличить зазор.
Материал неплохо поддается механической обработке, например шлифованию или сверлению. Для сглаживания поверхностей, придания глянца или склеивания отдельных частей можно использовать дихлорэтан или дихлорметан. Не забывайте, что эти растворители весьма токсичны и летучи, а потому требуют соблюдения техники безопасности. Покраске PETG поддается с трудом, но при желании материал можно обработать грунтовкой, а затем покрасить.
Хранение PETG (REC Relax)PETG достаточно гигроскопичен, и его хранение зависит от климатических условий вашего региона. Если вы используете пластик в условиях влажного климата, то при неправильном хранении материал может впитывать влагу из воздуха. Чтобы избежать чрезмерного набора влаги, материал следует хранить в прохладном сухом месте. Точка росы для безопасного хранения PETG пластика должна быть ниже нуля. Самый простой и при этом весьма эффективный способ — это хранение филамента в герметичных пакетах с силикагелем. Наши катушки поставляются в вакуумной упаковке, но после вскрытия катушку можно поместить в обычный или вакуумный Zip-пакет подходящего размера с пакетиком влагопоглотителя внутри, предварительно выжав или откачав из пакета побольше воздуха. Также для хранения можно использовать жесткие герметичные боксы или просто плотно закрывающиеся контейнеры с силикагелем. Статью про хранение пластика можно прочитать здесь.
Лучший вариант — не давать филаменту набирать влагу вообще, но на практике это почти нереализуемо. Значит, перед 3D-печатью желательно подстраховаться и просушить пластик.
Как понять, что пластик отсырел? 3D-печать может сопровождаться характерными щелчками лопающихся пузырьков, укладка может быть неравномерной, на поверхностях изделий могут появляться всевозможные дефекты. Все это, как правило, сопровождается снижением межслойной адгезии, а нередко и изменением механических свойств самого материала, например прочности. Чем больше в пластике влаги, тем больше он теряет прочность при 3D-печати, а если влаги очень много, то это становится уже видно невооруженным глазом (пропуски, пузырьки и так далее), при этом прочность падает уже разительно.
PETG можно высушить несколькими способами. Самые популярные — это сушка в электрическом духовом шкафу, фруктосушилке, специализированной сушилке для филамента, в закрытой камере 3D-принтера. Многие пользователи даже сушат пластики на батареях отопления. Профессиональные студии 3D-печати и крупные производства обычно используют специализированные cушильные шкафы.
Мы рекомендуем использовать для просушки филамента специализированные сушилки пластика для 3D-печати или же фруктосушилки, как более дешевый вариант. Сами катушки под брендом REC сделаны из ударопрочного поликарбоната, выдерживающего продолжительное нагревание до 130°C.
Мы очень ответственно относимся к производству филаментов и проводим множество испытаний для проверки качества производимых материалов. Результаты испытаний доступны по ссылкам ниже.
Испытание:
На ударную вязкость по Шарпи
На изгиб
На разрыв вдоль слоев
На разрыв поперек слоев
На сжатие
СанЭпидем
*Все испытания проводились на 3D-печатных образцах с толщиной слоя 0,2 мм.
Безопасность PETGВсе материалы для 3D-печати, производимые нашей компанией, имеют сертификаты безопасности. С сертификатом безопасности на REC Relax (PETG) можно ознакомиться по этой ссылке.
Lexan — wikidoc
Файл:Lexan.png
Химическая структура Lexan
LEXAN — зарегистрированная торговая марка General Electric из высокопрочного термопласта на основе поликарбонатной смолы, предназначенного для замены стекла в тех случаях, когда потребность в прочности оправдывает его более высокую стоимость. . Это поликарбонатный полимер, полученный реакцией бисфенола А с карбонилхлоридом, также известным как фосген. Lexan — это торговая марка листового поликарбоната толщиной от 0,75 мм (0,03 дюйма) до 12 мм (0,48 дюйма). Приложения в основном в трех областях — строительство (остекление и купола), промышленность (защита машин и готовые детали), а также связь и вывески.
Лексан был открыт в 1953 году химиком GE доктором Дэниелом Фоксом, когда он работал над покрытием проводов. Доктор Герман Шнелл из Bayer в Германии подал заявку на патент США на практически идентичную молекулу в том же году, когда GE подала заявку на патент, в 1955 году.
Lexan производится компанией GE Plastics, подразделением General Electric. Он производится на нескольких заводах GE, крупнейший из которых находится в Маунт-Вернон, штат Индиана; Картахена, Испания; и Берген-оп-Зум, Нидерланды. Штаб-квартира GE Plastics находится в Питтсфилде, Массачусетс. Джек Уэлч, бывший генеральный директор GE, начинал инженером-химиком в этом подразделении в Питтсфилде.
Лексан похож на полиметилметакрилат (оргстекло/люцит/плексиглас), который обычно называют акрилом, по внешнему виду, но он гораздо более прочный, часто до такой степени, что его называют «пуленепробиваемым» (в зависимости от толщины образца и тип используемого оружия). Лексан используется в аэрокосмической промышленности для фонарей самолетов, ветровых стекол и других окон, но его можно найти и в предметах домашнего обихода, таких как бутылки, компакт-диски и DVD-диски. Возможно, наиболее заметным потребительским продуктом Lexan являются Apple Computer iBook и iPod; блестящий белый пластик — это лексан. Он также используется компанией Nalgene для изготовления 1-литровой бутылки для воды с широким горлышком, популярной среди туристов и альпинистов. Lexan также используется другими производителями бутылок для воды. Однако Lexan выщелачивает бисфенол А, химическое вещество, которое некоторые исследования связывают с раком. Эти исследования показывают, что воздействие низких уровней BPA вызывает ряд серьезных последствий для здоровья лабораторных животных. [1]
Экспертная группа из 12 ученых обнаружила, что существует «некоторая обеспокоенность тем, что воздействие химического вещества бисфенола А в утробе матери вызывает нервные и поведенческие эффекты», согласно проекту отчета, подготовленному Национальной программой токсикологии (NTP). ) Центр оценки рисков для репродукции человека.
Для взрослого населения в целом группа экспертов обнаружила «незначительную озабоченность неблагоприятными репродуктивными эффектами после воздействия».
[2]
Аналогичные продукты, предлагаемые другими компаниями, см. в разделе Поликарбонаты.
Лексан также используется в:
- гоночных автомобилей для замены более тяжелых (и бьющихся) лобовых и оконных стекол.
- теплицы для укрытия.
- Скейтборды Flexdex «Clear» модели
- для кузовов радиоуправляемых автомобилей
- для мотоциклетных очков
- Радиоуправляемые вертолетные стабилизаторы и гироскопы производства RDLohr
- Кубик Рубика цветные плитки
- Шайбы для аэрохоккея
- Несколько гитарных медиаторов
- Альтернатива медным мундштукам для духовых музыкальных инструментов.
- Все вагоны метро Нью-Йорка, от R110A до более новых вагонов, таких как R160B, оснащены лексаном для защиты от вандализма. [3]
Лексан в популярной культуре
- Молекула лексана была показана в Звездный путь IV: Путешествие домой визуально изображена на экране компьютера Apple Macintosh, описанном в фильме как «прозрачный алюминий». [ необходима ссылка ]
- Лексан часто используется в Разрушителя мифов для защиты ведущих шоу и команды от любых взрывов.
Внешние ссылки
- GE LEXAN®
Каталожные номера
- ↑ поликарбонат#Потенциальные опасности при контакте с пищевыми продуктами см. описание поликарбоната
- ↑ http://cerhr.niehs.nih.gov/chemicals/bisphenol/draftBPA_MtgSumm080807.pdf
- ↑ http://www.nycsubway.org/cars/r110a.html Описание NYCS R110A
ca:лексан
Шаблон: Исходники WikiDoc
Поликарбонат (ПК) – свойства, применение и структура
Что такое поликарбонат (ПК)?
Что такое поликарбонат (ПК)?
Поликарбонат представляет собой прочный, аморфный и прозрачный термопластичный полимер с высокими эксплуатационными характеристиками.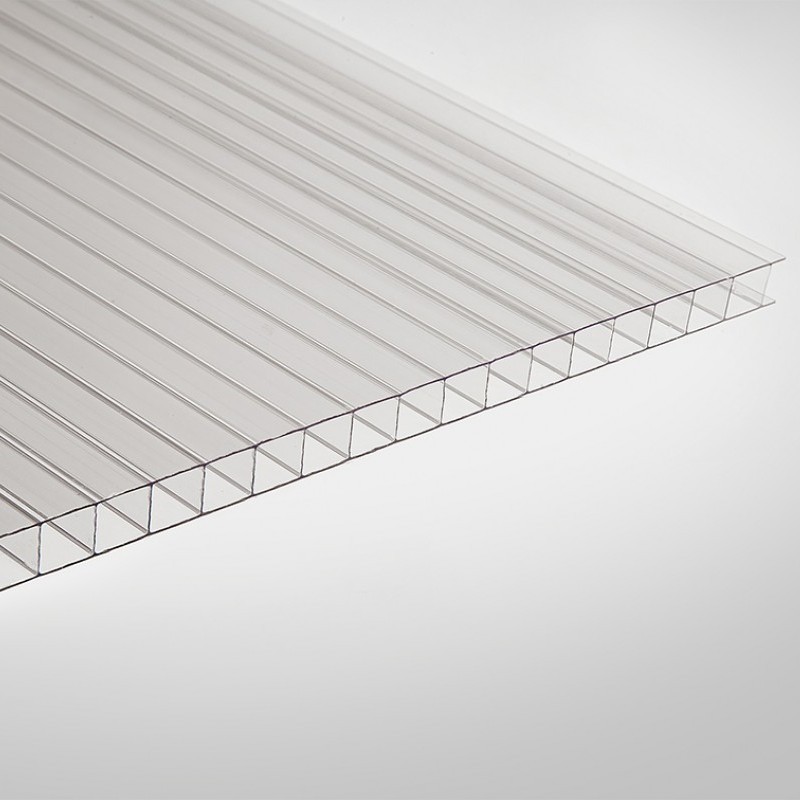
- Высокая ударная вязкость
- Высокая стабильность размеров
- Хорошие электрические свойства среди прочих
По своим характеристикам поликарбонат аналогичен полиметилметакрилату (ПММА, акрил). Но ПК дороже, прочнее и используется в более широком диапазоне температур. Он имеет температуру плавления 155°C.
Поскольку ПК демонстрирует превосходную совместимость с некоторыми полимерами, он широко используется в смесях, таких как ПК/АБС, ПК/ПЭТ и ПК/ПММА. Некоторые из распространенных приложений — это компакт-диски, защитные каски, пуленепробиваемые стекла, линзы автомобильных фар, детские бутылочки для кормления, кровля, остекление и т. д.
ЗНАЕТЕ ЛИ ВЫ? Поликарбонатбыл впервые получен в 1953 году доктором Х. ![]() |
Как производится ПК?
Как производится ПК?
Поликарбонаты производятся путем конденсационной полимеризации бисфенола А (BPA; C 15 H 16 O 2 ) и фосген (COCl 2 ).Каковы свойства поликарбоната?
Каковы свойства поликарбоната?
ПК — идеальный материал, известный своими универсальными характеристиками. Он широко используется в промышленности из-за его экологически чистой обработки и возможности вторичной переработки. Он включает в себя уникальный набор химических и физических свойств. Это делает его подходящим для стекла, ПММА и ПЭ. К основным свойствам поликарбонатов относятся:- Прочность – Прочность поликарбоната составляет от -20°C до 140°C. Они практически не ломаются.
- Высокая ударопрочность – ПК обладает высокой прочностью, что делает его устойчивым к ударам и разрушениям.
Он обеспечивает безопасность и комфорт в приложениях, требующих высокой надежности и производительности. Полимер имеет плотность 1,2 – 1,22
- Коэффициент пропускания – ПК представляет собой чрезвычайно прозрачный пластик, способный пропускать более 90% света как стекло. Листы поликарбоната доступны в широком диапазоне оттенков. Эти листы можно настраивать в зависимости от приложения конечного пользователя.
- Легкий – Эта функция предоставляет OEM-производителям практически неограниченные возможности проектирования по сравнению со стеклом. Свойство повышает эффективность и упрощает процесс установки. Это также снижает общие транспортные расходы.
- Защита от ультрафиолетового излучения – Поликарбонаты могут блокировать ультрафиолетовое излучение. Они обеспечивают 100% защиту от вредных ультрафиолетовых лучей.
- Optical Nature – Обладая аморфной структурой, поликарбонат обладает превосходными оптическими свойствами.
Показатель преломления прозрачного поликарбоната составляет 1,584.
- Химическая стойкость – Хорошая химическая стойкость к разбавленным кислотам, алифатическим углеводородам и спиртам. Показывает умеренную стойкость к маслам и жирам. PC легко подвергается воздействию разбавленных щелочей, ароматических и галогенированных углеводородов. Производители рекомендуют чистить ПК средствами, не изменяющими их химическую природу. Он чувствителен к абразивным щелочным чистящим средствам.
- Термостойкость – Поликарбонаты обладают высокой термостойкостью. Они термостабильны до 135°C. Дальнейшая термостойкость может быть улучшена путем добавления антипиренов без ущерба для свойств материала.
СОВЕТ : Если у вас есть особые требования, попробуйте использовать аспект «ключевая характеристика», чтобы сузить область поиска и найти интересующую марку поликарбоната.
Каковы сильные стороны и недостатки высокотемпературных сортов поликарбоната?
Каковы сильные стороны и ограничения высокотемпературных марок поликарбоната?
Сильные стороны | Ограничения |
|
|
Как добавки или смеси термопластов оптимизируют свойства материала?
Как добавки или смеси термопластов оптимизируют свойства материала?
Добавление добавок
Сопротивление ползучести поликарбонатов может быть улучшено до 28 МПа путем добавления 5-40% наполнителей при температуре 210°F.

- ,
- прочность на изгиб и
- прочность на растяжение.
Добавление добавок может улучшить огнестойкость, термическую стабильность, устойчивость к ультрафиолетовому излучению и стабильность цвета. Они также улучшают некоторые другие свойства. Поликарбонатные листы с покрытием также обладают лучшей устойчивостью к атмосферным воздействиям, повреждениям и химическим воздействиям.
- Стабилизаторы на основе бензотриазола полезны для стабилизации ПК от УФ-излучения. Они также защищают от ультрафиолетового излучения.
- Стабилизаторы на основе эфиров фосфорной кислоты улучшают термическую стабильность поликарбоната.
- Антипирены, такие как галогенированные, фосфорсодержащие и силиконовые, широко используются в качестве добавок. Они помогают достичь требуемых характеристик UL, увеличить LOI и снизить теплоту сгорания продуктов из поликарбоната.
Смеси термопластов
Смеси поликарбонатакоммерчески успешны. Они обеспечивают правильный баланс между производительностью и производительностью.
Смеси ПК/полиэстера : Подходит для применений, требующих высокой химической стойкости. Смеси ПК/ПБТ обладают более высокой химической стойкостью, чем смеси ПК/ПЭТ. Это связано с более высоким кристаллическим поведением ПБТ. Смешанные сорта ПЭТ обладают превосходной термостойкостью.
Смеси ПК/АБС : прочность поликарбоната и высокая термостойкость сочетаются с пластичностью и технологичностью АБС. Это обеспечивает отличное сочетание свойств. См. смеси ПК/АБС здесь »
Как обрабатывается ПК?
Как обрабатывается ПК?
Общие методы производства деталей из поликарбоната:- Экструзия
- Литье под давлением
- Выдувное формование
- Термоформование
Поликарбонат расплавляют и под высоким давлением помещают в форму, чтобы придать ему желаемую форму.
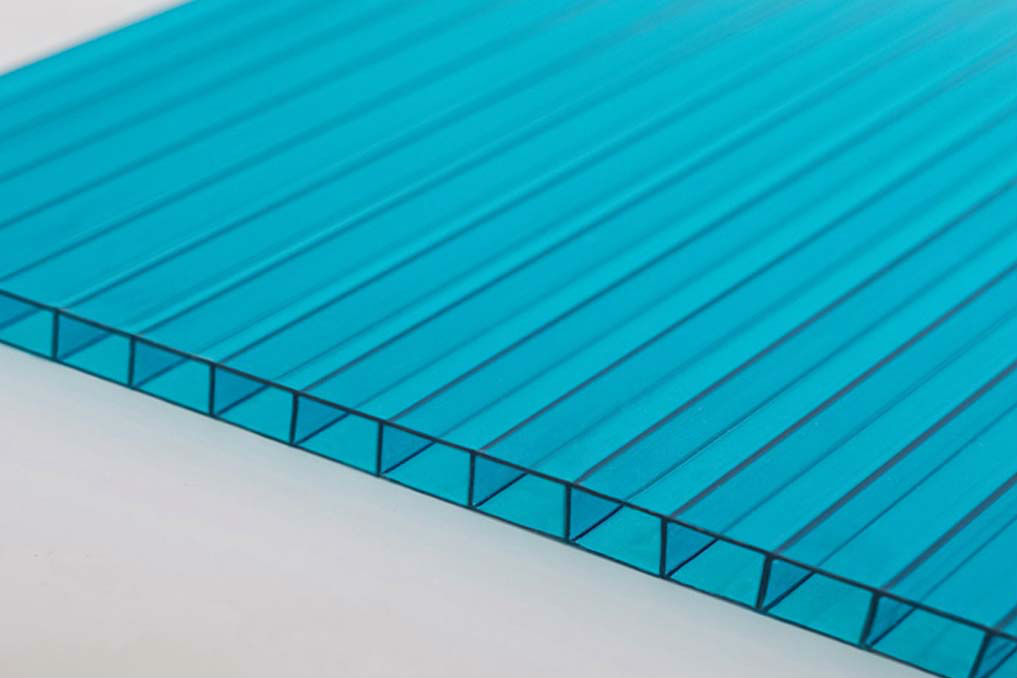
Во избежание деградации материала идеальное максимальное время пребывания составляет от 6 до 12 минут в зависимости от выбранной температуры расплава. Двумя основными методами обработки поликарбоната являются литье под давлением и экструзия.
Литье под давлением
Литье под давлением является наиболее распространенным методом производства поликарбонатов и их смесей. Поликарбонат очень вязкий. Обычно его обрабатывают при высоких температурах, чтобы уменьшить его вязкость. В этом процессе горячий расплав полимера выдавливается в форму под высоким давлением. Форма при охлаждении придает расплавленному полимеру желаемую форму и характеристики. Этот процесс обычно используется для производства бутылок и тарелок из поликарбоната. Так как поликарбонат является плохотекучим пластиком, толщина стенки не должна быть слишком тонкой.
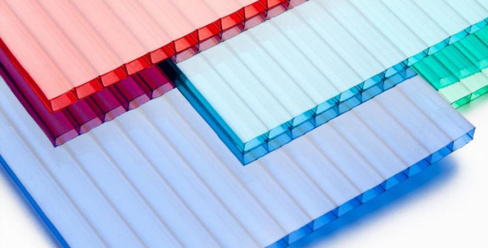
Некоторые рекомендации, которые необходимо соблюдать при обработке поликарбоната методом литья под давлением, приведены ниже:
Смола | Температура плавления, °С | Температура формы, °C | Усадка при литье, % |
ПК | 280-320 | 80-100 | 0,5-0,8 |
Высокотемпературный ПК | 310-340 | 100-150 | 0,8-0,9 |
Заполненный ПК | 310-330 | 80-130 | 0,3-0,5 |
ПК/АБС | 240-280 | 70-100 | 0,5-0,7 |
ПК/ПБТ | 250-270 | 60-80 | 0,8-1,0 |
ПК/ПЭТ | 260-280 | 60-80 | 0,6-0,8 |
Экструзия
В процессе экструзии расплав полимера проходит через полость, которая помогает придать ему окончательную форму.
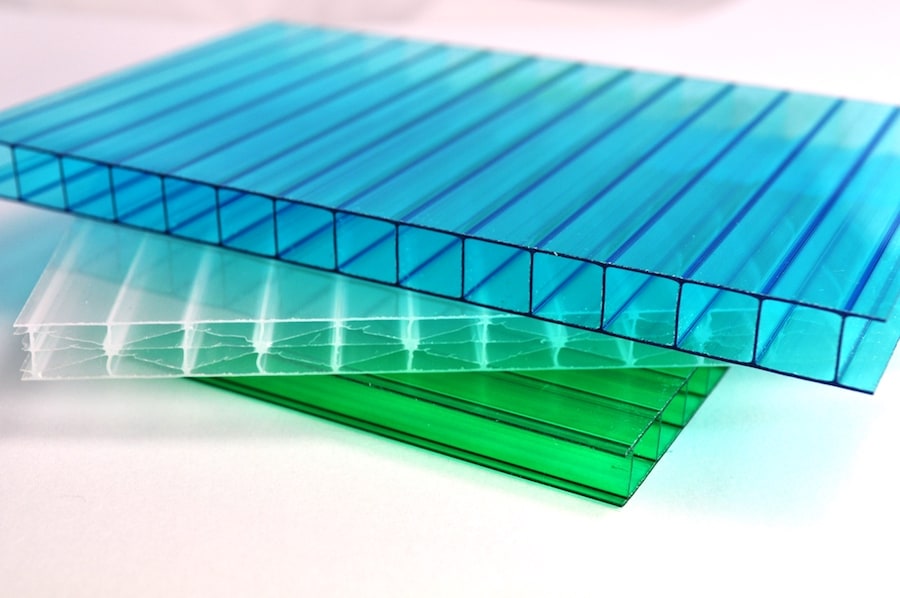
- Температура экструзии: 230-260°C
- Рекомендуется соотношение L/D 20-25
3D-печать
Поликарбонат — самый прочный термопластичный материал. Это интересный выбор в качестве нити для 3D-печати. ПК известен тем, что сохраняет термостойкость. Он не разбивается, как оргстекло.
- Машинная гибка при комнатной температуре
- Температура печати от 260 до 300°C
- Рекомендуемая температура печатного стола 90°C или выше
- Скорость печати: идеальная 30 мм/с, может быть увеличена до 60 или 80 мм/с
Фото: Polymaker
Поликарбонатный материал можно склеивать несколькими способами.
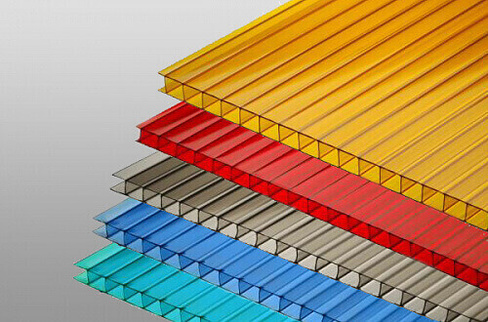
Безопасен ли ПК?
Безопасен ли ПК?
Поликарбонатный пластик — идеальный материал для детских бутылочек, многоразовых бутылочек для воды, поильников и других контейнеров для еды и напитков. Хотя безопасность ПК подверглась тщательной проверке, поскольку он сделан с бисфенолом А (BPA).Исследовательские и правительственные учреждения по всему миру продолжают изучать возможность миграции низких уровней BPA из поликарбонатных изделий (разложение материала при контакте с водой) в продукты питания и напитки. Эти анализы показали, что:
- Потенциальное воздействие на человека бисфенола-А из ПК-продуктов, контактирующих с пищевыми продуктами и напитками, невелико.
- Они не представляют известного риска для здоровья человека.
Несколько регулирующих органов по всему миру: Управление по санитарному надзору за качеством пищевых продуктов и медикаментов США, Научный комитет Европейской комиссии по пищевым продуктам и Агентство по пищевым стандартам Великобритании.

Можно ли перерабатывать ПК?
Можно ли перерабатывать ПК?
Все приложения, сделанные для поликарбонатного пластика, на 100% подлежат вторичной переработке и обозначаются кодом переработки «7». Одним из методов является химическая переработка, при которой лом ПК вступает в реакцию с фенолом с получением мономеров, которые очищаются для дальнейшей полимеризации.Исследователи также работают над разработкой новых процессов переработки поликарбонатов в другой тип пластика, который не выделяет бисфенол А (БФА) в окружающую среду, когда он используется или выбрасывается на свалку.
Каковы разработки в области поликарбоната на биологической основе?
Каковы разработки в области поликарбоната на биологической основе?
Многие компании разработали поликарбонат на биологической основе.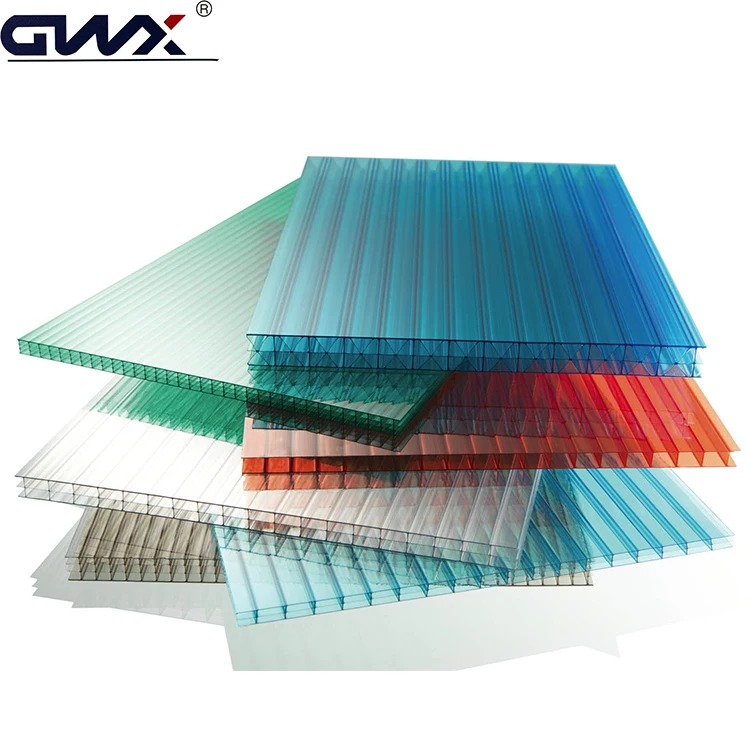
За последние несколько лет в этом сегменте было замечено несколько новых разработок. Среди них:
DURABIO™ от Mitsubishi Chemical Corporation — это инженерный пластик на биологической основе. Он изготовлен из мономера изосорбида растительного происхождения. Его прозрачность и оптическая однородность превосходят таковые у обычной поликарбонатной смолы на основе BPA.
POLYSORB® Isosorbide от Roquette — это раствор на растительной основе, альтернативный BPA. Он может быть использован в качестве мономера в синтезе поликарбоната. Поликарбонаты на основе изосорбида могут использоваться для обеспечения повышенной химической стойкости, устойчивости к ультрафиолетовому излучению и царапинам, в частности, в строительной и автомобильной промышленности.