Какую температуру выдерживает эпоксидная смола после застывания
На чтение 4 мин. Опубликовано
Без эпоксидных смол уже трудно представить современную промышленность и даже высокотехнологичное производство. А это значит, что с такими субстанциями порой приходится работать в достаточно жестких условиях. Например, встречаются следующие факторы: повышенный радиоактивный фон, воздействия агрессивных сред, химических реагентов и температурных скачков. А есть ли температура плавления эпоксидной смолы, ведь после полимеризации она превращается в жесткий и особо прочный материал — об этом в статье.
Технические характеристики эпоксидной смолы
Прежде чем выяснять, какую температуру выдерживает эпоксидная смола после застывания, стоит узнать об основных технических параметрах данной субстанции. Это следующие характеристики:
- полный процесс полимеризации происходит в течение 24–36 часов;
- ускорить процедуру отвердевания смолы можно путем увеличения температурного режима до +70⁰С;
- в условиях пониженных температур (до +15⁰С) время отвердевания смолистой субстанции понижается;
- при затвердевании эпоксидка не дает усадку и не расширяется;
- после отвердевания смолу можно подвергать любым обработкам: шлифовке, полировке, сверлению, обточке, окраске и пр.;
- рекомендованная температура эксплуатации эпоксидной смолы установлена в пределах от -50⁰С до +150⁰С;
- предельно допустимый температурный режим при эксплуатации составляет до +80⁰С;
- отвердевший материал показывает отличные показатели по устойчивости к агрессивным воздействиям, в том числе щелочам, растворителям и повышенной влажности.

Эпоксидная смола обладает ограниченным сроком хранения. Она должна быть использована не позднее 1,5 года с момента ее выпуска.
Температурный режим плавления вещества
По техрегламенту установлено, что температура, при которой происходит плавление эпоксидки, составляет +155⁰С. Но, учитывая заявленные технические характеристики, говорить о том, что эпоксидка станет плавиться, сложно. Даже термостойкий эпоксидный клей или привычная для бытовых работ эпоксидка ЭД-20 после полимеризации даже в условиях сверхвысоких температур будут вести себя следующим образом:
- растрескиваться;
- пениться;
- менять свою структуру, не переходя в жидкое состояние (крошиться и ломаться).
Некоторые смолы (в зависимости от типа используемого отвердителя) могут загораться, причем выделяя большое количество копоти. Процесс горения продолжится до момента тепловой подпитки (например, в условиях открытого пламени). Как только источник огня будет ликвидирован, застывшая смола гореть перестанет.
Несмотря на способность смолы гореть, такое вещество не относится к материалам повышенной пожароопасности.
Даже при горении эпоксидка намного безопаснее многих иных искусственных веществ. Например, пенопласта или вспененного полистирола. Поэтому говорить о том, какую температуру выдерживает эпоксидный клей до момента плавления, не имеет смысла. Практически всегда отвердевшая эпоксидка не плавится, а разрушается, превращаясь в обугленную бесформенную массу.
Есть ли быстрозастывающие смолы
Все эпоксидки подразделяются на две крупные группы. Это конструкционные смолы и декоративные (или ювелирные). Декоративные эпоксидные субстанции отличаются прозрачностью и более быстрым временем полимеризации. Используются они в основном для дизайнерских работ для изготовления сувенирной продукции.

Допустимая температура эксплуатации готовых изделий
Техническими регламентами приняты определенные нормы эксплуатации изделий и отремонтированных вещей, при работе с которыми использовалась эпоксидная смола. Это следующие показатели:- постоянная температура: от -40⁰С до +120⁰С;
- предельно допустимая: от -40⁰С до +150⁰С.
Но некоторые марки эпоксидок, по оценкам производителей, обладают иными показателями. Например, такими экстремальными (предельно допустимыми) показателями:
- эпоксидный клей марки ПЭО-490К (ЛЗОС, г.Лыткарино): +350⁰С;
- эпоксидка ПЭО-13К (ЛЮМЭКС, г.Санкт-Петербург): +196⁰С;
- компаунд ПЭО-28М (ПЛАНЕТ, г.Великий Новгород): +130⁰С.
Подобные эпоксидные субстанции являются специфическими. Многие профессионалы относят их даже не к эпоксидным, а к эпоксиднокремнийорганическим. Дополнительное включение кремния и создает повышенную устойчивость субстанций к тепловому воздействию.
Полезные советы при работе с эпоксидкой
Температурный режим – один из важных и основополагающих факторов при работе с эпоксидными смолами. Поэтому при использовании смолистой субстанции обязательно следует придерживаться рекомендованных условий. В идеале, в помещении, где происходит процесс полимеризации и заливка эпоксидки, температура должна быть в пределах +24⁰–30⁰С. Следует придерживаться и иных рекомендаций:
- в рабочем помещении должно быть не только тепло, но и сухо;
- ингредиенты до момента смешивания (смолы и отвердитель) находятся в герметично закрытой упаковке;
- при замешивании смеси в смолу добавляется отвердитель, а не наоборот;
- при добавлении катализатора эпоксидку можно немного разогреть до +40⁰–50⁰С;
- стандартное время первой полимеризации смолистой субстанции — 1 сутки при температуре в +24⁰С;
- период набора максимальной прочности составляет до недели;
- при смешивании слишком больших доз смолы и отвердителя, эпоксидка может закипеть и потерять свои рабочие свойства.
Выводы
Эпоксидные смолы – популярный и удобный материал для работы. Но следует понимать разницу между промышленными составами и ювелирной эпоксидкой. При замешивании смолистой субстанции строго придерживайтесь инструкции и не выполняйте все рекомендации специалистов.
Температура плавления и эксплуатации эпоксидной смолы, клея
Эпоксидным смолам, без использования которых трудно представить себе современное высокотехнологическое производство, часто приходится работать в очень жестких условиях. Это и повышенная радиация, и воздействие на изделия из эпоксидок химических реагентов, и широчайший диапазон температур, от минус 30 до 200°C градусов. Притом имеется в виду не разовое экстремальное понижение или повышение до указанных пределов, а постоянное воздействие таких температур на связывающий материал.
Нет нужды говорить, что бытовой клей ЭДП или смола ЭД-20, ЭД-22 для подобных температурных перепадов не годятся. Уже полностью отвержденные, они начнут сначала трескаться, потом, в зависимости от применимого когда-то отвердителя, вспенятся, не переходя в жидкую фазу, и начнут разрушаться на мелкие фракции, меняя цвет и структуру.
Могут и загореться, опять-таки в зависимости от исходных веществ и в каком виде были полимеризованы, в виде тонкого покрытия или монолита, занимающего определенный и большой объем в пространстве. Тонкая эпоксидная пленка может воспламениться с выделением огромного количества копоти, если она напрямую контактирует с открытым пламенем. Но горение будет продолжаться только до того момента, пока сохраняется такой контакт и идет интенсивная подпитка теплом. Уберите пламя от эпоксидной пленки, и она тут же погаснет.
Поэтому говорить о пожароопасности использования эпоксидных компаундов в быту или при ремонте не стоит. Горят они не лучше других искусственных материалов, и уж намного безопаснее того же вспененного полистирола или пенопласта, вспомните хотя бы ночной клуб «Белая лошадь» с его многочисленным жертвами от продуктов горения потолочной плитки, с выделением при этом фосгена.
Поэтому говорить о какой-то температуре плавления застывшей эпоксидной смолы нет смысла, в подавляющем большинстве случаев она не плавится, а просто разрушается, превращаясь в бесструктурную обугленную массу.
Огнеупорные смолы
Существуют огнеупорные смолы, это, в первую очередь, безгалогенные KDP-555MC80, KDP-540MC75, KDP-550MC65. Первые цифры в индексе после буквосочетания KDP означают критическую температуру, которую может выдержать эта смола, при ее использования в качестве связывающего каких-нибудь композитов. Основная область применения таких огнеупорных смол – авиационная и космическая промышленности, где материалы, сделанные с использованием KDP, применяются в изготовление внешних контуров крыльев, обтекателей, выдерживающих большие динамические нагрузки управляющих полетом стабилизаторов, элеронов и лонжеронов.
Немалую долю в огнестойкость таких материалов вносят углепластики, которые способны выдержать и кратно высокие температуры. Но сама основа приобретает огнеупорные свойства, в первую очередь, из-за вносимых в нее в процессе полимеризации добавок в виде элементоорганических соединений. В первую очередь – кремнийорганики.
Во время модификации эпоксидной смолы этими элементами происходит изменение многих свойств такой смолы, и часто весьма существенное. Изменения не проходят даром, при сохранении главного параметра в виде термостойкости требуется обычно еще какой-нибудь один. Например, сохранение некоторой пластичности или стабильности свойств смолы как диэлектрика, притом в широком температурном диапазоне. Обычно этого добиваются включением в полимерную цепочку ациклических диэпоксидов вместо основы диановых смол, но тогда увеличивается хрупкость изделий из такой смолы.
Обычно, чем больше числовой индекс у эпоксидных смол (ЭД 16, 20, 22) тем вернее под воздействием запредельно-высоких температур состоится переход застывшей, полимеризированной формы смолы сразу в деструктивно-кристаллическое состояние, с предварительным растрескиванием монолита. Перехода в какое-то жидкое агрегатное состояние в поведении смолы не предусмотрено. Возможно разве что некоторое предварительное размягчение, смолы деформируются.
Более стойким к воздействию высоких температур оказываются смолы с числовыми индексами ЭД-6 и ЭД-15. При воздействии относительно низких температур в пределах 200-250°C градусов изделия из такой смолы начинают выделять газообразные продукты и бесцветную вязкую жидкость. Это следствие процессов, обратных полимеризации, которая происходила при отверждении продукта. О полноценной обратной реакции речи, конечно, не идет, процессы деструкции преобладают над «расшивкой» молекул, а указанная температура в ее верхнем пределе является критической и предраспадной. При длительности ее воздействия более часа, а тем более при ее повышении, процессы распада эпоксидных компонентов делаются необратимыми, с резким падением всех присущих материалу свойств.
Самые термостойкие материалы эпоксидного ряда получают синтезом фторированных дифенилолпропанов. Эти вещества играют роль скрытых, или латентных отвердителей, химически-нейтральных к смоле при комнатной температуре, но начинающими активно работать на полимеризацию смолы при воздействии на нее температуры в 100°C и более градусов, когда начинают меняться ее химические и физические свойства. К ним относят дициандиамид, меломин, изофталилдигидразид.
Именно изделия из этих эпоксидных смол, с введенными в них пластификаторами кремнийорганического ряда, ставятся в качестве головок обтекателей у выводимых на орбиту кораблей, пускаются на армированные углепластиком элементы динамического управления ракетоносителями и сверхзвуковыми самолетами.
В перспективе разработка элементов силового каркаса элементов управления гиперзвуковыми аппаратами. Верхний предел температуры для них превышает на настоящий момент 550°C градусов. Хотя этого, конечно, мало, но и химики не стоят на месте, разрабатываются новые методы усовершенствования физических свойств олигомеров. Перспективным представляется направление с введением в состав эпоксидных полимеров мелкодисперсных порошков из тугоплавких металлов или их карбидов, например, карбида вольфрама.
Обычные составы
Впрочем, описываемые смолы сложны в производстве, требуют специальных боксов-реакторов для отверждения, огнеупорных форм, в которых делаются эти отливки, так что массовому потребителю они малоинтересны, да еще и чрезвычайно дороги. Более интересны для него были бы обычные смолы класса ЭД или его аналогов, в которых для отверждения использовались нестандартные вещества, да еще с введением в них наполнителей пластификаторов, повышающих термостойкость.
Наибольший спрос на жаропрочные материалы из эпоксидных смол отмечается у авто- и мотолюбителей. Камнем преткновения у которых чаще всего выступают компоненты соединений в глушителях, которые быстро выгорают. Вот здесь жаростойкость изделий из эпоксидки или материалов с нею может быть усилена применением армирования прокладок углепластиком или даже самым обыкновенным стеклопластиком.
С введением в застывающую смолу в местах соединения или прокладок дополнительного армирующего и цементирующего элемента в виде мелкодисперсных стальных опилок или даже алюминиевой пудры, которая в связке со смолой отлично держит температуру до 340°C градусов. Правда, страдает ударная прочность такой смолы.
Смолы с наполнителями, а тем более армированные, и подавно не поддаются плавлению. Речь может идти только о постепенном их обугливании и разрушении.
Если же говорить о полноценном плавлении эпоксидных материалов при воздействии высокой температуры, то оно возможно только с попеременным воздействием на них быстродействующих едких растворителей и высокой температуры. Тогда, наряду с физическими изменениями в кристаллической решетке полимера будет происходить и химическое ослабление межмолекулярных связей.
Очевидно, что температура эксплуатации эпоксидной смолы имеет широкий диапазон. Здесь все зависит от полимерного состава и добавок, внесенных в него.
Какую температуру выдерживает эпоксидная смола?
Для получения качественного материала, обладающего высокой прочностью и другими полезными качествами, эпоксидная смола подвергается расплавлению. Для этого необходимо знать, какая температура плавления этой субстанции является оптимальной. Кроме того, важными являются и другие условия, необходимые для правильного отвержения эпоксидки.
Предельная температура эксплуатации
Безусловно, температура влияет на рабочее состояние и правильное застывание эпоксидной смолы, но, чтобы понять, какая температура является максимальной для эксплуатации вещества, стоит ознакомиться с её главными техническими характеристиками.
- Полимеризация смолистой субстанции происходит при нагревании поэтапно и занимает от 24 до 36 часов. Полностью этот процесс может завершиться через несколько дней, но его можно ускорить, осуществляя нагрев смолы до температуры +70°С.
- Правильное отвержение позволяет добиться того, что эпоксидка не расширяется, а эффект усадки фактически исключён.
- После того как смола застыла, её можно обрабатывать любым способом – обтачивать, окрашивать, шлифовать, сверлить.
- Высокотемпературная эпоксидная смесь в застывшем состоянии отличается отличными техническими и эксплуатационными свойствами. Она обладает такими важными показателями, как кислотостойкость, устойчивость к высокому уровню влажности, воздействию растворителей и щелочей.
При этом рекомендованной температурой рабочей смолы является режим в пределах от -50°С до +150°С, однако при этом установлена и предельная температура +80°С. Такая разница связана с тем, что эпоксидная субстанция может иметь разные составляющие, соответственно, физические свойства и температуру, при которой она твердеет.
Режим плавления
Многие производственные, высокотехнологичные процессы невозможно представить без применения эпоксидных смол. Исходя из технического регламента плавление смолы, то есть переход вещества из жидкого в твёрдое состояние и наоборот осуществляется при +155°С.
Но в условиях повышенного ионизирующего облучения, воздействия агрессивной химии и чрезмерно высоких температур, достигающих +100… 200°С, используются только определённые составы. Разумеется, речь не идёт о смолах ЭД и клее ЭДП. Такой вид эпоксидных смесей не плавится. Полностью застывшие эти изделия просто разрушаются, проходя стадии растрескивания и перехода в жидкое состояние:
- они могут растрескиваться или вспениваться из-за кипения;
- изменять цвет, внутреннюю структуру;
- становиться хрупкими и крошиться;
- в жидкое состояние эти смолянистые вещества тоже могут не переходить по причине особого состава.
В зависимости от отвердителя некоторые материалы способны воспламеняться, выделяют много копоти, но только при постоянном контакте с открытым огнём. В этой ситуации, вообще, нельзя говорить о температуре плавления смолы, так как она попросту подвергается разрушению, постепенно распадаясь на мелкие составные части.
Сколько выдерживает после застывания?
Конструкции, материалы и изделия, созданные с применением эпоксидной смолы, изначально сориентированы на стандарты температур, установленные согласно принятым нормам эксплуатации:
- постоянной считается температура от –40°С до +120°С;
- максимальной температурой является +150°С.
Но такие требования относятся не ко всем маркам смол. Для специфических категорий эпоксидных субстанций существуют свои экстремальные нормы:
- заливочный эпоксидный компаунд ПЭО-28М – +130°С;
- высокотемпературный клей ПЭО-490К – +350°С;
- оптический клей на эпоксидной основе ПЭО-13К – +196°С.
Подобные составы за счёт содержания в них дополнительных компонентов, таких как кремний и другие органические элементы, приобретают улучшенные характеристики. Добавки введены в их состав совсем не случайно – они увеличивают стойкость смол к термическому воздействию, разумеется, после того как смола застывает. Но не только – это могут быть полезные диэлектрические свойства или хорошая пластичность.
Повышенной устойчивостью к высоким температурам обладают эпоксидные субстанции марок ЭД-6 и ЭД-15 – они выдерживают до +250°С. Но самыми термостойкими признаны смолистые вещества, полученные с применением меламина и дициандиамида – отвердителей, способных вызывать полимеризацию уже при +100°С. Изделия, при создании которых применены эти смолы, отличаются повышенными эксплуатационными качествами – они нашли применение в военной и космической промышленности. Сложно представить, но предельная температура, которая не способна их разрушить, превышает +550°С.
Рекомендации при работе
Соблюдение температурного режима – главное условие при эксплуатации эпоксидных составов. В помещении тоже должен поддерживаться определённый климат (не ниже +24°С и не выше +30°С).
Рассмотрим дополнительные требования для работы с материалом.
- Герметичность упаковки компонентов – эпоксидки и отвердителя – вплоть до процесса их смешивания.
- Неукоснительным должен быть порядок замешивания – именно отвердитель добавляется в смоляную субстанцию.
- Если используется катализатор, смолу необходимо нагреть до +40.50°С.
- В помещении, где проводятся работы, важен не только контроль над температурой и её стабильностью, но и за тем, чтобы в нём сохранялась минимальная влажность – не больше 50%.
- Несмотря на то что первый этап полимеризации составляет 24 часа при температурном режиме +24°С, предельную прочность материал набирает в течение 6-7 дней. Однако именно в первые сутки важно, чтобы температурный режим и влажность сохранялись в неизменном состоянии, поэтому нельзя допускать малейших колебаний и перепадов этих показателей.
- Не стоит замешивать слишком большие порции отвердителя и смолы. В этом случае есть риск её закипания и утраты свойств, необходимых для эксплуатации.
- Если работа с эпоксидной смолой совпала с холодным временем года, нужно заранее прогреть рабочее помещение, поместив туда упаковки с эпоксидкой, чтобы она также приобрела нужную температуру. Холодный состав допускается подогреть, используя водяную баню.
Нельзя забывать, что в холодном состоянии смола становится мутной по причине формирования в ней микроскопических пузырей, а избавиться от них крайне трудно. К тому же субстанция может не застывать, оставаясь вязкой и липкой. При температурных перепадах также можно столкнуться с такой неприятностью, как «апельсиновая корка» – неровная поверхность с волнами, буграми и углублениями.
Однако следуя этим рекомендациям, соблюдая все необходимые требования, можно получить безупречно ровную, качественную поверхность смолы благодаря её правильному отвержению.
В следующем видео рассказывается о секретах эксплуатации эпоксидной смолы.
При какой температуре плавится эпоксидная смола?
Температура застывания эпоксидной смолы
Какую температуру выдерживает эпоксидная смола после застывания
Эпоксидным смолам, без использования которых трудно представить себе современное высокотехнологическое производство, часто приходится работать в очень жестких условиях. Это и повышенная радиация, и воздействие на изделия из эпоксидок химических реагентов, и широчайший диапазон температур, от минус 30 до 200°C градусов. Притом имеется в виду не разовое экстремальное понижение или повышение до указанных пределов, а постоянное воздействие таких температур на связывающий материал.
Нет нужды говорить, что бытовой клей ЭДП или смола ЭД-20, ЭД-22 для подобных температурных перепадов не годятся. Уже полностью отвержденные, они начнут сначала трескаться, потом, в зависимости от применимого когда-то отвердителя, вспенятся, не переходя в жидкую фазу, и начнут разрушаться на мелкие фракции, меняя цвет и структуру.
Могут и загореться, опять-таки в зависимости от исходных веществ и в каком виде были полимеризованы, в виде тонкого покрытия или монолита, занимающего определенный и большой объем в пространстве. Тонкая эпоксидная пленка может воспламениться с выделением огромного количества копоти, если она напрямую контактирует с открытым пламенем. Но горение будет продолжаться только до того момента, пока сохраняется такой контакт и идет интенсивная подпитка теплом. Уберите пламя от эпоксидной пленки, и она тут же погаснет.
Поэтому говорить о пожароопасности использования эпоксидных компаундов в быту или при ремонте не стоит. Горят они не лучше других искусственных материалов, и уж намного безопаснее того же вспененного полистирола или пенопласта, вспомните хотя бы ночной клуб «Белая лошадь» с его многочисленным жертвами от продуктов горения потолочной плитки, с выделением при этом фосгена.
Поэтому говорить о какой-то температуре плавления застывшей эпоксидной смолы нет смысла, в подавляющем большинстве случаев она не плавится, а просто разрушается, превращаясь в бесструктурную обугленную массу.
Огнеупорные смолы
Существуют огнеупорные смолы, это, в первую очередь, безгалогенные KDP-555MC80, KDP-540MC75, KDP-550MC65. Первые цифры в индексе после буквосочетания KDP означают критическую температуру, которую может выдержать эта смола, при ее использования в качестве связывающего каких-нибудь композитов. Основная область применения таких огнеупорных смол – авиационная и космическая промышленности, где материалы, сделанные с использованием KDP, применяются в изготовление внешних контуров крыльев, обтекателей, выдерживающих большие динамические нагрузки управляющих полетом стабилизаторов, элеронов и лонжеронов.
Немалую долю в огнестойкость таких материалов вносят углепластики, которые способны выдержать и кратно высокие температуры. Но сама основа приобретает огнеупорные свойства, в первую очередь, из-за вносимых в нее в процессе полимеризации добавок в виде элементоорганических соединений. В первую очередь – кремнийорганики.
Во время модификации эпоксидной смолы этими элементами происходит изменение многих свойств такой смолы, и часто весьма существенное. Изменения не проходят даром, при сохранении главного параметра в виде термостойкости требуется обычно еще какой-нибудь один. Например, сохранение некоторой пластичности или стабильности свойств смолы как диэлектрика, притом в широком температурном диапазоне. Обычно этого добиваются включением в полимерную цепочку ациклических диэпоксидов вместо основы диановых смол, но тогда увеличивается хрупкость изделий из такой смолы.
Обычно, чем больше числовой индекс у эпоксидных смол (ЭД 16, 20, 22) тем вернее под воздействием запредельно-высоких температур состоится переход застывшей, полимеризированной формы смолы сразу в деструктивно-кристаллическое состояние, с предварительным растрескиванием монолита. Перехода в какое-то жидкое агрегатное состояние в поведении смолы не предусмотрено. Возможно разве что некоторое предварительное размягчение, смолы деформируются.
Более стойким к воздействию высоких температур оказываются смолы с числовыми индексами ЭД-6 и ЭД-15. При воздействии относительно низких температур в пределах 200-250°C градусов изделия из такой смолы начинают выделять газообразные продукты и бесцветную вязкую жидкость. Это следствие процессов, обратных полимеризации, которая происходила при отверждении продукта. О полноценной обратной реакции речи, конечно, не идет, процессы деструкции преобладают над «расшивкой» молекул, а указанная температура в ее верхнем пределе является критической и предраспадной. При длительности ее воздействия более часа, а тем более при ее повышении, процессы распада эпоксидных компонентов делаются необратимыми, с резким падением всех присущих материалу свойств.
Самые термостойкие материалы эпоксидного ряда получают синтезом фторированных дифенилолпропанов. Эти вещества играют роль скрытых, или латентных отвердителей, химически-нейтральных к смоле при комнатной температуре, но начинающими активно работать на полимеризацию смолы при воздействии на нее температуры в 100°C и более градусов, когда начинают меняться ее химические и физические свойства. К ним относят дициандиамид, меломин, изофталилдигидразид.
Именно изделия из этих эпоксидных смол, с введенными в них пластификаторами кремнийорганического ряда, ставятся в качестве головок обтекателей у выводимых на орбиту кораблей, пускаются на армированные углепластиком элементы динамического управления ракетоносителями и сверхзвуковыми самолетами.
В перспективе разработка элементов силового каркаса элементов управления гиперзвуковыми аппаратами. Верхний предел температуры для них превышает на настоящий момент 550°C градусов. Хотя этого, конечно, мало, но и химики не стоят на месте, разрабатываются новые методы усовершенствования физических свойств олигомеров. Перспективным представляется направление с введением в состав эпоксидных полимеров мелкодисперсных порошков из тугоплавких металлов или их карбидов, например, карбида вольфрама.
Обычные составы
Впрочем, описываемые смолы сложны в производстве, требуют специальных боксов-реакторов для отверждения, огнеупорных форм, в которых делаются эти отливки, так что массовому потребителю они малоинтересны, да еще и чрезвычайно дороги. Более интересны для него были бы обычные смолы класса ЭД или его аналогов, в которых для отверждения использовались нестандартные вещества, да еще с введением в них наполнителей пластификаторов, повышающих термостойкость.
Наибольший спрос на жаропрочные материалы из эпоксидных смол отмечается у авто- и мотолюбителей. Камнем преткновения у которых чаще всего выступают компоненты соединений в глушителях, которые быстро выгорают. Вот здесь жаростойкость изделий из эпоксидки или материалов с нею может быть усилена применением армирования прокладок углепластиком или даже самым обыкновенным стеклопластиком.
С введением в застывающую смолу в местах соединения или прокладок дополнительного армирующего и цементирующего элемента в виде мелкодисперсных стальных опилок или даже алюминиевой пудры, которая в связке со смолой отлично держит температуру до 340°C градусов. Правда, страдает ударная прочность такой смолы.
Смолы с наполнителями, а тем более армированные, и подавно не поддаются плавлению. Речь может идти только о постепенном их обугливании и разрушении.
Если же говорить о полноценном плавлении эпоксидных материалов при воздействии высокой температуры, то оно возможно только с попеременным воздействием на них быстродействующих едких растворителей и высокой температуры. Тогда, наряду с физическими изменениями в кристаллической решетке полимера будет происходить и химическое ослабление межмолекулярных связей.
Очевидно, что температура эксплуатации эпоксидной смолы имеет широкий диапазон. Здесь все зависит от полимерного состава и добавок, внесенных в него.
Источник: https://PractEco.ru/tekhnologiya/temperatura-plavleniya-epoksidnoj-smoly.html
Прочнейший клей, который склеит почти все, за исключением капрона, оргстекла, полиэтилена и других непористых эластичных материалов — двухкомпонентная эпоксидная смола. Вещество также применяется в рукоделии, изготовлении мебели, декупаже, авто, творчестве, строительстве. Иначе оно называется компаунд эпоксидный. В свободном виде эпоксидка не применяется, только в сочетании с отвердителем, который дает возможность проявиться после реакции полимеризации ее уникальным свойствам. По этой причине важно знать, как развести эпоксидную смолу правильно.
Как работать с эпоксидной смолой
Для работы с эпоксидной смолой понадобится отвердитель, одноразовый стаканчик, 2 шприца и палочка для перемешивания.
Совет
Вливайте отвердитель в смолу, а не наоборот. Обычно отвердитель имеет жидкую консистенцию и при резком нажатии на шприц может разбрызгиваться, поэтому делаете это осторожно.
Инструкция по применению:
- Возьмите шприц, наберите в него необходимое количество смолы и выпустите в стаканчик. То же самое проделайте с отвердителем. Пропорции смешивания у разных производителей различны, потому перед началом работы внимательно прочитайте инструкцию по применению. Неправильно разведенная эпоксидка плохо застывает.
- Хорошенько перемешайте смолу с отвердителем, масса должна стать однородной. Смешивать необходимо медленно и осторожно, если делать это резкими движениями и быстро, то в массе появятся пузырьки. Жидкая консистенция состава обеспечит быстрый выход пузырьков наружу, в изначально густых компонентах они останутся. Плотность смолы зависит от производителя. Недостаточно хорошо смешанные компоненты обусловят плохое застывание состава.
- Полимеризация не происходит мгновенно, необходимо немного подождать пока масса приобретет требующуюся для работы консистенцию.
- Залейте в форму или сделайте линзу.
- Подождите указанное производителем в инструкции время, пока эпоксидная смола окончательно застынет.
Совет
Во время застывания к массе хорошо прилипают пылинки и разная грязь. Предотвратить это поможет использование емкостей и коробок с крышкой. Сделайте изделие в коробке и закройте крышкой на время затвердевания состава.
Эпоксидная смола имеет условные стадии застывания:
- Вначале масса очень жидкая и легко стекает, что делает ее максимально подходящей для заливки в форму. Жидкая консистенция позволяет эпоксидке проникнуть в мельчайшие углубления, более густому составу это не под силу, и рельеф получится не очень явным.
- По прошествии некоторого времени эпоксидная смола становится гуще и подходит для изготовления выпуклых линз на плоской основе. Сделать подобную линзу из жидкой смолы не удастся — состав будет скатываться вниз с заготовки. На этой стадии лучше всего заливать нерельефные формы в домашних условиях.
- Наименее подходящая консистенция смеси для работы — наподобие густого меда. При набирании эпоксидки на палочку легко формируются пузырьки, убрать которые очень сложно. На этой стадии состав подходит для того, чтобы склеить детали между собой. Эпоксидка характеризуется отличной адгезией и прекрасно прилипает к большинству материалов (на основе этого свойства был разработан клей ЭДП.), но легко отслаивается от полипропилена, полиэтилена, силикона, резины, поверхностей, покрытых пленкой жира.
- Эпоксидная смола становится очень густой и липкой, отделить немного от основной массы проблематично.
- Следующая стадия — резиновая. Эпоксидка не прилипает к рукам, но легко мнется и гнется, из нее получится сделать множество изделий, но если вы хотите, чтобы она затвердела в нужном положении, то закрепите ее, иначе она вернется в первоначальное состояние.
- Окончательно затвердевшая эпоксидная смола. Ее нельзя продавить ногтем, на ощупь она похожа на пластик.
Совет
Если нет формы из специального материала, то смажьте имеющуюся растительным маслом, но сначала проверьте, как отреагирует на него конкретно этот состав эпоксидки.
Эпоксидна смола от разных производителей характеризуется различным временем отвердения. Время наступления стадий определяются исключительно опытным путем. Существует мягкая эпоксидная смола, которая остается резиновой даже после полного застывания, что для некоторых изделий является идеальным вариантом.
Как развести
Разводить пропорции необходимо очень тщательно, так как недостаточное либо избыточное количество отвердителя в смеси отрицательно сказывается на качестве образующегося полимера.
Избыток отвердителя характеризуется тем, что состав остается устойчивым к нагреванию, действию химических веществ и воды, но становится менее прочным. Кроме того, излишек выделяется на поверхности при эксплуатации изделия, поэтому необходимо точно знать, как развести эпоксидную смолу правильно.
Недостаточное количество отвердителя делает смолу липкой, так как ее часть остается несвязанной.
Для получения различных смесей отвердитель и эпоксидная смола смешиваются в различных пропорциях, о чем вы узнаете, прочитав инструкцию по применению. Современный состав обычно делается так: на 1 часть отвержающих компонентов берутся 2 части смолы или отвердитель и смола смешиваются 1 к 1.
На скорость полимеризации оказывают влияние тип отвердителя и температура состава. Чтобы ускорить процесс, слегка нагрейте массу. Повышение температуры на 10° С обеспечит ускорение полимеризации в 3 раза. Существуют составы, которые включают в себя ускорители отвердения, есть и такие, которые застывает при низких температурах.
Эпоксидная смола становится твердой при температуре от —10 до +200° С, что зависит от вида применяемого состава. Чаще всего в быту применяются отвердитель холодного типа, он встречается в условиях маломощного производства и там, где термическая обработка недопустима.
Отвердители горячего типа применяются в процессе получения изделий с высокой прочностью, которые будут подвергаться значительным нагрузкам и действию высоких температур. Горячая полимеризация способствует формированию густой сетки молекул, которая и обеспечивает устойчивость состава.
Полезные советы
Советы и рекомендации профессионалов помогут облегчить работу с эпоксидной смолой и сделать все максимально качественно:
- Перед началом работы застелите стол полиэтиленовой пленкой, чтобы избежать протекания и загрязнения его поверхности. Бумага не защитит от пятен, так как эпоксидка пропитывает ее.
- Не допускайте попадание воды в отвердитель, эпоксидную смолу или смесь этих веществ. Если работать с составом при высокой влажности воздуха в помещении, застывание будет происходить плохо.
- Можете придать эпоксидке любой оттенок. Это делается с помощью добавления в состав специальных тоннеров, но их стоимость сравнительно высока. Более приемлемым по цене вариантом являются чернила гелевых ручек, краска, находящаяся внутри фломастеров, маркеров или витражная.
- Не работайте с эпоксидкой при температуре окружающего воздуха ниже +22° С, так как существует вероятность, что состав плохо застынет.
- Если смолу подержать в холодном помещении, например, на балконе, в ней могут появиться хлопья или крупинки. Чтобы вернуть состав в первоначальное состояние, нагрейте его до 40—60° С.
- Поставив изделие на батарею отопления, вы сократите продолжительность застывания эпоксидной смолы. Обеспечьте не слишком сильное повышение температуры, чтобы состав не закипел с образованием множества пузырьков.
- Если близко к поверхности эпоксидной смолы сформировался пузырек — просто подуйте на него через коктейльную трубочку или раскрученную ручку. Образовавшийся пузырек лопнет.
- Эпоксидка характеризуется повышенной текучестью, по этой причине не применяйте состав в качестве покрытия (лака) для рельефных изделий.
- Сделать качественно линзы на заготовках с плоской поверхностью удастся, только разместив их в идеально горизонтальном положении. В противном случае линзы получатся неровными — с одной стороны выше, с другой — ниже.
- Если линза сползается к центру и не закрывает края заготовки, это говорит о том, что эпоксидки было налито мало или она очень жидкая. Попробуйте залить еще один слой, это позволит исправить положение.
- Чтобы с течением времени эпоксидная смола не пожелтела под действием солнечных лучей и тепла, приобретайте продукт, в составе которого имеется УФ-фильтр.
- При попадании эпоксидки на кожу рук оттирайте загрязнения спиртом, после чего вымойте руки с мылом.
- Если смола попала в глаза или была проглочена — обратитесь к врачу.
Эпоксидные смолы токсичны в большей или меньшей степени, в зависимости от состава. По этой причине работать с ними необходимо в хорошо проветриваемой комнате или под вытяжкой. Полностью обезопасить себя от вдыхания паров органических кислот можно, работая с эпоксидкой в респираторе.
Источник: https://goodklei.ru/vidy/epoksidnaya-smola.html
Сколько сохнет эпоксидная смола, можно ли ускорить этот процесс
Время застывания или засыхания эпоксидного состава, будь то эпоксидка для ювелирных поделок, заливка-покрытие для пола или эпоксидный клей, зависит от многих факторов. Ключевую роль играют возраст состава или сколько лет прошло после выпуска эпоксидного материала заводом-изготовителем, срок годности, соотносимый с датой производства. Среди факторов, влияющих на скорость полимеризации, значимыми величинами будут:
- Состав реактива-отвердителя.
- Количество отвердителя при добавлении в эпоксидную смолу или клей.
- Температура, при которой производится смешивание компонентов и застывание готового состава.
- Площадь заливаемой поверхности или ее объем.
Мнение эксперта Олег Васильев Мастер по изготовлению мебели и предметов интерьера из эпоксидной смолы. Создает уникальные вещи на заказ на своем производстве. Задать вопрос мастеру Нельзя удержаться, чтобы не сказать о том, что термины «сохнет» или «застывает» практически не верны и применяются только для бытового разговора. Смесь эпоксидной смолы и отвердителя проходит стадию отверждения.
О составе отвердителей
Самые массовые реактивы-катализаторы, запускающие механизм полимеризации – это полиэтиленполиамин (ПЭПА) и триэтилентетраамин (ТЭТА). Оба относятся к аминовой группе отвердителей эпоксидной смолы, но действуют несколько по-разному.
ПЭПА принято относить к «холодным» реактивам, это означает, что для нормального, в течение суток, застывания катализатор добавляют в основной состав смолы, замешивают и наносят на какие-то поверхности или отливают в виде объемного изделия при обычной комнатной температуре, в пределах 20-25°C. Изделия или поверхности из такой смолы выдерживают без ущерба для качества температуру до 350-400°C градусов, и только после 450-500°C начнется разрушение застывшего полимера.
При нагревании смеси эпоксидной смолы с полиэтиенполиаминным отвердителем время засыхания рабочего раствора уменьшится, но некоторые эксплуатационные качества готовых застывших поверхностей или объемов могут ухудшиться. В частности, уменьшится сопротивление на разрыв от стекловолокна при его изготовлении, с 9,3-11,0 до меньших величин или разрушающее напряжение при изгибе в Мпа вместо величин 60-100 может стать всего 40, а при растяжении вместо 35-70 – всего в 30.
Триэтилентетраамин ведет себя несколько иначе. Относясь к «горячим» катализаторам застывания эпоксидного состава, у ТЭТА рабочие температуры при длительной эксплуатации в среднем на 100°C градусов выше, чем у ПЭПА, температура начала разрушения при перегреве готовых изделий – 473-480°C, а разрушающее напряжение Мпа на изгиб держится в пределах 90-130, а на растяжение – 70-98.
Для ТЭТА желателен некоторый нагрев готовой смеси, что вызовет ускорение реакции застывания. Чем температура смеси будет ближе к 50°C градусам, тем скорость полимеризации будет выше.
Только нужно иметь в виду, что повышение температуры нагрева для ускорения процесса выше 50°C крайне нежелательно. В больших объемах (иногда этот «большой объем» равен всего 100-150 куб. см) может начаться быстрый саморазогрев готовой эпоксидной смеси, вплоть до закипания, даже задымления.
Поэтому если нужно сделать объемную отливку из эпоксидки с отвердителем ТЭТА, то проводить ее нужно в несколько этапов, заливая объем слоями, и при этом давая каждому предыдущему слою полностью застыть. Хлопотно, тогда воспользуйтесь ПЭПА, у которого коэффициент саморазогрева ниже в разы и можно заливать сразу большой объем.
Поэтому «горячие» катализаторы полимеризации находят большее применение в тех случаях, когда будущие изделия будут подвергаться значительным нагрузкам и воздействию высоких температур. В процессе застывания повышенная температура эпоксидной массы с отвердителем способствует образованию более густой молекулярной сетки с обширным и разветвленными валентными связями, а это и прочность, и жаростойкость, и большее сопротивление на растяжение, изгиб, разрыв и скручивание.
Повышение температуры смеси эпоксидка с отвердителем на 10°C градусов ускоряет застывание такой смеси в 3 раза.
Мнение эксперта Олег Васильев Мастер по изготовлению мебели и предметов интерьера из эпоксидной смолы. Создает уникальные вещи на заказ на своем производстве. Задать вопрос мастеру Но при этом резко возрастает и вероятность «закипания» смеси с образованием пузырьков в толще отвержденной смеси.
Зависимость скорости высыхания от площади заливки
С температурой разобрались, хотя есть еще один интересный нюанс, но и он полностью связан со следующей темой. Иногда смолы с аминовыми отвердителями типа ТЭТА не нуждаются в подогреве, он происходит спонтанно, и связано это с той формой, в которую заливают исходное сырье.
Здесь прослеживается следующая зависимость: чем компактнее форма заливки, то есть чем ближе она по форме к кубу и тем более к шару, тем быстрее и интенсивнее будет происходить процесс саморазогрева, вплоть до закипания и даже задымления, что безусловно может испортить заготовку.
Если эпоксидной смолы с отвердителем взято небольшое количество, то при комнатной температуре 100 г состава полностью полимеризуются уже через 5-6 часов. Но тот же самый объем смолы, разлитый по площади в 100 кв. см, будет застывать уже сутки, то есть в смоле с отвердителем ТЭТА образуется некая критическая масса, зависимая от объема, который занимает такая эпоксидная смесь, и эта критическая масса тем меньше, чем больше занимаемый ею объем стремится к шарообразной форме.
Полная аналогия с плутонием: в форме цилиндра его нужно, предположим, 5 килограммов для начала самопроизвольной цепной реакции деления ядер, а в форме шара всего 2 килограмма. В форме же плоского листа масса металла может быть хоть до центнера, и ничего не произойдет.
Только в случае с эпоксидкой процессы протекают химические, затрагивающие сугубо внешне оболочки атомов вещества и его молекулярные связи, а с делящимися материалами вроде плутония или урана-235 в дело вступает чистая физика, где задействованы уже внутриядерные процессы. Но механизм схож: образование критической массы, зависимой от компактности размещения.
Мнение эксперта Олег Васильев Мастер по изготовлению мебели и предметов интерьера из эпоксидной смолы. Создает уникальные вещи на заказ на своем производстве. Задать вопрос мастеру Речь идет о площади теплоотдачи такой «критической массы». Чем больше площадь, тем меньше разогревается смесь и тем больше время ее отверждения. У шара эта площадь минимальна и, соответственно, разогрев наибольший.
Как смешать компоненты оптимально
От точности отмеривания доз основного эпоксидного компонента зависит время застывания смолы и качество получаемых отливок или покрываемых площадей. Кроме того, большое значение имеет тщательность зачистки обрабатываемых поверхностей или форм для заливки.
В зачистку входит как удаление пыли и предварительное придание некоторой шероховатости обрабатываемой поверхности, но второе не обязательно, так и химическая подготовка стенок емкости для отливок или заливаемых площадей. Обычно это обезжиривание ацетоном или спиртом, нужно только дождаться испарения их частиц перед заливкой эпоксидным составами, иначе и спирт, и ацетон вступят в реакцию затвердения и изменят ей время, ведь они применяются и в качестве пластификаторов уже в готовых застывших изделиях.
Как проводится работа:
- Компоненты эпоксидки тщательно отмеряют. Для этого нужно воспользоваться одноразовым мерным стаканчиками с делениями, пусть даже без оцифровки. Для небольших объемов, где точность может быть критична, лучше применять медицинские шприцы большого объема на 20 или 50 мл.
- Для ускорения процесса застывания (сушки) эпоксидную смолу, пока без отвердителя, подогревают на водяной бане до 40-50°C при постоянном медленном помешивании. Быстро мешать не следует, от этого образуются воздушные пузырьки, которые при быстром протекании процесса могут не успеть выйти на поверхность и так и остаться в толще застывшего полимера.
- Далее следует быстро влить при постоянном помешивании отвердитель, проследить, чтобы смесь получилась однородной.
- Использовать полученный состав в течение не более 30 минут. Если задержитесь, смесь может критически загустеть и не лечь равномерно.
Здесь описывается работа с неким конкретным образцом смолы и отвердителя. В реальности и компоненты разных эпоксидок можно отмерять по весу, а не по объему, и время использования может составлять от указанных 30 минут до нескольких часов. Все зависит от типа и области применения смолы, позиционируемой производителем
Стадии застывания
Смесь эпоксидки и отвердителя не встает вся разом, образования сплошных и сверхдлинных (в молекулярном масштабе) полимерных цепочек во всей массе эпоксидного состава не происходит. Полимеризация идет отдельными фрагментами, которые только потом, со временем, сливаются в единую полимерную массу.
Процесс застывания, загущения и сушки изделия из эпоксидной смолы в смеси с отвердителем проходит несколько стадий:
- Жидкая текучая консистенция, позволяющая за счет этой текучести заполнить малейшие неровности каверны заливаемого материала.
- Загущение смеси до состояния холодного гречишного меда. В таком виде смесь уже неспособна полностью залить поверхности со сложным и ярко выраженным рельефом.
- Густота уже такая, что из опрокинутого сосуда сползает со скоростью не более сантиметра в секунду. Годится только для склеивания крупных деталей.
- Такая густата, что при попытке отделения хоть часть от общей массы за этой частью тянется длинный шлейф смолы, застывающий на глазах.
- «Резиновая стадия», к рукам уже не липнет, можно сгибать, растягивать, перекручивать отливку из состава.
- На ощупь изделие из оргстекла или пластмассы. Твердое, прочное, мало подверженное внешним воздействиям.
Эпоксидная смола — как правильно применять
Прочнейший клей, который склеит почти все, за исключением капрона, оргстекла, полиэтилена и других непористых эластичных материалов — двухкомпонентная эпоксидная смола. Вещество также применяется в рукоделии, изготовлении мебели, декупаже, авто, творчестве, строительстве. Иначе оно называется компаунд эпоксидный. В свободном виде эпоксидка не применяется, только в сочетании с отвердителем, который дает возможность проявиться после реакции полимеризации ее уникальным свойствам. По этой причине важно знать, как развести эпоксидную смолу правильно.
Что такое эпоксидная смола
Эпоксидная смола — это олигомеры, которые содержат эпоксидные группы и при воздействии отвердителей формируют сшитые полимеры. Отвердителями могут быть полиамины и другие соединения. Самыми распространенными эпоксидными смолами являются продукты поликонденсации с бисфенолом А либо поликонденсации с фенолами эпихлоргидрина.
Жидкая эпоксидная смола может быть различных оттенков: от белого, прозрачного, до винно-красного. Но обычно имеет вид желто-оранжевой прозрачной жидкости, по консистенции напоминающей мед, или твердой, коричневой (как гудрон) массы.
Состав
Эпоксидная смола по химическому составу представляет собой синтетическое олигомерное соединение. Подобные вещества на сегодняшний день востребованы практически во всех отраслях промышленности. После соединения эпоксидной смолы с отвердителями получаются:
- прочные и мягкие материалы;
- твердые и жесткие;
- материалы, напоминающие резину.
Эпоксидная смола обладает устойчивостью к воздействию кислот, галогенов, щелочей, но растворяется в ацетоне и сложных эфирах без формирования пленки. После отвердения летучие вещества не выделяются, происходит совсем незначительная усадка состава.
Как работать с эпоксидной смолой
Для работы с эпоксидной смолой понадобится отвердитель, одноразовый стаканчик, 2 шприца и палочка для перемешивания.
Совет
Вливайте отвердитель в смолу, а не наоборот. Обычно отвердитель имеет жидкую консистенцию и при резком нажатии на шприц может разбрызгиваться, поэтому делаете это осторожно.
Инструкция по применению:
- Возьмите шприц, наберите в него необходимое количество смолы и выпустите в стаканчик. То же самое проделайте с отвердителем. Пропорции смешивания у разных производителей различны, потому перед началом работы внимательно прочитайте инструкцию по применению. Неправильно разведенная эпоксидка плохо застывает.
- Хорошенько перемешайте смолу с отвердителем, масса должна стать однородной. Смешивать необходимо медленно и осторожно, если делать это резкими движениями и быстро, то в массе появятся пузырьки. Жидкая консистенция состава обеспечит быстрый выход пузырьков наружу, в изначально густых компонентах они останутся. Плотность смолы зависит от производителя. Недостаточно хорошо смешанные компоненты обусловят плохое застывание состава.
- Полимеризация не происходит мгновенно, необходимо немного подождать пока масса приобретет требующуюся для работы консистенцию.
- Залейте в форму или сделайте линзу.
- Подождите указанное производителем в инструкции время, пока эпоксидная смола окончательно застынет.
Совет
Во время застывания к массе хорошо прилипают пылинки и разная грязь. Предотвратить это поможет использование емкостей и коробок с крышкой. Сделайте изделие в коробке и закройте крышкой на время затвердевания состава.
Эпоксидная смола имеет условные стадии застывания:
- Вначале масса очень жидкая и легко стекает, что делает ее максимально подходящей для заливки в форму. Жидкая консистенция позволяет эпоксидке проникнуть в мельчайшие углубления, более густому составу это не под силу, и рельеф получится не очень явным.
- По прошествии некоторого времени эпоксидная смола становится гуще и подходит для изготовления выпуклых линз на плоской основе. Сделать подобную линзу из жидкой смолы не удастся — состав будет скатываться вниз с заготовки. На этой стадии лучше всего заливать нерельефные формы в домашних условиях.
- Наименее подходящая консистенция смеси для работы — наподобие густого меда. При набирании эпоксидки на палочку легко формируются пузырьки, убрать которые очень сложно. На этой стадии состав подходит для того, чтобы склеить детали между собой. Эпоксидка характеризуется отличной адгезией и прекрасно прилипает к большинству материалов (на основе этого свойства был разработан клей ЭДП.), но легко отслаивается от полипропилена, полиэтилена, силикона, резины, поверхностей, покрытых пленкой жира.
- Эпоксидная смола становится очень густой и липкой, отделить немного от основной массы проблематично.
- Следующая стадия — резиновая. Эпоксидка не прилипает к рукам, но легко мнется и гнется, из нее получится сделать множество изделий, но если вы хотите, чтобы она затвердела в нужном положении, то закрепите ее, иначе она вернется в первоначальное состояние.
- Окончательно затвердевшая эпоксидная смола. Ее нельзя продавить ногтем, на ощупь она похожа на пластик.
Совет
Если нет формы из специального материала, то смажьте имеющуюся растительным маслом, но сначала проверьте, как отреагирует на него конкретно этот состав эпоксидки.
Эпоксидна смола от разных производителей характеризуется различным временем отвердения. Время наступления стадий определяются исключительно опытным путем. Существует мягкая эпоксидная смола, которая остается резиновой даже после полного застывания, что для некоторых изделий является идеальным вариантом.
Как развести
Разводить пропорции необходимо очень тщательно, так как недостаточное либо избыточное количество отвердителя в смеси отрицательно сказывается на качестве образующегося полимера.
Избыток отвердителя характеризуется тем, что состав остается устойчивым к нагреванию, действию химических веществ и воды, но становится менее прочным. Кроме того, излишек выделяется на поверхности при эксплуатации изделия, поэтому необходимо точно знать, как развести эпоксидную смолу правильно.
Недостаточное количество отвердителя делает смолу липкой, так как ее часть остается несвязанной.
Для получения различных смесей отвердитель и эпоксидная смола смешиваются в различных пропорциях, о чем вы узнаете, прочитав инструкцию по применению. Современный состав обычно делается так: на 1 часть отвержающих компонентов берутся 2 части смолы или отвердитель и смола смешиваются 1 к 1.
На скорость полимеризации оказывают влияние тип отвердителя и температура состава. Чтобы ускорить процесс, слегка нагрейте массу. Повышение температуры на 10° С обеспечит ускорение полимеризации в 3 раза. Существуют составы, которые включают в себя ускорители отвердения, есть и такие, которые застывает при низких температурах.
Эпоксидная смола становится твердой при температуре от —10 до +200° С, что зависит от вида применяемого состава. Чаще всего в быту применяются отвердитель холодного типа, он встречается в условиях маломощного производства и там, где термическая обработка недопустима.
Отвердители горячего типа применяются в процессе получения изделий с высокой прочностью, которые будут подвергаться значительным нагрузкам и действию высоких температур. Горячая полимеризация способствует формированию густой сетки молекул, которая и обеспечивает устойчивость состава.
Расход на 1м2
Сколько будет израсходовано эпоксидной смолы, зависит от цели ее применения. Если воспользоваться эпоксидкой как клеем, то на расход повлияют свойства соединяемых поверхностей:
- пористость;
- шероховатость;
- способность впитывать вещества.
Совет
Нанесите минимально приемлемое количество эпоксидки на склеиваемые поверхности, затем прижмите их друг к другу и зафиксируйте в таком положении до полного застывания клея.
Расход на площадь имеет большое значение при изготовлении, например, напольного покрытия. Если необходимо покрыть бетонный гладкий пол, просто чтобы он не пылил, то достаточно будет 100 г на 1 м2. При изготовлении более прочного покрытия, армированного и идеально ровного потребуется до 3,5 кг эпоксидной смолы на 1 м2.
Модифицированные эпоксидки различных оттенков применяются при устройстве полимерных наливных полов. Полимер выливается из емкости на пол и растекается благодаря силе тяжести. Подобное нанесение обуславливает расход от 1 кг эпоксидки на 1м2 на один слой.
Сколько сохнет
Полное застывание эпоксидки обычно происходит через 24 часа. Изделия (например, броши, заколки), которые не подвергаются значительным нагрузкам, готовы к эксплуатации уже через 12 часов.
Какую температуру выдерживает
Температура плавления застывшей эпоксидной смолы составляет до +150—180° С, при этом ее прочность уменьшится незначительно. Некоторые марки клея выдерживают кратковременный нагрев до +400° С и продолжительный — до +250° С.
Вредна ли для здоровья
После застывания эпоксидная смола при нормальных условиях эксплуатации абсолютно безвредна для человеческого организма. Но ее применение ограничивается тем, что при отвердении в условиях промышленного производства в составе остается немного растворимого остатка (золь-фракции). Именно этот остаток может нанести серьезный ущерб здоровью, если будет вымыт растворителями и проникнет в организм человека. Эпоксидные смолы до застывания ядовиты и способны отрицательно повлиять на здоровье.
Полезные советы
Советы и рекомендации профессионалов помогут облегчить работу с эпоксидной смолой и сделать все максимально качественно:
- Перед началом работы застелите стол полиэтиленовой пленкой, чтобы избежать протекания и загрязнения его поверхности. Бумага не защитит от пятен, так как эпоксидка пропитывает ее.
- Не допускайте попадание воды в отвердитель, эпоксидную смолу или смесь этих веществ. Если работать с составом при высокой влажности воздуха в помещении, застывание будет происходить плохо.
- Можете придать эпоксидке любой оттенок. Это делается с помощью добавления в состав специальных тоннеров, но их стоимость сравнительно высока. Более приемлемым по цене вариантом являются чернила гелевых ручек, краска, находящаяся внутри фломастеров, маркеров или витражная.
- Не работайте с эпоксидкой при температуре окружающего воздуха ниже +22° С, так как существует вероятность, что состав плохо застынет.
- Если смолу подержать в холодном помещении, например, на балконе, в ней могут появиться хлопья или крупинки. Чтобы вернуть состав в первоначальное состояние, нагрейте его до 40—60° С.
- Поставив изделие на батарею отопления, вы сократите продолжительность застывания эпоксидной смолы. Обеспечьте не слишком сильное повышение температуры, чтобы состав не закипел с образованием множества пузырьков.
- Если близко к поверхности эпоксидной смолы сформировался пузырек — просто подуйте на него через коктейльную трубочку или раскрученную ручку. Образовавшийся пузырек лопнет.
- Эпоксидка характеризуется повышенной текучестью, по этой причине не применяйте состав в качестве покрытия (лака) для рельефных изделий.
- Сделать качественно линзы на заготовках с плоской поверхностью удастся, только разместив их в идеально горизонтальном положении. В противном случае линзы получатся неровными — с одной стороны выше, с другой — ниже.
- Если линза сползается к центру и не закрывает края заготовки, это говорит о том, что эпоксидки было налито мало или она очень жидкая. Попробуйте залить еще один слой, это позволит исправить положение.
- Чтобы с течением времени эпоксидная смола не пожелтела под действием солнечных лучей и тепла, приобретайте продукт, в составе которого имеется УФ-фильтр.
- При попадании эпоксидки на кожу рук оттирайте загрязнения спиртом, после чего вымойте руки с мылом.
- Если смола попала в глаза или была проглочена — обратитесь к врачу.
Эпоксидные смолы токсичны в большей или меньшей степени, в зависимости от состава. По этой причине работать с ними необходимо в хорошо проветриваемой комнате или под вытяжкой. Полностью обезопасить себя от вдыхания паров органических кислот можно, работая с эпоксидкой в респираторе.
характеристики, температура применения, срок годности и отзывы
Эпоксидные смолы изготавливаются и применяются у нас в стране уже больше 60 лет. Использоваться такие материалы могут как в промышленности, так и в быту. Разновидностей таких средств на рынке сегодня имеется множество. К примеру, очень неплохие отзывы от потребителей заслужила эпоксидная смола ЭД-20. Характеристиками этот материал, как рабочими, так и эксплуатационными, отличается достаточно хорошими.
Форма выпуска
Представляет собой ЭД-20 плавкий и растворимый пластичный материал, являющийся продуктом конденсации дифенилпропана и эпихлоргидрина в щелочных средах. Имеется сегодня на рынке и раствор такой смолы в толуоле. Поставляется этот материал на промышленные объекты в стальных барабанах на 53 кг или флягах. Для бытовых целей эта смола расфасовывается в обычные флаконы. Внешне это средство представляет собой медоподобную вязкую прозрачную жидкость.
Поставляется на рынок ЭД-20 как двухкомпонентный состав. В качестве отвердителя для этого средства используются стандартные материалы. Это могут быть, к примеру, предназначенные для эпоксидных смол ТЭТА, ПЭПА и пр. В твердом виде этот материал является диэлектриком и отличается стойкостью к разного рода растворителям.
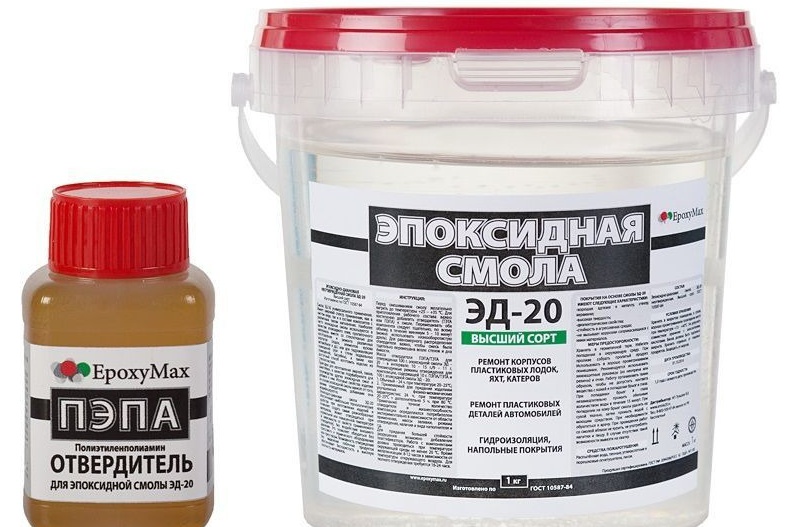
Состав по ГОСТ
Характеристики эпоксидной смолы ЭД-20, как и любого другого подобного материала, определяются, конечно же, в первую очередь ее составом. Согласно действующим нормативам, ЭД-20 должна содержать:
массовую долю эпоксидных групп — не более 20-22,5 %;
омыляемого хлора — 0,3-0,8 %;
иона хлора — 0,001-0,005 %;
гидроксильных групп — 1,7 %;
летучих веществ — 0,2-0,8 %.
Средняя многочисленная доля эпоксидных групп в этом материале равна 20 %, что отражено в его названии.
Производитель и срок хранения
Поставляет на рынок стран постсоветского пространства и за рубеж это средство ФПК «Завод им. Свердлова». Основано это предприятие было еще до революции — в 1916 г. В настоящий момент оно относится к объектам оборонного комплекса. Головной офис компании находится в г. Дзержинске. Также эту смолу выпускают и некоторые другие заводы на территории постсоветского пространства.
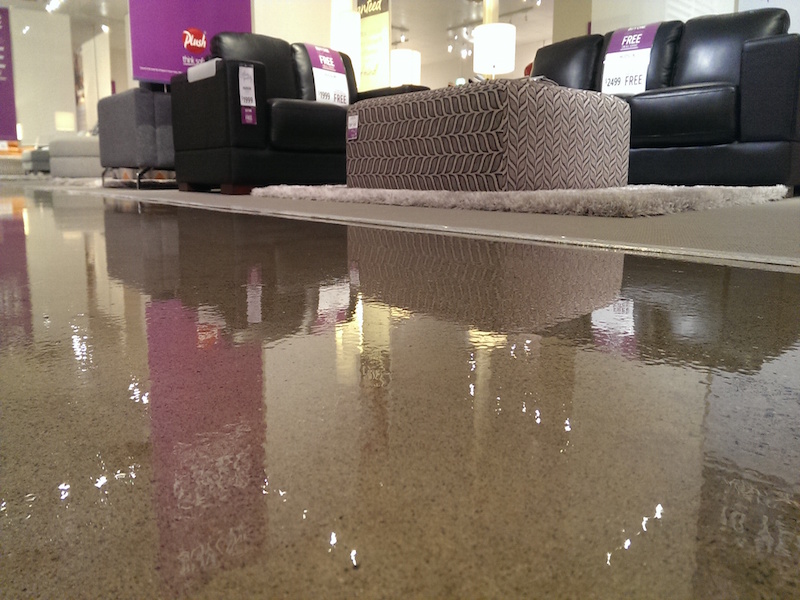
Гарантийный срок хранения этого материала составляет 18 месяцев со дня изготовления. Отвердитель ЭД-20 может при этом не терять свои свойства с даты выпуска в течение 2 лет. Храниться этот материал должен в темном месте при температуре не выше 40 °С.
Технические характеристики эпоксидной смолы ЭД-20
Одной из особенностей этого средства является неэластичность. Никаких пластификаторов в такую смолу при изготовлении не добавляется. При движении поверхностей под отвердевшим слоем этого материала на нем могут появиться трещины.
Вязкость у этой смолы в рабочем состоянии достаточно высокая. Поэтому очень часто ее перед использованием разбавляют растворителями.
Помимо этого, эпоксидная смола ЭД-20 отличается следующими характеристиками:
время полимеризации — 1,5 часа;
время полного застывания — 1 сутки;
ударная вязкость — 5-25 кдж/м2;
теплостойкость — 55-170 °С;
прочность при изгибе — 80-140 МПа;
плотность при 20 °С — 1,16-1,25 кг/м3.
Вот такие имеет эпоксидная смола ЭД-20 характеристики. Температура применения этого материала минимальная равна 20 °С. Такой способ использования называется холодным. В промышленных условиях затвердевание этого материала может происходить и при очень высоких температурах. Это так называемый горячий способ полимеризации.
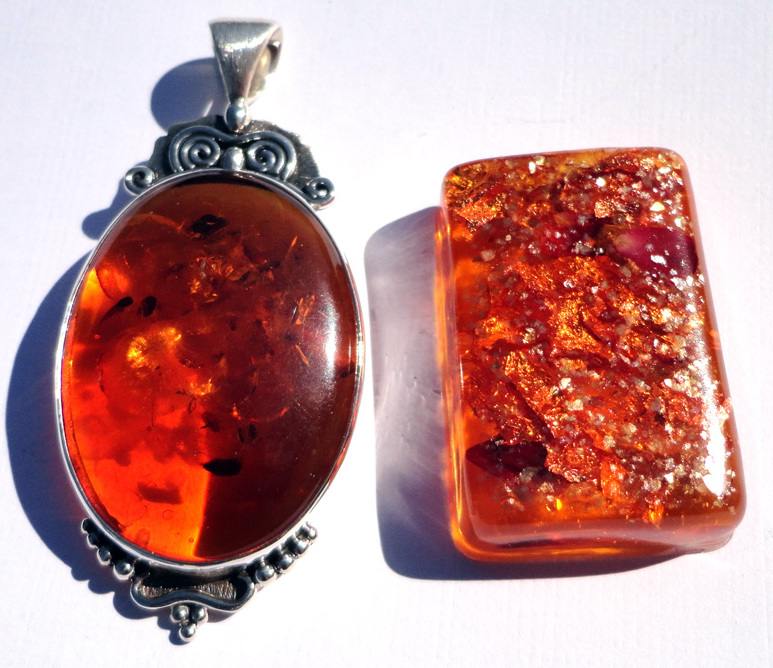
Традиционные сферы применения
Усадку при использовании ЭД-20 дает очень небольшую. К тому же, как мы выяснили, полимеризуется это средство достаточно быстро. Благодаря таким свойствам применение этот материал нашел очень широкое как в промышленности, так и в строительстве или быту. Использоваться смола ЭД-20, технические характеристики которой делают это средство практически универсальным, может, к примеру:
в приборостроении;
в авиапромышленности;
мебельной промышленности;
при ремонте элементов конструкции автомобилей;
в радиотехнической промышленности.
Очень широко этот материал применяется и дизайнерами. Из него могут создаваться, к примеру, столешницы, галантерейные изделия, разного рода влагостойкие товары, предназначенные для использования в ванных комнатах. Применяется эпоксидка и для грунтования разного рода поверхностей.
Еще одной областью использования ЭД-20 является изготовление эмалей, лаков, шпаклевок. Также с применением этого материала делают и эпоксидные смолы других марок. В быту этот материал часто используется в качестве клея. С его применением допускается скреплять как дерево, так и металл, пластик, керамику, стекло.
Где еще может использоваться
Технические характеристики эпоксидная смола марки ЭД-20, таким образом, имеет очень даже неплохие. Поэтому она нашла свое применение в том числе и при производстве разного рода современных материалов. К примеру, достаточно часто это средство используется для пропитки стеклотканей и стеклонитей. Также ЭД-20 применяют для:
гидроизоляции бассейнов;
создания углеволокна и пластмасс;
изготовления пластоцементов;
заливки 3D-полов;
герметизации плат компьютеров.
Используется этот материал и при изготовлении бронежилетов.
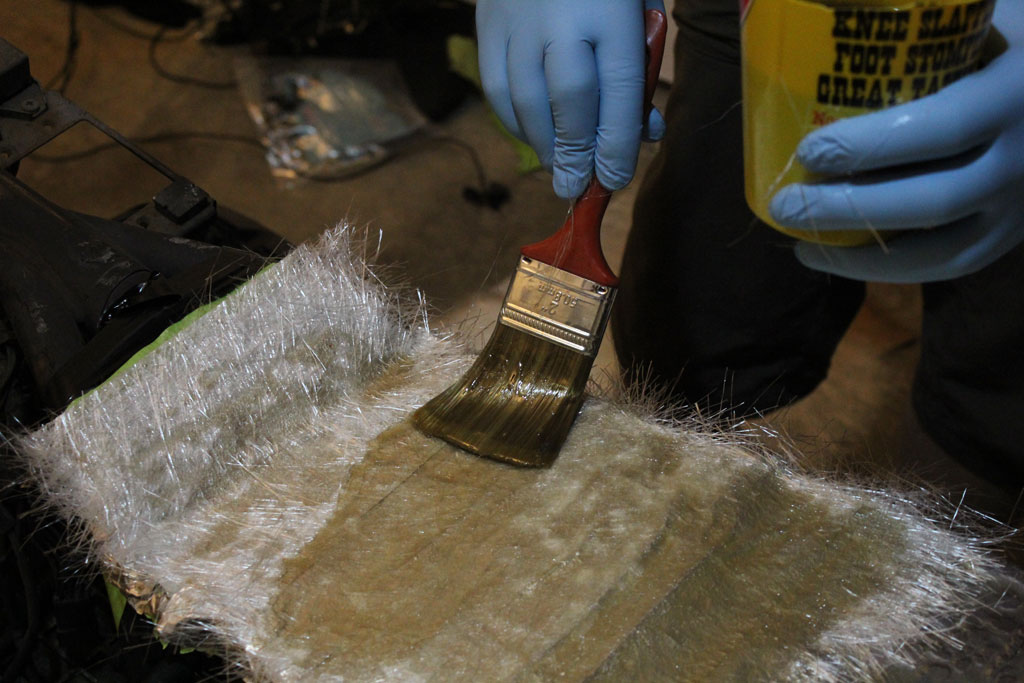
Важно
Как считают многие мастера, на самом деле имеет очень даже неплохие эпоксидная смола ЭД-20 характеристики. Заливку разного рода материалов и изделий с ее использованием, однако, нужно делать осторожно. Смешивать эпоксидную смолу ЭД-20 с отвердителем допускается только маленькими партиями. Сразу большой объем такого рабочего материала изготавливать нельзя. В противном случае смесь может закипеть и задымиться. К примеру, критический объем ЭД-20 с отвердителем ПЭПА в домашних условиях составляет не более 200-250 г.
Добавлять отвердитель в смолу этой разновидности нужно строго в количестве, рекомендованном производителем. В противном случае он не прореагирует и просто останется в массе. Регулировать скорость схватывания рабочего материала в данном случае, как при изготовлении полиэфирки, нельзя. Подвергать прессованию этот материал при производстве каких-либо изделий не требуется.
С какими средствами и материалами можно комбинировать
Смешивать ЭД-20 допускается со многими другими смолами. К примеру, достаточно часто ее комбинируют с полиэфиркой. В жидком виде при этом две эти разновидности смол никогда не смешивают. Поверхность сначала покрывают эпоксидкой, а затем — полиэфиркой. В обратном порядке эти материалы не применяют. В этом случае комбинирование, к сожалению, дает плохой эффект.
Положительные отзывы
Основным плюсом этого материала потребители, конечно же, считают, универсальность и широкую сферу использования, в том числе и в быту. У людей, предпочитающих ремонтировать разного рода домашние вещи самостоятельно, флакончик такой смолы под рукой имеется всегда.
Также достоинствами этого материала считаются:
простота в применении;
невысокая стоимость;
возможность окрашивания в любой цвет.
Многие мастера считают очень неплохими и другие технические характеристики эпоксидной смолы ЭД-20. Расход этого материала, к примеру, при его невысокой стоимости обычно является небольшим. При грунтовании, например, на 1 м2 пористой поверхности уходит около 150 г ее смеси с отвердителем, а глянцевой — не более 100 г.
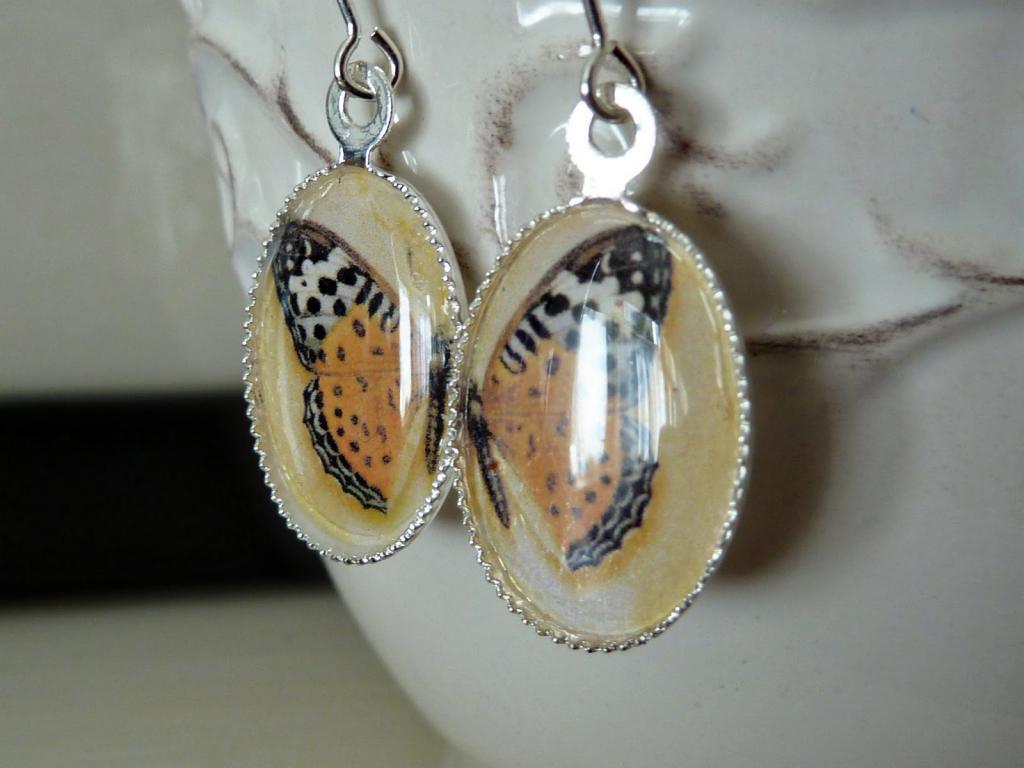
Отрицательные отзывы
Выше мы рассмотрели, какие имеет характеристики эпоксидная смола ЭД-20. Отзывы о ней в Сети, благодаря ее неплохим свойствам, действительно существуют в основном положительные. Но часто на разного рода специализированных форумах потребители отмечают и некоторые недостатки этого материала. Основным минусом такой смолы считается, конечно же, то, что из-за риска закипания ее нельзя заливать очень толстым слоем.
Также к недостатком ЭД-20 относят и наличие в ее толще пузырей после застывания. Чтобы избежать появления такой проблемы, опытные мастера советуют при нанесении прогревать это средство горелкой.
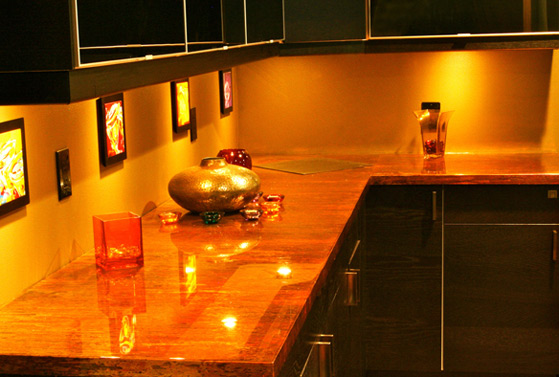
Многие потребители считают ЭД-20 все же прошлым веком. Судя по отзывам, современные аналогичные средства, имеющиеся на рынке, хотя и стоят дороже, в использовании все же могут считаться более удобными. К примеру, аналог ЭД-20 чешская смола CHS Epoxy 520 с отвердителем 921 ОП отличается прозрачностью и может заливаться достаточно толстым слоем без пузырей.
Горит ли эпоксидная смола, горючесть и температура горения
При многообразии марок эпоксидных смол и широчайшем их применении вопрос о том, горит ли эпоксидная смола не праздный. Ведь используют ее в быту, при строительстве или во время проведения ремонта все больше людей, а вопрос пожарной безопасности применяемых про строительстве и ремонте материалов встает все более остро.
Но абсолютно безопасных в пожарном отношении материалов вообще нет. При определенных условиях способен гореть даже гранит. Попытаемся разобраться, насколько относительно безопасна эпоксидная смола в уже застывшем виде, в форме изделий или готовых материалов, и какие ее марки можно использовать, не боясь, что при возникновении экстремальных ситуаций она воспламенится.
Гореть при нагреве сверх какого-то критического значения может не вся смола, а какие-то ее фракции. Что горючего может быть в длинной полимерной цепочке, до какой степени должно дойти тепловое движение молекулы, чтобы горючая фракция оторвалась, а в реальном физическом мире это проявилось в виде языка пламени, и нужно добавить появление обильной черной копоти. Потому что эпоксидная смола, а особенно эпоксидные клеи с некоторыми добавками действительно могут гореть. Вот давайте и рассмотрим условия, при которых это происходит.
Бытовые варианты
Числовой индекс в названии смол российского производства означает степень их текучести в неактивированном состоянии, то есть ЭД-22 более жидкая, чем ЭД-20. Среди заявленных свойств у этих смол значится и негорючесть. Рассматривая их молекулярную структуру, мы увидим соединение-олигомер, в основе которого диглицидиловый эфир дифинололпропана. В качестве отвердителя для обеих ЭД (эпоксиднодианов) может выступать:
- фенолформальдегиды;
- ангидриды поликарбоновых кислот;
- алифатические и ароматические амины;
- полиамиды;
- некоторые другие отвердители.
Катализаторами процесса полимеризации они не выступают: катализатор только инициирует реакцию, не вступая в нее сам, а все биоорганические отвердители являются активными участниками процесса, встраивая свободнорадикальные «хвосты» своих более простых, чем у эпоксидки, молекул в общую полимерную цепочку.
На этикетках отвердителей, которыми комплектуются смолы, всегда есть данные об их составе и при какой температуре можно смешивать оба компонента. Температурный показатель – один из главнейших, на который стоит ориентироваться при изготовлении изделий из эпоксидки или при заливке каких-то площадей ею. Отвердители ПЭПА относят к «холодным», это означает, что желательный диапазон температур, при которых происходит реакция их полимеризации с эпоксидной основой, не должен доходить до 150-200°C градусов. Потому что при этих температурах прочно и, казалось бы, навсегда отвердевшая смола начнет плавиться.
При нагревании любого вещества усиливаются тепловые колебания в его структуре, независимо от степени жесткости этой структуры.
На деле это означает, что от длинных цепочек застывших молекул начинают отрываться самые слабые и легкие соединения. Стоит только где-то рядом появиться открытому пламени, эти вырвавшиеся из структуры застывшей и начавшей плавиться эпоксидки обрывки молекул вспыхивают и быстро сгорают при наличии притока кислорода. Но для этого температура должная подняться уже до 380-420°C градусов.
Если же в смоле был использован более «горячий» аминовый отвердитель ТЭТА, который при реакции полимеризации может обеспечить саморазогрев эпоксидного состава до 40-50°C градусов, то такие застывшие эпоксидки плавятся уже при 180-250°C градусов, а температуры их разрушения с выходом горючих эфиров наружу и, соответственно, воспламенения, лежит уже в диапазоне температур 490-560°C. Это что касается бытовых эпоксидных смол.
Промышленные составы
С промышленными образцами, применяемыми для склейки или герметизирующей заливки, в качестве отвердителей используют совсем другие составы, и для полимеризации там совсем другой диапазон температур: от 150°C до 200°C градусов, притом до нижнего предела нагрев делают каскадным, ступенчатым, а потом уже резко повышают до верхнего, являющимся рабочей температурой.
У таких смол температура размягчения может доходить до 400°C и более градусов, а горения вообще не наблюдается: структура изделия просто рассыпается на мелкие фрагменты. Но это происходит, когда катастрофическая температура достигнет 900-1200°C. В быту такие смолы просто невозможно приготовить за неимением соответствующего оборудования. Сфера применения таких смол – авиастроение, с отливкой композитных материалов в виде несущих конструкций крыла или не силового каркаса фюзеляжа.
Негорючесть данных материалов, как, впрочем, и бытовых, обусловлена сложностью и разветвленностью полимерных связей, образуемых во время застывания материала при смешивании эпоксидки и отвердителя.
Чем выше температура застывания, тем разветвленнее и сложнее полимерные связи, и тем сложнее высокой температуре при нагреве готового изделия вырвать из полимерной цепочки горючую фракцию, а значит – тем сложнее будет поджечь такую смолу.
Смолы для изготовления композитных материалов как раз и создают с такими заранее заданным свойствами. Они, скорее, разрушатся, потекут, распадутся на фрагменты, чем загорятся, но это, повторим, касается смол для промышленности.
Для домашнего мастера гораздо интереснее чисто утилитарные проблемы, которые могут возникнуть с эпоксидным составами в случае возгорания жилого помещения. Тогда спешим вас «успокоить»: квартира сгорит, но эпоксидное покрытие пола пострадает мало. Так же, как мало пострадает сделанный вашими руками красивый кухонный «фартук» в зоне мойки и плиты или эпоксидный стол. Для горения изделий из эпоксидки требуется постоянный контакт с открытым пламенем и хороший приток кислорода. Иначе они быстро гаснут, а в случае с полом вообще могут не загореться из-за высокой температуры только в верхней части помещения и сильной теплоотдачи залитого на пол эпоксидного слоя в нижележащие уровни пола – бетон или что там было в качестве выравнивающей основы.
Резюмируя и отвечая на вопрос по существу «горит ли эпоксидная смола» скажем, что горит, но чрезвычайно плохо, и причиной пожара быть никак не может.
Мнение эксперта
Олег Васильев
Мастер по изготовлению мебели и предметов интерьера из эпоксидной смолы. Создает уникальные вещи на заказ на своем производстве.
Задать вопрос мастеруВ общем случае пожарную опасность могут представлять отвердители для эпоксидной смолы, особенно с добавками ацетонов, которыми иногда грешат нерадивые продавцы смол, увеличивая время жизни смеси при заливке. Речь может идти о том, что подобные отвердители сами по себе являются горючими веществами.
Поликонденсация и отверждение эпоксидных полимеров
Предварительный тест
Рекомендуемое чтение
Цели
Успешное завершение этого модуля должно позволить студенту:
- Чтобы получить представление о полимеризации путем образования форполимера и его отверждения с образованием готового полимера.
- Для расчета эпоксидной эквивалентной массы форполимера и восьми эквивалентов массы для отверждения с учетом структурных формул.
- Чтобы различать термореактивный пластик и термопласт.
Теория
В общем, существует два совершенно разных типа полимеризации, присоединение и конденсация, также называемые полимеризацией с цепным и ступенчатым ростом соответственно. Цепная или аддитивная полимеризация может быть проиллюстрирована реакцией стирола со свободным радикалом:
Конденсационные полимеры или полимеры ступенчатого роста образуются с вытеснением небольшой молекулы для каждой единицы, добавленной к полимерной цепи, и реакция протекает последовательно, образуя димер, тример и т. Д.Для полимера, такого как поли (этилентерефталат), это можно проиллюстрировать следующим образом:
всего:
Тип конденсационной полимеризации, который дает линейный полимер (или «форполимер», как обычно называют) с реакционноспособными группами на концах цепи, который может быть отвержден с образованием сетчатого полимера, представляет собой поликонденсацию эпоксидных полимеров. Образование эпоксидного полимера можно проиллюстрировать реакцией между 2,2-бис (4-гидроксифенил) пропаном (I) (бисфенолом-A) и эпихлоргидрином (II) с первоначальным образованием форполимера, как показано ниже:
Этот процесс можно повторить с любой стороны, чтобы получить продукт, который может быть представлен как:
Это диглицидиловый эфир бисфенола-A (DGEBA), где n представляет количество раз, когда повторяющееся звено встречается в форполимере.Если n равно 0 или 1, продукт представляет собой вязкую жидкость. Если n больше 1, продукт является хрупким твердым телом. Относительные количества реагентов определяют значение n — большой избыток эпихлоргидрина, способствующий образованию жидкости.
Сшивание или отверждение с образованием твердого вещества проиллюстрировано для обычного полифункционального амина на Фигуре 1.
фигура 1Некоторые ангидриды, такие как фталевый ангидрид (III), также используются в качестве отвердителей. Сначала они реагируют со свободной гидроксильной группой в цепи, освобождая группу карбоновой кислоты для реакции либо с гидроксилом другой цепи, либо с эпоксидной группой.
(III)Эпоксидные смолы — это термореактивных материалов в отличие от термопластичных материалов . Термореактивные пластмассы отверждаются или «устанавливаются» в форму, которая сохраняется до температуры разложения пластмассы без плавления, в то время как термопласты имеют температуры плавления или ожижения. Термореактивные пластики также нерастворимы в отвержденном состоянии, тогда как термопласты обычно содержат несколько растворителей.
Эпоксидные смолы начали коммерчески внедрять в 1947 году. 1 В 1974 г. в основном смолы использовались в качестве защитных покрытий, где они превосходны из-за крайне инертной природы отвержденного продукта. Также используются клеи, ламинаты и литейные смолы. Смолы демонстрируют низкую усадку в реакциях отверждения, что делает их чрезвычайно ценными при заполнении пространств.
Система эпоксидной смолы требует двух компонентов: диэпоксида или его эквивалента (эпихлоргидрин эквивалентен диэпоксиду, так как другая эпоксидная группа образуется при разрушении первой) и реакционноспособного диола или полиола.Эпихлоргидрин является наиболее доступным и дешевым эквивалентом диэпоксида, и почти все коммерческие эпоксидные системы используют его. Бисфенол-А также широко используется, поскольку ароматическая природа увеличивает реакционную способность гидроксила и увеличивает прочность образующейся смолы. Алифатический триол, такой как глицерин (IV), был использован для более плотного сшивания.
(IV)Другими полигидроксильными соединениями, которые находят применение в составах эпоксидных смол, являются новолаки, которые являются продуктами реакции фенолов и формальдегида в растворе кислоты и могут быть представлены следующим образом:
Эти материалы могут давать эпоксидные смолы высокой прочности.
Комбинация доступных диэпоксидов или эквивалентов и полигидроксисоединений дает большое количество возможных эпоксидных преполимеров. Количество возможных смол увеличивается еще больше за счет количества возможных отвердителей, которые можно использовать для каждого из форполимеров. Первичные амины и ангидриды ранее упоминались как отвердители, однако доступны другие типы, и отверждение может быть анионным,
катионный,
или кислотами Льюиса, или вторичными или третичными аминами.
Освободившаяся алкоксидная группа может реагировать с другим эпоксидом или отщеплять активный водород от прореагировавшей эпоксидной группы, обеспечивая другой анион, способный к дальнейшей реакции с другими эпоксидными группами. Вторичные амины подвергаются реакциям, подобным третичным аминам, после предварительных реакций (подобно первичным аминам), которые образуют третичные амины. Выбор отвердителя предусматривает широкий выбор отвержденных смол.
Для получения оптимальных свойств отвержденной смолы необходимо контролировать стехиометрию реакции отверждения.Эпоксидные форполимеры характеризуются содержанием эпоксида или эквивалентной массой эпоксида, которая представляет собой массу смолы, содержащей один моль эпоксидных групп. Для соединения (V)
(V)Эквивалентная масса — это молекулярная масса, деленная на два, количество эпоксидных групп. Эквивалентная масса отвердителя — это молекулярная масса агента, деленная на количество участков в молекуле, способных открывать эпоксидные кольца. Для первичных аминов это будет молекулярная масса, деленная на количество заменяемых атомов водорода.Таким образом, один эквивалент эпоксидного форполимера отверждается одним эквивалентом отвердителя.
Степень отверждения в системе смола / отвердитель можно измерить с помощью различных методов. Поскольку большая часть эпоксидных смол используется в областях, где требуется их прочность, многие тесты, такие как определение точки размягчения по Вика и температуры прогиба, измеряют увеличение прочности материала. 2 Поскольку материал является сшитым и, следовательно, не растворяется в большинстве систем растворителей, степень набухания в растворителе может использоваться для отслеживания степени отверждения.
Экспериментальная
Следующая реакция, которая будет проведена в этом эксперименте, может быть представлена следующим образом:
Эта реакция известна как реакция «улучшения», и она используется в коммерческих целях для превращения жидкой смолы с низким молекулярным весом, такой как Epon 829, в форполимеры с более высокой молекулярной массой, которые более подходят для использования в покрытиях и клеях. в этой лаборатории используется как клей.
Чтобы определить соотношение реагентов, которые будут использоваться в синтезе, полезно использовать уравнение Каротера в форме, показанной ниже.
(A / B) — (C / D) = (A + C) / Eгде: | A = вес смолы, подлежащей продвижению |
B = эквивалентный вес смолы EPON 829 | |
C = масса бисфенола A | |
D = эквивалентная масса бисфенола A | |
E = желаемый эквивалентный вес форполимера |
Эквивалентная масса используемой смолы будет предоставлена инструктором лаборатории, и эквивалентная масса высокочистого бисфенола А принимается равной половине молекулярной массы, или 114 г / моль.Учащийся рассчитает процентное содержание реагентов, необходимых для получения массы эпоксида (эквивалентной массы) 300 г / например, для форполимера.
Синтез осуществляется в следующей ступенчатой последовательности:- Установите реакционный котел с двигателем для перемешивания, термометром и нагревательным кожухом в кожухе обычным образом (конденсатор не требуется). Каждый раз, когда нужно вставить газовый стержень в резиновую пробку, стекло следует смазать глицерином. Оберните обе руки полотенцами, чтобы в случае разрушения стекла полотенца защищали руки, а стекло нужно было вставить легким вращающим движением.
- Добавьте рассчитанный ранее вес смолы, чтобы получить общую реакционную смесь 300 грамм, и начните нагревание при умеренном перемешивании.
- При температуре 100 o C добавьте в чайник бисфенол А. Продолжайте нагревать, пока весь бисфенол А не растворится.
- После 2 часов нагревания перелейте реакционную смесь в емкость, указанную инструктором лаборатории. Сохраните окончательный образец решения, использованный для определения WPE.
- Очистите реактор, растворив остаточную смолу ацетоном.Это легче всего сделать, пока колба еще теплая, так как смола плохо растворяется при охлаждении до комнатной температуры.
Приготовьте две колбы Эрленмейера, поместив пипеткой 20 мл стандартизированной HCl в пиридине (который получают путем разбавления 16 мл концентрированной HCl до одного литра пиридином) в каждую колбу. Точно взвесьте примерно 0,75 г образца раствора, сохраненного на шаге 5 по разнице, в каждую колбу, используя весы Меттлера.Разница в весе достигается путем взвешивания заполненной пробирки, заливки указанного количества в колбу и повторного взвешивания пробирки. Разница двух весов в весе, добавленном к колбе.
Колбы осторожно нагревают на горячей плите с настройкой 2 в течение 20 минут. Добавляют шесть капель индикатора фенолфталеина, и образцы титруют до конечной точки фенолфталеина 0,1 н. Гидроксидом калия в метаноле. При титровании следует соблюдать осторожность, так как перед изменением цвета растворы становятся мутными.
WPE рассчитывается по следующей формуле:
(ПРИМЕЧАНИЕ: ВСЕ РАБОТЫ С ПИРИДИНОМ ДОЛЖНЫ ПРОИЗВОДИТЬСЯ В ВЫТЯЖКЕ. ТАКЖЕ СЛЕДУЕТ ПРИНИМАТЬ ЗАБОТУ, ЧТОБЫ ИЗБЕЖАТЬ ИСПАРЕНИЯ МЕТАНОЛА В СТАНДАРТЕ ГИДРОКСИДА КАЛИЯ.)
Этот продукт будет протестирован на адгезию в течение следующего лабораторного периода.
Подготовка образца адгезии
Четыре образца адгезии будут приготовлены следующим образом:
1. | В пластмассовом стакане взвесьте 50 г эпоксидной смолы. образец. | ||||||
2. | Рассчитайте необходимое количество отвердителя (CA) для образцов по следующей формуле: | ||||||
грамм смолы | х | вес на активный | х | соотношение | = | грамма | |
Смола WPE | водород в CA | множитель (1) | CA | ||||
Вес активного водорода в CA определяется путем расчета молекулярная масса и деление на количество активных атомов водорода.Коэффициент отношения равен второе значение в соотношении эпоксидная смола: отвердитель, которое будет присвоено инструктор. | |||||||
3. | Взвесьте CA в пластиковый стакан с эпоксидной смолой и тщательно перемешайте. После смешивания смесь должна быть слегка мутной. | ||||||
4. | Покройте субстрат, предоставленный инструктором, смесью таким образом, чтобы толщина сухой пленки будет около 2 мил. | ||||||
5. | Удалите излишки клея со сторон стойки деревянным аппликатором. | ||||||
6. | Поместите подложку с покрытием в печь, предварительно нагретую до 100 o C и выдержать 1 час. |
Модель Instron 1140 будет использоваться для измерения прочности клеев, сделанных в этом эксперименте. Краткое описание Instron включено в качестве приложения к этому разделу. Шаги теста также включены в приложение. Клей будет протестирован при следующих параметрах:
Тензодатчик: | 500 кг |
Скорость диаграммы: | 20-50 см / мин |
Скорость крейцкопфа: | 5 см / мин |
Полная шкала: | 100 кг |
Тест завершен, когда перо вернется к нулевому напряжению на графике.Осмотрите испытанный участок и определите тип разрушения покрытия, оценив его по следующей шкале:
А | нарушение адгезии покрытия на подложке |
С | когезионный разрыв покрытия |
переменного тока | комбинация A и C |
S | разрыв клея на шпильке |
КС | комбинация C и S |
Рассчитайте предел прочности на разрыв , необходимый для этого разрушения.
Расчет прочности на растяжение
ПРОЧНОСТЬ НА РАЗРЫВ (T.S.) = Сила / Площадь
Т.С. = | (значение полной шкалы, кг) (% полной шкалы при разрыве) (ускорение под действием силы тяжести, г) |
(толщина образца, см) (ширина образца, см) |
пример: | T.S. = (200 b кг) (a) (9,8 м / с 2 ) / wT |
Т.S. = (200 кг) (0,51) (9,8 м / сек 2 ) (1,31 см) (0,323 см) | |
т.с. = 2362 г . м / с 2 см 2 = 2,362×10 3 Н / см 2 | |
УДЛИНЕНИЕ = | = расстояние перемещенных губок (дюймы) |
Lo = начальное расстояние кулачков (дюймы) |
пример: | Относительное удлинение = | d (скорость диаграммы / скорость ползуна) |
Lo | ||
Относительное удлинение = | 3.5 дюймов (5 см / мин / 10 см / мин) | |
4,0 дюйма | ||
Относительное удлинение = 0,43 | ||
Относительное удлинение = 43% | ||
МОДУЛЬ = | Начальное напряжение | |
пример: | Модуль = | (значение полной шкалы) (% полной шкалы при разрыве) (г) / вес T |
[d ‘(скорость диаграммы / скорость ползуна)] / Lo | ||
Модуль = | (200 кг) (.8) (9,8 м / с 2 ) (1,31 см) (0,323 см) | |
{(1,1 дюйма) (5 см / мин / 10 см / мин)} / 4 дюйма | ||
Модуль = | 26 950,7 кг . м / с 2 . см 2 | |
Модуль = | 2,7 x 10 4 Н / см 2 |
b 200 кг получается при использовании свинцового элемента на 500 кг и настройке диапазона 20 М.
Рисунок 3
Инстрон
.отвердитель эпоксидной смолы / отвердитель с низкой точкой плавления hhpa Cas No 85-42-7, поставка производителем с самой низкой ценой
Отвердитель эпоксидной смолы / hhpa Отвердитель с низкой температурой плавления CAS NO 85-42-7, поставка производителем по самой низкой цене
Введение:
Большой опыт производства и торговли:
Он широко используется в качестве отвердителя эпоксидной смолы во многих отраслях промышленности.
Контактная информация:
Менеджер по продукту
Лено
icason036 (@) icason.com
36 Skype ID: com . О смолах, отверждаемых УФ-излучением — Техническая информация


Что такое смола с УФ-отверждением?
Смолы, отверждаемые УФ-излучением, представляют собой материалы, которые полимеризуются и отверждаются за короткое время за счет энергии, излучаемой устройствами ультрафиолетового излучения.
Они особенно используются в качестве промышленных материалов для герметизации, склеивания и нанесения покрытий.
Превосходные характеристики смол, отверждаемых УФ-излучением
- Поскольку скорость отверждения высокая, рабочий час сокращается.
- Поскольку они не отверждаются без УФ-облучения, ограничений в процессе нанесения покрытия немного.
- Отверждаются при низкой температуре.
- Однокомпонентная смола, не содержащая растворителей, обеспечивает хорошую обрабатываемость.
- Доступно множество отвердевших свойств.
Поскольку продукты обладают этими преимуществами, снижение затрат может быть достигнуто в различных областях.


Виды УФ-отверждаемых смол

На следующей странице сравниваются эти два типа.


На следующей странице представлены продукты ThreeBond различных типов.





Подходит для серийного производства средних и крупных деталей.

Для склеивания и частичной временной фиксации компактных деталей.

Встраиваемый в производственную линию.

Для частичного облучения экспериментальных или крупногабаритных изделий.
Мы, компания ThreeBond, предлагаем различные модели, от простых до линейных встраиваемых.
Баллов на выбор лампы или фонарного дома
- Соответствующая длина волны лампы Короткая длина волны эффективна для поверхностного отверждения, а длинноволновая — для глубинного.
- Достаточная интенсивность излучения Выбирайте их с учетом ослабления силы света из-за длительного использования лампы.
Пожалуйста, обратите внимание на два вышеупомянутых пункта, чтобы выбрать лампу и фонарик для системы УФ-излучения.


Для панели дисплея сотового телефона

Примечания по применению при их использовании
- Установите оптимальные условия облучения (освещенность, время и т. Д.).) в соответствии с вашей целью.
- Оцените смолы при тех же условиях отверждения, что и при массовом производстве, чтобы минимизировать первоначальные проблемы массового производства.
- Регулярно проверяйте соблюдение установленных условий облучения.
Используйте местную вентиляцию и используйте перчатки и защитные средства, чтобы предотвратить повреждение кожи.

Поскольку УФ-отверждаемая смола является однокомпонентной и не содержит растворителей, она не загрязняет рабочую среду каким-либо растворителем.Этот клей затвердевает за секунды. Его превосходство в массовом производстве значительно сокращает производственные процессы.
Мы, ThreeBond, всегда стараемся предлагать продукты, которые наилучшим образом соответствуют вашим требованиям к дизайну.
Другие серии семинаров по клеям
№ 5
О смолах, отверждаемых УФ-излучением
-

. Неконтролируемое отверждение • Эпоксидная смола морского класса WEST SYSTEM
Основы неконтролируемого лечения
Химическая реакция, при которой смешанная эпоксидная смола отверждается, является экзотермической или выделяющей тепло. Если оставить для затвердевания в содержащейся массе, например в котле для смешивания, он может выделять достаточно тепла, чтобы расплавить пластик, обжечь кожу или воспламенить окружающие горючие материалы. Чем больше или толще эпоксидная масса, тем больше выделяется тепла и тем выше вероятность неконтролируемого отверждения. 100-граммовая масса смешанной эпоксидной смолы может нагреваться до 400 ° F.
Чтобы предотвратить накопление тепла и неконтролируемое отверждение, перенесите эпоксидную смолу из емкости для смешивания на роликовый поддон или другой широкий и неглубокий контейнер. Заполняйте большие полости эпоксидной смолой несколькими слоями, а не одним толстым слоем. Тепловыделение и неконтролируемое отверждение (экзотермический эффект) маловероятны при типичных работах по склеиванию и нанесению покрытий, поскольку при распределении эпоксидной смолы на более тонкие слои тепло рассеивается.
Во время неконтролируемого отверждения смешанная смола и отвердитель становятся горячими и пенистыми, поскольку они термически разлагаются с образованием токсичных паров.К ним относятся монооксид углерода, оксиды азота, аммиака и, возможно, некоторые альдегиды. Затвердевшая эпоксидная смола может выделять аналогичные пары, если ее слишком нагреть. Это может произойти, если вы воспользуетесь пламенем для освобождения оборудования, закрепленного на эпоксидной смоле. Чтобы снизить этот риск, используйте достаточно тепла, чтобы освободить оборудование. При необходимости работайте в хорошо проветриваемом помещении.
Пока застывает остатки смешанной эпоксидной смолы, отложите емкость в сторону, чтобы за ней можно было наблюдать. Используйте вентилятор, чтобы рассеять пары и отвести их. Респираторы с очисткой воздуха могут быть неэффективными против этих паров.
Самовозгорание представляет опасность, когда отвердители смешиваются с опилками, древесной стружкой или другими целлюлозными материалами. Когда отвердитель проливается на опилки или смешивается с ними, воздух и влага вступают в реакцию с амином с выделением тепла. Если тепло не рассеивается достаточно быстро, опилки могут воспламениться. Не используйте опилки или другие целлюлозные материалы для поглощения пролитого отвердителя. Точно так же не выливайте неиспользованный отвердитель в мусорное ведро с опилками или другими целлюлозными материалами.
Эпоксидная смола WEST SYSTEM и отвердители классифицируются как негорючие, поскольку их температура вспышки превышает 200 ° F и они медленно испаряются.Печи, дровяные печи и другие источники тепла не представляют серьезной опасности возгорания в присутствии паров эпоксидной смолы.

Пиковые экзотермические температуры различных продуктов WEST SYSTEM
Управление экзотермией
Проверенные методы борьбы с экзотермией
Если вы все же хотите залить или отлить большой объем эпоксидной смолы, вот несколько проверенных методов минимизации тепловыделения, которые мы разработали на протяжении многих лет.
Залейте эпоксидную смолу в определенное время, несколько порций
Выбор времени важен при выполнении нескольких заливок.В идеале вы хотите дождаться пика умеренного экзотермического эффекта и начала его падения, прежде чем смешивать новую партию и разливать. Слишком долгое ожидание может привести к недостаточной связи между двумя заливками. Недостаточное ожидание может привести к перегреву и распространению трещин.
Выберите 209 Extra Slow Hardener или G / flex
Более медленное отверждение позволяет получить более глубокую заливку до того, как произойдет чрезмерное нагревание. По этой причине мы рекомендуем использовать наши самые медленные системы при заливке большего количества эпоксидной смолы: смола 105 с отвердителем 209 Extra Slow Hardener или G / flex.
Работайте при более низких температурах.
Более низкие температуры в цехе и охлаждение самой эпоксидной смолы будут работать в ваших интересах, замедляя отверждение и контролируя экзотермическую реакцию эпоксидной смолы. Более глубокая заливка может быть достигнута с меньшим тепловыделением, если начать с охлажденной эпоксидной смолы и холодной основы, пока эпоксидная смола не затвердеет до мягкого твердого вещества. Затем вы можете подвергнуть его комнатной температуре или выше, чтобы завершить лечение.
Используйте радиаторы.
Радиатор — это объект, который может поглощать много тепла.Если вы наносите эпоксидную смолу на тяжелый металлический объект или поверх него, он будет поглощать гораздо больше тепла, чем объект с меньшей плотностью.
Наполнители с высокой плотностью также могут действовать как теплоотвод, уменьшая экзотермию, поглощая больше тепла, чем наполнитель с низкой плотностью, и занимая больший объем. Это оставляет меньше места для смешанной смолы и отвердителя, что снижает тепловую реакцию.
Если используется неправильная комбинация эпоксидной смолы и наполнителя для определенной температуры отверждения, эпоксидная смола может выделять достаточно тепла, чтобы тлеть и гореть.Добавление большего количества наполнителя с низкой плотностью, безусловно, уменьшит количество эпоксидной смолы в данном объеме, но наполнитель будет действовать как изолятор, а не радиатор. —Из Controlling Exotherm Майк Барнард в Epoxyworks 39.
.Температура плавления эпоксидной смолы застывшей: Какую температуру выдерживает эпоксидная смола после застывания

Они особенно используются в качестве промышленных материалов для герметизации, склеивания и нанесения покрытий.













О смолах, отверждаемых УФ-излучением
